Microvias PCB Manufacturing
Microvias PCB Manufacturing,Microvias PCBs represent a cutting-edge solution in modern electronics manufacturing, revolutionizing the way electronic devices are designed and assembled. These PCBs feature tiny holes drilled into the substrate, enabling connections between different layers with unprecedented precision and density. By utilizing micro-sized vias, Microvias PCBs allow for the creation of smaller, lighter, and more sophisticated electronic products. They facilitate high-density interconnects, ensuring optimal signal integrity, reduced signal skew, and efficient thermal management. With their ability to accommodate complex circuit layouts and meet the demands of miniaturization, Microvias PCBs are indispensable in various industries, including consumer electronics, telecommunications, automotive, aerospace, and medical devices. As the demand for smaller and more powerful electronic devices continues to grow, Microvias PCBs play a crucial role in driving innovation and pushing the boundaries of what’s possible in electronics design.
What is a Microvias PCB?
Microvias are small holes drilled into a printed circuit board (PCB) to create connections between different layers of the board. They are typically used in high-density interconnect (HDI) PCBs, where space is limited and the routing of traces between layers needs to be more efficient.
Microvias are significantly smaller than traditional plated-through holes, with diameters typically ranging from 0.1mm to 0.2mm or even smaller. Their small size allows for denser packing of components and routing of traces, enabling the creation of smaller and more compact electronic devices.
Microvias can be categorized into two main types: blind vias and buried vias.
- Blind vias connect the outer layer of the PCB to one or more inner layers but do not penetrate through the entire board. They are “blind” because they are visible from only one side of the board.
- Buried vias, on the other hand, connect inner layers of the PCB without penetrating the outer layers. They are “buried” within the PCB and are not visible from the outer surfaces.
Microvias are typically created using laser drilling or mechanical drilling techniques, depending on the specific requirements of the PCB design. Laser drilling offers higher precision and can create smaller diameter holes, making it suitable for high-density PCBs.
Overall, microvias play a crucial role in modern PCB manufacturing, enabling the development of smaller, lighter, and more advanced electronic devices with increased functionality and performance.
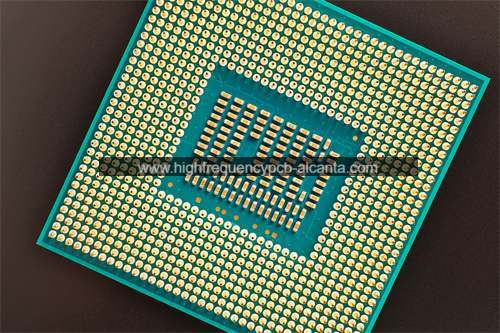
Microvias PCB Manufacturing
What are the Microvias PCB Design Guidelines?
Here are some general guidelines for designing PCBs with microvias:
- Minimum Annular Ring: The annular ring is the copper pad surrounding the drilled hole. It’s crucial to maintain a sufficient annular ring width to ensure good connectivity and reliability. Typically, a minimum annular ring width of 0.05mm to 0.075mm is recommended for microvias.
- Aspect Ratio: The aspect ratio is the ratio of the PCB thickness to the diameter of the drilled hole. For microvias, it’s essential to keep the aspect ratio within a reasonable range to ensure proper plating and reliability. Generally, aspect ratios of 1:1 to 1:10 are common for microvias.
- Layer Transition: When transitioning between different layers using microvias, consider the signal integrity and impedance control requirements. Proper placement of microvias and careful routing can help minimize signal degradation and impedance mismatches.
- Stackup Design: Design the PCB stackup carefully, considering the number of layers, the thickness of dielectric materials between layers, and the placement of signal, power, and ground planes. A well-designed stackup can optimize signal integrity, power distribution, and thermal management.
- Clearance and Spacing: Maintain adequate clearance and spacing between microvias, traces, and other components to prevent short circuits and ensure manufacturability. Follow the manufacturer’s recommended design rules for minimum clearances and spacings.
- Manufacturability Considerations: Consult with your PCB manufacturer early in the design process to ensure that your design meets their manufacturing capabilities and requirements. Consider factors such as minimum drill size, material limitations, and manufacturing tolerances.
- Signal Integrity: Pay attention to signal integrity issues such as impedance control, signal skew, and crosstalk. Proper layout techniques, such as controlled impedance routing and signal length matching, can help mitigate these issues.
- Thermal Management: Consider thermal management techniques, such as thermal vias and copper pours, to dissipate heat from high-power components and ensure reliable operation of the PCB.
By following these guidelines and best practices, you can design PCBs with microvias that meet your performance, reliability, and manufacturability requirements.
What is the Microvias PCB Fabrication Process?
The fabrication process for PCBs with microvias involves several steps, including design, material selection, drilling, plating, etching, and testing. Here’s an overview of the typical microvias PCB fabrication process:
- Design: The process begins with PCB design using specialized software. Designers create the circuit layout, including the placement of components, routing of traces, and insertion of microvias. Design considerations such as signal integrity, power distribution, and thermal management are taken into account during this phase.
- Material Selection: Selecting the right materials is crucial for microvias PCB fabrication. This includes choosing the appropriate substrate material (typically FR-4 or other high-performance laminates), copper foil thickness, and solder mask materials based on the specific requirements of the PCB design.
- Drilling: Microvias are drilled into the PCB using specialized equipment such as laser drills or mechanical drills with high precision. Laser drilling is preferred for creating small-diameter microvias with high aspect ratios. The drilling process must be carefully controlled to ensure accurate hole placement and dimension.
- Desmear and Surface Preparation: After drilling, the PCB undergoes a desmear process to remove any residues or debris generated during drilling. Surface preparation techniques such as chemical etching or plasma treatment are then applied to promote adhesion and facilitate subsequent plating processes.
- Plating: Microvias are plated with conductive materials (typically copper) to create electrical connections between different layers of the PCB. This involves several steps, including electroless copper deposition, through-hole plating, and copper buildup to fill the microvias completely.
- Etching: Once the microvias are plated, the outer layers of the PCB are etched to define the circuit traces and remove excess copper. Photolithography techniques are used to apply a resist layer and define the desired circuit pattern, followed by chemical etching to remove the unwanted copper.
- Surface Finish: After etching, the PCB surface is coated with a surface finish to protect the copper traces from oxidation and ensure solderability. Common surface finishes include HASL (hot air solder leveling), ENIG (electroless nickel immersion gold), and OSP (organic solderability preservatives).
- Quality Control and Testing: The fabricated PCBs undergo rigorous quality control and testing to ensure they meet the required specifications and standards. This may include visual inspection, electrical testing, impedance testing, and reliability testing to verify performance and reliability.
- Final Inspection and Packaging: Once the PCBs pass quality control, they are inspected for any defects or imperfections before being packaged and shipped to the customer.
Overall, the fabrication process for microvias PCBs requires precision, attention to detail, and adherence to strict manufacturing standards to produce high-quality PCBs with reliable performance.
How do you manufacture a Microvias PCB?
Manufacturing a PCB with microvias involves several steps, from design to final testing. Here’s a detailed overview of the manufacturing process:
- Design: The process starts with PCB design using specialized software. Designers create the circuit layout, including component placement, trace routing, and microvia insertion. Design considerations such as signal integrity, power distribution, and thermal management are taken into account during this phase.
- Material Selection: Choose the appropriate materials for the PCB based on the design requirements. This includes selecting the substrate material (such as FR-4 or high-frequency laminates), copper foil thickness, and solder mask materials.
- Drilling Microvias: Microvias are drilled into the PCB using specialized equipment like laser drills or mechanical drills. Laser drilling is preferred for creating small-diameter microvias with high aspect ratios. The drilling process must be carefully controlled to ensure precise hole placement and dimensions.
- Desmear and Surface Preparation: After drilling, the PCB undergoes a desmear process to remove any residues or debris generated during drilling. Surface preparation techniques such as chemical etching or plasma treatment are then applied to promote adhesion and facilitate subsequent plating processes.
- Plating Microvias: Microvias are plated with conductive materials (usually copper) to create electrical connections between different layers of the PCB. This involves several steps, including electroless copper deposition, through-hole plating, and copper buildup to fill the microvias completely.
- Etching Outer Layers: Once the microvias are plated, the outer layers of the PCB are etched to define the circuit traces and remove excess copper. Photolithography techniques are used to apply a resist layer and define the desired circuit pattern, followed by chemical etching to remove the unwanted copper.
- Surface Finish: After etching, the PCB surface is coated with a surface finish to protect the copper traces from oxidation and ensure solderability. Common surface finishes include HASL (hot air solder leveling), ENIG (electroless nickel immersion gold), and OSP (organic solderability preservatives).
- Quality Control and Testing: The fabricated PCBs undergo rigorous quality control and testing to ensure they meet the required specifications and standards. This may include visual inspection, electrical testing, impedance testing, and reliability testing to verify performance and reliability.
- Final Inspection and Packaging: Once the PCBs pass quality control, they are inspected for any defects or imperfections before being packaged and shipped to the customer.
Overall, manufacturing a PCB with microvias requires precision, attention to detail, and adherence to strict manufacturing standards to produce high-quality PCBs with reliable performance.
How much should a Microvias PCB cost?
The cost of a PCB with microvias can vary depending on several factors, including the complexity of the design, the number of layers, the size of the board, the materials used, the manufacturing technology required, and the quantity ordered. However, to provide a general idea, here are some factors that can influence the cost:
- Design Complexity: PCBs with microvias often have higher complexity due to the need for precise drilling and plating processes. Designs with intricate routing, fine pitch components, and high-density interconnects may increase manufacturing costs.
- Number of Layers: PCBs can have multiple layers, with each additional layer increasing the cost of manufacturing. Microvias are commonly used in high-density interconnect (HDI) PCBs with multiple layers to achieve compact designs.
- Material Selection: The choice of substrate material, copper thickness, and surface finish can impact the cost of the PCB. High-performance materials and finishes may increase the cost compared to standard options.
- Manufacturing Technology: The manufacturing technology used, such as laser drilling for microvias, can affect the cost. Advanced processes that require specialized equipment and expertise may result in higher manufacturing costs.
- Order Quantity: Ordering larger quantities of PCBs typically reduces the unit cost due to economies of scale. However, prototype or small-batch orders may incur higher costs per unit.
- Turnaround Time: Expedited manufacturing or quick-turn services may come at an additional cost compared to standard lead times.
- Supplier and Location: PCB fabrication costs can vary between different suppliers and regions. Factors such as labor costs, overheads, and shipping fees can impact the overall cost.
It’s essential to obtain quotes from multiple PCB manufacturers and consider all the factors mentioned above to estimate the cost accurately. Additionally, working closely with your manufacturer to optimize the design for manufacturability can help reduce costs without compromising quality.
What is Microvias PCB base material?
The base material for a PCB with microvias is typically a high-performance laminate chosen based on the specific requirements of the application. Some common materials used as the base substrate for microvias PCBs include:
- FR-4: FR-4 (Flame Retardant 4) is the most widely used substrate material for PCBs due to its affordability and good electrical and mechanical properties. It consists of woven fiberglass cloth impregnated with an epoxy resin.
- High-Frequency Laminates: For applications requiring high-speed signal transmission, such as RF and microwave circuits, high-frequency laminates are used. These laminates have low dielectric constants and low loss tangents to minimize signal loss.
- Polyimide (PI): Polyimide substrates are flexible and have excellent thermal and chemical resistance, making them suitable for applications where flexibility and durability are essential, such as in flexible PCBs (FPCBs).
- Rogers Materials: Rogers Corporation manufactures a range of high-performance laminates specifically designed for high-frequency applications. These materials offer superior electrical properties, including low dielectric loss and excellent signal integrity.
- Isola Materials: Isola is another manufacturer that produces high-performance laminates for demanding PCB applications. Their materials offer a balance of electrical, mechanical, and thermal properties suitable for various applications.
The choice of base material depends on factors such as the desired electrical performance, thermal characteristics, mechanical strength, and cost considerations. Additionally, the base material should be compatible with the manufacturing processes involved in creating microvias, such as drilling, plating, and etching. Working closely with your PCB manufacturer to select the appropriate base material based on your specific requirements is crucial for the success of your microvias PCB project.
Which company makes Microvias PCB?
There are many companies that produce microvias PCBs, including some well-known PCB manufacturers and suppliers. Some of these companies include Rogers Corporation, Isola Group, Panasonic Electric Works, TTM Technologies, Advanced Circuits, and others.
Our company is also a professional PCB manufacturer with advanced production equipment and rich experience, capable of producing various types of PCBs, including microvias PCBs. Our manufacturing processes and technologies enable us to meet customers’ requirements for high-density interconnects and complex circuit layouts. Here are our capabilities and advantages in producing microvias PCBs:
- Advanced Manufacturing Equipment: We have advanced laser drilling equipment and high-precision mechanical drilling equipment capable of producing microvias with small diameters and high densities.
- Rich Experience: Our engineering team has extensive experience in PCB design and manufacturing, providing professional design advice and technical support to ensure that the design and manufacturing of microvias PCBs meet customers’ requirements and standards.
- Quality Assurance: We strictly adhere to international standards and industry specifications in production, employing advanced quality control systems and inspection equipment to ensure the reliability and stability of each microvias PCB.
- Customization Services: We can customize microvias PCBs according to customers’ specific requirements, including different layers, materials, thicknesses, etc., to meet the diverse needs of customers’ applications.
- Fast Delivery: With efficient production processes and flexible scheduling, we offer fast delivery services to ensure that customers receive their orders on time.
In summary, as a professional PCB manufacturer, our company has the capability and experience to produce microvias PCBs and is committed to providing customers with high-quality, high-performance customized solutions.
What are the 7 qualities of good customer service?
Good customer service is essential for building strong relationships with customers and fostering loyalty. Here are seven qualities that are typically associated with good customer service:
- Responsiveness: A key quality of good customer service is being responsive to customer inquiries, requests, and concerns in a timely manner. This involves promptly addressing customer issues and providing assistance whenever needed.
- Empathy: Empathy involves understanding and acknowledging the feelings and perspectives of customers. Good customer service representatives listen actively, show empathy towards customers’ concerns, and strive to find solutions that meet their needs.
- Clear Communication: Effective communication is vital in delivering good customer service. This includes providing clear and concise information, explaining complex concepts in a simple manner, and ensuring that customers understand the solutions or options available to them.
- Knowledgeability:Good customer service representatives possess a deep understanding of the products or services they are offering. They are knowledgeable about the features, benefits, and usage of the products/services, allowing them to answer customer questions accurately and provide valuable assistance.
- Professionalism: Professionalism is essential in all interactions with customers. This includes maintaining a positive attitude, remaining calm and composed, and adhering to company policies and standards while dealing with challenging situations.
- Problem-Solving Skills: Good customer service involves effectively resolving customer issues and complaints. Customer service representatives should be skilled in identifying problems, analyzing root causes, and offering practical solutions that address customers’ concerns.
- Consistency: Consistency is key to delivering a great customer experience. Good customer service is not just about occasional exceptional interactions but also about consistently meeting or exceeding customer expectations every time they engage with the company.
By embodying these qualities, businesses can build trust, loyalty, and satisfaction among their customer base, ultimately leading to long-term success and growth.
FAQs (Frequently Asked Questions)
What are Microvias PCBs?
Microvias PCBs are printed circuit boards (PCBs) that feature small holes drilled into the substrate to create connections between different layers of the board. These micro-sized vias allow for high-density interconnects in compact electronic devices.
What are the advantages of using Microvias PCBs?
Microvias PCBs offer several advantages, including increased routing density, improved signal integrity, reduced signal skew, and enhanced thermal management. They enable the design of smaller and more compact electronic devices with higher functionality.
How are Microvias PCBs manufactured?
The manufacturing process for Microvias PCBs involves several steps, including design, drilling of microvias, plating, etching, surface finishing, and testing. Specialized equipment and techniques are used to create small-diameter holes and ensure reliable electrical connections between different layers.
What types of Microvias are commonly used in PCBs?
Two main types of Microvias are commonly used: blind vias and buried vias. Blind vias connect the outer layer of the PCB to one or more inner layers without penetrating the entire board. Buried vias, on the other hand, connect inner layers without extending to the outer layers.
What are the design considerations for Microvias PCBs?
Design considerations for Microvias PCBs include minimum annular ring width, aspect ratio limits, layer transition optimization, stackup design for impedance control, clearance and spacing requirements, and manufacturability considerations.
What are the applications of Microvias PCBs?
Microvias PCBs are used in various applications, including smartphones, tablets, laptops, wearables, IoT devices, medical devices, aerospace, and automotive electronics. They are particularly suitable for high-density and high-speed electronic systems.
How do Microvias PCBs contribute to miniaturization in electronics?
Microvias PCBs enable the creation of smaller and more compact electronic devices by allowing for higher routing density and more efficient use of PCB real estate. This helps in reducing the overall size and weight of electronic products while maintaining or even enhancing their functionality.