IPC Class III PCB Manufacturer
IPC Class III PCB Manufacturer,IPC Class III PCBs represent the pinnacle of quality and reliability in the realm of printed circuit boards. Engineered to endure extreme conditions and stringent performance requirements, IPC Class III PCBs adhere to meticulous design guidelines and manufacturing standards. These circuit boards are crafted with advanced materials and manufacturing techniques, ensuring optimal performance in critical applications such as aerospace, defense, medical devices, and automotive systems. IPC Class III PCBs undergo rigorous testing and inspection processes to guarantee adherence to the highest quality standards, providing unparalleled reliability and longevity. With their ability to withstand harsh environments, temperature extremes, and mechanical stress, IPC Class III PCBs offer peace of mind to industries where failure is not an option. From complex signal integrity considerations to robust thermal management solutions, these PCBs exemplify excellence in electronic engineering and manufacturing, delivering uncompromising performance and reliability.
What is an IPC Class III PCB?
IPC Class III PCB (Printed Circuit Board) refers to a stringent standard set by the IPC (Association Connecting Electronics Industries) for the quality and reliability of printed circuit boards. This classification is primarily utilized in industries where the reliability and durability of electronic components are critical, such as aerospace, military, medical devices, and automotive applications.
To meet the IPC Class III standard, PCBs must adhere to rigorous requirements regarding design, manufacturing processes, materials used, and inspection criteria. These requirements are significantly more stringent compared to IPC Class I and Class II standards.
Some key characteristics of IPC Class III PCBs include:
- High Reliability:IPC Class III PCBs are designed to withstand harsh environmental conditions, extreme temperatures, and high levels of vibration and shock.
- Tight Tolerances: These PCBs have strict tolerances for dimensions, hole sizes, and trace widths to ensure precise functionality and compatibility with other electronic components.
- Advanced Materials: Class III PCBs often require the use of advanced materials such as high-performance substrates and specialized coatings to enhance durability and reliability.
- Robust Manufacturing Processes: Manufacturers must adhere to rigorous quality control measures throughout the PCB fabrication process, including precise etching, drilling, and soldering techniques.
- Thorough Inspection: IPC Class III PCBs undergo comprehensive inspection procedures, including visual inspection, electrical testing, and reliability testing, to identify and mitigate any defects or potential failures.
- Longevity and Endurance: These PCBs are designed to have a long operational life and withstand extended periods of use without degradation or failure.
Overall, IPC Class III PCBs are engineered to meet the most demanding requirements for reliability, durability, and performance in critical electronic applications, making them essential components in mission-critical systems where failure is not an option.
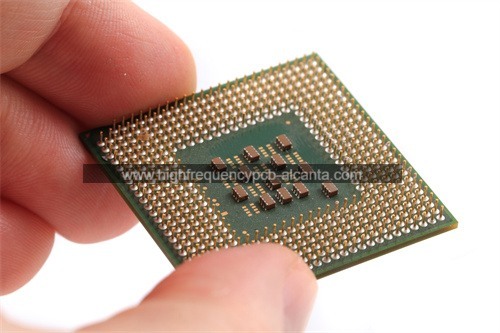
IPC Class III PCB Manufacturer
What are the IPC Class III PCB Design Guidelines?
IPC Class III PCB design guidelines encompass a range of specifications and recommendations aimed at ensuring the highest level of reliability and performance in printed circuit board designs. Here are some key aspects typically covered by IPC Class III PCB design guidelines:
- Component Placement and Orientation: Components should be placed and oriented to minimize the risk of interference, optimize signal integrity, and facilitate efficient heat dissipation. Critical components, such as high-frequency devices or those sensitive to environmental factors, should receive particular attention.
- Trace Routing and Impedance Control: Trace routing should adhere to specified guidelines to minimize signal degradation, crosstalk, and electromagnetic interference (EMI). Impedance control ensures consistent signal integrity, especially for high-speed digital or analog signals.
- Grounding and Power Distribution: Proper grounding and power distribution are crucial for minimizing noise, ensuring stable power delivery, and preventing ground loops. Separate analog and digital ground planes may be necessary to prevent interference between sensitive circuitry.
- Thermal Management: Effective thermal management is essential for preventing overheating and ensuring the reliability of components, particularly in applications subject to high temperatures or thermal cycling. This may involve incorporating thermal vias, heat sinks, or thermal pads to dissipate heat efficiently.
- Signal Integrity: Designs should consider signal integrity principles to minimize reflections, signal loss, and timing errors. This includes controlling trace length, impedance matching, and minimizing discontinuities such as vias or bends.
- Reliability and Durability: PCBs must be designed to withstand environmental stressors, mechanical shock, vibration, and temperature extremes. This may involve selecting appropriate materials, ensuring robust mechanical support for components, and employing conformal coatings or encapsulation for protection.
- Design for Manufacturability (DFM): PCB designs should be optimized for manufacturability to minimize production costs and ensure consistent quality. This includes adhering to standard design rules, minimizing fabrication complexity, and providing clear documentation for assembly and testing.
- Testing and Inspection: Design guidelines may include recommendations for testing and inspection procedures to verify the integrity and functionality of the finished PCB. This may involve in-circuit testing, boundary scan testing, and visual inspection to identify and rectify any defects.
By adhering to IPC Class III PCB design guidelines, designers can create robust, reliable, and high-performance circuit boards suitable for use in demanding applications where reliability is paramount.
What is the IPC Class III PCB Fabrication Process?
The IPC Class III PCB fabrication process involves several steps to ensure that the printed circuit boards meet the stringent quality and reliability standards required for use in critical applications. Here’s an overview of the typical fabrication process:
- Design Verification: Before fabrication begins, the PCB design undergoes thorough verification to ensure that it meets the specifications and requirements outlined in the design guidelines. This verification may involve design rule checks (DRC) and design for manufacturability (DFM) analysis.
- Material Selection: High-quality materials are selected based on the specific requirements of the PCB design, including substrate materials (e.g., FR-4, polyimide), copper foil thickness, and surface finish options (e.g., HASL, ENIG, OSP).
- Preparation of Substrate: The substrate material is prepared by cutting it to the required dimensions and cleaning it thoroughly to remove any contaminants that could affect the adhesion of the copper layers.
- Copper Cladding: Copper foil is bonded to one or both sides of the substrate using an adhesive or lamination process. The copper foil is then etched to remove excess copper, leaving behind the desired circuit pattern.
- Drilling: Precision drilling machines are used to create holes for through-hole components and vias. The holes are drilled to precise diameters and locations according to the PCB design.
- Electroless Copper Deposition: After drilling, the walls of the holes are coated with a thin layer of electroless copper to facilitate the plating process and ensure good electrical conductivity.
- Through-Hole Plating: Through-hole plating is performed to create electrical connections between the layers of the PCB. The plated-through holes are filled with copper using an electroplating process, ensuring robust electrical connections.
- Outer Layer Imaging: The outer layer circuit patterns are transferred onto the copper foil using a photoresist and photolithography process. UV light is used to expose the photoresist, and then the unexposed areas are removed through development, leaving behind the circuit pattern.
- Etching: Chemical etching is used to remove the excess copper from the outer layers, leaving behind the desired circuit traces and pads. The remaining photoresist is then stripped away, revealing the copper traces.
- Surface Finish: Surface finish processes such as HASL (Hot Air Solder Leveling), ENIG (Electroless Nickel Immersion Gold), or OSP (Organic Solderability Preservatives) are applied to protect the exposed copper surfaces and provide solderability for component attachment.
- Quality Control and Inspection: Throughout the fabrication process, quality control measures are implemented to ensure that the PCBs meet the IPC Class III standards. Inspection techniques such as automated optical inspection (AOI) and electrical testing are used to detect any defects or irregularities.
- Documentation and Traceability: Detailed documentation of the fabrication process, including materials used, process parameters, and inspection results, is maintained to ensure traceability and compliance with regulatory requirements.
By following these steps and adhering to strict quality control measures, manufacturers can produce IPC Class III PCBs that meet the highest standards of reliability, durability, and performance for use in mission-critical applications.
How do you manufacture an IPC Class III PCB?
Manufacturing an IPC Class III PCB involves adhering to stringent standards and processes to ensure the highest level of reliability, durability, and performance. Here’s a detailed overview of the steps involved in manufacturing an IPC Class III PCB:
- Design Verification: Before manufacturing begins, the PCB design undergoes thorough verification to ensure compliance with IPC Class III standards. This includes design rule checks (DRC), design for manufacturability (DFM) analysis, and design review to identify and address any potential issues.
- Material Selection: High-quality materials are selected based on the specific requirements of the PCB design and the application. This includes choosing the appropriate substrate material (e.g., FR-4, polyimide), copper foil thickness, and surface finish options (e.g., HASL, ENIG, OSP).
- Preparation of Substrate: The substrate material is prepared by cutting it to the required dimensions and cleaning it thoroughly to remove any contaminants that could affect the adhesion of the copper layers.
- Copper Cladding: Copper foil is bonded to one or both sides of the substrate using an adhesive or lamination process. The copper foil is then etched to remove excess copper, leaving behind the desired circuit pattern.
- Drilling: Precision drilling machines are used to create holes for through-hole components and vias. The holes are drilled to precise diameters and locations according to the PCB design.
- Electroless Copper Deposition: After drilling, the walls of the holes are coated with a thin layer of electroless copper to facilitate the plating process and ensure good electrical conductivity.
- Through-Hole Plating: Through-hole plating is performed to create electrical connections between the layers of the PCB. The plated-through holes are filled with copper using an electroplating process, ensuring robust electrical connections.
- Outer Layer Imaging: The outer layer circuit patterns are transferred onto the copper foil using a photoresist and photolithography process. UV light is used to expose the photoresist, and then the unexposed areas are removed through development, leaving behind the circuit pattern.
- Etching: Chemical etching is used to remove the excess copper from the outer layers, leaving behind the desired circuit traces and pads. The remaining photoresist is then stripped away, revealing the copper traces.
- Surface Finish: Surface finish processes such as HASL (Hot Air Solder Leveling), ENIG (Electroless Nickel Immersion Gold), or OSP (Organic Solderability Preservatives) are applied to protect the exposed copper surfaces and provide solderability for component attachment.
- Component Assembly: Surface mount and through-hole components are assembled onto the PCB using automated pick-and-place machines and soldering techniques such as reflow soldering or wave soldering.
- Testing and Inspection: Comprehensive testing and inspection are performed throughout the manufacturing process to ensure compliance with IPC Class III standards. This includes visual inspection, automated optical inspection (AOI), electrical testing, and reliability testing to identify and rectify any defects or irregularities.
- Documentation and Traceability: Detailed documentation of the manufacturing process, including materials used, process parameters, inspection results, and traceability information, is maintained to ensure accountability and compliance with regulatory requirements.
By following these steps and adhering to strict quality control measures, manufacturers can produce IPC Class III PCBs that meet the highest standards of reliability, durability, and performance for use in mission-critical applications.
How much should an IPC Class III PCB cost?
The cost of an IPC Class III PCB can vary significantly depending on several factors, including the complexity of the design, the quality of materials used, the manufacturing processes involved, and the quantity ordered. Here are some key factors that can influence the cost:
- Design Complexity: PCBs with intricate layouts, dense component placement, and high layer counts typically require more advanced manufacturing processes and may incur higher costs.
- Material Selection: High-quality materials, such as advanced substrates and specialty coatings, may come at a premium compared to standard materials. The choice of materials can impact the performance, reliability, and cost of the PCB.
- Manufacturing Processes: IPC Class III PCBs require stringent manufacturing processes, including tight tolerances, advanced inspection techniques, and rigorous quality control measures. These processes may involve additional time, labor, and resources, contributing to higher production costs.
- Quantity:Economies of scale often apply in PCB manufacturing, meaning that larger production quantities can lead to lower per-unit costs. However, smaller batch sizes may incur setup fees and higher overhead costs, potentially increasing the cost per unit.
- Additional Services: Additional services such as design verification, prototyping, testing, and certification may incur additional costs but are essential for ensuring compliance with IPC Class III standards and meeting customer requirements.
- Supplier Selection: The choice of PCB manufacturer or supplier can also impact the cost. Suppliers with advanced capabilities, certifications, and a track record of quality and reliability may command higher prices.
Given these factors, it’s challenging to provide a precise cost estimate for an IPC Class III PCB without specific details about the design requirements, manufacturing specifications, and quantity needed. Generally, IPC Class III PCBs are expected to be more expensive than lower-class PCBs (IPC Class I or II) due to their stringent quality and reliability requirements.
For a more accurate cost estimate, it’s recommended to consult with PCB manufacturers or suppliers, providing them with detailed specifications and quantity requirements to obtain quotes tailored to your project’s needs.
Which company manufactures IPC Class III PCBs?
There are many companies that manufacture IPC Class III PCBs, especially those focused on high-end electronic products and applications. Some well-known companies include Foxconn, Sanmina, TTM Technologies, and other specialized PCB manufacturers.
The production of IPC Class III PCBs requires highly specialized technology and equipment to ensure compliance with stringent quality standards and reliability requirements. These companies typically possess advanced manufacturing equipment, rigorous quality control processes, and experienced engineering teams to meet customers’ demands for high-reliability circuit boards.
As for our company, we also manufacture IPC Class III PCBs. We have advanced production equipment and technology, as well as an experienced team capable of meeting customers’ needs for high-quality, high-reliability PCBs. We strictly adhere to IPC standards and employ advanced quality control processes to ensure that each PCB meets the highest quality standards.
Our company values customer needs and satisfaction, offering customized solutions and maintaining close communication with customers throughout the design, manufacturing, testing, and delivery processes. Whether in aerospace, defense, medical devices, or automotive industries, we can provide reliable IPC Class III PCBs to support and safeguard our customers’ projects.
What are the 7 qualities of good customer service?
Good customer service is characterized by several key qualities that contribute to a positive experience for the customer. Here are seven qualities often associated with excellent customer service:
- Responsiveness: Good customer service involves promptly addressing customer inquiries, concerns, and requests. This includes responding to emails, calls, and messages in a timely manner and ensuring that customers feel heard and valued.
- Empathy: Empathy is essential for understanding and relating to customers’ emotions, needs, and perspectives. Good customer service representatives demonstrate empathy by actively listening to customers, acknowledging their feelings, and showing genuine concern for their well-being.
- Clarity: Effective communication is crucial for providing good customer service. This involves conveying information clearly and concisely, avoiding jargon or technical language, and ensuring that customers understand the information provided.
- Professionalism: Professionalism encompasses a range of behaviors, including politeness, courtesy, and respectfulness. Good customer service representatives maintain a professional demeanor at all times, even in challenging situations, and strive to uphold the company’s reputation.
- Problem-solving skills: Customers may encounter issues or problems that require resolution. Good customer service involves effectively identifying and addressing these issues, offering solutions or alternatives, and following through to ensure customer satisfaction.
- Proactivity: Anticipating customer needs and taking proactive steps to address them is a hallmark of excellent customer service. This may involve offering helpful suggestions, providing information or assistance before it’s requested, and going above and beyond to exceed customer expectations.
- Consistency: Consistency in service delivery is essential for building trust and loyalty with customers. Good customer service should be consistent across all touchpoints and interactions, ensuring that customers receive the same high-quality experience every time they engage with the company.
By embodying these qualities, businesses can cultivate a reputation for providing exceptional customer service and foster long-lasting relationships with their customers.
FAQs
What is IPC Class III?
IPC Class III refers to the highest standard of quality and reliability for printed circuit boards (PCBs) set by the IPC (Association Connecting Electronics Industries). It is typically used in industries where reliability and durability are critical, such as aerospace, military, medical devices, and automotive applications.
What are the key characteristics of IPC Class III PCBs?
IPC Class III PCBs are characterized by stringent requirements for design, manufacturing processes, materials, and inspection criteria. They are designed to withstand harsh environmental conditions, extreme temperatures, and high levels of vibration and shock.
Why is IPC Class III important?
IPC Class III ensures that PCBs meet the highest standards of quality, reliability, and performance, particularly in mission-critical applications where failure is not an option. Compliance with IPC Class III standards provides assurance to customers and regulatory agencies regarding the reliability and durability of electronic components.
What are the differences between IPC Class I, II, and III?
IPC Class I, II, and III represent different levels of quality and reliability for PCBs. Class I is the lowest standard, suitable for general consumer electronics. Class II is a higher standard, suitable for industrial and commercial applications. Class III is the highest standard, suitable for applications where reliability and durability are paramount.
What are the design guidelines for IPC Class III PCBs?
IPC Class III PCB design guidelines include specifications and recommendations for component placement, trace routing, grounding, thermal management, signal integrity, reliability, and durability. These guidelines ensure that PCB designs meet the stringent requirements for reliability and performance.
How are IPC Class III PCBs manufactured?
IPC Class III PCBs are manufactured using advanced processes and materials to meet the stringent quality and reliability standards. The manufacturing process involves substrate preparation, copper cladding, drilling, electroplating, imaging, etching, surface finishing, component assembly, testing, inspection, and documentation.
How much do IPC Class III PCBs cost?
The cost of IPC Class III PCBs can vary depending on factors such as design complexity, material selection, manufacturing processes, quantity ordered, and additional services required. Generally, IPC Class III PCBs are more expensive than lower-class PCBs due to their stringent quality and reliability requirements.