Microtrace Substrate Manufacturer
Microtrace Substrate Manufacturer,Microtrace Substrates are foundational materials pivotal in the realm of microelectronics. These substrates serve as the canvases upon which intricate electronic components, including transistors, diodes, and integrated circuits, are meticulously crafted. Renowned for their precision and reliability, Microtrace Substrates offer a robust platform for the construction of miniaturized devices crucial in modern technology.
Characterized by their exceptional electrical properties, thermal conductivity, and mechanical stability, Microtrace Substrates are tailored to meet the demanding requirements of diverse applications. Whether facilitating the operation of high-speed RF devices, powering sophisticated sensors, or enabling the seamless integration of advanced semiconductor technologies, these substrates play a vital role in driving innovation and progress across industries.
Manufactured through sophisticated processes encompassing epitaxial growth, photolithography, and thin film deposition, Microtrace Substrates undergo rigorous quality control measures to ensure impeccable performance and reliability. With their versatility and scalability, these substrates continue to fuel advancements in microelectronics, paving the way for groundbreaking technologies that shape our interconnected world.
What is a Microtrace Substrate?
A Microtrace Substrate typically refers to a material used in the fabrication of microelectronic devices or components. These substrates are usually made of semiconductor materials like silicon, gallium arsenide, or other compound semiconductors.
In microelectronics, the substrate serves as the foundation upon which various components such as transistors, diodes, and integrated circuits are built. The choice of substrate material depends on factors such as the desired electrical properties, thermal conductivity, and compatibility with the manufacturing process.
Microtrace substrates are crucial for the performance and reliability of microelectronic devices, as they provide mechanical support and electrical connections for the components fabricated on them. These substrates undergo precise manufacturing processes to ensure uniformity and consistency, which are essential for the functionality of the final devices.
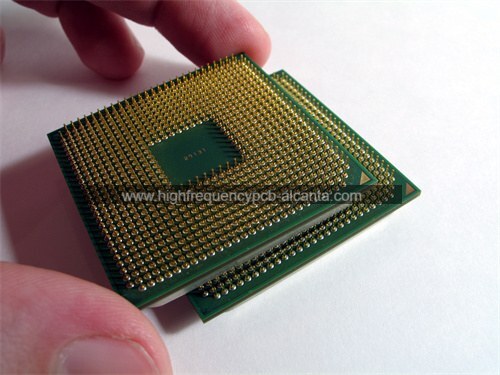
Microtrace Substrate Manufacturer
What are Microtrace Substrate Design Guidelines?
Microtrace substrate design guidelines typically encompass a set of principles and recommendations aimed at optimizing the performance, reliability, and manufacturability of microelectronic devices. These guidelines often include the following aspects:
- Material Selection: Choosing the appropriate substrate material based on the specific requirements of the device, such as electrical properties, thermal conductivity, mechanical strength, and compatibility with the fabrication process.
- Dimensional Considerations: Specifying the dimensions and thickness of the substrate to ensure mechanical stability, proper heat dissipation, and compatibility with packaging requirements.
- Surface Preparation: Ensuring the substrate surface is clean, flat, and free from contaminants or defects that could negatively impact device performance or yield.
- Layer Stack Design: Designing the layer stack of the substrate, including any epitaxial layers or insulating layers, to meet the electrical and thermal requirements of the device.
- Pattern and Layout Guidelines: Providing recommendations for the layout and placement of device components on the substrate to minimize parasitic effects, optimize signal integrity, and facilitate manufacturability.
- Alignment and Registration: Defining tolerances for alignment and registration between different layers or features on the substrate to ensure proper functionality and yield during the manufacturing process.
- Interconnect Design: Designing interconnect structures, such as metal traces and vias, to minimize resistance, capacitance, and signal delay while ensuring reliability and manufacturability.
- Thermal Management: Incorporating features such as thermal vias, heat sinks, or thermal interface materials to efficiently dissipate heat generated by the device and prevent thermal degradation.
- Electrical Isolation:Implementing techniques to ensure electrical isolation between different device components or regions on the substrate to prevent unwanted coupling or interference.
- Packaging Compatibility: Ensuring that the substrate design is compatible with the chosen packaging technology and assembly processes, including considerations for wire bonding, flip-chip bonding, or surface mount technology.
These guidelines may vary depending on the specific application, technology node, and manufacturing process used for the microelectronic device. Adhering to these design guidelines helps to optimize device performance, reliability, and yield while reducing development time and cost.
What is the Microtrace Substrate Fabrication Process?
The fabrication process for microtrace substrates involves several steps, typically including the following:
- Substrate Preparation: The process begins with preparing the substrate material, which is often a semiconductor wafer such as silicon or gallium arsenide. The substrate is cleaned thoroughly to remove any contaminants and defects that could affect device performance.
- Epitaxial Growth (Optional): In some cases, epitaxial layers are grown on the substrate surface to modify its electrical properties or create specific structures. Epitaxy involves depositing thin layers of semiconductor material onto the substrate using techniques like chemical vapor deposition (CVD) or molecular beam epitaxy (MBE).
- Photolithography: Photolithography is used to define the pattern of features on the substrate. A layer of photoresist is spin-coated onto the substrate surface, exposed to ultraviolet (UV) light through a photomask, and developed to remove the exposed regions, leaving behind a patterned resist mask.
- Etching: Etching is performed to transfer the pattern from the photoresist mask onto the substrate surface. Different types of etching processes, such as dry etching (plasma etching) or wet etching (chemical etching), may be used depending on the substrate material and the desired feature geometry.
- Thin Film Deposition: Thin films of materials such as metals (e.g., aluminum, copper) or insulators (e.g., silicon dioxide, silicon nitride) are deposited onto the substrate surface using techniques like physical vapor deposition (PVD), chemical vapor deposition (CVD), or atomic layer deposition (ALD). These thin films are used to create interconnects, insulation layers, and other device structures.
- Planarization (Optional): Planarization techniques like chemical mechanical polishing (CMP) may be employed to flatten the substrate surface and remove any topographical irregularities introduced during the deposition and etching processes.
- Metallization: Metal traces and interconnects are formed by patterning and etching thin metal films deposited on the substrate surface. Multiple layers of metal may be deposited and patterned to create complex interconnect structures.
- Dielectric Deposition and Etching: Insulating layers (dielectrics) are deposited onto the substrate surface to electrically isolate different device components and interconnects. These dielectric layers are patterned and etched to create vias and isolate regions as needed.
- Final Processing: Additional processing steps, such as annealing, passivation, and surface treatments, may be performed to improve device performance, reliability, and stability.
- Quality Control and Testing: Throughout the fabrication process, quality control measures are implemented to ensure the integrity and functionality of the substrate. After fabrication, the substrates undergo testing to verify their electrical properties, structural integrity, and reliability.
These steps represent a general overview of the microtrace substrate fabrication process, which can vary depending on the specific requirements of the device and the technology used. Advanced fabrication techniques and materials may also be employed to achieve higher levels of performance and integration.
How do you manufacture a Microtrace Substrate?
Manufacturing a microtrace substrate involves a series of intricate processes that require precision and expertise. Here’s a general outline of the steps involved in manufacturing a microtrace substrate:
- Substrate Selection: Choose a suitable substrate material based on the requirements of the microelectronic device. Common substrate materials include silicon, gallium arsenide, silicon carbide, and various compound semiconductors.
- Cleaning and Preparation: Clean the substrate surface thoroughly to remove any contaminants and ensure a clean starting surface. This step is crucial to prevent defects and ensure uniformity in subsequent processing steps.
- Epitaxial Growth (Optional): If required for the device design, grow epitaxial layers on the substrate surface using techniques such as chemical vapor deposition (CVD) or molecular beam epitaxy (MBE). Epitaxial layers can modify the electrical properties of the substrate and create specific structures.
- Photolithography: Define the desired pattern of features on the substrate surface using photolithography. This process involves depositing a photosensitive material (photoresist) onto the substrate, exposing it to UV light through a photomask, and developing it to remove the exposed regions, leaving behind a patterned resist mask.
- Etching: Transfer the pattern from the resist mask onto the substrate surface through etching. Different etching techniques, such as dry etching (plasma etching) or wet etching (chemical etching), may be used depending on the substrate material and the desired feature geometry.
- Thin Film Deposition: Deposit thin films of materials such as metals (e.g., aluminum, copper) or insulators (e.g., silicon dioxide, silicon nitride) onto the substrate surface using techniques like physical vapor deposition (PVD), chemical vapor deposition (CVD), or atomic layer deposition (ALD). These thin films are used to create interconnects, insulation layers, and other device structures.
- Metallization: Pattern and etch the deposited metal films to create metal traces and interconnects. Multiple metal layers may be deposited and patterned to create complex interconnect structures.
- Dielectric Deposition and Etching: Deposit insulating layers (dielectrics) onto the substrate surface to electrically isolate different device components and interconnects. These dielectric layers are patterned and etched to create vias and isolate regions as needed.
- Planarization (Optional): Use planarization techniques such as chemical mechanical polishing (CMP) to flatten the substrate surface and remove any topographical irregularities introduced during previous processing steps.
- Final Processing: Perform additional processing steps such as annealing, passivation, and surface treatments to improve device performance, reliability, and stability.
- Quality Control and Testing: Implement quality control measures throughout the manufacturing process to ensure the integrity and functionality of the microtrace substrate. After fabrication, the substrates undergo testing to verify their electrical properties, structural integrity, and reliability.
Manufacturing microtrace substrates requires expertise in semiconductor processing techniques, equipment operation, and quality control procedures. Each step in the process must be carefully executed to achieve the desired device performance and reliability.
How much should a Microtrace Substrate cost?
The cost of a microtrace substrate can vary widely depending on several factors, including:
- Substrate Material: Different substrate materials have varying costs. Silicon substrates are generally less expensive compared to compound semiconductor substrates like gallium arsenide or silicon carbide.
- Size and Complexity: The size and complexity of the substrate, including the number of layers, features, and intricacy of the design, can significantly impact the cost. Larger substrates with more complex designs typically require more manufacturing steps and resources, thus increasing the cost.
- Manufacturing Technology: The specific manufacturing technology and processes used to fabricate the substrate also influence the cost. Advanced fabrication techniques and equipment may require higher capital investment and operational expenses, leading to higher substrate costs.
- Quality and Yield Requirements: Substrates manufactured to tighter tolerances and higher quality standards often command a higher price. Additionally, substrates with higher yields (i.e., fewer defects per unit area) may cost more due to the increased manufacturing precision and quality control measures required.
- Volume and Supply Chain Factors: The volume of substrates ordered and the dynamics of the supply chain can affect pricing. Bulk orders typically result in lower unit costs due to economies of scale, while factors such as material availability, lead times, and supplier relationships can also impact pricing.
- Market Demand: Market demand and competition can influence substrate pricing. In a competitive market with multiple suppliers, pricing may be more competitive, whereas limited availability or high demand for specialized substrates may lead to higher prices.
Given these variables, it’s challenging to provide a specific cost for a microtrace substrate without knowing the specific requirements and context of the application. However, microtrace substrates can range from a few dollars to several hundred dollars or more per unit, depending on the factors mentioned above. Customers typically work closely with substrate manufacturers to determine the most cost-effective solution that meets their performance and budgetary requirements.
What is Microtrace Substrate base material?
The base material used for microtrace substrates can vary depending on the specific requirements of the application and the fabrication process. However, some common materials used as substrates for microelectronic devices, including those with microtraces, include:
- Silicon (Si): Silicon is the most widely used substrate material in microelectronics due to its abundance, excellent electrical properties, and well-established manufacturing processes. Silicon substrates are used in a wide range of applications, from integrated circuits to MEMS (Microelectromechanical Systems) devices.
- Gallium Arsenide (GaAs): Gallium arsenide substrates are commonly used for high-frequency and high-speed electronic devices, such as RF (Radio Frequency) amplifiers and microwave components. GaAs substrates offer superior electron mobility compared to silicon, making them well-suited for applications requiring high-frequency operation.
- Silicon Carbide (SiC): Silicon carbide substrates are known for their excellent thermal conductivity, high breakdown voltage, and resistance to high temperatures and harsh environments. SiC substrates are often used in power electronics, high-temperature sensors, and devices requiring high-power density.
- Sapphire (Al2O3): Sapphire substrates, specifically single-crystal sapphire, are used in various applications where high optical transparency, mechanical strength, and thermal stability are required. Sapphire substrates find applications in optoelectronics, LEDs (Light-Emitting Diodes), and RF devices.
- Glass: Glass substrates are used in certain microelectronic applications, particularly those involving optical devices, displays, and sensors. Glass substrates offer advantages such as optical transparency, flatness, and compatibility with certain deposition and patterning processes.
- Other Compound Semiconductors: In addition to GaAs and SiC, other compound semiconductor materials such as indium phosphide (InP), gallium nitride (GaN), and zinc oxide (ZnO) are used as substrates for specific applications requiring unique electrical, optical, or thermal properties.
The choice of substrate material depends on factors such as the electrical properties required for the device, the intended application, thermal considerations, and compatibility with the fabrication process. Each substrate material has its advantages and limitations, and selecting the appropriate substrate is crucial for achieving desired device performance and reliability.
Which company makes Microtrace Substrates?
Several companies manufacture Microtrace Substrates. These companies include well-known semiconductor manufacturers, specialized microelectronics manufacturing companies, and research institutions. In the semiconductor industry, companies such as Intel, TSMC, Samsung, and NVIDIA have extensive experience and technology in the manufacture of Microtrace Substrates. Additionally, specialized microelectronics manufacturing companies like GLOBALFOUNDRIES, Tower Semiconductor, SMIC, among others, provide production services for Microtrace Substrates.
As a newly emerging company, our company also manufactures Microtrace Substrates. We have advanced manufacturing equipment and technology, as well as an experienced team dedicated to the field of microelectronics manufacturing for many years. Our manufacturing process is carefully designed and optimized to ensure the production of high-quality, high-performance Microtrace Substrates. We prioritize technological innovation and quality management, continuously improving production efficiency and product quality.
Our company can customize Microtrace Substrates according to customer requirements, including different materials, sizes, thicknesses, and design specifications. We can provide comprehensive services from raw material procurement to production processing, quality inspection, and delivery, ensuring customers receive satisfactory products and services. We are committed to establishing long-term partnerships with customers, developing together, and sharing success.
With our company’s professional expertise and quality service, we believe we have the capability to succeed in the manufacturing of Microtrace Substrates and provide customers with competitive solutions.
What are the 7 qualities of good customer service?
Good customer service is essential for building strong relationships with customers and fostering loyalty. Seven qualities of good customer service include:
- Responsiveness: Being prompt and attentive to customer inquiries, concerns, and requests. Responding quickly to customer needs demonstrates that their satisfaction is a priority.
- Empathy: Showing understanding and compassion towards customers’ situations or issues. Empathizing with customers helps to build rapport and trust, even in challenging situations.
- Effective Communication: Communicating clearly and effectively with customers, whether it’s through verbal communication, written correspondence, or online interactions. Good communication ensures that customers receive accurate information and feel valued.
- Problem-solving Skills: Being able to identify and address customer problems or issues efficiently and effectively. Good problem-solving skills involve analyzing situations, finding solutions, and taking appropriate action to resolve customer concerns.
- Product Knowledge: Having a thorough understanding of the products or services offered by the company. Knowledgeable customer service representatives can provide accurate information, answer questions, and offer guidance to customers, enhancing their overall experience.
- Professionalism: Maintaining professionalism and courtesy in all interactions with customers. Treating customers with respect, patience, and professionalism, regardless of the situation, helps to create a positive impression and build trust.
- Follow-up and Follow-through: Following up with customers to ensure that their needs have been met and their concerns have been addressed satisfactorily. Additionally, following through on commitments and promises made to customers helps to build credibility and reinforce trust in the company.
By embodying these qualities, businesses can deliver exceptional customer service experiences that leave a lasting impression and contribute to customer satisfaction and loyalty.
FAQs
What are Microtrace Substrates?
Microtrace Substrates are materials used in the fabrication of microelectronic devices or components. They serve as the foundation upon which various components such as transistors, diodes, and integrated circuits are built.
What are the key features of Microtrace Substrates?
Key features of Microtrace Substrates include precise dimensions, excellent electrical properties, thermal conductivity, compatibility with manufacturing processes, and mechanical stability.
What materials are used to manufacture Microtrace Substrates?
Common materials used for Microtrace Substrates include silicon, gallium arsenide, silicon carbide, sapphire, and other compound semiconductors.
What applications are Microtrace Substrates used in?
Microtrace Substrates are used in a wide range of applications, including integrated circuits, MEMS (Microelectromechanical Systems), sensors, RF (Radio Frequency) devices, power electronics, and optoelectronics.
How are Microtrace Substrates fabricated?
The fabrication process for Microtrace Substrates involves steps such as substrate preparation, epitaxial growth (if required), photolithography, etching, thin film deposition, metallization, dielectric deposition, and final processing.
What are the advantages of using Microtrace Substrates?
Advantages of Microtrace Substrates include high precision, reliability, scalability, compatibility with advanced technologies, and the ability to integrate complex device structures on a small scale.
What factors should be considered when choosing a Microtrace Substrate?
Factors to consider when choosing a Microtrace Substrate include the electrical properties required for the device, thermal conductivity, mechanical stability, compatibility with fabrication processes, and cost-effectiveness.
Where can I purchase Microtrace Substrates?
Microtrace Substrates can be purchased from semiconductor manufacturers, specialized microelectronics manufacturing companies, and distributors specializing in semiconductor materials.