Semiconductor BGA Substrate Manufacturer
Semiconductor BGA Substrate Manufacturer,Semiconductor BGA Substrate is a vital component in semiconductor packaging, featuring a ball grid array (BGA) layout for integrated circuits. This substrate facilitates direct chip-to-board connections, optimizing space and enhancing electrical performance. Composed of multiple layers including insulating, metal, and conductor layers, Semiconductor BGA Substrates ensure reliable connections and efficient heat dissipation. They support high-density integration, enabling smaller form factors in electronic devices while maintaining reliability. Semiconductor BGA Substrates find applications in various industries, including telecommunications, automotive, and consumer electronics, where space-saving and performance are paramount. This technology drives advancements in semiconductor packaging, enabling sleek designs and improved functionality in electronic products.
What is Semiconductor BGA Substrate?
A Semiconductor BGA (Ball Grid Array) Substrate is a crucial component in semiconductor packaging technology. BGA substrates are used to mount and interconnect integrated circuits (ICs) within electronic devices. The BGA substrate acts as a platform for the ICs and provides electrical connections between the ICs and the rest of the device.
Here are some key points about semiconductor BGA substrates:
Mounting Platform: BGA substrates provide a stable and reliable mounting platform for semiconductor chips. The chips are typically attached to the substrate using wire bonding or flip-chip bonding techniques.
Electrical Connections: BGA substrates have a grid of solder balls or pads on the bottom side, which are used to create electrical connections between the semiconductor chips and the device’s printed circuit board (PCB). These connections allow signals to pass between the ICs and other components in the device.
Signal Integrity: BGA substrates are designed to maintain signal integrity by minimizing signal losses and noise. They may include features such as controlled impedance traces, signal vias, and ground planes to ensure reliable signal transmission.
Thermal Management: BGA substrates often incorporate features for thermal management to dissipate heat generated by the semiconductor chips. This can include thermal vias, heat spreaders, and thermal interface materials to improve heat dissipation and prevent overheating.
Materials: BGA substrates are typically made from materials with high thermal conductivity, such as ceramics or certain types of organic substrates. These materials provide mechanical stability and efficient heat dissipation, which are important for the reliable operation of semiconductor devices.
Overall, semiconductor BGA substrates play a critical role in the packaging and performance of integrated circuits in electronic devices, providing both mechanical support and electrical connectivity while managing thermal issues to ensure the reliability and functionality of the devices.
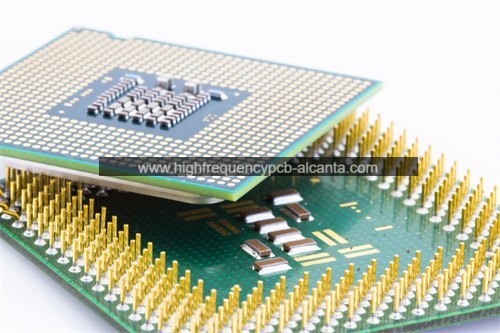
Semiconductor BGA Substrate Manufacturer
What are the Functions of Semiconductor BGA Substrate?
Semiconductor BGA (Ball Grid Array) substrates play several critical functions in electronic devices:
Mechanical Support: BGA substrates provide a stable and robust platform for mounting semiconductor chips (ICs) within electronic devices. They ensure that the chips are securely held in place and protected from physical damage during handling, assembly, and operation.
Electrical Interconnection: BGA substrates facilitate electrical connections between the semiconductor chips and the rest of the device’s circuitry. Solder balls or pads arranged in a grid pattern on the bottom of the substrate establish these connections. This allows signals to flow between the chips and other components, enabling the device to function properly.
Signal Routing: BGA substrates contain intricate patterns of conductive traces that route signals between the semiconductor chips and other parts of the device’s circuitry. These traces are designed to maintain signal integrity, minimize electromagnetic interference, and ensure that signals reach their intended destinations without degradation.
Power Distribution: BGA substrates distribute electrical power from the device’s power source to the semiconductor chips and other components. They incorporate power distribution networks comprising power planes, traces, and vias to deliver power efficiently and reliably, ensuring that all components receive the necessary power for proper operation.
Thermal Management: BGA substrates play a crucial role in managing the heat generated by the semiconductor chips during operation. They feature thermal vias, heat spreaders, and other thermal management elements to dissipate heat away from the chips and prevent overheating. Proper thermal management helps maintain the reliability and longevity of the semiconductor devices.
Integration of Passive Components: In some cases, BGA substrates may integrate passive components such as resistors, capacitors, or inductors directly onto the substrate itself. This integration reduces the footprint of the device’s circuitry, enhances performance, and simplifies the assembly process.
Overall, semiconductor BGA substrates are essential components in electronic devices, providing mechanical support, electrical interconnection, signal routing, power distribution, thermal management, and potential integration of passive components to ensure the functionality, reliability, and performance of the devices.
What are the Different Types of Semiconductor BGA Substrate?
There are several different types of semiconductor BGA (Ball Grid Array) substrates, each designed to meet specific requirements and performance characteristics. Some common types include:
Organic BGA Substrates: These substrates are made from organic materials such as epoxy resin or polyimide. Organic BGA substrates are lightweight, cost-effective, and offer good electrical properties. They are suitable for many applications but may have limitations in terms of heat dissipation compared to ceramic substrates.
Ceramic BGA Substrates: Ceramic BGA substrates are manufactured from materials like alumina (aluminum oxide) or aluminum nitride. These substrates offer excellent thermal conductivity, mechanical strength, and dimensional stability. Ceramic BGA substrates are often used in high-power applications or in environments where thermal management is critical.
Flex BGA Substrates: Flex BGA substrates are made from flexible materials such as polyimide or polyester. These substrates are bendable and can conform to irregular shapes, making them suitable for applications where space is limited or where flexibility is required. Flex BGA substrates are commonly used in portable electronic devices like smartphones and tablets.
Metal Core BGA Substrates: Metal core BGA substrates feature a metal core layer sandwiched between two insulating layers. The metal core provides excellent thermal conductivity, allowing for efficient heat dissipation. Metal core BGA substrates are often used in high-power LED lighting applications and other devices where thermal management is critical.
Composite BGA Substrates: Composite BGA substrates are made from a combination of different materials, such as fiberglass reinforced epoxy or ceramic-filled polymer. These substrates offer a balance of properties such as mechanical strength, thermal conductivity, and cost-effectiveness. Composite BGA substrates are used in a wide range of applications across various industries.
High-Frequency BGA Substrates: High-frequency BGA substrates are specifically designed to support high-speed, high-frequency signals with minimal signal loss and distortion. These substrates often feature specialized materials and manufacturing techniques optimized for high-frequency performance. They are commonly used in telecommunications, aerospace, and other industries where high-speed data transmission is crucial.
These are just a few examples of the different types of semiconductor BGA substrates available. The choice of substrate type depends on factors such as the application requirements, performance specifications, cost considerations, and manufacturing constraints.
How does Semiconductor BGA Substrate Relate to IC Packaging?
Semiconductor BGA (Ball Grid Array) substrates are an integral part of IC (Integrated Circuit) packaging. They serve as the foundation upon which semiconductor chips are mounted and interconnected within electronic devices. Here’s how semiconductor BGA substrates relate to IC packaging:
Mounting Platform: BGA substrates provide a stable platform for mounting semiconductor chips. These chips are typically attached to the substrate using wire bonding or flip-chip bonding techniques. The substrate ensures that the chips are securely held in place and protected from mechanical stresses.
Electrical Interconnection: BGA substrates facilitate electrical connections between the semiconductor chips and the rest of the device’s circuitry. Solder balls or pads on the bottom of the substrate establish these connections, allowing signals to pass between the chips and other components.
Signal Routing: BGA substrates contain intricate patterns of conductive traces that route signals between the semiconductor chips and other parts of the device’s circuitry. These traces ensure that signals reach their intended destinations without degradation, maintaining signal integrity throughout the system.
Power Distribution: BGA substrates distribute electrical power from the device’s power source to the semiconductor chips and other components. They incorporate power distribution networks comprising power planes, traces, and vias to deliver power efficiently and reliably to all components.
Thermal Management: BGA substrates play a crucial role in managing the heat generated by the semiconductor chips during operation. They feature thermal management elements such as thermal vias, heat spreaders, and thermal interface materials to dissipate heat away from the chips and prevent overheating.
Integration of Passive Components: In some cases, BGA substrates may integrate passive components such as resistors, capacitors, or inductors directly onto the substrate itself. This integration reduces the footprint of the device’s circuitry and simplifies the assembly process.
Overall, semiconductor BGA substrates are essential components in IC packaging, providing mechanical support, electrical interconnection, signal routing, power distribution, thermal management, and potential integration of passive components to ensure the functionality, reliability, and performance of electronic devices. They form a critical link between semiconductor chips and the rest of the device’s circuitry, enabling the proper operation of integrated circuits in various applications.
What are the Differences Between Semiconductor BGA Substrate and PCB?
Semiconductor BGA (Ball Grid Array) substrates and PCBs (Printed Circuit Boards) are both essential components in electronic devices, but they serve different purposes and have distinct characteristics. Here are some key differences between them:
Function:
Semiconductor BGA Substrate: BGA substrates primarily serve as a mounting and interconnection platform for semiconductor chips (ICs) within electronic devices. They provide mechanical support, electrical connections, signal routing, power distribution, and thermal management for the ICs.
PCB: PCBs are the main structural and electrical backbone of electronic devices. They provide a platform for mounting and interconnecting various electronic components, including ICs, resistors, capacitors, and connectors. PCBs facilitate electrical connections between components and support the functionality of the entire device.
Component Mounting:
Semiconductor BGA Substrate: BGA substrates are specifically designed to mount and interconnect semiconductor chips. They typically feature solder balls or pads arranged in a grid pattern on the bottom side to facilitate the attachment of ICs.
PCB: PCBs accommodate the mounting of various electronic components, including ICs, using soldering, surface-mounting, or through-hole mounting techniques. Components are typically mounted on the surface of the PCB or inserted into pre-drilled holes and soldered in place.
Complexity:
Semiconductor BGA Substrate: BGA substrates tend to have a simpler and more focused design, tailored specifically for mounting and interconnecting semiconductor chips. They may incorporate advanced features for signal routing, power distribution, and thermal management, but their primary function is to support ICs.
PCB: PCBs can be highly complex, with multiple layers of conductive traces and components mounted on both sides. They accommodate a wide range of electronic components and support complex circuit designs, including signal processing, power regulation, and communication functions.
Materials:
Semiconductor BGA Substrate: BGA substrates are often made from materials with high thermal conductivity, such as ceramics or certain types of organic substrates. These materials provide mechanical stability and efficient heat dissipation, which are crucial for semiconductor devices.
PCB: PCBs can be made from a variety of materials, including fiberglass-reinforced epoxy (FR-4), polyimide, and metal-core laminates. The choice of material depends on factors such as cost, electrical performance, mechanical strength, and thermal properties.
Application:
Semiconductor BGA Substrate: BGA substrates are primarily used in semiconductor packaging applications, where they provide the necessary support and connectivity for ICs in electronic devices such as smartphones, computers, and consumer electronics.
PCB: PCBs are used in a wide range of electronic devices and systems, including computers, smartphones, televisions, automotive electronics, industrial equipment, and medical devices. They serve as the foundation for electronic circuits and enable the functionality of these devices.
Overall, while both semiconductor BGA substrates and PCBs are crucial components in electronic devices, they have different functions, designs, and applications, tailored to the specific requirements of semiconductor packaging and electronic circuitry, respectively.
What are the Main Structures and Production Technologies of Semiconductor BGA Substrate?
The main structures and production technologies of semiconductor BGA (Ball Grid Array) substrates can vary depending on the specific requirements of the application and the materials used. However, here are some common structures and production technologies:
Substrate Material:
Organic Materials: Organic BGA substrates are often made from materials such as epoxy resin or polyimide. These materials are lightweight, cost-effective, and offer good electrical properties.
Ceramic Materials: Ceramic BGA substrates are manufactured from materials like alumina (aluminum oxide) or aluminum nitride. They offer excellent thermal conductivity, mechanical strength, and dimensional stability.
Layer Structure:
Single-Layer: Simple BGA substrates may consist of a single layer of substrate material with conductive traces and pads on one side.
Multilayer: More complex BGA substrates may feature multiple layers of substrate material, with conductive traces and vias connecting different layers. Multilayer substrates allow for greater design flexibility and higher routing density.
Conductive Traces and Pads:
Etched Copper Traces: Conductive traces are typically made from copper and are etched onto the substrate surface using lithography and chemical etching processes.
Solder Pads or Balls: BGA substrates feature solder pads or balls on the bottom side, which are used to establish electrical connections with the device’s printed circuit board (PCB).
Via Formation:
Plated Through-Hole Vias: Vias are holes drilled through the substrate material and then plated with conductive material to establish electrical connections between different layers of the substrate.
Blind and Buried Vias: In some cases, BGA substrates may incorporate blind vias (which connect only one or more inner layers) or buried vias (which are completely enclosed within the substrate) to reduce signal interference and routing complexity.
Solder Mask and Surface Finish:
Solder Mask: A solder mask layer is applied to the substrate surface to insulate conductive traces and prevent solder bridges during assembly. The solder mask is typically applied using a screen printing process.
Surface Finish: The surface of BGA substrates is often finished with a layer of conductive material to facilitate soldering. Common surface finishes include electroless nickel immersion gold (ENIG), hot air solder leveling (HASL), and immersion tin or silver.
Thermal Management Features:
Thermal Vias: BGA substrates may incorporate thermal vias to improve heat dissipation and thermal management. These vias allow heat to flow away from the semiconductor chips and into the surrounding substrate material.
Heat Spreaders: In some cases, BGA substrates may feature integrated heat spreaders or heat sinks to further enhance thermal performance.
Overall, the production technologies of semiconductor BGA substrates involve a combination of materials processing, lithography, etching, drilling, plating, and surface finishing techniques to create complex structures with precise electrical and thermal properties. The specific production processes used depend on factors such as substrate material, design requirements, and manufacturing capabilities.
Frequently Asked Questions (FAQs)
What is a BGA substrate?
A BGA substrate is a component used in semiconductor packaging to mount and interconnect integrated circuits (ICs) within electronic devices. It provides mechanical support, electrical connections, signal routing, power distribution, and thermal management for the ICs.
What are the main functions of a BGA substrate?
The main functions of a BGA substrate include providing mechanical support for semiconductor chips, facilitating electrical connections between the chips and other components, routing signals between different parts of the device’s circuitry, distributing power to the chips, and managing heat generated by the chips during operation.
What materials are BGA substrates made of?
BGA substrates can be made from various materials, including organic materials such as epoxy resin or polyimide, ceramic materials such as alumina or aluminum nitride, and composite materials. The choice of material depends on factors such as thermal conductivity, mechanical strength, and cost.
What production technologies are used to manufacture BGA substrates?
The production technologies used to manufacture BGA substrates include materials processing, lithography, etching, drilling, plating, and surface finishing techniques. These processes are used to create complex structures with precise electrical and thermal properties.
What are the advantages of using BGA substrates in semiconductor packaging?
Some advantages of using BGA substrates include improved electrical performance, higher routing density, better thermal management, and reduced package size compared to other packaging technologies such as quad flat packages (QFP) or dual in-line packages (DIP).
What are some common applications of BGA substrates?
BGA substrates are used in a wide range of electronic devices and systems, including smartphones, computers, tablets, automotive electronics, medical devices, and telecommunications equipment. They are particularly well-suited for high-performance and space-constrained applications.
What factors should be considered when selecting a BGA substrate for a specific application?
Factors to consider when selecting a BGA substrate include material properties (such as thermal conductivity and dielectric constant), electrical performance (such as impedance control and signal integrity), mechanical strength, cost, and compatibility with assembly and manufacturing processes.
Conclusion
In conclusion, semiconductor BGA (Ball Grid Array) substrates are crucial components in electronic devices, providing essential functions such as mechanical support, electrical interconnection, signal routing, power distribution, and thermal management for semiconductor chips. They serve as the foundation upon which integrated circuits are mounted and interconnected within electronic systems, enabling the functionality, reliability, and performance of these devices.
BGA substrates come in various types, structures, and materials, each tailored to meet specific requirements and performance characteristics. They are manufactured using advanced production technologies involving materials processing, lithography, etching, drilling, plating, and surface finishing techniques to create complex structures with precise electrical and thermal properties.
Overall, semiconductor BGA substrates play a vital role in semiconductor packaging, enabling the miniaturization, high performance, and reliability of electronic devices across a wide range of applications. Their continued development and optimization are essential for driving innovation and meeting the evolving needs of the electronics industry.