Multi-Cavity PCB| RF PCB Manufacturing
Multi-Cavity PCB| RF PCB Manufacturing,Multi-cavity PCBs, also known as multi-chamber PCBs, are specialized printed circuit boards designed to accommodate multiple compartments or cavities within their structure. These cavities are strategically placed and sized to house various electronic components such as integrated circuits (ICs), connectors, and passive components. The design of multi-cavity PCBs allows for efficient integration of complex electronic systems in a compact and organized manner. By segregating components into separate
What is a Multi-cavity PCB?
A multi-cavity PCB (Printed Circuit Board) is a type of circuit board that features multiple cavities or compartments within its structure. These cavities are typically designed to accommodate various components, such as integrated circuits (ICs), connectors, or other electronic components.
The primary advantage of using a multi-cavity PCB is the ability to integrate multiple components in a compact and organized manner, which can help reduce the overall size of the electronic device and improve its overall performance. Additionally, multi-cavity PCBs can also help enhance the thermal management and electromagnetic interference (EMI) shielding of the device by providing separate compartments for different components.
Overall, multi-cavity PCBs are commonly used in a wide range of electronic devices, including smartphones, tablets, computers, and other consumer electronics, as well as in industrial and automotive applications.
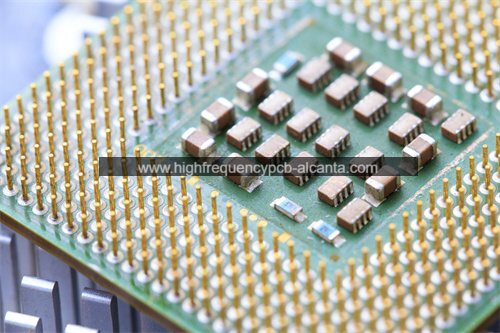
Multi-Cavity PCB| RF PCB Manufacturing
What are the Multi-cavity PCB Design Guidelines?
Here are some general design guidelines for multi-cavity PCBs:
- Component Placement: Ensure that components are placed strategically within each cavity to optimize space utilization and minimize signal interference.
- Cavity Size and Shape: Design cavities with adequate size and shape to accommodate the components while allowing for proper airflow and heat dissipation.
- Signal Integrity: Maintain signal integrity by minimizing trace lengths, using proper routing techniques, and ensuring adequate separation between high-speed and low-speed signals.
- Thermal Management: Incorporate thermal vias, heatsinks, and other thermal management techniques to dissipate heat effectively and prevent component overheating.
- EMI/RFI Shielding: Implement shielding techniques such as ground planes, shielding cans, and ferrite beads to minimize electromagnetic interference (EMI) and radio frequency interference (RFI).
- Mechanical Stability: Design the PCB with sufficient mechanical support and reinforcement to withstand vibrations, shocks, and other mechanical stresses.
- Manufacturability: Consider manufacturability aspects such as panelization, solder mask application, and assembly process requirements to ensure ease of manufacturing and assembly.
- Testing and Debugging: Include test points, probe access points, and other debugging features to facilitate testing and troubleshooting during the manufacturing and assembly process.
- Documentation: Provide comprehensive documentation including assembly drawings, component placement files, and manufacturing notes to assist in the fabrication and assembly of the multi-cavity PCB.
By following these guidelines, designers can create multi-cavity PCBs that meet the requirements for functionality, reliability, and manufacturability.
What is the Multi-cavity PCB Fabrication Process?
The fabrication process for multi-cavity PCBs typically involves several steps:
- Design: The process begins with the design of the PCB layout, including the placement of components and the routing of traces within each cavity. Special attention is paid to ensuring proper spacing, signal integrity, thermal management, and manufacturability.
- Material Selection: Once the design is finalized, the appropriate materials are selected for the PCB substrate, copper layers, and any additional layers or coatings required for the specific application.
- Panelization: Multiple PCBs are often fabricated together on a single panel to optimize production efficiency. The individual PCBs are arranged in a panel layout, with the necessary spacing and routing channels between them.
- Substrate Preparation: The chosen substrate material, typically FR-4 fiberglass, is prepared by cutting it to size and cleaning it to remove any contaminants that could affect the adhesion of the copper layers.
- Copper Cladding: A thin layer of copper foil is bonded to both sides of the substrate material using heat and pressure. This forms the conductive layers that will carry electrical signals throughout the PCB.
- Photoresist Application: A layer of photoresist material is applied to the surface of the copper layers. The photoresist is then exposed to ultraviolet light through a photomask, which defines the desired circuit pattern for each layer.
- Etching: The exposed areas of the copper layers are etched away using a chemical solution, leaving behind the desired circuit traces and component pads. This process is repeated for each layer of the PCB, including inner layers if a multilayer PCB is being fabricated.
- Drilling: Holes are drilled through the substrate material at locations specified in the design for mounting components and providing electrical connections between layers.
- Plating: The drilled holes are plated with a conductive material, typically copper, to create vias that establish electrical connections between different layers of the PCB.
- Surface Finish: A surface finish is applied to the exposed copper surfaces to protect them from oxidation and ensure solderability during assembly.
- Testing: The fabricated PCBs undergo electrical testing to verify that all connections are intact and that the circuit functions as intended.
- Separation: Once testing is complete, the individual PCBs are separated from the panel using a routing or scoring process.
- Quality Control: The finished PCBs are inspected for any defects or imperfections that could affect performance or reliability.
- Assembly: Finally, the PCBs are assembled with the necessary components, either through automated pick-and-place machines or manual soldering techniques, to complete the electronic device.
By following these steps, manufacturers can produce high-quality multi-cavity PCBs that meet the requirements for functionality, reliability, and performance.
How do you manufacture a Multi-cavity PCB?
Manufacturing a multi-cavity PCB involves several steps, similar to those of a standard PCB fabrication process, with additional considerations for the multiple cavities. Here’s an overview of the manufacturing process:
- Design: The design phase involves creating the PCB layout with multiple cavities to accommodate various components. The layout should consider the placement of components, routing of traces, and thermal management within each cavity.
- Material Selection: Choose the appropriate substrate material, typically FR-4 fiberglass, and copper foil for the conductive layers. Consider any additional materials needed for specialized requirements such as high temperature or impedance control.
- Panelization: Arrange multiple PCBs on a single panel to optimize production efficiency. Designate the spacing and routing channels between PCBs to facilitate separation after fabrication.
- Substrate Preparation: Cut the substrate material to size and clean it to remove any contaminants that could affect adhesion.
- Copper Cladding: Bond copper foil to both sides of the substrate material using heat and pressure. This forms the conductive layers for the PCB.
- Photoresist Application: Apply a layer of photoresist material to the copper surfaces. Use a photomask to expose the desired circuit pattern for each cavity.
- Etching: Use a chemical solution to etch away the exposed copper, leaving behind the circuit traces and component pads for each cavity.
- Drilling: Drill holes through the substrate material at designated locations for mounting components and creating vias between layers.
- Plating: Plate the drilled holes with a conductive material, typically copper, to establish electrical connections between layers.
- Surface Finish: Apply a surface finish to the exposed copper surfaces to protect them from oxidation and ensure solderability during assembly.
- Testing: Perform electrical testing to verify the integrity of the connections and functionality of the circuit within each cavity.
- Separation: After testing, separate the individual PCBs from the panel using routing or scoring techniques.
- Quality Control: Inspect the finished PCBs for any defects or imperfections that could affect performance or reliability.
- Assembly: Finally, assemble the PCBs with the necessary components, considering the layout and orientation of each cavity, to complete the electronic device.
Throughout the manufacturing process, attention should be paid to maintaining consistency and quality control to ensure the final product meets the desired specifications for functionality, reliability, and performance.
How much should a Multi-cavity PCB cost?
The cost of a multi-cavity PCB can vary widely depending on factors such as:
- Size: The physical dimensions of the PCB, including the number and size of cavities, can impact the cost.
- Complexity: The complexity of the circuit design, including the number of layers, component density, and routing requirements, can affect the cost.
- Material: The choice of substrate material, copper thickness, and surface finish can influence the cost.
- Quantity: Typically, the unit cost decreases as the quantity of PCBs ordered increases due to economies of scale.
- Manufacturing Process: Specialized manufacturing processes, such as impedance control, blind/buried vias, and controlled-depth drilling, can add to the cost.
- Lead Time: Expedited production or shipping options may incur additional costs.
- Additional Services: Services such as PCB assembly, testing, and design validation may be available for an extra fee.
To get an accurate estimate of the cost for a multi-cavity PCB, it’s best to consult with PCB manufacturers or use online PCB quotation tools. These tools allow you to input specific details about your PCB requirements and receive a cost estimate based on those parameters. Additionally, requesting quotes from multiple manufacturers can help you compare prices and choose the most cost-effective option for your project.
What is Multi-cavity PCB base material?
The base material for a multi-cavity PCB is typically a type of substrate material that forms the foundation of the printed circuit board. The most common base material used for PCBs is fiberglass-reinforced epoxy laminate, commonly referred to as FR-4. FR-4 is a versatile and widely used substrate material known for its excellent electrical insulation properties, mechanical strength, and cost-effectiveness.
FR-4 is composed of layers of woven fiberglass fabric impregnated with epoxy resin. This combination provides the PCB with the necessary rigidity and durability to support the components and withstand the stresses of assembly and use.
In addition to FR-4, other base materials may be used for specific applications or requirements. For example, high-frequency applications may require substrates with low dielectric constants and low loss tangents, such as polytetrafluoroethylene (PTFE) or ceramic materials. Similarly, high-temperature applications may call for substrates with enhanced thermal performance, such as polyimide (PI) or aluminum-backed substrates.
Ultimately, the choice of base material for a multi-cavity PCB depends on factors such as the desired electrical performance, mechanical properties, thermal characteristics, and cost considerations.
Which company makes Multi-cavity PCB?
Multi-cavity PCB (Multi-cavity Printed Circuit Board) is a common type of printed circuit board used in electronic devices to integrate multiple components and achieve various functionalities of electronic components. At present, many electronic manufacturing companies can produce multi-cavity PCBs, including well-known PCB manufacturers and electronic device manufacturers.
Our company is also a professional PCB manufacturer with advanced production equipment and an experienced technical team. We can customize and produce various types of multi-cavity PCBs according to customer requirements to meet the requirements of different application scenarios.
Our company’s advantages include:
Advanced technology and equipment: We have advanced production equipment and a technical team that can provide high-quality, high-precision multi-cavity PCB production services.
Rich experience: We have many years of experience in the PCB manufacturing field, familiar with various processes and techniques, to ensure the production of high-quality products that meet customer requirements.
Flexible customization services: We can customize the design and production of multi-cavity PCBs according to customer requirements, including different sizes, layers, materials, and process requirements.
Quality assurance: We strictly manage production and quality control according to international standards and customer requirements to ensure that each multi-cavity PCB has stable quality and reliability.
Good customer service: We value communication and cooperation with customers, providing timely technical support and after-sales service to ensure customer satisfaction.
In summary, our company can provide customers with high-quality, customized multi-cavity PCB production services to help customers achieve their design and manufacturing goals for electronic devices.
What are the 7 qualities of good customer service?
Good customer service typically exhibits the following qualities:
- Responsiveness: Customers appreciate timely responses to their inquiries, concerns, or issues. Being readily available and providing prompt assistance can enhance customer satisfaction.
- Empathy: Understanding and empathizing with customers’ needs and emotions can help build rapport and trust. Empathetic responses demonstrate that the company cares about its customers’ experiences.
- Clarity: Clear communication is essential for conveying information effectively and avoiding misunderstandings. Customer service representatives should provide accurate and concise explanations or instructions.
- Professionalism: Maintaining professionalism in all interactions, whether in person, over the phone, or online, fosters a positive impression of the company and its representatives. This includes being courteous, respectful, and maintaining a positive attitude.
- Problem-solving skills: Effective problem-solving involves identifying and addressing customers’ concerns in a timely and satisfactory manner. Customer service agents should be empowered to resolve issues efficiently and creatively.
- Consistency: Consistency in service delivery ensures that customers receive the same level of quality and support across all touchpoints and interactions with the company. Consistent service builds trust and loyalty over time.
- Follow-up: Following up with customers after resolving an issue or completing a transaction demonstrates commitment to their satisfaction and allows for feedback. Proactive follow-up can help identify areas for improvement and strengthen customer relationships.
By embodying these qualities, businesses can provide exceptional customer service that meets or exceeds customers’ expectations and contributes to long-term success.
FAQs
What is a multi-cavity PCB?
A multi-cavity PCB is a type of printed circuit board that features multiple cavities or compartments within its structure. These cavities are designed to accommodate various components, allowing for compact and organized integration of electronics.
What are the advantages of using multi-cavity PCBs?
Multi-cavity PCBs offer several advantages, including space optimization, improved thermal management, reduced electromagnetic interference (EMI), and enhanced organization of components. They are commonly used in electronic devices where space is limited and multiple components need to be integrated efficiently.
What types of components can be accommodated in multi-cavity PCBs?
Multi-cavity PCBs can accommodate a wide range of components, including integrated circuits (ICs), connectors, passive components (such as resistors and capacitors), and other electronic devices. The design of the cavities can be customized to fit specific component requirements.
How are multi-cavity PCBs manufactured?
The manufacturing process for multi-cavity PCBs is similar to that of standard PCBs, with additional considerations for the multiple cavities. It involves steps such as design, material selection, substrate preparation, copper cladding, etching, drilling, plating, surface finish, testing, separation, and quality control.
What factors should be considered when designing a multi-cavity PCB?
When designing a multi-cavity PCB, factors such as component placement, cavity size and shape, signal integrity, thermal management, EMI shielding, mechanical stability, manufacturability, testing, and documentation should be carefully considered to ensure optimal performance and reliability.
What industries commonly use multi-cavity PCBs?
Multi-cavity PCBs are commonly used in various industries, including consumer electronics, telecommunications, automotive, aerospace, medical devices, industrial automation, and more. They are particularly useful in applications where space is limited and multiple components need to be integrated efficiently.
Can multi-cavity PCBs be customized to specific requirements?
Yes, multi-cavity PCBs can be customized to meet specific requirements such as size, shape, number of cavities, component placement, material selection, and manufacturing process. Customization allows for tailored solutions that meet the unique needs of each application.