High Frequency Antenna PCB Manufacturer
High Frequency Antenna PCB Manufacturer,High Frequency Antenna PCBs are specialized printed circuit boards designed for efficient signal transmission in wireless communication systems. They feature high-performance materials with low dielectric loss and precise impedance control, crucial for maintaining signal integrity at frequencies typically above 1 GHz. These PCBs support the integration of complex antenna designs, enabling enhanced wireless connectivity in applications such as 5G networks, radar systems, and satellite communications. High Frequency Antenna PCBs are engineered for reliability and durability, with optimized RF performance to minimize signal loss and maximize efficiency. They play a critical role in modern telecommunications by facilitating high-speed data transmission and robust connectivity.
What is a High Frequency Antenna PCB?
A High Frequency Antenna PCB (Printed Circuit Board) refers to a specialized circuit board designed to optimize the performance of antennas operating at high frequencies, typically above 1 GHz. These antennas are crucial in various applications such as telecommunications, radar systems, wireless communication devices, and RFID (Radio Frequency Identification) systems.
The design of a High Frequency Antenna PCB is critical because it directly affects the antenna’s efficiency, bandwidth, and radiation pattern. Key considerations include the substrate material (often specialized high-frequency laminates like Rogers or Taconic), trace width and spacing, via design, and impedance matching techniques. These factors help minimize signal losses, maximize radiation efficiency, and maintain signal integrity at high frequencies.
Moreover, the PCB layout for high frequency antennas often involves precise placement of components and traces to minimize electromagnetic interference (EMI) and ensure stable performance across different environmental conditions. Advanced simulation tools are frequently used to predict and optimize antenna characteristics before fabrication.
In summary, a High Frequency Antenna PCB is a sophisticated circuit board optimized for antennas operating at frequencies where conventional PCB design principles may not suffice. Its design intricacies ensure optimal performance and reliability in demanding high-frequency applications.
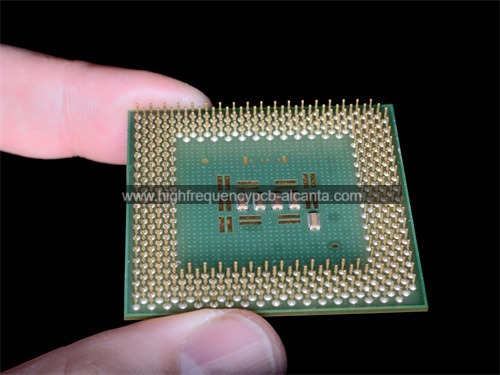
High Frequency Antenna PCB Manufacturer
What are High Frequency Antenna PCB Design Guidelines?
Designing a PCB for high frequency antennas requires careful consideration of several key guidelines to ensure optimal performance. Here are some essential guidelines:
- Substrate Material Selection: Choose a high-frequency laminate material with low dielectric loss tangent (low Dk and Df values) to minimize signal loss and maintain signal integrity at high frequencies. Materials like Rogers, Taconic, or similar specialized laminates are commonly used.
- Trace Width and Spacing: Use wider trace widths to reduce resistance and inductance, which can affect signal loss and impedance matching at high frequencies. Maintain consistent trace widths and controlled impedance throughout the transmission lines to minimize reflections.
- Ground Plane Design: Ensure a solid ground plane beneath the antenna and transmission lines. This helps to minimize electromagnetic interference (EMI), provides shielding, and improves antenna radiation efficiency.
- Via Design: Minimize the number of vias in the signal path to reduce parasitic capacitance and inductance, which can degrade high-frequency signals. Use through-hole vias rather than blind or buried vias whenever possible for better electrical performance.
- Component Placement: Place components strategically to minimize parasitic effects and maintain signal integrity. Keep high-frequency components and transmission lines short and direct to reduce signal loss and interference.
- Antenna Integration: Integrate the antenna design closely with the PCB layout to optimize performance. Ensure proper spacing and isolation between antenna elements and other components to avoid interference.
- Impedance Matching: Use impedance matching techniques (such as tapered traces, matching networks, or series capacitors/inductors) to ensure maximum power transfer between components and transmission lines, improving overall efficiency.
- EMC Considerations: Implement good electromagnetic compatibility (EMC) practices to minimize EMI emissions and susceptibility. This includes proper grounding, shielding, and PCB layout techniques to manage electromagnetic fields effectively.
- Simulation and Prototyping: Use electromagnetic simulation tools (e.g., HFSS, CST Microwave Studio) to model and optimize the antenna PCB design before fabrication. Prototype and test designs to validate performance and ensure they meet specifications.
- Documentation and Standards Compliance: Document the design thoroughly, including material specifications, trace geometries, and layer stack-up details. Ensure compliance with relevant industry standards and guidelines for high-frequency PCB design.
Following these guidelines helps ensure that a high-frequency antenna PCB performs optimally in terms of signal integrity, efficiency, and reliability, meeting the demanding requirements of modern wireless communication and radar systems.
What is the High Frequency Antenna PCB Fabrication Process?
The fabrication process for a High Frequency Antenna PCB involves several specialized steps to ensure the PCB meets the stringent requirements for high-frequency operation. Here’s a structured outline of the fabrication process:
- Material Selection: Choose a high-frequency laminate material such as Rogers, Taconic, or similar. These materials have low dielectric loss tangent (Df) and consistent dielectric constant (Dk) across a range of frequencies.
- Design Preparation: Prepare the PCB design using CAD (Computer-Aided Design) software. Define the layer stack-up, including the number of layers, copper thickness, and material properties. Design the PCB layout considering trace widths, spacing, via types, and component placement optimized for high-frequency performance.
- Pre-production Checks:Conduct pre-production design checks and simulations using electromagnetic simulation tools (e.g., HFSS, CST Microwave Studio) to verify impedance matching, signal integrity, and antenna performance.
- Photolithography: Start with the inner layer processing. Clean and prepare the copper-clad laminate. Apply a photoresist material to the laminate and use UV light to expose the PCB pattern.
- Etching: Develop the PCB by removing the unexposed photoresist and etching away the unwanted copper using an etchant solution. This defines the conductive traces and signal paths according to the PCB design.
- Drilling: Drill holes for vias and component mounting pads using precision CNC drilling machines. Ensure accuracy in hole size and placement to maintain signal integrity and alignment for multilayer PCBs.
- Plating: Plate the drilled holes with conductive material (typically copper) to establish electrical connections between layers. This process involves electroplating copper to ensure continuity and conductivity throughout the PCB.
- Outer Layer Processing: Apply photoresist to the outer layers, expose them to UV light through a photomask to define the outer layer traces and features, and etch away excess copper.
- Surface Finish: Apply a surface finish to protect exposed copper traces and pads from oxidation and facilitate soldering during assembly. Common surface finishes for high-frequency PCBs include ENIG (Electroless Nickel Immersion Gold) or immersion silver.
- Solder Mask Application: Apply solder mask over the PCB surface, leaving openings for component pads and vias. Solder mask helps protect the PCB from environmental factors, prevents solder bridges during assembly, and provides insulation.
- Silkscreen Printing: Optionally, add component designators, logos, and other markings using silkscreen printing. This step helps with component placement during assembly.
- Testing and Inspection: Perform electrical testing, including impedance testing, continuity checks, and possibly high-frequency signal testing using network analyzers or similar equipment. Inspect the PCB for defects, ensuring compliance with design specifications.
- Final Inspection and Packaging: Conduct a final inspection to verify quality and functionality. Cut the PCB panels into individual boards if necessary. Package the finished PCBs appropriately for shipment or further assembly.
Throughout the fabrication process, adherence to design specifications, material handling practices, and quality control measures is critical to producing high-quality High Frequency Antenna PCBs that meet performance requirements for applications such as telecommunications, radar systems, and wireless devices.
How do you manufacture a High Frequency Antenna PCB?
Manufacturing a High Frequency Antenna PCB involves specialized processes tailored to ensure optimal performance at high frequencies. Here’s a detailed outline of the manufacturing process:
- Material Selection:Choose a high-frequency laminate material with low dielectric loss tangent (Df) and consistent dielectric constant (Dk) across frequencies. Popular choices include Rogers, Taconic, or similar specialized materials.
- Design Preparation: Develop the PCB design using CAD software, considering factors like layer stack-up, trace widths, spacing, via types, and component placement optimized for high-frequency performance. Ensure the design meets impedance matching and signal integrity requirements.
- Pre-production Checks: Conduct design verification using electromagnetic simulation tools (e.g., HFSS, CST Microwave Studio) to simulate antenna performance, impedance matching, and signal propagation characteristics.
- Inner Layer Processing:
– Cleaning and Preparation: Clean the copper-clad laminate thoroughly.
– Lamination: Apply a layer of prepreg (pre-impregnated resin) and place the inner layers together.
– Curing: Heat and pressure are applied to cure the prepreg, bonding the layers into a single panel.
- Drilling: Precisely drill holes for vias and component mounting pads using CNC drilling machines. Maintain accuracy in hole size and placement, critical for maintaining signal integrity in high-frequency applications.
- Electroless Copper Deposition: Coat the drilled holes with a thin layer of electroless copper to ensure electrical continuity between layers.
- Copper Plating: Plate the entire panel with additional copper to build up the trace and pad thicknesses as per the design specifications.
- Etching: Apply photoresist to define the circuit pattern on the outer copper layers. Expose the panel to UV light through a photomask, then etch away the unwanted copper using an etchant solution.
- Surface Finish Application: Apply a surface finish to protect exposed copper traces and pads, typically using ENIG (Electroless Nickel Immersion Gold) or immersion silver. This step ensures good solderability and corrosion resistance.
- Solder Mask Application: Apply solder mask over the PCB surface, leaving openings for component pads and vias. Solder mask protects the PCB from environmental factors, prevents solder bridges during assembly, and provides insulation.
- Silkscreen Printing: Optionally, add component designators, logos, and other markings using silkscreen printing. This aids in component placement during assembly.
- Testing and Inspection:
– Electrical Testing: Perform tests such as continuity checks, impedance testing, and potentially high-frequency signal testing using network analyzers.
– Visual Inspection: Inspect the PCB for defects, ensuring compliance with design specifications.
- Final Inspection and Packaging: Conduct a final inspection to verify quality and functionality. Cut the PCB panels into individual boards if necessary. Package the finished PCBs for shipment or further assembly.
Throughout the manufacturing process, strict adherence to design specifications, quality control measures, and handling practices for high-frequency materials is essential to produce High Frequency Antenna PCBs that meet performance requirements for applications such as telecommunications, radar systems, and wireless devices.
How much should a High Frequency Antenna PCB cost?
The cost of a High Frequency Antenna PCB can vary widely depending on several factors:
- Complexity of Design: PCBs with intricate designs, such as those requiring multiple layers, tight trace widths, and specialized materials, tend to cost more due to the complexity of manufacturing.
- Material Choice: High-frequency PCBs often require specialized laminates (e.g., Rogers, Taconic) with low dielectric loss tangent (Df) and consistent dielectric constant (Dk). These materials are more expensive than standard FR4.
- Board Size and Thickness: Larger boards and thicker copper layers increase material costs and manufacturing complexity.
- Surface Finish: Different surface finishes (e.g., ENIG, immersion silver) have varying costs, with finishes like gold plating being more expensive.
- Quantities:Bulk orders generally reduce per-unit costs due to economies of scale. Prototype or small batch orders may have higher costs per unit.
- Lead Time: Expedited manufacturing or quick-turn services typically incur additional costs compared to standard lead times.
As a rough estimate, for a basic single-layer High Frequency Antenna PCB in small quantities (e.g., prototype quantities), you might expect prices starting from around $50 to $100 per board. However, for more complex designs or larger quantities, prices can range from a few hundred to several thousand dollars per board.
It’s important to obtain quotes from PCB manufacturers based on your specific design requirements and quantities. Factors such as design complexity, material specifications, board size, surface finish, and production volume all play significant roles in determining the final cost.
What is High Frequency Antenna PCB base material?
The base material used for High Frequency Antenna PCBs is typically a specialized type of laminate designed to support high-frequency signals with minimal signal loss and interference. Some common materials used include:
- Rogers Corporation Laminates: Rogers materials, such as RO4000 series (e.g., RO4350B, RO4003C), are popular choices. These laminates have low dielectric loss tangent (Df) and stable dielectric constant (Dk) over a wide frequency range, making them suitable for high-frequency applications.
- Taconic Laminates: Taconic materials, like TLY, TLC, or TLX series, are also widely used. They offer similar characteristics to Rogers laminates, providing low loss and high reliability for high-frequency circuits.
- Isola Laminates: Isola offers materials like IS620, IS680, and others designed for high-frequency applications. These laminates provide good electrical performance and thermal stability.
- Arlon Laminates: Arlon materials, such as 85N, 85HP, and others, are known for their high-performance characteristics suitable for RF and microwave circuits.
These materials are selected for their low loss tangent (Df), which minimizes signal attenuation, and their consistent dielectric constant (Dk), which ensures predictable electrical performance across different frequencies. They also typically have good thermal management properties and mechanical stability, important for maintaining performance under varying environmental conditions.
Choosing the right base material is crucial in designing High Frequency Antenna PCBs to ensure optimal signal integrity, minimal losses, and reliable performance in applications such as telecommunications, radar systems, wireless communication devices, and RF/microwave circuits.
Which company makes High Frequency Antenna PCBs?
Many companies are capable of manufacturing High Frequency Antenna PCBs, including specialized PCB manufacturers and suppliers worldwide. For example, companies like Rogers, Taconic, Isola, and others provide PCB substrate materials specifically designed for high-frequency applications, known for their low dielectric loss tangent (Df) and stable dielectric constant (Dk), which are essential for RF (Radio Frequency) and microwave circuit designs.
As for our company, we also have the capability to manufacture High Frequency Antenna PCBs, and we possess the following production capabilities and strengths:
- Professional Design Team: We have an experienced PCB design team capable of designing and optimizing the layout and structure of High Frequency Antenna PCBs according to specific customer requirements and specifications.
- Advanced Manufacturing Equipment: We are equipped with state-of-the-art PCB manufacturing equipment and technology, including high-precision CNC drilling machines, automated chemical processing lines, and surface treatment lines, ensuring the precision and consistency of PCB production.
- High-Quality Substrate Materials: We select and use high-quality PCB substrate materials from renowned brands such as Rogers, Taconic, or Isola, which meet the stringent requirements for electrical performance and stability in high-frequency PCB applications.
- Quality Control and Testing: We strictly adhere to ISO quality management system standards and implement rigorous quality control measures and testing processes to ensure that every High Frequency Antenna PCB produced meets customer design specifications and standards.
- Customized Customer Service: We offer flexible customized services to meet customer-specific application requirements for High Frequency Antenna PCBs, including layout design, material selection, surface treatment, and other personalized services.
In summary, our company has the capability and experience to manufacture High Frequency Antenna PCBs, providing customers with high-quality, reliable PCB solutions for various RF and microwave circuit applications. We are committed to delivering excellent PCB manufacturing and service through advanced technology and a professional team.
What are the qualities of good customer service?
Good customer service encompasses several key qualities that collectively contribute to a positive experience for customers. Here are some essential qualities:
- Responsiveness: Good customer service involves promptly addressing customer inquiries, concerns, and requests. Timely responses demonstrate respect for the customer’s time and urgency.
- Empathy:Showing empathy means understanding and acknowledging the customer’s feelings, concerns, and perspectives. It involves listening actively and demonstrating compassion.
- Clarity and Communication: Effective communication is crucial in customer service. It involves providing clear, concise information and instructions, avoiding jargon, and ensuring the customer understands the message.
- Problem-Solving Skills: Being able to effectively resolve customer issues and complaints is a hallmark of good customer service. This includes understanding the problem, proposing solutions, and following through until the issue is resolved satisfactorily.
- Product Knowledge: Having a deep understanding of the products or services offered allows customer service representatives to provide accurate information, offer recommendations, and address customer questions effectively.
- Professionalism: Maintaining a professional demeanor and attitude at all times, even in challenging situations, contributes to a positive customer experience. This includes remaining calm, polite, and respectful.
- Reliability and Dependability:Customers value consistency and reliability. Providing consistent service quality and fulfilling promises and commitments build trust and confidence.
- Proactive Support: Anticipating customer needs and offering proactive assistance or recommendations demonstrates initiative and a commitment to customer satisfaction.
- Personalization: Tailoring interactions to meet the specific needs and preferences of individual customers enhances their experience. This can include remembering past interactions, preferences, and personalizing recommendations.
- Feedback Handling: Actively seeking and listening to customer feedback, whether positive or negative, and using it constructively to improve products, services, and processes.
Overall, good customer service creates a positive impression, builds customer loyalty, and contributes to the overall success and reputation of a business or organization. It involves continuous improvement and a customer-centric approach in all interactions.
FAQs
Why are High Frequency Antenna PCBs important?
These PCBs are important because they enable efficient transmission and reception of high-frequency signals with minimal losses. They are designed to maintain signal integrity, provide impedance matching, and optimize radiation patterns for antennas.
What materials are used in High Frequency Antenna PCBs?
High Frequency Antenna PCBs use specialized laminate materials with low dielectric loss tangent (Df) and stable dielectric constant (Dk) across a wide frequency range. Common materials include Rogers, Taconic, Isola, and similar high-frequency laminates.
What design considerations are important for High Frequency Antenna PCBs?
Key design considerations include trace width and spacing, via design, impedance matching techniques, ground plane design, and minimizing electromagnetic interference (EMI). These factors are critical to achieving optimal performance at high frequencies.
How do you ensure the performance of High Frequency Antenna PCBs?
Performance is ensured through rigorous design validation using electromagnetic simulation tools to predict and optimize antenna characteristics. Quality manufacturing processes, including precise drilling, plating, and surface finishes, also contribute to performance.
What are the typical applications of High Frequency Antenna PCBs?
These PCBs are used in a wide range of applications such as cellular base stations, satellite communication systems, radar systems, WiFi routers, RFID readers, automotive radar systems, and other wireless communication devices.
What are the challenges in manufacturing High Frequency Antenna PCBs?
Challenges include maintaining tight tolerances for trace dimensions, controlling impedance across layers, minimizing signal losses due to dielectric absorption and conductor losses, and ensuring reliable performance in diverse environmental conditions.
Can High Frequency Antenna PCBs be customized?
Yes, these PCBs can be customized based on specific application requirements. Customization options include material selection, layer stack-up design, trace geometry, surface finishes, and incorporating features for specialized antenna designs.