Step Cavity Package Substrate Manufacturer
Step Cavity Package Substrate Manufacturer,Step Cavity Package Substrates are specialized PCBs designed with recessed areas or cavities to accommodate semiconductor chips or other electronic components. This design minimizes the overall profile of the package, enhancing thermal management and reducing electrical noise. By embedding components within the substrate, Step Cavity Packages optimize signal integrity and improve reliability in high-frequency applications. They are crucial in compact electronic devices where space constraints are critical, such as mobile phones, IoT devices, and automotive electronics. These substrates are engineered with high precision to ensure consistent performance, making them ideal for applications requiring robustness, thermal efficiency, and miniaturization.
What is a Step Cavity Package Substrate?
A Step Cavity Package Substrate is a specialized type of substrate used in integrated circuit (IC) packaging. It features a cavity (or recess) that is created in layers of the substrate material, typically made from materials like ceramics or high-performance resins. This cavity is designed with multiple steps or levels, allowing for precise placement and integration of IC components such as dies or chips.
The steps in the cavity accommodate different components of the IC package, providing a structured environment for secure positioning and connection of the components. This design helps in managing thermal dissipation, electrical performance, and mechanical stability, crucial for high-frequency applications and power electronics.
Step cavity substrates are used in various industries where compact size, high reliability, and efficient thermal management are essential, such as telecommunications, automotive electronics, and aerospace. The manufacturing process involves advanced techniques to ensure precise dimensions and material properties, meeting stringent performance requirements demanded by modern electronic devices.
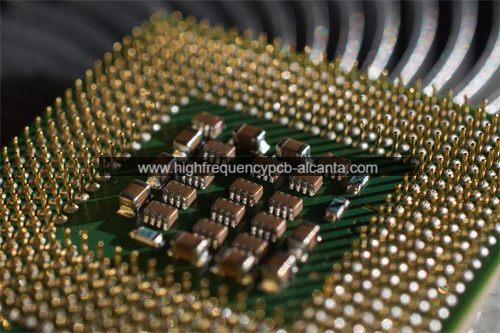
Step Cavity Package Substrate Manufacturer
What are the Step Cavity Package Substrate Design Guidelines?
Design guidelines for Step Cavity Package Substrates typically focus on several key aspects to ensure optimal performance and reliability:
- Cavity Dimensions and Tolerances:Specify the exact dimensions (depth, width, length) of each step in the cavity to accommodate specific components. Tolerances ensure proper fit and alignment of IC chips or other elements.
- Material Selection:Choose substrate materials based on thermal conductivity, electrical properties, and mechanical strength requirements. Materials often used include ceramics (e.g., LTCC, HTCC) or high-performance resins (e.g., FR-4, PTFE) depending on application needs.
- Layer Configuration:Define the number and arrangement of substrate layers to achieve desired electrical impedance, signal integrity, and thermal management. Consideration of layer stack-up impacts routing complexity and overall performance.
- Signal and Power Integrity:Design routing paths to minimize signal loss, impedance mismatches, and crosstalk. Proper power distribution and decoupling capacitor placement are critical for stable operation.
- Thermal Management:Incorporate features like heat sinks, thermal vias, or metal-filled vias to enhance heat dissipation from active components within the cavity. Ensure sufficient thermal conductivity through substrate layers to maintain operational temperatures within safe limits.
- Mechanical Durability:Ensure structural integrity to withstand mechanical stresses during assembly, handling, and operation. Consider factors such as board flexure, vibration resistance, and compatibility with mounting methods (e.g., soldering, adhesive bonding).
- Manufacturing Feasibility:Design for manufacturability (DFM) considerations such as panelization, tooling requirements, and assembly processes. Optimizing design for automated assembly can reduce production costs and improve yield.
- Environmental and Reliability Standards:Adhere to industry standards (e.g., IPC standards) for reliability testing, solderability, and environmental resistance (e.g., moisture, temperature cycling) to ensure long-term performance under varied operating conditions.
By following these design guidelines, engineers can develop Step Cavity Package Substrates that meet performance expectations for diverse applications in electronics, telecommunications, automotive, and beyond. Each guideline ensures that the substrate design balances electrical, thermal, and mechanical requirements effectively.
What is the Step Cavity Package Substrate Fabrication Process?
The fabrication process of Step Cavity Package Substrates involves several key steps to achieve precise cavity structures and integrate electronic components effectively. Here’s a typical process outline:
- Substrate Material Selection:Choose a substrate material based on thermal, electrical, and mechanical requirements. Common materials include ceramics (e.g., LTCC, HTCC) or high-performance resins (e.g., FR-4, PTFE).
- Layer Preparation:Start with substrate layers that are typically thin and flat. These layers may already have circuit patterns and vias defined for electrical connectivity.
- Cavity Definition:Use precision milling or laser ablation techniques to create cavities in selected substrate layers. Cavities are designed with multiple steps or levels to accommodate different components of the IC package.
- Metallization:Apply conductive layers (metallization) to the substrate surfaces and within the cavities. This step ensures electrical connectivity between layers and components.
- Dielectric Layers:Introduce dielectric layers between conductive layers to insulate circuits and ensure signal integrity. Dielectrics also help in managing thermal dissipation.
- Via Formation:Create vias (plated or filled) to establish electrical connections between different layers of the substrate and to provide thermal pathways for heat dissipation.
- Component Integration:Place and bond IC chips, passive components, and other elements within the cavities. Precision placement is crucial to align components with electrical pads and ensure proper electrical and thermal performance.
- Encapsulation:Optionally, encapsulate the entire substrate assembly with protective materials such as epoxy or resin to enhance mechanical stability and protect components from environmental factors.
- Testing and Inspection:Conduct thorough testing and inspection processes to verify electrical functionality, signal integrity, thermal performance, and mechanical reliability of the finished Step Cavity Package Substrate.
- Final Finishing: Complete the substrate fabrication with surface finishing processes (e.g., solder mask application, surface coating) as required for specific application needs.
The fabrication of Step Cavity Package Substrates requires precise engineering and manufacturing techniques to meet stringent performance standards for various high-tech applications, including telecommunications, automotive electronics, aerospace, and medical devices. Each step in the process contributes to achieving optimal electrical, thermal, and mechanical properties in the final substrate product.
How do you Manufacture a Step Cavity Package Substrate?
Manufacturing a Step Cavity Package Substrate involves a detailed process to ensure precision in cavity formation and integration of electronic components. Here’s a structured outline of the manufacturing steps:
- Material Selection:Choose substrate materials based on thermal conductivity, electrical properties, and mechanical strength requirements. Common choices include ceramics (e.g., LTCC, HTCC) or high-performance resins (e.g., FR-4, PTFE).
- Substrate Preparation:Begin with flat substrate layers, typically thin and prepared with initial circuit patterns and vias for electrical connectivity.
- Cavity Definition:Utilize advanced techniques such as precision milling or laser ablation to create cavities within selected substrate layers. These cavities are designed with multiple steps or levels to accommodate different IC components.
- Metallization:Apply conductive layers (metallization) onto the substrate surfaces and within the cavities. This process ensures electrical connectivity between layers and components.
- Dielectric Layer Application:Introduce dielectric layers between conductive layers to insulate circuits, manage thermal dissipation, and maintain signal integrity.
- Via Formation:Establish vias (plated or filled) to create electrical connections between different substrate layers and provide pathways for thermal dissipation.
- Component Integration:Place and bond IC chips, passive components, and other elements precisely within the cavities. This step ensures alignment with electrical pads and optimal electrical and thermal performance.
- Encapsulation (Optional):Optionally encapsulate the entire substrate assembly with protective materials such as epoxy or resin to enhance mechanical stability and safeguard components from environmental factors.
- Testing and Inspection:Conduct rigorous testing and inspection procedures to validate electrical functionality, signal integrity, thermal management, and mechanical reliability of the completed Step Cavity Package Substrate.
- Final Finishing:Complete the manufacturing process with surface finishing steps as required, such as solder mask application or surface coating, to meet specific application needs.
Manufacturing Step Cavity Package Substrates demands precise engineering and manufacturing expertise to achieve high reliability and performance. Each step in the process contributes to ensuring that the substrate meets stringent quality standards for diverse applications in electronics, telecommunications, automotive, and more.
How Much Should a Step Cavity Package Substrate Cost?
The cost of a Step Cavity Package Substrate can vary widely based on several factors, including:
- Materials:The type and quality of substrate materials (ceramics, high-performance resins) used significantly impact costs. Ceramics like LTCC or HTCC tend to be more expensive than standard FR-4 substrates due to their superior thermal and electrical properties.
- Complexity:The intricacy of the cavity design, number of steps, and complexity of the substrate layers affect manufacturing time and material usage, thereby influencing costs.
- Size and Thickness:Larger substrates or those requiring specific thicknesses may incur higher material and processing costs.
- Volume and Production Scale: Economies of scale apply, with larger production volumes generally lowering per-unit costs due to optimized manufacturing processes and bulk material purchasing.
- Additional Features:Optional features like advanced metallization techniques, specialized surface finishes, or encapsulation may add to the overall cost.
- Quality Standards:Compliance with stringent quality standards and reliability testing can contribute to higher costs but ensures product performance and longevity.
To provide a ballpark figure, Step Cavity Package Substrates typically range in cost from several dollars to tens of dollars per unit, depending on the above factors. For precise pricing, it’s advisable to consult with substrate manufacturers who can offer detailed quotes based on specific design requirements, volume, and material choices.
What is the Base Material for Step Cavity Package Substrates?
The base material for Step Cavity Package Substrates can vary depending on the specific application requirements and performance criteria. Common base materials used include:
- Ceramics (LTCC, HTCC):Low Temperature Co-Fired Ceramic (LTCC) and High Temperature Co-Fired Ceramic (HTCC) substrates are popular choices due to their excellent thermal conductivity, high mechanical strength, and compatibility with high-frequency applications. These ceramics are suitable for applications requiring robust thermal management and reliability.
- High-Performance Resins:Certain high-performance resins such as FR-4 (Flame Retardant-4), PTFE (Polytetrafluoroethylene), and other specialized resin systems are also used. They offer good electrical properties, mechanical stability, and are more cost-effective compared to ceramics.
- Metal Core Substrates:In some cases, metal core substrates (e.g., aluminum or copper) are utilized for Step Cavity Package Substrates, particularly for applications requiring efficient heat dissipation and structural rigidity.
Each base material has distinct advantages and is chosen based on factors like thermal conductivity requirements, electrical performance, mechanical durability, and cost considerations. The selection of the base material plays a critical role in determining the overall performance and reliability of Step Cavity Package Substrates in various electronic and high-tech applications.
Which Company Makes Step Cavity Package Substrates?
Step Cavity Package Substrates are typically manufactured by specialized electronic materials and manufacturing companies. For example, internationally renowned companies such as Murata, Kyocera, and TDK have deep technical expertise and market influence in producing high-performance ceramic substrates like LTCC and HTCC. These companies employ advanced manufacturing processes and technologies to provide critical base materials for high-frequency applications and reliability requirements in electronic devices.
In addition, companies focused on high-performance substrate manufacturing, such as Rogers Corporation in the United States, are also capable of producing Step Cavity Package Substrates. They are well-known for their materials used in high-frequency and microwave applications. These companies usually have global sales and technical support networks to meet customer demands worldwide.
As for our company, we are proud to announce that we have the capability to manufacture Step Cavity Package Substrates. We specialize in the research and manufacturing of advanced electronic materials, equipped with advanced production facilities and a skilled technical team dedicated to providing high-quality, high-performance electronic packaging solutions. Our manufacturing processes strictly adhere to international standards to ensure excellent performance in electrical characteristics, thermal management, and mechanical stability.
Our Step Cavity Package Substrates are suitable for high-end applications in telecommunications, automotive electronics, aerospace, and beyond. We offer customized design and production according to specific customer requirements. Whether it’s material selection, process optimization, or quality control, we uphold rigorous standards and innovative spirit to meet various customer needs and challenges.
What are the 7 Qualities of Good Customer Service?
The 7 qualities of good customer service are:
- Responsiveness:Promptly addressing customer inquiries, concerns, and requests demonstrates attentiveness and respect for their time.
- Empathy:Understanding and showing empathy towards customers’ perspectives and feelings builds rapport and trust.
- Communication:Clear and effective communication ensures that information is conveyed accurately and comprehensively.
- Knowledge:Having in-depth knowledge about products or services enables agents to provide accurate information and solutions.
- Problem-solving:Ability to resolve issues efficiently and effectively, demonstrating dedication to customer satisfaction.
- Professionalism:Maintaining a courteous and respectful demeanor in all interactions enhances the customer experience.
- Follow-up:Following up with customers to ensure their issues are fully resolved and they are satisfied shows commitment to service excellence.
FAQs
What are the benefits of using Step Cavity Package Substrates?
They offer improved performance, reduced package size, and enhanced thermal management.
What applications are suitable for Step Cavity Package Substrates?
They are suitable for high-performance electronic devices, including smartphones, tablets, and advanced computing systems.
How do Step Cavity Package Substrates compare to traditional substrates?
They provide better integration, improved thermal performance, and support for more complex designs.
What materials are used in Step Cavity Package Substrates?
Common materials include FR-4, BT epoxy, polyimide, and ceramics.
How are the cavities in Step Cavity Package Substrates created?
Cavities are typically created using laser drilling or precise etching techniques.
Can Step Cavity Package Substrates be customized?
Yes, they can be customized to meet specific design and performance requirements.
What quality control measures are in place for Step Cavity Package Substrates?
Rigorous testing and inspection processes are implemented to ensure high quality and reliability.