Open Multi-step Cavity PCB Manufacturer
Open Multi-step Cavity PCB Manufacturer,Open multi-step cavity PCBs represent a sophisticated evolution in printed circuit board design, meticulously crafted to meet the demands of high-frequency electronic applications. Featuring intricate layering and precisely engineered cavities within the substrate, these PCBs offer unparalleled performance in signal integrity, thermal management, and electromagnetic interference (EMI) reduction. By strategically placing cavities and adjusting layer thicknesses, Open multi-step cavity PCBs achieve optimal impedance control, ensuring seamless transmission of high-speed signals. This advanced design not only enhances the reliability and efficiency of electronic devices but also enables them to operate in challenging environments with minimal interference. From telecommunications infrastructure to aerospace electronics, Open multi-step cavity PCBs empower cutting-edge technologies with their ability to deliver consistent, high-performance solutions. Embodying a fusion of precision engineering and innovative design, these PCBs represent the pinnacle of modern electronic manufacturing, setting new standards for reliability and functionality in high-frequency applications.
What is an Open multi-step cavity PCB?
An Open multi-step cavity PCB is a type of printed circuit board (PCB) design that incorporates multiple layers and steps within its construction. This design is often utilized in high-frequency applications where signal integrity, impedance control, and thermal management are critical.
The “open” aspect refers to the presence of cavities or cutouts within the PCB substrate, which can be strategically placed to reduce electromagnetic interference (EMI) and crosstalk between different signal traces. These cavities also aid in thermal dissipation, allowing for better heat management, which is crucial in electronic devices with high power densities.
The “multi-step” feature indicates that the PCB has multiple layers with different heights or thicknesses, creating a stepped structure. This design helps to control impedance by matching the electrical properties of transmission lines, such as microstrips or striplines, to the required specifications. By adjusting the thickness and spacing of these layers, engineers can achieve precise impedance matching for high-speed signal transmission.
Overall, an Open multi-step cavity PCB offers advantages in terms of signal integrity, EMI reduction, thermal performance, and impedance control, making it suitable for applications such as high-speed data communication, wireless devices, radar systems, and advanced electronics where reliability and performance are paramount.
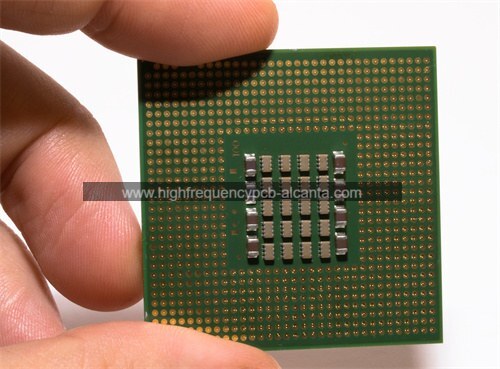
Open Multi-step Cavity PCB Manufacturer
What are the Open multi-step cavity PCB Design Guidelines?
Designing an Open multi-step cavity PCB requires careful consideration of several key guidelines to ensure optimal performance. Here are some important design guidelines:
- Cavity Placement: Strategically place cavities within the PCB to minimize electromagnetic interference (EMI) and crosstalk between adjacent signal traces. Consider the location of high-speed signal paths and sensitive components when determining cavity placement.
- Cavity Dimensions: Design cavities with appropriate dimensions to achieve the desired EMI shielding and thermal dissipation properties. The dimensions should be calculated based on the wavelength of the signals and the desired level of attenuation.
- Layer Stackup: Plan a layer stackup that includes multiple layers with different thicknesses to create the stepped structure required for impedance control. Ensure that signal traces are routed on layers with consistent impedance characteristics to maintain signal integrity.
- Impedance Matching: Use controlled impedance routing techniques to match the impedance of transmission lines (e.g., microstrips, striplines) to the characteristic impedance of the PCB substrate. Adjust the width, spacing, and layer thickness to achieve the desired impedance values.
- Grounding: Implement a solid ground plane on one or more layers of the PCB to provide a low-impedance return path for signals and reduce ground bounce. Ensure that ground vias are placed strategically to minimize ground loops and impedance discontinuities.
- Thermal Management: Incorporate thermal vias and heat sinks into the design to facilitate heat dissipation from components and cavities. Distribute thermal vias evenly across the PCB to ensure uniform temperature distribution.
- Signal Integrity: Follow best practices for high-speed signal routing, such as minimizing signal traces’ length, avoiding sharp bends, and maintaining consistent trace widths. Use signal integrity simulation tools to analyze and optimize signal paths for minimal loss and distortion.
- Manufacturability: Consider manufacturability constraints when designing the PCB, such as minimum feature sizes, spacing requirements, and material limitations. Work closely with the PCB manufacturer to ensure that the design can be fabricated reliably and cost-effectively.
By adhering to these design guidelines, engineers can create Open multi-step cavity PCBs that meet the stringent requirements of high-frequency applications while ensuring robust performance and reliability.
What is the Open multi-step cavity PCB Fabrication Process?
The fabrication process for Open multi-step cavity PCBs involves several steps, each crucial for ensuring the final product meets design specifications and performance requirements. Here’s an overview of the fabrication process:
- Design Preparation: Start by preparing the PCB design using a computer-aided design (CAD) software. This includes defining the layer stackup, cavity placement, routing of signal traces, and other design elements according to the project requirements.
- Material Selection: Choose appropriate substrate materials with properties suitable for high-frequency applications and thermal management. Common materials include high-frequency laminates like FR-4, Rogers, or PTFE-based substrates.
- Layer Stackup Design: Design the layer stackup to incorporate multiple layers with varying thicknesses to create the stepped structure required for impedance control and cavity formation.
- Cavity Formation: Use precision milling or routing techniques to create cavities within the PCB substrate according to the design specifications. The cavities are typically created by removing material from specific layers using CNC machines.
- Copper Plating: Apply copper plating to the inner layers of the PCB to form the conductive traces and planes. This process involves cleaning the substrate, applying a layer of copper through electroplating, and then etching away excess copper to define the circuit traces.
- Through-Hole Plating: Drill holes for vias and through-hole components, and then plate the holes with copper to create electrical connections between different layers of the PCB.
- Lamination: Assemble the layers of the PCB stackup using heat and pressure to bond them together into a single rigid structure. This process, known as lamination, ensures proper alignment of layers and electrical continuity between them.
- Circuit Patterning: Apply a layer of photoresist material to the outer layers of the PCB and then use photolithography to define the circuit patterns. The exposed areas of the photoresist are removed, allowing for the selective etching of copper to form the final circuit traces.
- Surface Finishing: Apply surface finish coatings to protect the exposed copper surfaces and improve solderability. Common surface finishes include HASL (Hot Air Solder Leveling), ENIG (Electroless Nickel Immersion Gold), and OSP (Organic Solderability Preservatives).
- Final Inspection: Perform thorough inspection and testing of the finished PCB to ensure that it meets quality standards and design specifications. This may include electrical testing, dimensional measurements, and visual inspection.
- Assembly: Once the PCBs pass inspection, they can be assembled with electronic components using soldering techniques such as reflow soldering or wave soldering.
By following these steps carefully, manufacturers can produce high-quality Open multi-step cavity PCBs that meet the demanding requirements of high-frequency electronic applications.
How do you manufacture an Open multi-step cavity PCB?
Manufacturing an Open multi-step cavity PCB involves a specialized process due to its complex design requirements. Here’s a detailed overview of the manufacturing process:
- Design Preparation: Begin by creating a detailed design of the Open multi-step cavity PCB using CAD software. This involves defining the layer stackup, cavity dimensions, signal routing, and other critical aspects of the design.
- Material Selection: Choose appropriate substrate materials that meet the specific requirements of the application, such as high-frequency laminates with low dielectric loss and excellent thermal conductivity.
- Layer Stackup Design: Design the layer stackup with multiple layers, each with varying thicknesses to create the stepped structure necessary for impedance control and cavity formation. Ensure that the stackup configuration aligns with the design specifications.
- Cavity Formation: Use precision machining techniques such as milling or routing to create cavities within the PCB substrate according to the design specifications. These cavities help reduce electromagnetic interference (EMI) and improve thermal management.
- Copper Plating: Apply a thin layer of copper to the inner layers of the PCB through processes like electroless copper deposition or electroplating. This copper layer forms the conductive traces and planes of the PCB.
- Through-Hole Plating: Drill holes for vias and through-hole components using specialized drilling equipment. After drilling, the holes are plated with copper to establish electrical connections between different layers of the PCB.
- Circuit Patterning: Apply a layer of photoresist to the outer layers of the PCB and use photolithography to define the circuit patterns. The exposed areas of the photoresist are then removed, allowing for selective etching of copper to form the final circuit traces.
- Surface Finishing: Apply surface finish coatings to protect the exposed copper surfaces and improve solderability. Common surface finishes include HASL (Hot Air Solder Leveling), ENIG (Electroless Nickel Immersion Gold), and OSP (Organic Solderability Preservatives).
- Lamination: Assemble the layers of the PCB stackup using heat and pressure to bond them together into a single rigid structure. This process ensures proper alignment of layers and electrical continuity between them.
- Final Inspection: Conduct thorough inspection and testing of the finished PCB to verify that it meets quality standards and design specifications. This may include electrical testing, dimensional measurements, and visual inspection.
- Assembly: Once the PCBs pass inspection, they can be assembled with electronic components using soldering techniques such as reflow soldering or wave soldering.
Manufacturing an Open multi-step cavity PCB requires expertise in advanced PCB fabrication techniques and specialized equipment to ensure the precise implementation of the design specifications. Collaboration between design engineers and manufacturing specialists is essential to achieve the desired performance and reliability.
How much should an Open multi-step cavity PCB cost?
The cost of an Open multi-step cavity PCB can vary widely depending on several factors such as:
- Complexity of Design: More complex designs with intricate cavity structures, multiple layers, and tight tolerances will generally incur higher manufacturing costs.
- Material Selection: High-quality substrate materials with specific properties for high-frequency applications and thermal management may be more expensive than standard PCB materials.
- Layer Count:PCBs with a higher number of layers will typically be more expensive due to increased material and manufacturing complexity.
- Surface Finish: The choice of surface finish can impact the cost, with options like ENIG (Electroless Nickel Immersion Gold) generally being more expensive than HASL (Hot Air Solder Leveling) or OSP (Organic Solderability Preservatives).
- Production Volume: Larger production volumes often result in lower per-unit costs due to economies of scale, while prototypes or small batch runs may have higher costs per unit.
- Manufacturing Process: Specialized manufacturing processes such as precision milling or routing for cavity formation may add to the overall cost.
- Additional Services: Extra services such as electrical testing, impedance control verification, and conformal coating application can contribute to the total cost.
As a rough estimate, the cost of an Open multi-step cavity PCB can range from tens to hundreds or even thousands of dollars per board, depending on the aforementioned factors.
What is the Open multi-step cavity PCB base material?
The base material used for Open multi-step cavity PCBs is typically selected based on the specific requirements of the application, such as high-frequency performance, thermal management, and mechanical stability. Some common base materials used for these PCBs include:
- High-Frequency Laminates: These laminates are specifically designed for high-frequency applications and offer low dielectric constant (Dk) and low dissipation factor (Df). Examples include materials from manufacturers like Rogers Corporation, Isola Group, and Taconic Advanced Dielectric Division.
- PTFE-Based Materials: Polytetrafluoroethylene (PTFE) based substrates, such as those used in RF and microwave applications, offer excellent electrical properties, including low loss tangent and high thermal stability.
- Ceramic-Based Materials: Ceramic-based substrates provide high thermal conductivity and excellent mechanical stability, making them suitable for applications requiring efficient heat dissipation and reliability.
- Metal-Core PCBs: These PCBs feature a metal core, such as aluminum or copper, sandwiched between layers of dielectric material. They offer enhanced thermal conductivity and are commonly used in applications with high power densities or strict thermal management requirements.
The choice of base material depends on factors such as operating frequency, power handling capabilities, thermal performance, and cost considerations. Design engineers typically select the base material that best meets the requirements of the specific application while optimizing performance and cost-effectiveness.
Which company makes Open multi-step cavity PCBs?
There are many companies manufacturing Open multi-step cavity PCBs, some of which include high-end PCB manufacturers, electronic equipment manufacturers, and specific PCB technology providers. For example, Rogers Corporation, Isola Group, Taconic Advanced Dielectric Division and other companies have extensive experience and expertise in the field of high-frequency PCB materials, and they provide a variety of high-performance substrate materials for Open multi-step cavity PCBs.
As a PCB manufacturing company with advanced production equipment and technology, our company can also produce Open multi-step cavity PCBs. We have a professional engineering team and technical staff capable of designing and manufacturing complex PCB structures according to customers’ specific requirements. We can provide advanced processes such as multi-layer, multi-step design, precision milling and cutting, and use high-quality substrate materials to ensure PCB high performance and reliability.
Our manufacturing capabilities and experience enable us to serve the needs of a variety of industries, including communications, aerospace, medical devices, automotive electronics and more. We can provide customized solutions based on customers’ design requirements and application scenarios, and ensure the delivery of high-quality, standard-compliant products.
Our company is committed to customer satisfaction and product quality and has a good reputation in the field of PCB manufacturing. Our production process strictly follows international standards and quality management systems to ensure that every link meets the highest standards. We also provide timely technical support and after-sales service to establish long-term and stable cooperative relationships with customers.
Whether customers require simple double-sided PCBs or complex multi-layer Open multi-step cavity PCBs, our company can provide them with a solution that meets their needs. We will make unremitting efforts to provide customers with high-quality products and professional services and become your trustworthy partner.
What are the 7 qualities of good customer service?
Good customer service is characterized by several key qualities that contribute to a positive customer experience. Here are seven qualities of good customer service:
- Responsiveness: Good customer service involves promptly addressing customer inquiries, concerns, and requests. Responding to customers in a timely manner demonstrates attentiveness and a commitment to meeting their needs.
- Empathy:Empathy is essential for understanding and acknowledging customers’ emotions, concerns, and perspectives. Showing empathy helps build rapport and trust with customers by making them feel understood and valued.
- Clear Communication:Effective communication is crucial for conveying information clearly and accurately to customers. Good customer service representatives communicate in a friendly, professional manner and use language that is easy for customers to understand.
- Problem-Solving Skills: Good customer service involves the ability to identify and resolve customer issues efficiently and effectively. Customer service representatives should be resourceful and proactive in finding solutions that meet customers’ needs and expectations.
- Product Knowledge: Having a deep understanding of the products or services offered allows customer service representatives to provide accurate information and guidance to customers. A thorough knowledge of the product or service builds credibility and instills confidence in customers.
- Consistency: Consistency in service delivery ensures that customers receive a uniform and reliable experience across all interactions with a company. Consistent service builds trust and loyalty by setting clear expectations and delivering on promises.
- Customer Focus: Good customer service is centered around the needs and preferences of the customer. Customer service representatives should be attentive and responsive to customer feedback, striving to exceed expectations and deliver personalized experiences.
By embodying these qualities, organizations can cultivate strong relationships with customers and differentiate themselves in the marketplace through exceptional service.
FAQs
What is an Open multi-step cavity PCB?
An Open multi-step cavity PCB is a type of printed circuit board (PCB) design that incorporates multiple layers with varying thicknesses and cavities within the substrate. It is often used in high-frequency applications for improved signal integrity, thermal management, and electromagnetic interference (EMI) reduction.
What are the advantages of Open multi-step cavity PCBs?
Open multi-step cavity PCBs offer several advantages, including enhanced signal integrity, reduced EMI, improved thermal dissipation, and precise impedance control. These features make them suitable for high-frequency applications such as telecommunications, aerospace, and radar systems.
How are cavities created in Open multi-step cavity PCBs?
Cavities in Open multi-step cavity PCBs are typically created using precision machining techniques such as milling or routing. These cavities are strategically placed within the PCB substrate to minimize EMI and optimize thermal performance.
What materials are used in Open multi-step cavity PCBs?
The base material for Open multi-step cavity PCBs can vary depending on the specific requirements of the application. Common materials include high-frequency laminates, PTFE-based substrates, and ceramic-based materials, chosen for their excellent electrical properties and thermal conductivity.
How do Open multi-step cavity PCBs differ from standard PCBs?
Open multi-step cavity PCBs differ from standard PCBs in their complex layer stackup, which includes multiple layers with varying thicknesses and cavities within the substrate. These features enable superior performance in terms of signal integrity, thermal management, and EMI reduction compared to standard PCBs.
What are some typical applications of Open multi-step cavity PCBs?
Open multi-step cavity PCBs are commonly used in high-frequency applications such as wireless communication systems, radar systems, RF/microwave devices, and aerospace electronics, where reliable performance and stringent design requirements are essential.
How can I design and manufacture Open multi-step cavity PCBs?
Designing and manufacturing Open multi-step cavity PCBs requires specialized expertise and equipment. It involves tasks such as layer stackup design, cavity placement, controlled impedance routing, and precision machining. Working with experienced PCB manufacturers and design engineers can help ensure successful fabrication of these complex PCBs.