Rogers 4003C PCB Manufacturing
Rogers 4003C PCB Manufacturing,Rogers 4003C PCBs represent the pinnacle of high-frequency circuit board technology. Engineered using Rogers Corporation’s RO4003C laminate material, these PCBs offer unparalleled performance in RF and microwave applications. With a low dielectric constant and minimal dissipation factor, they ensure exceptional signal integrity and reduced loss, critical for maintaining precise impedance control. Rogers 4003C PCBs are renowned for their reliability and consistency across a wide frequency spectrum, making them the preferred choice for demanding electronic systems such as antennas, radar systems, and high-speed digital circuits. Their superior thermal stability and robust construction further enhance their suitability for aerospace, telecommunications, and other mission-critical applications. Whether it’s for cutting-edge research or commercial deployment, Rogers 4003C PCBs empower engineers with the tools they need to push the boundaries of high-frequency electronics.
What is a Rogers 4003C PCB?
The Rogers 4003C PCB (Printed Circuit Board) refers to a type of circuit board manufactured using Rogers Corporation’s high-frequency laminate material known as RO4003C. Rogers Corporation is a leading manufacturer of advanced materials for various industries, including electronics.
RO4003C is a thermoset laminate material specifically designed for high-frequency applications. It offers excellent electrical properties, such as low dielectric constant (εr) and low dissipation factor (Df), making it suitable for RF (Radio Frequency) and microwave circuits where signal integrity is crucial.
The Rogers 4003C PCBs are often used in applications such as RF amplifiers, antennas, high-frequency communication systems, radar systems, and other demanding electronic applications where performance at high frequencies is essential. These PCBs are known for their high reliability, excellent signal integrity, and consistent performance across a wide range of frequencies.
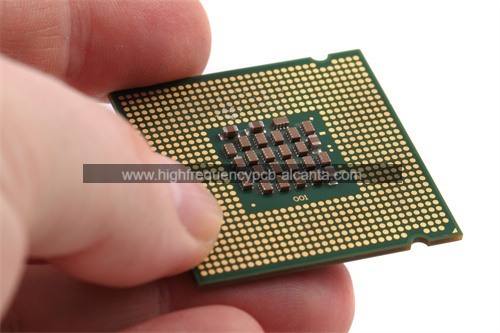
Rogers 4003C PCB Manufacturing
What are the Rogers 4003C PCB Design Guidelines?
Designing with Rogers 4003C PCBs requires adherence to specific guidelines to ensure optimal performance. Here are some general design guidelines for Rogers 4003C PCBs:
- Dielectric Constant (εr): Understand the dielectric constant of RO4003C (approximately 3.38 ± 0.05) and consider it in your impedance calculations.
- Signal Integrity: Ensure controlled impedance matching for signal integrity. Design transmission lines with appropriate widths and separations to achieve the desired impedance.
- Copper Thickness: Select the appropriate copper thickness based on your design requirements and manufacturing capabilities. Typical copper thicknesses range from 0.5 oz to 2 oz per square foot.
- Copper Weight Balance: Maintain copper weight balance on each layer to prevent warping or twisting of the board during fabrication.
- Layer Stackup: Design an appropriate layer stackup considering the number of signal layers, power planes, and ground planes required for your application.
- Via Design: Optimize via design for minimal impedance disruption. Use appropriate via structures such as plated-through vias (PTH) or microvias depending on the frequency and density of your design.
- Thermal Considerations: Account for thermal management by placing thermal relief pads for vias connected to thermal planes and considering the overall heat dissipation requirements of your design.
- Component Placement: Carefully place components to minimize signal path lengths and avoid routing sensitive traces near high-speed connectors, high-frequency components, or noisy components.
- Routing Guidelines: Follow best practices for routing high-speed signals, such as maintaining consistent trace widths, avoiding sharp bends, and minimizing crosstalk between adjacent traces.
- Grounding:Implement a solid ground plane for effective grounding, minimizing ground loops and providing a low impedance return path for signals.
- Solder Mask and Silkscreen: Ensure proper solder mask coverage and silkscreen markings to prevent solder bridges and aid in component placement and identification.
- Manufacturability: Design with manufacturability in mind, considering the capabilities of your chosen fabrication and assembly processes.
By following these guidelines and consulting with Rogers Corporation or experienced PCB designers, you can effectively design and fabricate PCBs using Rogers 4003C material while optimizing performance and reliability for your specific application.
What is the Rogers 4003C PCB Fabrication Process?
The fabrication process for Rogers 4003C PCBs involves several steps, similar to the fabrication of other printed circuit boards. Here’s an overview of the typical process:
- Preparation of Design Files: The process begins with the preparation of design files using PCB design software. These files include the PCB layout, Gerber files, drill files, and other necessary documentation.
- Material Selection: Choose Rogers 4003C laminate material for the PCB based on the specific requirements of the application. Ensure that the material thickness matches the design specifications.
- Layer Stackup Design: Design the layer stackup of the PCB considering the number of layers required for the circuit design, signal integrity, and impedance control. The layer stackup defines the arrangement of copper layers, prepreg layers, and core materials.
- Preparation of Substrate Materials: Cut the Rogers 4003C laminate material into appropriate panel sizes based on the PCB layout and layer stackup design.
- Cleaning and Surface Preparation: Clean the substrate materials to remove any contaminants and ensure proper adhesion of the copper foil during lamination. Surface preparation may involve processes such as degreasing and chemical treatment.
- Copper Cladding: Apply copper foil to both sides of the substrate material using lamination or bonding processes. The copper foil thickness should match the design requirements.
- Drilling: Drill holes for vias and component mounting using CNC (Computer Numerical Control) drilling machines. Ensure precise hole alignment and size accuracy.
- Copper Plating: Plate the drilled holes with copper to create electrical connections between layers. This process may involve electroplating or other methods to deposit copper uniformly.
- Outer Layer Imaging: Apply a photosensitive resist material to the outer copper layers and expose them to UV light through a photomask with the PCB layout pattern. Develop and etch the exposed copper to create the circuit traces.
- Inner Layer Imaging: Repeat the imaging and etching process for the inner copper layers of the PCB.
- Lamination: Assemble the PCB layers together with prepreg layers and laminate them under heat and pressure to form a solid structure. This process bonds the layers together and ensures proper insulation between them.
- Solder Mask Application: Apply solder mask over the PCB surface to insulate the copper traces and protect them from oxidation. Define openings for solder pads, vias, and other exposed areas.
- Silkscreen Printing: Print component outlines, reference designators, and other markings on the PCB surface using a silkscreen printing process. This aids in component placement and identification.
- Surface Finish: Apply surface finish to the exposed copper surfaces to improve solderability and protect against oxidation. Common surface finishes include HASL (Hot Air Solder Leveling), ENIG (Electroless Nickel Immersion Gold), and OSP (Organic Solderability Preservative).
- Quality Inspection: Conduct visual inspection, electrical testing, and other quality control checks to ensure the PCBs meet the required specifications and standards.
- Routing and Profiling: Cut the panelized PCBs into individual boards using routing or scoring methods. Remove any excess material and smooth the edges to achieve the final PCB shape.
- Final Inspection and Packaging: Perform a final inspection to verify the quality of the finished PCBs before packaging them for shipping or assembly.
Overall, the fabrication process for Rogers 4003C PCBs involves a series of precise and controlled steps to produce high-quality circuit boards with excellent performance characteristics for high-frequency applications.
How do you manufacture a Rogers 4003C PCB?
Manufacturing a Rogers 4003C PCB involves a series of steps that are similar to the fabrication process of other printed circuit boards (PCBs), but with specific considerations due to the high-frequency properties of the Rogers 4003C material. Here’s a general outline of the manufacturing process:
- Preparation of Design Files: Develop the PCB design using CAD (Computer-Aided Design) software. This includes creating the PCB layout, generating Gerber files, and preparing drill files.
- Material Selection: Choose Rogers 4003C laminate material based on the specific requirements of the PCB design. Consider factors such as dielectric constant, thickness, and substrate properties.
- Panel Preparation: Cut the Rogers 4003C laminate material into panels of appropriate sizes. Ensure cleanliness and flatness of the panels to facilitate subsequent manufacturing processes.
- Copper Foil Application: Apply copper foil to both sides of the Rogers 4003C panels using a lamination process. The copper foil thickness should match the design requirements.
- Drilling: Use CNC (Computer Numerical Control) drilling machines to drill holes for vias and component mounting pads. Ensure precise hole placement and size accuracy.
- Copper Plating: Plate the drilled holes with copper to create electrical connections between layers. This process may involve electroplating or other methods to deposit copper uniformly.
- Outer Layer Imaging: Apply a photosensitive resist material to the outer copper layers and expose them to UV light through a photomask with the PCB layout pattern. Develop and etch the exposed copper to create the circuit traces.
- Inner Layer Imaging: Repeat the imaging and etching process for the inner copper layers of the PCB.
- Layer Alignment: Align the inner and outer layers of the PCB stackup to ensure proper registration of circuit traces and vias.
- Lamination: Assemble the PCB layers together with prepreg layers and laminate them under heat and pressure. This process bonds the layers together and ensures proper insulation between them.
- Solder Mask Application: Apply solder mask over the PCB surface to insulate the copper traces and protect them from oxidation. Define openings for solder pads, vias, and other exposed areas.
- Silkscreen Printing: Print component outlines, reference designators, and other markings on the PCB surface using a silkscreen printing process. This aids in component placement and identification.
- Surface Finish: Apply surface finish to the exposed copper surfaces to improve solderability and protect against oxidation. Common surface finishes include HASL (Hot Air Solder Leveling), ENIG (Electroless Nickel Immersion Gold), and OSP (Organic Solderability Preservative).
- Testing and Inspection: Perform electrical testing, visual inspection, and other quality control checks to ensure the PCBs meet the required specifications and standards.
- Routing and Profiling: Cut the panelized PCBs into individual boards using routing or scoring methods. Remove any excess material and smooth the edges to achieve the final PCB shape.
- Final Inspection and Packaging: Conduct a final inspection to verify the quality of the finished PCBs before packaging them for shipping or assembly.
Throughout the manufacturing process, it’s essential to follow best practices and guidelines specific to Rogers 4003C material to ensure the final PCBs meet the desired performance and reliability requirements for high-frequency applications.
How much should a Rogers 4003C PCB cost?
The cost of a Rogers 4003C PCB can vary significantly depending on several factors, including the following:
- Size and Complexity: Larger and more complex PCBs typically require more material and fabrication time, resulting in higher costs.
- Layer Count: The number of layers in the PCB affects fabrication complexity and material usage. Rogers 4003C PCBs can range from single-layer to multi-layer configurations.
- Material Costs: Rogers 4003C laminate material tends to be more expensive compared to standard FR-4 material due to its high-frequency properties and performance characteristics.
- Surface Finish and Special Features: Additional features such as special surface finishes (e.g., ENIG, immersion silver) and advanced fabrication techniques (e.g., controlled impedance, blind/buried vias) can increase the cost.
- Quantity: Larger quantities typically result in lower per-unit costs due to economies of scale in manufacturing.
- Turnaround Time: Expedited production schedules may incur additional costs compared to standard lead times.
- Supplier and Location: PCB fabrication costs can vary between different suppliers and geographic regions based on factors such as labor rates, overhead costs, and market demand.
To get an accurate cost estimate for a Rogers 4003C PCB, it’s recommended to contact multiple PCB manufacturers or suppliers and provide them with detailed specifications of your design, including dimensions, layer count, material requirements, surface finish, and quantity. They can then provide you with customized quotes based on your specific requirements. Additionally, online PCB fabrication cost calculators offered by some manufacturers can provide ballpark estimates based on certain parameters you input.
What is the Rogers 4003C PCB base material?
The base material of Rogers 4003C PCBs is a high-frequency laminate known as RO4003C. RO4003C is a thermoset laminate material specifically designed for high-frequency applications, particularly in the RF (Radio Frequency) and microwave frequency ranges.
RO4003C laminate material is composed of a woven fiberglass reinforcement impregnated with a ceramic-filled, flame-retardant thermoset resin. This composition provides excellent electrical properties, including low dielectric constant (εr) and low dissipation factor (Df), which are crucial for maintaining signal integrity in high-frequency circuits.
The RO4003C material has a relatively low loss tangent (tanδ), which means it exhibits minimal signal attenuation, making it suitable for applications where signal loss needs to be minimized.
Overall, Rogers 4003C PCBs utilize RO4003C laminate material as the base substrate, offering high-performance characteristics ideal for demanding high-frequency electronic applications.
Which company makes Rogers 4003C PCBs?
Rogers 4003C PCBs are manufactured by Rogers Corporation. Rogers Corporation is a globally renowned materials technology company, specializing in the development and production of various advanced materials, including high-performance laminates used in electronics, communications, automotive, aerospace, and other industries. Its RO4003C laminate material is the preferred choice for high-frequency circuit designs, offering excellent electrical properties and stability to meet the requirements of high-frequency RF applications.
Our company is also capable of producing Rogers 4003C PCBs, providing customers with high-quality customized solutions. With advanced manufacturing equipment and a skilled technical team, we can produce according to customers’ specific requirements, ensuring that the product quality and performance meet the highest standards. We prioritize customer needs, offering professional technical support and excellent service to meet various demands for Rogers 4003C PCBs.
Our production process strictly adheres to quality management standards and continuously improves and optimizes to ensure that the manufactured Rogers 4003C PCBs meet customer expectations and achieve high-quality standards. We are willing to cooperate with customers, explore solutions together, and provide the best technical support and product services for their projects.
What are the 7 qualities of good customer service?
Good customer service is characterized by several key qualities that contribute to a positive experience for customers. Here are seven qualities of good customer service:
- Responsiveness: Good customer service involves being prompt and timely in addressing customer inquiries, concerns, and requests. Customers appreciate quick responses, whether it’s answering questions, resolving issues, or providing assistance.
- Empathy: Empathy is the ability to understand and share the feelings of customers. Good customer service representatives listen actively, show genuine concern for customers’ needs, and demonstrate empathy in their interactions. This helps build trust and rapport with customers.
- Clarity and Communication: Effective communication is essential for good customer service. Customer service representatives should communicate clearly, using language that is easy to understand. They should provide accurate information, instructions, and updates to customers, avoiding jargon or technical terms whenever possible.
- Problem-Solving Skills: Good customer service involves having strong problem-solving skills to address customers’ issues and concerns effectively. Customer service representatives should be resourceful, proactive, and capable of finding solutions to resolve problems promptly and satisfactorily.
- Professionalism: Professionalism encompasses various aspects of behavior, including courtesy, respect, and integrity. Customer service representatives should maintain a professional demeanor at all times, treating customers with respect and courtesy, and upholding ethical standards in their interactions.
- Flexibility and Adaptability: Good customer service requires flexibility and adaptability to accommodate customers’ diverse needs and preferences. Customer service representatives should be willing to adjust their approach, policies, or procedures to meet customers’ expectations and ensure a positive experience.
- Follow-Up and Feedback: Following up with customers after resolving their issues or completing a transaction demonstrates commitment to customer satisfaction. Good customer service involves seeking feedback from customers, whether through surveys, reviews, or direct communication, to continuously improve service quality and address areas for enhancement.
By embodying these qualities, businesses can deliver exceptional customer service that fosters loyalty, satisfaction, and positive relationships with customers.
FAQs
What is Rogers 4003C PCB?
Rogers 4003C PCB refers to a printed circuit board manufactured using Rogers Corporation’s high-frequency laminate material known as RO4003C. It is designed for high-frequency applications, offering excellent electrical properties.
What are the key features of Rogers 4003C PCB?
The key features include low dielectric constant (εr), low dissipation factor (Df), minimal signal loss, high thermal stability, and reliable performance at high frequencies.
What are the applications of Rogers 4003C PCBs?
Rogers 4003C PCBs are commonly used in RF (Radio Frequency) and microwave circuits, high-speed digital applications, antennas, radar systems, aerospace, telecommunications, and other demanding electronic applications.
What are the advantages of using Rogers 4003C PCBs?
The advantages include superior signal integrity, minimal loss tangent, consistent performance across a wide frequency range, excellent thermal management, and high reliability.
How do Rogers 4003C PCBs differ from standard FR-4 PCBs?
Rogers 4003C PCBs offer superior performance at high frequencies compared to standard FR-4 PCBs. They have lower dielectric constant and loss tangent, which results in reduced signal loss and better impedance control.
What are the design considerations for Rogers 4003C PCBs?
Design considerations include controlled impedance matching, proper layer stackup design, optimized via design, thermal management, component placement for signal integrity, and adherence to Rogers 4003C material specifications.
Where can I find reliable suppliers for Rogers 4003C PCBs?
Reliable suppliers of Rogers 4003C PCBs can be found through online directories, industry trade shows, recommendations from peers, or by directly contacting PCB manufacturers who specialize in high-frequency materials and technologies.