Wire Bond Substrate Manufacturer
Wire Bond Substrate Manufacturer,Wire Bond Substrate is a critical component in semiconductor packaging, designed to facilitate the connection of integrated circuits (ICs) to a Printed Circuit Board (PCB) using wire bonding techniques. These substrates are composed of multiple layers, including insulating, metal, and conductive layers, ensuring robust electrical connections and effective thermal management. The wire bonding process involves attaching fine wires from the IC pads to the substrate pads, providing reliable electrical pathways. Wire Bond Substrates are essential in various applications, from consumer electronics to automotive and industrial devices, offering a balance of performance, cost-effectiveness, and ease of manufacturing.
A wire bond substrate is like the backstage manager in the world of electronics packaging, especially in the realm of semiconductor devices. It’s the unsung hero, providing a solid stage for integrated circuits (ICs) or other semiconductor stars to connect and communicate within the grand electronic performance.
Imagine wire bonding as the choreography – delicate, precise moves performed by thin wires, often dressed in aluminum or gold attire. These wires gracefully dance, establishing electrical connections between the semiconductor device and the substrate. First, they tango with the device’s contact pads, and then they waltz over to the corresponding pads on the substrate.
Think of the substrate as the venue, built from various materials like ceramics or the ever-versatile FR-4, an epoxy-based fiberglass. Choosing the substrate material is like selecting the right venue for a concert – considerations include thermal performance, electrical vibes, and budget constraints.
Wire bond substrates play a backstage manager’s role in the assembly and packaging of semiconductor devices, providing a reliable foundation for the components to harmonize and ensuring a seamless electrical connection. This technology takes center stage in the production of integrated circuits, microprocessors, and other electronic gadgets, making it an essential player in the electronic orchestra.
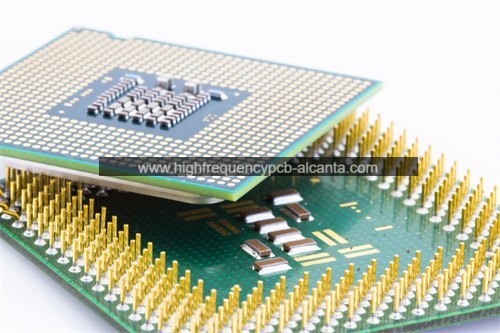
Wire Bond Substrate Manufacturer
What are the functions of Wire Bond Substrate?
Wire bond substrates act as the backbone of semiconductor packaging, seamlessly orchestrating various functions essential for the performance and integration of electronic components. Let’s explore these roles with a different lens:
Electric Symphony Conductor: At its core, a wire bond substrate conducts the electric orchestra, facilitating harmonious connections between the semiconductor device and the larger electronic ensemble. This is achieved through a delicate dance of thin wires, elegantly linking contact pads on the semiconductor device to their counterparts on the substrate.
Signal Maestro: Beyond mere connectivity, the substrate takes on the role of a signal maestro, ensuring the smooth transmission of electrical messages throughout the electronic composition. It acts as a conduit, guiding signals with precision and efficiency between different sections of the circuit.
Mechanical Virtuoso: Picture the wire bond substrate as a mechanical virtuoso, providing not only support but a stable stage for the semiconductor device. It’s the structural backbone, securing and positioning the device within the electronic performance, especially crucial in environments with vibrations or mechanical stresses.
Thermal Ballet Choreographer: In the world of temperature dynamics, the substrate becomes a thermal ballet choreographer. It manages the heat generated during the electronic performance, preventing overheating and ensuring the reliability of the entire ensemble. The choice of substrate material influences its thermal conductivity and heat dissipation properties.
Packaging Architect: Think of wire bond substrates as the architects of packaging, seamlessly integrating various components into a compact and organized assembly. This role contributes significantly to the art of miniaturization in electronic devices.
Compatibility Composer: The substrate must harmonize with semiconductor materials and manufacturing processes. It acts as a compatibility composer, ensuring a symphony of materials that adhere reliably to wires and semiconductor devices, creating enduring connections.
In essence, wire bond substrates aren’t just connectors; they are the maestros conducting a symphony of electrical connectivity, signal transmission, mechanical stability, thermal management, and packaging integration within the intricate world of semiconductor devices.
What are the different types of Wire Bond Substrate?
Wire bond substrates, like a diverse ensemble, take on various roles to cater to the unique demands of electronic applications. Let’s explore the symphony of types:
Ceramic Variations:
Alumina (Al2O3): Celebrated for impeccable electrical insulation and reliable thermal conductivity, alumina ceramic substrates take the spotlight where effective heat dissipation is paramount.
Aluminum Nitride (AlN): Stepping up the thermal game, aluminum nitride substrates shine in applications where superior heat dissipation is a non-negotiable requirement.
Organic Harmony:
FR-4 (Flame Retardant 4): The workhorse of organic substrates, FR-4, interlaces woven glass fabric with epoxy resin, delivering a cost-effective solution for diverse electronic applications, including the realm of PCBs.
Polyimide: Adding a flexible note to the composition, polyimide substrates sway to the requirements of applications demanding pliability, such as flexible circuits or adaptable electronic devices.
Metallic Ensemble:
Copper Crescendo: Taking the stage in high-power applications, copper substrates play the lead with their exceptional thermal conductivity, ensuring an efficient performance.
Aluminum Overture: Striking a chord between thermal efficiency and cost-effectiveness, aluminum substrates find their place in the orchestra of various electronic devices.
Silicon Sonata:
Silicon Wafers: Stepping into the limelight for microelectromechanical systems (MEMS) and specialized sensors, silicon wafers bring their finesse to the semiconductor stage.
Glass Melody:
Borosilicate Glass: Entering the composition for specialized applications demanding a harmonious blend of high thermal resistance and a low coefficient of thermal expansion.
Composite Fusion:
Metal Matrix Composites (MMCs): Infusing a dynamic mix of reinforcing materials, such as ceramic particles, into a metal matrix, these substrates create a symphony that harmonizes excellent thermal conductivity with mechanical strength.
Choosing a wire bond substrate orchestrates a composition influenced by the nuances of specific applications, thermal prerequisites, mechanical resilience, electrical characteristics, and budgetary constraints. The manufacturing choreography, whether through thick-film or thin-film technologies, takes center stage, showcasing the versatility of each substrate material in creating a unique and harmonious electronic melody.
How is Wire Bond Substrate related to PCB?
Wire bond substrates and Printed Circuit Boards (PCBs) engage in a collaborative duet, contributing unique attributes to the intricate choreography of electronic assembly. Let’s explore their dynamic connection through a different lens:
Performance Roles:
Wire Bond Substrate: Stepping onto the stage as a specialized performer, wire bond substrates shine in their role of providing a dedicated platform for integrated circuits and semiconductor devices. They excel in the art of creating precise electrical connections, orchestrating seamless signal transfers, and executing nuanced thermal management.
PCB: Playing the role of a versatile conductor, the PCB takes center stage to harmonize various electronic components, including wire bond substrates. It conducts a symphony of connections, weaving together resistors, capacitors, and ICs through an intricate network of conductive pathways.
Integration Choreography:
Wire Bond Substrate: With a graceful integration routine, wire bond substrates seamlessly embed themselves within the packaging of specific semiconductor devices. They perform with precision, catering to applications where meticulous electrical connections and thoughtful thermal considerations take precedence.
PCB: Executing an elaborate dance, the PCB becomes the central hub, gracefully integrating wire bond substrates and other electronic elements. It crafts the overarching structure that brings the entire electronic ensemble together.
Material and Design Ballet:
Wire Bond Substrate: Donning a diverse wardrobe of materials, from ceramics to organic elements like FR-4 or polyimide, wire bond substrates showcase a design tailored to the unique demands of the supported semiconductor device.
PCB: In a design ballet, the PCB emerges as a layered composition, utilizing materials like fiberglass-reinforced epoxy (FR-4). Its intricate design weaves a tapestry of conductive traces and insulating layers, creating an elegant network that forms the circuit.
Application Symphony:
Wire Bond Substrate: Stealing the limelight in the packaging of semiconductor devices such as integrated circuits and microprocessors, wire bond substrates become the focal point, catering to the specific needs of these intricate electronic performers.
PCB: Leading a symphony of applications, PCBs find their place in an array of electronic devices, from everyday gadgets to sophisticated industrial setups. Their standardized structure serves as an efficient canvas for connecting and mounting diverse electronic components.
In essence, wire bond substrates and PCBs engage in a collaborative dance, with wire bond substrates taking on a specialized role in semiconductor packaging, while PCBs conduct the overall symphony, bringing together a diverse ensemble of components into a cohesive electronic performance.
What is the main structure and production technology of Wire Bond Substrate?
The architecture of a wire bond substrate is contingent upon the selected material, weaving a tapestry of variations crafted to suit specific applications and the nuanced demands of semiconductor devices. Below unfolds a reimagined narrative, shedding light on the generalized structure and production intricacies of wire bond substrates:
Structural Symphony:
Material Ensemble:
Wire bond substrates embrace a diverse repertoire of materials, from the classic elegance of ceramics to the contemporary notes of organic compounds, metals, or the avant-garde fusion of composites. Among the performers on this stage are alumina, aluminum nitride, FR-4, polyimide, copper, and their counterparts.
Stratified Composition:
A layered composition emerges, akin to the movements in a musical piece. These layers play distinct roles – conducting electricity, insulating, reinforcing structurally, and orchestrating thermal dynamics with finesse.
Conductive Crescendos:
Conductive pathways, composed of metals such as copper or aluminum, etch their intricate melodies on the substrate. These pathways guide the electronic signals, conducting a symphony that harmonizes the semiconductor device with other instrumental components.
Pad Cadence:
Contact pads gracefully take center stage, poised on the substrate’s surface. They become the anchor points, inviting delicate wire bonds to join in the dance, creating connections that resonate with precision.
Die Attachment Ballet:
A dedicated area hosts the graceful attachment of the semiconductor die. Here, a ballet unfolds, and die attach materials play the role of choreographers, ensuring a secure and enduring connection.
Thermal Pas de Deux:
In response to the diverse applications, wire bond substrates choreograph their thermal management. Additional layers, akin to dancers in a pas de deux, may incorporate materials with exceptional thermal conductivity or architectural structures designed to dissipate heat gracefully.
Production Choreography:
The production of wire bond substrates follows a series of meticulously orchestrated movements:
Substrate Overture:
The material takes center stage in a prelude of substrate formation, where casting, molding, or machining crafts the foundational structure, setting the tone for the subsequent acts.
Layered Impression:
Deposition methods, akin to artists applying brush strokes, add layers of conductive and insulating materials. Sputtering, chemical vapor deposition (CVD), or the intricate dance of screen printing contribute to the textured canvas.
Photolithography Sonata:
The substrate enters a sonata of precision through photolithography. A photoresist, akin to a musical score, captures the intricate pattern, exposed through a mask and developed to perfection.
Etching Elegance:
The selective etching process reveals the refined contours of conductive traces and features, akin to a master sculptor unveiling a masterpiece.
Die Attachment Waltz and Wire Bonding Harmony:
In a captivating waltz, the semiconductor die is securely attached using die attach materials. Simultaneously, wire bonding takes the stage, weaving connections that resonate harmoniously between the semiconductor device and the substrate.
Optional Encapsulation Interlude:
As the performance nears its conclusion, an optional encapsulation interlude may take place, sheltering the semiconductor device and wire bonds from environmental elements.
This symphony of production technology adapts its tempo and rhythm to the material’s unique characteristics, design nuances, and the intended narrative of the wire bond substrate. Advanced techniques, reminiscent of thick-film or thin-film processes, add layers of sophistication to this artistic creation, shaping a performance that resonates with tailored precision.
Frequently Asked Questions (FAQs)
What Defines a Wire Bond Substrate?
A Wire Bond Substrate stands as a foundational material in semiconductor packaging, providing a stage for integrated circuits. Its primary roles include facilitating electrical connections and often contributing to thermal management.
What Role is Played by a Wire Bond Substrate Manufacturer?
A Wire Bond Substrate Manufacturer specializes in crafting and supplying essential materials or components for wire bonding applications. Their focus lies in tailoring substrates with specific materials and designs to meet the unique requirements of semiconductor devices.
Can Wire Bond Substrate Manufacturers Accommodate Customization Requests?
Yes, many Wire Bond Substrate Manufacturers offer customization services to meet the unique requirements of clients. This involves tailoring materials, designs, and production processes for various semiconductor devices and applications.
How Do Wire Bond Substrates Contribute to Thermal Regulation?
Certain wire bond substrates incorporate features designed for efficient thermal management. This may involve using materials with high thermal conductivity or integrating specific structures to enhance heat dissipation, ensuring optimal performance.
Are Wire Bond Substrates Limited to Semiconductor Devices?
While commonly associated with semiconductor devices, wire bond substrates extend beyond this realm. They find applications in various electronic components, including flexible circuits and sensors.
In Which Industries Are Wire Bond Substrates Utilized?
Wire bond substrates play vital roles in diverse industries, including semiconductor manufacturing, electronics, telecommunications, automotive electronics, and medical devices.
Conclusion
In conclusion, the realm of Wire Bond Substrates unfolds as a critical landscape in semiconductor packaging, guided by a symphony of materials, manufacturing intricacies, and versatile applications. As the foundational stage for integrated circuits, wire bond substrates choreograph an intricate dance of electrical connectivity and thermal management.
Manufacturers in this domain bear the responsibility of orchestrating this performance, specializing in the crafting and supply of materials tailored to the unique needs of semiconductor devices. With a diverse palette of materials, from ceramics to metals, wire bond substrates find resonance in industries spanning electronics, telecommunications, and medical devices.
The manufacturing process itself reads like a well-composed score, involving substrate fabrication, layer deposition, precise patterning through photolithography, and the delicate routines of die attachment and wire bonding. Customization, a key note in this melody, allows manufacturers to harmonize their products with the specific requirements of clients.
As these substrates contribute to the thermal ballet of electronic devices, their features may include materials with superior thermal conductivity or structures designed for efficient heat dissipation. Beyond the confines of semiconductors, wire bond substrates extend their performance to various electronic components, showcasing their versatility.
In the search for a trustworthy Wire Bond Substrate Manufacturer, thorough research becomes the overture. Considerations such as experience, reputation, adherence to quality standards, and responsiveness to customer needs guide the selection process. Trade shows, industry forums, and referrals serve as valuable overtures in this quest.
In essence, wire bond substrates encapsulate a dynamic interplay of technology, materials, and design, contributing to the seamless functionality of electronic devices. As the symphony of electronic components continues to evolve, wire bond substrates maintain their crucial role, adapting and innovating in tune with the ever-changing cadence of the semiconductor landscape.