24G Radar PCB Manufacturer
24G Radar PCB Manufacturer,24G radar PCBs are printed circuit boards specifically designed for 24 gigahertz frequency radar systems. These PCBs possess high-frequency signal processing capabilities and are made using high-quality materials to ensure stable and precise signal transmission. Design considerations include high-frequency signal integrity, RF component layout, and antenna design to achieve optimal performance. The manufacturing process involves meticulous material selection, specialized processes, and rigorous quality control to ensure each PCB meets design specifications and industry standards.
What is a 24G Radar PCB?
A 24G radar PCB refers to a printed circuit board (PCB) designed for use in a 24 GHz radar system. Radar systems at this frequency range are commonly used in automotive applications for features like collision avoidance, adaptive cruise control, and parking assistance. The “24G” indicates the frequency band, which is 24 gigahertz.
These PCBs are specialized to accommodate the specific requirements of radar systems, including high-frequency signal processing, impedance matching, and compact design to fit within the constraints of the radar module. They typically incorporate materials with high dielectric constants and low signal loss to ensure efficient transmission and reception of radar signals.
Moreover, these PCBs may include components such as antennas, amplifiers, mixers, and signal processing circuits tailored for radar applications. Design considerations also include factors like signal integrity, electromagnetic interference (EMI) mitigation, and thermal management to ensure reliable performance under various operating conditions.
Expanding upon your question, if you’re interested in the specifics of designing, manufacturing, or troubleshooting such PCBs, feel free to ask!
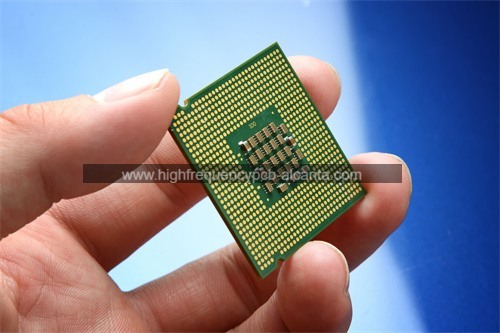
24G Radar PCB Manufacturer
What are the 24G Radar PCB Design Guidelines?
Designing a PCB for a 24 GHz radar system involves adhering to specific guidelines to ensure optimal performance. Here are some key design considerations:
- High-Frequency Signal Integrity: Maintain controlled impedance traces to minimize signal loss and reflections. This involves using high-quality materials with low dielectric constant and loss tangent. The PCB layout should minimize trace lengths and avoid sharp bends or corners that can cause signal degradation.
- RF Component Placement:Place RF components such as antennas, amplifiers, and mixers strategically on the PCB to minimize signal path lengths and reduce interference. Keep sensitive components away from noise sources like digital circuits to prevent cross-talk and EMI.
- Antenna Design: Design the antenna layout carefully to achieve the desired radiation pattern and gain. This may involve using phased array or patch antennas, which require precise placement and alignment. Antenna size and shape should also consider space constraints and desired beam characteristics.
- Power Distribution: Ensure stable power distribution across the PCB to prevent voltage drops and fluctuations that can affect RF performance. Use bypass capacitors and power planes to minimize noise and provide clean power to sensitive components.
- EMI Mitigation: Implement techniques to minimize electromagnetic interference (EMI), such as using shielding, ground planes, and proper grounding techniques. Shielding cans or RF enclosures may be necessary to contain emissions and prevent interference with other electronics.
- Thermal Management:Heat dissipation is crucial, especially for active components like amplifiers and mixers. Ensure adequate thermal vias, heatsinks, or other cooling mechanisms to maintain component temperatures within acceptable limits.
- Testing and Validation: Perform thorough testing and validation of the PCB design to verify its performance under real-world conditions. This may involve RF testing, antenna pattern measurements, and simulations using specialized software tools.
- Compliance: Ensure compliance with regulatory standards and requirements for RF emissions and safety. This includes FCC regulations in the United States and similar standards in other regions.
By following these guidelines, designers can create PCBs that meet the stringent requirements of 24 GHz radar systems, enabling reliable and accurate operation in automotive and other applications.
What is the 24G Radar PCB Fabrication Process?
The fabrication process for a 24 GHz radar PCB involves several steps to create a high-quality board capable of meeting the performance requirements of radar systems. Here’s an overview of the typical process:
- Design Preparation: The process starts with the PCB design created using specialized electronic design automation (EDA) software. The design includes the layout of components, traces, vias, and other features according to the specific requirements of the radar system.
- Material Selection: Choose the appropriate PCB substrate material based on factors such as dielectric constant, loss tangent, and thermal conductivity. Common materials for high-frequency applications include Rogers PCB materials or PTFE-based substrates, known for their excellent RF properties.
- Manufacturing Documentation: Generate manufacturing files, including Gerber files, drill files, and assembly drawings, which provide instructions to the PCB fabrication facility on how to produce the board accurately.
- Substrate Preparation: Begin with a clean substrate panel, typically made of fiberglass-reinforced epoxy laminate. The panel may undergo surface treatment processes such as cleaning, etching, and surface roughening to promote adhesion of the copper foil.
- Copper Cladding: Apply a thin layer of copper foil to both sides of the substrate panel using a lamination process. This copper foil forms the conductive layers of the PCB, and its thickness is carefully controlled to achieve the desired impedance and signal integrity.
- Photoresist Application:Coat the copper-clad substrate with a layer of photoresist material. This photoresist layer is sensitive to UV light and will be used to transfer the PCB design onto the copper surface.
- Exposure and Development: Use a photomask or film to expose the photoresist layer to UV light, selectively hardening or softening areas based on the PCB design. Then, develop the exposed areas to remove the unexposed photoresist, leaving behind the pattern of traces and pads.
- Etching:Submerge the panel in an etchant solution, such as ferric chloride or ammonium persulfate, to dissolve the unprotected copper and create the copper traces and pads. The remaining photoresist acts as a mask to protect the desired copper features.
- Drilling:Use precision drilling machines equipped with high-speed carbide drills to create holes (vias) for interconnecting different layers of the PCB. Laser drilling may be used for microvias in high-density designs.
- Plating:Plate the drilled vias with a thin layer of copper to electrically connect the conductive layers of the PCB. This process may involve electroplating or chemical deposition to ensure reliable electrical connections.
- Surface Finish: Apply a surface finish to protect the exposed copper traces and pads from oxidation and improve solderability. Common surface finishes include HASL (Hot Air Solder Leveling), ENIG (Electroless Nickel Immersion Gold), and OSP (Organic Solderability Preservatives).
- Quality Control: Conduct various quality control checks throughout the fabrication process, including dimensional verification, electrical testing, and visual inspection, to ensure the PCB meets the design specifications and quality standards.
- Routing and Separation: After fabrication, the panel is routed to separate individual PCBs, following the outlines defined in the design. Automated routing machines or CNC milling equipment may be used for this process.
- Final Inspection: Perform a final inspection to verify the integrity of the fabricated PCBs, checking for any defects or discrepancies. This may include electrical testing, dimensional measurements, and visual inspection under magnification.
- Packaging and Shipping: Once approved, the fabricated PCBs are packaged securely and shipped to the customer or assembly facility for component placement and soldering.
By following these steps, manufacturers can produce high-quality 24 GHz radar PCBs that meet the stringent performance and reliability requirements of radar systems in automotive and other applications.
How do you manufacture a 24G Radar PCB?
Manufacturing a 24 GHz radar PCB involves a series of steps to transform the design into a physical circuit board capable of meeting the performance requirements of radar systems. Here’s a step-by-step guide to the manufacturing process:
- Design Preparation: Begin with a detailed PCB design created using specialized software. This design includes the layout of components, traces, vias, and other features necessary for the radar system’s operation.
- 2. Material Selection: Choose the appropriate PCB substrate material based on the requirements of the radar system. High-frequency PCB materials like Rogers or PTFE-based substrates are commonly used for their excellent RF properties.
- Fabrication Documentation: Generate manufacturing files such as Gerber files, drill files, and assembly drawings, which provide instructions to the PCB fabrication facility on how to produce the board accurately.
- Panel Preparation:Start with a clean substrate panel made of fiberglass-reinforced epoxy laminate. The panel may undergo surface treatment processes like cleaning and roughening to ensure proper adhesion of the copper foil.
- Copper Cladding: Apply a thin layer of copper foil to both sides of the substrate panel using a lamination process. This copper foil forms the conductive layers of the PCB and is carefully controlled for thickness to achieve the desired impedance and signal integrity.
- Photoresist Application: Coat the copper-clad substrate with a layer of photoresist material. This photoresist layer is sensitive to UV light and will be used to transfer the PCB design onto the copper surface.
- Exposure and Development: Use a photomask or film to expose the photoresist layer to UV light, selectively hardening or softening areas based on the PCB design. Then, develop the exposed areas to remove the unexposed photoresist, leaving behind the pattern of traces and pads.
- Etching: Submerge the panel in an etchant solution, such as ferric chloride or ammonium persulfate, to dissolve the unprotected copper and create the copper traces and pads. The remaining photoresist acts as a mask to protect the desired copper features.
- Drilling: Use precision drilling machines equipped with high-speed carbide drills to create holes (vias) for interconnecting different layers of the PCB. Laser drilling may be used for microvias in high-density designs.
- Plating:Plate the drilled vias with a thin layer of copper to electrically connect the conductive layers of the PCB. This process may involve electroplating or chemical deposition to ensure reliable electrical connections.
- Surface Finish: Apply a surface finish to protect the exposed copper traces and pads from oxidation and improve solderability. Common surface finishes include HASL (Hot Air Solder Leveling), ENIG (Electroless Nickel Immersion Gold), and OSP (Organic Solderability Preservatives).
- Quality Control: Conduct various quality control checks throughout the fabrication process, including dimensional verification, electrical testing, and visual inspection, to ensure the PCB meets the design specifications and quality standards.
- Routing and Separation: After fabrication, the panel is routed to separate individual PCBs, following the outlines defined in the design. Automated routing machines or CNC milling equipment may be used for this process.
- Final Inspection: Perform a final inspection to verify the integrity of the fabricated PCBs, checking for any defects or discrepancies. This may include electrical testing, dimensional measurements, and visual inspection under magnification.
- Packaging and Shipping: Once approved, the fabricated PCBs are packaged securely and shipped to the customer or assembly facility for component placement and soldering.
By following these steps with precision and attention to detail, manufacturers can produce high-quality 24 GHz radar PCBs capable of meeting the stringent performance and reliability requirements of radar systems.
How much should a 24G Radar PCB cost?
The cost of a 24 GHz radar PCB can vary significantly depending on several factors, including the complexity of the design, the quality of materials used, the manufacturing processes involved, and the quantity ordered. Here are some factors that can influence the cost:
- Complexity of Design: PCBs with complex layouts, high-density components, and multiple layers will generally cost more to manufacture due to increased material and labor requirements.
- Materials: The choice of materials, such as high-frequency substrates and specialized laminates, can impact the cost. High-quality materials designed for RF applications typically cost more than standard PCB materials.
- Manufacturing Processes: Certain manufacturing processes, such as laser drilling for microvias or impedance-controlled trace routing, may add to the overall cost of production due to their specialized nature.
- Production Volume: Economies of scale often apply in PCB manufacturing, meaning that larger production volumes typically result in lower per-unit costs. Ordering larger quantities of PCBs can reduce the cost per board.
- Additional Services: Services such as surface finishing, panelization, and testing may incur additional costs but are essential for ensuring the quality and reliability of the PCB.
- Supplier and Location: PCB fabrication costs can also vary depending on the chosen supplier and their location. Different regions may have different labor costs, overhead expenses, and supply chain factors that influence pricing.
As a rough estimate, the cost of a 24 GHz radar PCB can range from tens to hundreds of dollars per board, with prices decreasing for higher production volumes. It’s essential to work closely with a reputable PCB manufacturer to obtain accurate quotes based on your specific requirements and volume needs. Additionally, consider factors like lead time, quality assurance, and customer support when selecting a PCB supplier.
What is the 24G Radar PCB base material?
The base material for a 24 GHz radar PCB is typically chosen to meet the stringent requirements of high-frequency RF (Radio Frequency) applications. Commonly used materials for such applications include:
- Rogers PCB Materials: Rogers Corporation produces a range of high-frequency laminates specifically designed for RF and microwave applications. These materials have low dielectric loss, low moisture absorption, and stable electrical properties over a wide frequency range. Examples include Rogers RO4000 series and RO3000 series laminates.
- PTFE-Based Substrates: Polytetrafluoroethylene (PTFE) or Teflon-based substrates are known for their excellent electrical properties, including low dielectric constant and low loss tangent. These materials are suitable for high-frequency applications due to their stability and performance characteristics.
- Aramid-Based Materials: Aramid-based materials, such as DuPont’s Pyralux® APR, offer good mechanical strength and thermal stability, making them suitable for high-frequency PCBs that require flexibility or thin constructions.
- Ceramic-Based Substrates: Ceramic materials like alumina (Al2O3) or aluminum nitride (AlN) offer high thermal conductivity and excellent electrical properties, making them suitable for high-power RF applications where heat dissipation is critical.
- Hybrid Substrates: Some PCB materials combine multiple substrates, such as PTFE and woven fiberglass, to achieve a balance of performance and cost-effectiveness.
When selecting a base material for a 24 GHz radar PCB, considerations include dielectric constant, loss tangent, thermal properties, mechanical strength, cost, and manufacturability. The chosen material should provide the required electrical performance while also meeting the mechanical and thermal requirements of the specific radar system application. It’s essential to consult with PCB designers and material suppliers to select the most suitable base material for your project.
Which company manufactures 24G Radar PCBs?
Many companies can manufacture 24G radar PCBs, including large PCB manufacturers, specialized RF (Radio Frequency) PCB suppliers, and custom circuit board manufacturers. Some well-known PCB manufacturers and suppliers such as Advanced Circuits, Sanmina, Rogers Corporation, Isola Group, etc., have the capability to produce high-performance 24G radar PCBs. These companies have advanced manufacturing equipment, extensive experience, and professional technical teams to meet various customer needs.
Our company is also a professional PCB manufacturer with rich experience and technical strength to provide high-quality 24G radar PCBs. We have advanced production equipment and processes to meet customers’ requirements for PCB quality, performance, and delivery time. Our production team undergoes professional training and strictly follows quality control procedures to ensure that each PCB meets design requirements and industry standards.
Our services also include technical support, design optimization suggestions, and customized solutions. We can provide different types of substrates, processes, and surface treatments according to customers’ specific requirements to ensure that PCBs achieve the best performance and reliability in 24GHz radar systems.
From design to production to delivery, we are committed to providing first-class service and products to customers. Our goal is to establish long-term partnerships with customers to promote technological innovation and development together. If you have any requirements or questions about 24G radar PCBs, please feel free to contact us, and we will be happy to assist you.
What are the qualities of good customer service?
Good customer service involves various qualities and practices that aim to meet or exceed customers’ needs and expectations. Here are some essential qualities of good customer service:
- Empathy: Good customer service representatives empathize with customers by understanding their concerns, frustrations, and needs. They listen actively and show genuine care and concern for resolving issues.
- Communication Skills: Effective communication is crucial in customer service. Representatives should be clear, articulate, and responsive in their interactions with customers, whether it’s through verbal communication, written messages, or body language.
- Patience: Dealing with customers, especially those who are upset or frustrated, requires patience. Good customer service professionals remain calm and composed, even in challenging situations, and take the time needed to address customers’ concerns thoroughly.
- Product Knowledge: A good understanding of the products or services being offered is essential for providing helpful assistance and guidance to customers. Customer service representatives should be knowledgeable about the features, benefits, and usage of the products to answer questions accurately and provide valuable recommendations.
- Problem-Solving Skills: Good customer service involves identifying and resolving issues effectively and efficiently. Representatives should be resourceful and proactive in finding solutions to customers’ problems, even if it requires escalating the issue to higher levels of management.
- Adaptability:Every customer interaction is unique, and situations can vary greatly. Good customer service professionals are adaptable and flexible in their approach, tailoring their responses and actions to suit each customer’s individual needs and preferences.
- Professionalism: Maintaining professionalism in all interactions is important for building trust and credibility with customers. This includes being courteous, respectful, and maintaining confidentiality when handling sensitive information.
- Follow-Up: Following up with customers after resolving an issue or completing a transaction demonstrates care and commitment to their satisfaction. Good customer service includes checking in to ensure that customers’ needs have been met and addressing any additional concerns that may arise.
- Positive Attitude: A positive attitude can make a significant difference in customer interactions. Good customer service representatives approach each interaction with enthusiasm, optimism, and a willingness to help, creating a positive experience for customers.
- Continuous Improvement:Good customer service is not static; it evolves and improves over time. Organizations committed to providing excellent customer service encourage feedback from customers and employees, identify areas for improvement, and implement changes to enhance the overall customer experience.
By embodying these qualities and practices, organizations can build strong relationships with customers, foster loyalty, and differentiate themselves from competitors in the marketplace.
FAQs
What are the key features of 24G radar PCBs?
Key features of 24G radar PCBs include high-frequency signal processing capabilities, impedance matching for efficient signal transmission, compact design to fit within radar modules, and integration of specialized components like antennas, amplifiers, and mixers.
What materials are commonly used in 24G radar PCBs?
Common materials used in 24G radar PCBs include high-frequency substrates like Rogers laminates or PTFE-based materials, known for their excellent RF properties. These materials offer low dielectric loss, stable electrical characteristics, and good thermal performance, essential for high-frequency applications.
What design considerations are important for 24G radar PCBs?
Design considerations for 24G radar PCBs include high-frequency signal integrity, RF component placement to minimize signal path lengths and interference, antenna design for desired radiation patterns, power distribution for stable operation, EMI mitigation, thermal management, and compliance with regulatory standards.
How are 24G radar PCBs manufactured?
The manufacturing process for 24G radar PCBs involves steps such as design preparation, material selection, substrate preparation, copper cladding, photoresist application, exposure and development, etching, drilling, plating, surface finish application, quality control, routing and separation, final inspection, and packaging.
What factors affect the cost of 24G radar PCBs?
The cost of 24G radar PCBs can vary based on factors such as the complexity of the design, choice of materials, manufacturing processes involved, production volume, additional services required, and the supplier’s location and capabilities.
Where can I find a manufacturer for 24G radar PCBs?
Several PCB manufacturers, including specialized RF PCB suppliers, offer services for producing 24G radar PCBs. It’s essential to choose a reputable manufacturer with experience in high-frequency PCBs and the capability to meet your specific requirements.