Glass Package Substrates Manufacturer
Glass Package Substrates Manufacturer,Glass Package Substrates (GPS) are innovative components in semiconductor manufacturing, revolutionizing the packaging of electronic devices. Unlike traditional substrates like silicon or organic materials, GPS utilize glass as their foundation. This advanced technology offers numerous benefits, including exceptional thermal performance, high-density interconnects, and superior electrical properties. Glass substrates facilitate efficient heat dissipation, crucial for maintaining semiconductor chip reliability in high-power applications. With fine-pitch traces and vias, GPS enable compact designs and intricate circuitry, ideal for miniaturized electronic devices. Additionally, GPS provide excellent electrical integrity, minimizing signal loss and enhancing overall device performance. Their hermetic sealing capabilities protect enclosed chips from moisture and contaminants, ensuring long-term reliability. As semiconductor technology advances, Glass Package Substrates continue to play a pivotal role in enabling smaller, faster, and more reliable electronic devices for various industries, including automotive, telecommunications, and consumer electronics.
What is a Glass Package Substrate (GPS)?
A Glass Package Substrate (GPS) is a type of packaging technology used in the semiconductor industry, particularly for advanced integrated circuits (ICs) and microprocessors.
Traditionally, semiconductor chips have been packaged using materials such as ceramic or organic substrates. However, with the increasing demand for high-performance and high-density chips, there’s a need for more advanced packaging solutions.
A Glass Package Substrate utilizes glass as the substrate material instead of traditional materials like ceramic or organic substrates. Glass offers several advantages, including excellent thermal and electrical properties, as well as high dimensional stability. These properties make it suitable for packaging high-performance chips that generate a lot of heat.
GPS technology allows for finer pitch interconnects, which means more connections can be made in a smaller area, enabling higher-density packaging. It also provides better reliability and durability compared to other packaging options.
Overall, Glass Package Substrates are becoming increasingly popular in the semiconductor industry, especially for applications where high performance, reliability, and miniaturization are critical requirements.
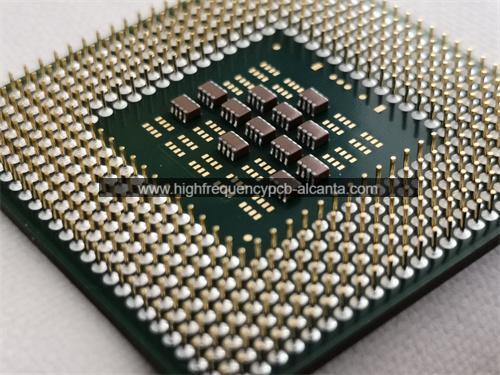
Glass Package Substrates Manufacturer
What are the GPS Design Guidelines?
Design guidelines for Glass Package Substrates (GPS) typically encompass several key aspects to ensure optimal performance and reliability. While specific guidelines may vary depending on the manufacturer and application requirements, some common principles include:
- Thermal Management: Efficient heat dissipation is crucial for maintaining the reliability and performance of semiconductor devices. GPS designs should incorporate features such as thermal vias, heat spreaders, and optimized layout to facilitate heat transfer away from the chip.
- Electrical Performance: High-speed signal integrity and low electrical losses are essential for many applications. Design guidelines focus on minimizing signal distortion, crosstalk, and impedance mismatches through careful routing, signal layer placement, and impedance control techniques.
- Mechanical Integrity: Glass substrates are typically more brittle than traditional packaging materials, so mechanical robustness is critical to withstand mechanical stress during manufacturing, assembly, and operation. Guidelines may include recommendations for substrate thickness, reinforcement structures, and minimizing areas of high mechanical stress concentration.
- Reliability and Durability: Design guidelines aim to enhance the reliability and longevity of GPS-based packages by addressing factors such as moisture ingress, thermal cycling, and mechanical shock. This may involve encapsulation techniques, hermetic sealing, and conformal coatings to protect sensitive components.
- Miniaturization and High-Density Integration: GPS technology enables the realization of compact and high-density package designs. Guidelines focus on optimizing layout, interconnect density, and package footprint to maximize the use of available space while ensuring manufacturability and reliability.
- Manufacturability and Cost: Design guidelines should consider the manufacturability of GPS-based packages, including factors such as process compatibility, yield optimization, and cost-effectiveness. Design choices that simplify manufacturing processes and minimize material waste can help reduce production costs.
- Electromagnetic Compatibility (EMC): Ensuring compatibility with electromagnetic interference (EMI) regulations is crucial for electronic devices. Guidelines may include strategies for minimizing electromagnetic emissions and susceptibility through shielding, grounding, and noise mitigation techniques.
Overall, adherence to these design guidelines helps ensure that GPS-based packages meet performance, reliability, and manufacturability requirements for a wide range of semiconductor applications.
What is the GPS Fabrication Process?
The fabrication process for Glass Package Substrates (GPS) involves several steps to create a robust and high-performance substrate for semiconductor packaging. While specific details may vary depending on the manufacturer and technology used, a typical GPS fabrication process involves the following key stages:
- Substrate Preparation: The process begins with the preparation of glass substrates. High-quality glass sheets are selected and cleaned thoroughly to remove any contaminants or impurities that could affect the subsequent processing steps.
- Substrate Etching:Etching is performed to create features such as vias, trenches, and circuit patterns on the glass substrate. Various techniques such as wet chemical etching, dry etching (plasma etching), or laser ablation may be used depending on the desired pattern complexity and substrate material.
- Metallization: Metallization involves depositing thin metal layers onto the substrate surface to create conductive traces and interconnects. Commonly used metals include copper, aluminum, and gold. Metallization may be achieved through techniques such as physical vapor deposition (PVD) or sputtering.
- Dielectric Deposition: Dielectric materials are deposited onto the substrate to insulate and protect the metallized traces. Silicon dioxide (SiO2), silicon nitride (Si3N4), or various polymer materials may be used as dielectric layers. Techniques such as chemical vapor deposition (CVD) or spin coating are employed for dielectric deposition.
- Laser Ablation: Laser ablation is used to selectively remove dielectric material and expose metal traces at desired locations. This step helps define the final circuit pattern and vias on the substrate.
- Surface Planarization: Surface planarization techniques such as chemical mechanical polishing (CMP) or mechanical lapping are employed to achieve a smooth and flat surface finish. This is crucial for ensuring uniformity and reliability of subsequent processing steps.
- Through-Silicon Via (TSV) Formation (Optional): In some cases, through-silicon vias (TSVs) may be incorporated into GPS structures to enable vertical interconnects between different layers. TSVs are typically created using techniques such as deep reactive ion etching (DRIE) followed by metallization.
- Packaging and Assembly: Once the substrate fabrication is complete, semiconductor chips are attached to the substrate using flip-chip or wire bonding techniques. Additional packaging layers, such as mold compounds or underfills, may be applied to encapsulate the device and provide mechanical protection.
- Testing and Quality Assurance: Comprehensive testing and quality assurance measures are performed to ensure the functionality, reliability, and performance of the finished GPS packages. This may include electrical testing, thermal cycling, and visual inspection to identify any defects or anomalies.
By following these fabrication steps, manufacturers can produce Glass Package Substrates that meet the stringent requirements of modern semiconductor packaging applications, including high performance, reliability, and miniaturization.
How do you manufacture a GPS?
Manufacturing Glass Package Substrates (GPS) involves a series of intricate processes that demand precision and expertise. Here’s a step-by-step guide to manufacturing a GPS:
- Substrate Selection: High-quality glass substrates are chosen based on specific requirements such as size, thickness, and thermal properties. These substrates are typically made of materials like borosilicate glass or quartz.
- Cleaning and Preparation: The selected glass substrates undergo thorough cleaning to remove any contaminants or particles that could affect the manufacturing process or the quality of the final product. This step is critical to ensure proper adhesion and patterning.
- Patterning: A thin layer of photoresist is applied uniformly onto the glass substrate. The substrate is then exposed to ultraviolet (UV) light through a photomask, which defines the desired circuit patterns and features. After exposure, the photoresist is developed, selectively removing the exposed areas and leaving behind the patterned resist.
- Metallization: Metal deposition is performed to create conductive traces, pads, and vias on the substrate. Common metals used for metallization include copper, aluminum, and gold. The metal is deposited onto the substrate using techniques such as physical vapor deposition (PVD) or chemical vapor deposition (CVD). The patterned photoresist acts as a mask, allowing the metal to be deposited only in the desired areas.
- Etching: Any remaining photoresist is removed, leaving behind the metal traces and features on the glass substrate. Chemical etching may also be employed to further define the geometry of the metal features and remove any excess material.
- Die Attachment and Wire Bonding: Semiconductor chips (die) are attached to the substrate using die attach materials such as adhesives or solder. Wire bonding is then performed to connect the bond pads on the semiconductor chips to the corresponding pads on the substrate using thin metal wires (typically gold or aluminum). Alternatively, flip-chip bonding may be used, where the semiconductor chips are directly bonded to the substrate without the need for wire bonding.
- Encapsulation and Sealing: The assembled package may be encapsulated with a protective material such as epoxy resin to provide mechanical support and environmental protection. Additionally, hermetic sealing may be performed to ensure airtightness and prevent moisture ingress. This can be achieved through techniques like glass frit sealing or solder sealing.
- Testing and Inspection: The completed GPS packages undergo rigorous testing and inspection to verify their electrical functionality, thermal performance, mechanical integrity, and reliability. This may include electrical continuity tests, thermal cycling tests, visual inspection, and other quality control measures.
- Trimming and Singulation: After testing, the GPS panels or arrays are trimmed and singulated into individual packages or modules. This may involve cutting the substrate using laser dicing or mechanical sawing techniques to separate the individual devices.
- Packaging and Final Inspection: The singulated GPS packages are then packaged into trays, tubes, or reels for shipment to customers. Final inspection is performed to ensure that the packaged devices meet the specified requirements and standards before they are shipped out.
Throughout the manufacturing process, strict quality control measures are implemented to ensure the consistency, reliability, and performance of the GPS packages. Advanced manufacturing equipment and techniques are employed to achieve precise geometries and high yields.
How much should a GPS cost?
The cost of a Glass Package Substrate (GPS) can vary widely depending on several factors including:
- Size and Complexity: Larger substrates with more intricate circuitry and features will generally cost more to manufacture than smaller, simpler substrates.
- Material Quality: The quality and type of glass substrate used can affect the cost. Higher quality glass materials may command a higher price.
- Manufacturing Process: The complexity and sophistication of the manufacturing processes involved in producing the GPS will impact its cost. Advanced processes such as fine-line lithography, hermetic sealing, and high-density interconnects may increase manufacturing costs.
- Volume: Economies of scale apply in manufacturing. Larger production volumes typically result in lower per-unit costs due to efficiencies gained in materials procurement, equipment utilization, and labor.
- Customization:Customized features, specifications, or special requirements may increase the cost of the GPS due to additional engineering, testing, and production setup.
- Supplier and Location: Different manufacturers and suppliers may offer GPS solutions at different price points based on their capabilities, expertise, and geographic location.
- Market Demand: Market demand and competition can also influence pricing. In a competitive market with multiple suppliers, prices may be more competitive compared to markets with limited options.
Without specific details about the size, complexity, volume, and other factors influencing the production of a GPS, it’s challenging to provide a precise cost estimate. However, GPS packages are typically a critical component in semiconductor devices and electronic systems, and their cost is often factored into the overall cost of the end product.
What is GPS base material?
The base material of a Glass Package Substrate (GPS) is typically a type of glass. Different types of glass may be used depending on the specific requirements of the application, but some common materials include:
- Borosilicate Glass: Borosilicate glass is a type of glass containing silica and boron trioxide as the main glass-forming constituents. It is known for its low coefficient of thermal expansion, high thermal shock resistance, and excellent chemical durability. These properties make borosilicate glass well-suited for applications requiring high reliability and stability over a wide temperature range.
- Quartz Glass (Fused Silica): Quartz glass, also known as fused silica, is a high-purity form of glass consisting almost entirely of silicon dioxide (SiO2). It exhibits exceptional optical transparency, thermal stability, and resistance to chemical corrosion. Quartz glass is often used in applications requiring high precision, such as optical components, semiconductor manufacturing, and high-temperature environments.
- Aluminosilicate Glass: Aluminosilicate glass is a type of glass containing aluminum oxide (alumina) and silica as the main components. It offers a balance of mechanical strength, thermal performance, and chemical resistance. Aluminosilicate glass is commonly used in electronics packaging applications where a combination of properties such as durability, thermal management, and hermetic sealing is required.
These are just a few examples of the types of glass materials that can be used as the base material for GPS. The choice of base material depends on factors such as thermal performance, mechanical strength, electrical properties, and cost considerations, among others. Different glass compositions and formulations may be selected to meet the specific requirements of the application and optimize the performance of the GPS package.
Which company makes GPS?
There are many companies worldwide that manufacture GPS (Global Positioning System) devices. Some of these companies specialize in the development of navigation devices and technologies, while others focus on producing GPS chips, modules, receivers, and other components. Some well-known GPS device manufacturers include Garmin, Trimble Navigation, TomTom in the United States, as well as Huawei and ZTE in China. These companies play significant roles in advancing navigation and positioning technologies through continuous innovation and development.
As an emerging technology company, our company is dedicated to the research, design, and production of GPS technology. We have a passionate and innovative team committed to developing high-performance, reliable GPS solutions to meet the demand for precise positioning and navigation.
Our company possesses advanced research and development facilities and manufacturing processes, utilizing the latest technologies and methods to design and manufacture GPS devices. Our products cover various application areas, including automotive navigation, aerospace, military applications, logistics, and transportation. Whether it’s individual consumers, enterprise customers, or government agencies, we can provide customized solutions to meet their specific positioning and navigation needs.
Customer-centricity is at the core of our company, and we are committed to providing excellent customer service and support. Our team works closely with customers from needs analysis to product delivery, ensuring they receive satisfactory solutions and a high-quality service experience. Our goal is to become a trusted partner for our customers, collaboratively driving the development of GPS technology and achieving mutual success.
Through our efforts and innovations, we believe we can achieve greater success in the field of GPS technology and deliver more value and better services to our customers.
What are the 7 qualities of good customer service?
Good customer service is essential for building strong relationships with customers and fostering loyalty. Seven qualities that contribute to excellent customer service include:
- Responsiveness: Customers appreciate prompt responses to their inquiries, concerns, or issues. Being available and attentive to customer needs shows that you value their time and are committed to addressing their concerns promptly.
- Empathy: Empathizing with customers by understanding their perspective, feelings, and needs helps to build rapport and trust. Showing empathy demonstrates that you care about their experience and are willing to listen and understand their concerns.
- Clear Communication: Effective communication is key to ensuring that customers understand the information provided and the actions being taken to resolve their inquiries or concerns. Using clear and concise language, active listening, and providing relevant information helps to avoid misunderstandings and confusion.
- Knowledgeability: Customers expect service representatives to have the knowledge and expertise needed to address their questions or issues effectively. Being well-informed about products, services, policies, and procedures allows service representatives to provide accurate information and assistance.
- Professionalism: Maintaining a professional demeanor, regardless of the situation, instills confidence in customers and reflects positively on the company. This includes being courteous, respectful, and maintaining a positive attitude, even in challenging or stressful circumstances.
- Problem-Solving Skills: Demonstrating effective problem-solving skills enables service representatives to identify and resolve issues efficiently. Being proactive, resourceful, and adaptable in finding solutions demonstrates a commitment to customer satisfaction and can turn a negative experience into a positive one.
- Consistency: Consistency in the quality of service provided across different interactions and channels helps to build trust and reliability. Customers should receive the same level of attention, support, and assistance regardless of how they choose to engage with the company.
By embodying these qualities, organizations can deliver exceptional customer service experiences that leave a lasting impression and foster customer loyalty and advocacy.
FAQs
How accurate is GPS?
The accuracy of GPS depends on several factors, including the number of satellites in view, signal interference, and the quality of the GPS receiver. Generally, GPS can provide position accuracy within a few meters under optimal conditions.
What devices use GPS?
GPS technology is used in various devices, including smartphones, tablets, navigation systems in vehicles, aviation and marine navigation systems, fitness trackers, and outdoor recreation devices.
Can GPS work indoors?
GPS signals can have difficulty penetrating buildings and other structures, making it challenging for GPS receivers to work reliably indoors. However, some specialized indoor positioning systems use alternative methods such as Wi-Fi or Bluetooth to provide indoor location services.
Is GPS free to use?
Yes, GPS is freely accessible to anyone with a GPS receiver. The US government operates and maintains the GPS satellite constellation, and there are no subscription fees or charges for accessing GPS signals.
Can GPS be jammed or spoofed?
Yes, GPS signals can be intentionally disrupted or manipulated by jamming or spoofing techniques. This can interfere with the operation of GPS receivers and affect their accuracy. However, there are efforts to develop technologies to mitigate the impact of GPS jamming and spoofing.
How many satellites are in the GPS constellation?
The GPS constellation consists of a minimum of 24 operational satellites orbiting the Earth, plus several additional satellites as backups. These satellites are arranged in multiple orbits to provide global coverage.
Can GPS be used for tracking?
Yes, GPS is commonly used for tracking purposes, including vehicle tracking, asset tracking, wildlife tracking, and personal tracking applications. GPS-enabled devices can transmit their location data to a central system for monitoring and analysis.