Insulating Substrate Manufacturer
Insulating Substrate Manufacturer,Insulating Substrates are essential components in electronic circuits, providing electrical isolation between conductive layers and ensuring reliable performance. These substrates are made from materials with high dielectric strength and low electrical conductivity, such as ceramics, glass epoxy, or polymers. They support the circuit’s electrical pathways while preventing unwanted electrical interference and short circuits. Insulating substrates are crucial for applications involving high voltages or sensitive electronic components, including power supplies, automotive electronics, and high-frequency devices. Their role in maintaining signal integrity and protecting against electrical faults makes them fundamental in the design and manufacture of reliable and efficient electronic systems.
What is Insulating Substrate?
An insulating substrate, often referred to as a dielectric substrate, is a key component in electronic and electrical systems, providing a foundational layer that separates conductive paths and maintains electrical isolation. These substrates are crucial in ensuring the functionality and reliability of various electronic devices, including printed circuit boards (PCBs), integrated circuits (ICs), and other electronic components.
The primary function of an insulating substrate is to prevent electrical shorts and cross-talk between different conductive elements within a device. This is achieved by offering high electrical resistance and minimal leakage current, thus maintaining the integrity of the electrical signals and power distribution. The substrate also provides mechanical support, which is essential for the structural stability of the electronic components.
Insulating substrates are made from various materials, each chosen based on specific application requirements. Common materials include ceramic, plastic, and composite materials. For instance, ceramic substrates are favored in high-frequency and high-power applications due to their excellent thermal conductivity and stability. Plastic substrates, such as those made from epoxy resins or polyimides, are used in more general applications due to their flexibility and ease of processing.
In addition to electrical isolation, insulating substrates can also contribute to thermal management by dissipating heat generated during the operation of electronic devices. This helps prevent overheating and prolongs the lifespan of the components.
Overall, the choice of insulating substrate material and its properties significantly impact the performance, reliability, and efficiency of electronic devices.
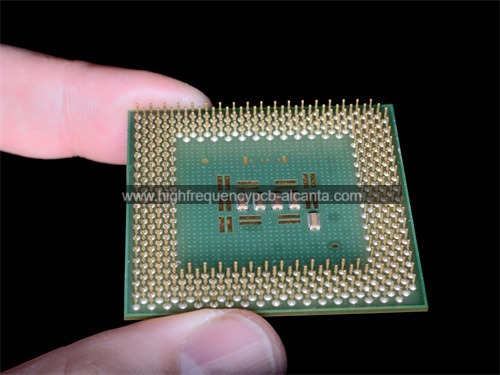
Insulating Substrate Manufacturer
What are the Insulating Substrate Design Guidelines?
Designing insulating substrates involves several key guidelines to ensure optimal performance and reliability of electronic devices. Here are some essential design guidelines for insulating substrates:
- Material Selection: Choose an insulating material based on the specific requirements of the application. For high-frequency or high-power applications, materials like ceramics with high thermal conductivity and low dielectric losses are preferred. For general applications, polymers or composites might be suitable due to their flexibility and cost-effectiveness.
- Electrical Insulation: Ensure that the insulating substrate provides sufficient electrical resistance to prevent short circuits and leakage currents between conductive layers. The dielectric strength of the substrate material should be high enough to handle the maximum operating voltage.
- Thermal Management: Consider the thermal conductivity of the substrate material to effectively dissipate heat generated by electronic components. Proper thermal management prevents overheating and improves the overall reliability of the device.
- Mechanical Support: The substrate must provide adequate mechanical support for the electronic components. It should be robust enough to withstand mechanical stresses during assembly and operation, including thermal expansion and contraction.
- Thickness and Tolerance: Design the substrate with appropriate thickness and tolerance to meet the specific requirements of the circuit layout. Variations in substrate thickness can affect signal integrity and overall performance. Ensure tight tolerance control to maintain consistency and reliability.
- Surface Finish: The surface finish of the substrate should be compatible with the subsequent manufacturing processes, such as soldering or bonding. Surface roughness and cleanliness are important for ensuring good adhesion of conductive layers and components.
- Compatibility with Manufacturing Processes: Ensure that the substrate material and design are compatible with the manufacturing processes used for the final product. This includes considerations for etching, plating, and other fabrication techniques.
- Environmental Considerations: Take into account the operating environment of the device, including exposure to moisture, chemicals, or extreme temperatures. Choose substrate materials that can withstand environmental conditions without degrading in performance.
- Signal Integrity: For high-speed or high-frequency applications, ensure that the substrate design minimizes signal loss and electromagnetic interference. Proper grounding, shielding, and layout practices are essential to maintain signal integrity.
- Cost and Efficiency: Balance performance requirements with cost considerations. While high-performance materials may offer superior properties, they may also be more expensive. Optimize the design to achieve the desired performance within budget constraints.
By following these guidelines, designers can create insulating substrates that enhance the performance, reliability, and longevity of electronic devices while meeting specific application requirements.
What is the Insulating Substrate Fabrication Process?
The fabrication process for insulating substrates involves several steps, each crucial for ensuring the quality and performance of the final product. Here’s an overview of the typical steps involved in the fabrication of insulating substrates:
- Material Selection and Preparation: The process begins with selecting the appropriate insulating material based on the specific requirements of the application. This material could be ceramic, polymer, or composite. Once selected, the material is prepared for processing, which might involve cutting it into appropriate sizes or shapes.
- Substrate Formation: The chosen material is shaped into the desired substrate form. For ceramic substrates, this typically involves pressing or molding the raw ceramic powders into thin sheets or discs. For polymer substrates, processes like extrusion or casting might be used to form the substrate.
- Sintering (for Ceramics): In the case of ceramic substrates, the shaped material is subjected to a sintering process. This involves heating the material to a high temperature to bond the ceramic particles together, increasing the substrate’s mechanical strength and electrical insulation properties.
- Lamination (for Polymers): For polymer substrates, lamination involves stacking multiple layers of the polymer material and bonding them together using heat and pressure. This creates a multi-layered substrate with enhanced mechanical and electrical properties.
- Surface Treatment: The substrate surface may undergo treatment to improve adhesion properties for subsequent layers or components. This can include processes such as polishing, cleaning, or applying a primer to ensure a smooth and clean surface.
- Patterning and Etching: If the substrate is part of a printed circuit board (PCB), patterning and etching are used to define conductive paths. A photosensitive layer is applied to the substrate, and a pattern is exposed using a photomask. The exposed areas are then etched away to create the desired circuit patterns.
- Coating and Plating: To enhance the substrate’s electrical performance and protect it from environmental factors, additional coatings or plating may be applied. This can include layers of metal (such as copper) for electrical conductivity or protective coatings to resist moisture and chemicals.
- Inspection and Quality Control: The fabricated substrates undergo rigorous inspection and quality control to ensure they meet the required specifications. This includes checking for defects, verifying dimensions, and testing electrical properties.
- Cutting and Finishing: The final substrates are cut to the required size and shape for integration into electronic devices. Additional finishing processes might be applied to meet specific design requirements or to prepare the substrate for assembly with other components.
- Packaging and Delivery: Once the substrates pass quality control, they are packaged and prepared for delivery. Packaging ensures that the substrates are protected during transit and storage until they are ready for use in electronic assemblies.
This fabrication process ensures that insulating substrates meet the required performance criteria, including electrical insulation, thermal management, and mechanical support, while also adhering to manufacturing standards and specifications.
How Do You Manufacture Insulating Substrate?
Manufacturing insulating substrates involves a series of steps designed to ensure high performance and reliability. Here’s a detailed overview of the manufacturing process for insulating substrates:
- Material Selection: Choose the appropriate insulating material based on application requirements. Common materials include ceramics (such as alumina or zirconia), polymers (such as polyimide or epoxy), and composites. Material selection impacts the substrate’s electrical, thermal, and mechanical properties.
- Material Preparation: Prepare the selected material for processing. This step involves obtaining raw materials, mixing, and possibly pre-treating them. For ceramics, this may include grinding powders to achieve the desired particle size. For polymers, it might involve melting or dissolving the material.
- Forming the Substrate:
– Ceramics: Shape the ceramic material into the desired form using techniques like pressing, casting, or extrusion. The material is shaped into sheets, discs, or other configurations based on the final substrate design.
– Polymers: Form the polymer material into substrate shapes through processes such as extrusion, molding, or casting. Lamination can also be used to create multi-layered substrates from polymer films.
- Sintering (for Ceramics): Subject the shaped ceramic substrate to a sintering process. This involves heating the substrate to high temperatures in a kiln to fuse the ceramic particles together, enhancing its strength and electrical insulation properties.
- Lamination (for Polymers): For multi-layered polymer substrates, apply layers of polymer material and bond them together using heat and pressure in a lamination process. This creates a cohesive, multi-layered substrate with improved mechanical and electrical characteristics.
- Surface Treatment:Prepare the substrate surface for subsequent processing. This may include cleaning, polishing, or applying a primer to ensure good adhesion of additional layers or components.
- Patterning and Etching:
– Photolithography: Apply a photosensitive layer to the substrate. Expose it to UV light through a photomask to define circuit patterns. The exposed areas are then chemically treated to create the desired circuit design.
– Etching: Remove unwanted material from the substrate using chemical or plasma etching processes to create precise patterns and features.
- Coating and Plating: Apply protective coatings or metal plating to the substrate as needed. This can include layers of conductive metals (such as copper) for electrical paths or protective coatings to enhance resistance to environmental factors like moisture or chemicals.
- Inspection and Quality Control: Perform rigorous inspections and quality control tests to ensure that the substrate meets required specifications. This includes checking for defects, verifying dimensional accuracy, and testing electrical and thermal properties.
- Cutting and Finishing: Cut the substrate to the required size and shape, and apply any additional finishing processes to meet design requirements. This may involve trimming edges or adding features to prepare the substrate for integration into electronic devices.
- Packaging and Delivery: Package the finished substrates to protect them during transport and storage. Ensure that they are properly labeled and prepared for delivery to customers or for use in further manufacturing processes.
By following these steps, manufacturers can produce high-quality insulating substrates that meet the performance and reliability standards required for various electronic and electrical applications.
How Much Should Insulating Substrate Cost?
The cost of insulating substrates can vary widely based on several factors, including the type of material, complexity of the design, and specific application requirements. Here’s a detailed overview of factors that influence the cost of insulating substrates:
- Material Type: Different materials come with varying price points. For instance, ceramic substrates, which are used in high-frequency or high-power applications, tend to be more expensive due to their specialized properties and manufacturing processes. Plastic or polymer substrates, used in more general applications, are typically less expensive.
- Substrate Thickness and Size: The thickness and size of the substrate affect the cost. Larger substrates or those with non-standard thicknesses may require additional processing and materials, increasing the overall cost.
- Design Complexity: Complex designs, including multi-layer structures or substrates with intricate patterns, require more advanced manufacturing techniques and additional design work. This complexity can drive up the cost compared to simpler designs.
- Manufacturing Processes: The cost can also be influenced by the specific manufacturing processes used. For example, advanced processes like high-precision etching or plating may add to the cost. Additionally, custom or low-volume production runs can be more expensive than standard, high-volume production.
- Surface Finish and Coatings: Special surface finishes or coatings, such as those required for enhanced thermal or electrical performance, can add to the cost. The type and quality of these finishes impact both the performance and the price.
- Environmental and Performance Requirements: Substrates designed to withstand harsh environmental conditions or high-performance applications (e.g., high-temperature or high-frequency operations) may use specialized materials or require additional testing, which can increase the cost.
- Volume and Quantity: The cost per unit can decrease with higher volume orders. Bulk purchasing or long-term contracts can often lead to cost savings, while custom or small-batch orders may be more expensive.
- Supplier and Region: The cost can vary based on the supplier and geographic location. Different suppliers may offer varying pricing structures, and regional factors such as transportation costs and tariffs can also affect the overall price.
- Lead Time and Availability: Shorter lead times or expedited production can increase the cost. Availability of materials and current market conditions also play a role in pricing.
Overall, while insulating substrates can range from relatively inexpensive for basic polymer types to more costly for advanced ceramics or custom designs, the final cost should be evaluated in the context of the specific application requirements and overall project budget.
What is Insulating Substrate Base Material?
Insulating substrate base material refers to the foundational material used in the construction of insulating substrates. It provides the essential properties of electrical insulation, mechanical support, and thermal management for electronic devices. Here’s a detailed look at insulating substrate base materials:
- Ceramic: Ceramic substrates are known for their excellent electrical insulation, high thermal conductivity, and mechanical strength. They are often used in high-frequency and high-power applications due to their ability to handle high temperatures and provide stable performance. Common ceramics include alumina (Al₂O₃) and beryllium oxide (BeO). Ceramic substrates are preferred for their durability and reliability in demanding environments.
- Plastic Polymers: Plastic-based substrates, such as those made from epoxy resins, polyimides, or PTFE (Teflon), are widely used in standard electronic applications. These materials offer good electrical insulation, flexibility, and cost-effectiveness. They are suitable for a variety of applications, including consumer electronics and general-purpose PCBs. They are often chosen for their ease of processing and availability.
- Composite Materials: Composites combine multiple materials to achieve specific performance characteristics. For example, composite substrates might include a combination of ceramic and polymer layers to enhance properties like thermal conductivity and mechanical strength. These materials are tailored to meet particular needs in advanced electronic applications.
- Metal Core: In metal-core substrates, such as those used in insulated metal substrates (IMS), a metal core (commonly aluminum or copper) is used as the base material. This configuration provides superior thermal management and is often employed in power electronics and LED applications where heat dissipation is critical. The metal core helps in efficiently spreading heat away from sensitive components.
- Glass Epoxy: Glass epoxy substrates, commonly referred to as FR4, are widely used in standard PCB applications. They consist of woven glass fiber impregnated with epoxy resin. This material provides good electrical insulation, mechanical strength, and is cost-effective. FR4 is a common choice for many electronic devices due to its balance of performance and affordability.
- Polyimide: Polyimide substrates offer high thermal stability, chemical resistance, and electrical insulation. They are used in applications that require flexibility and durability, such as in flexible PCBs and high-temperature environments. Polyimide is known for its ability to withstand extreme conditions while maintaining its insulating properties.
- Silicon: In some advanced applications, silicon can be used as the base material for insulating substrates, particularly in integrated circuits and semiconductor devices. Silicon substrates provide a platform for both electronic functionality and insulation.
Each base material has its own set of properties, including electrical insulation, thermal conductivity, mechanical strength, and flexibility, which influence its suitability for different applications. The choice of base material depends on the specific requirements of the electronic device, including performance, reliability, and cost considerations.
Which Company Makes Insulating Substrate?
Currently, there are many companies manufacturing insulating substrates, such as Dow Chemical, Fujitsu, NEC, Advanced Materials, and our company. These companies have extensive experience in the design and production of insulating substrates, providing high-performance insulation solutions for various electronic devices.
Dow Chemical is renowned for its innovative insulating materials, with ceramic substrates offering excellent electrical insulation and thermal management capabilities. Fujitsu specializes in high-performance plastic substrates, widely used in consumer electronics and communication devices. NEC provides a range of insulating substrates for high-frequency and high-temperature applications, catering to diverse market needs. Advanced Materials is known for its premium composite materials and specialized coating technologies, supporting high-end electronic applications.
Our company also has the capability to produce insulating substrates. Our products use high-performance base materials to ensure excellent performance under various application conditions. The features of our insulating substrates include:
- Superior Electrical Insulation: We use high-quality insulating materials such as ceramics and high-performance plastics to ensure excellent electrical isolation and effectively prevent short circuits and leakage issues.
- Effective Thermal Management: Our advanced materials and technologies ensure that the substrates have good thermal conductivity, effectively dissipating heat and preventing electronic devices from overheating.
- High Precision Processing: We possess modern processing equipment and a skilled technical team, capable of achieving high-precision substrate processing and production, ensuring the quality and performance of each substrate.
- Multi-layer Design Capability: Based on customer requirements, we can design and manufacture multi-layer insulating substrates to meet the needs of complex circuits and high-density components.
- Comprehensive After-Sales Service: We offer comprehensive after-sales services to ensure that customers receive timely technical support and solutions during use.
- Customized Service: We can provide customized insulating substrate design and manufacturing services according to specific customer needs, ensuring that products fully meet application requirements.
Through continuous technological innovation and strict quality control, our insulating substrates have gained wide recognition in the market, widely used in various electronic devices and industrial applications. If you have a need for insulating substrates, please feel free to contact us. We are committed to providing high-quality products and services.
In summary, whether it is material selection, processing technology, or after-sales service, our company is capable of producing high-quality insulating substrates to meet the needs of various applications.
What are the 7 Qualities of Good Customer Service?
Good customer service is essential for building strong relationships with customers and ensuring their satisfaction. Here are seven key qualities of good customer service:
- Responsiveness: Promptness in addressing customer inquiries, concerns, or issues is crucial. Good customer service means responding quickly and efficiently to customer needs, whether through phone, email, or live chat. A quick response time helps build trust and shows that the company values the customer’s time.
- Empathy: Understanding and addressing customers’ feelings and perspectives is important. Empathetic service involves actively listening to customers, acknowledging their concerns, and providing support that demonstrates genuine care. Empathy helps in creating a positive emotional connection with customers.
- Knowledgeable Staff: Providing accurate and relevant information is vital. Customer service representatives should be well-trained and knowledgeable about the products, services, and policies of the company. This enables them to offer reliable solutions and answers to customer queries.
- Patience: Handling customers with patience, especially when they are frustrated or confused, is essential. Good customer service involves staying calm and composed, taking the time to explain solutions, and avoiding any form of impatience or irritation.
- Clear Communication: Effective communication is key to good customer service. This means providing clear, concise, and easily understandable information. Avoiding jargon and ensuring that customers fully understand the solutions or answers provided helps in preventing misunderstandings.
- Personalization: Tailoring service to meet individual customer needs enhances the experience. Personalization involves recognizing customers, understanding their preferences, and offering solutions that are specifically relevant to their situations. This makes customers feel valued and appreciated.
- Follow-Up: Ensuring that customer issues are resolved completely and following up to confirm satisfaction is important. Good customer service includes checking in with customers after a resolution to ensure that their needs have been met and addressing any additional concerns that may arise.
By embodying these qualities, companies can provide exceptional customer service that not only resolves issues effectively but also fosters customer loyalty and satisfaction.
FAQs about Insulating Substrate
What is an insulating substrate?
An insulating substrate is a material used to electrically isolate different conductive elements in electronic devices. It also provides mechanical support and can assist with thermal management.
What materials are commonly used for insulating substrates?
Common materials include ceramics (e.g., alumina), plastics (e.g., epoxy, polyimide), and composites. Each material is chosen based on the specific needs of the application.
Why is thermal management important in insulating substrates?
Thermal management helps dissipate heat generated by electronic components, preventing overheating and ensuring the device operates reliably.
What factors should be considered when selecting an insulating substrate?
Key factors include electrical insulation properties, thermal conductivity, mechanical strength, thickness, and compatibility with manufacturing processes.
How does substrate thickness affect performance?
Substrate thickness can impact electrical performance, signal integrity, and mechanical stability. The right thickness is chosen based on the specific design requirements of the device.
Can insulating substrates be customized?
Yes, insulating substrates can be customized in terms of material, thickness, size, and design to meet specific application needs.