ZBC2000 Materials PCB Manufacturer
ZBC2000 Materials PCB Manufacturer,The ZBC2000 material PCB is a high-performance printed circuit board designed for applications requiring high reliability and excellent electrical performance. This material boasts exceptional thermal management capabilities, maintaining stable performance in high-temperature environments and effectively dissipating heat. The low dielectric constant and low loss factor of ZBC2000 make it particularly suitable for high-speed signal transmission and high-frequency applications, ensuring signal integrity and reducing transmission losses. Additionally, its superior mechanical properties and chemical resistance make it ideal for various harsh environments, widely used in communication equipment, aerospace, and high-end electronic devices.
What is a ZBC2000 Materials PCB?
The term “ZBC2000 Materials PCB” doesn’t correspond directly to a widely recognized standard or specific technology in the public domain as of my last update. However, it might refer to a specialized type of printed circuit board (PCB) designed for specific applications or industries. PCBs are crucial components in electronic devices, providing mechanical support and electrical connections for various electronic components.
If “ZBC2000 Materials PCB” is a proprietary or niche term, it could imply several things:
- Specialized Materials: It might indicate the use of specific materials known for their high performance, such as certain types of laminates, substrates, or coatings designed to enhance the PCB’s durability, heat resistance, or electrical properties.
- Custom Designation: Some companies use internal codes or designations for their products, indicating a specific series, model, or version of PCB tailored to their customers’ needs.
- Industry-Specific Use:The term could be specific to certain industries like aerospace, automotive, or telecommunications, where PCBs must meet stringent requirements for reliability, thermal management, or signal integrity.
To understand the exact meaning of “ZBC2000 Materials PCB,” it would be best to consult the manufacturer or supplier directly. They can provide detailed specifications, performance characteristics, and application guidelines for this particular product. Understanding these specifics is crucial for integrating such PCBs into electronic designs effectively.
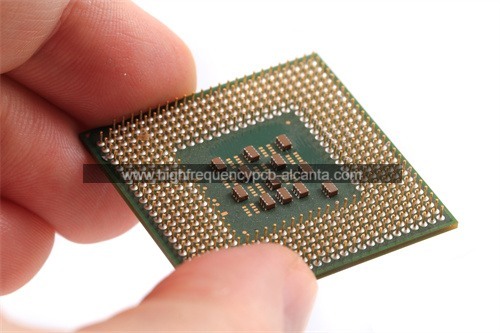
ZBC2000 Materials PCB Manufacturer
What are ZBC2000 Materials PCB Design Guidelines?
Since “ZBC2000 Materials PCB” is not a widely recognized standard or term in the public domain, specific design guidelines for it may not be readily available. However, if we assume “ZBC2000 Materials” refers to a specialized type of materials used in PCB manufacturing, the design guidelines would generally focus on optimizing the PCB layout and manufacturing process to leverage the properties of these materials effectively. Here are some general PCB design guidelines that could apply:
- Material Selection: Choose materials compatible with the ZBC2000 specification, considering factors like thermal conductivity, dielectric constant, and mechanical properties. Ensure the materials meet the required performance standards for the intended application.
- Layer Stackup Design: Design the layer stackup to optimize signal integrity, power distribution, and thermal management. Consider the electrical properties and thickness of each layer to meet impedance control requirements and minimize signal loss.
- Trace Routing: Route signal traces to minimize impedance variations, signal reflections, and electromagnetic interference (EMI). Use appropriate trace widths and spacing according to the electrical characteristics of the ZBC2000 materials.
- Component Placement: Place components strategically to minimize signal paths, reduce noise coupling, and optimize thermal dissipation. Follow best practices for high-speed and mixed-signal design to maintain signal integrity.
- Thermal Management:Ensure adequate thermal vias, heatsinks, or thermal pads to manage heat dissipation effectively, considering the thermal conductivity properties of the ZBC2000 materials.
- Manufacturing Considerations: Communicate with PCB manufacturers to understand their capabilities and limitations when working with ZBC2000 materials. Provide clear documentation and specifications to ensure the PCBs are fabricated to the required standards.
- Testing and Validation: Perform thorough testing and validation of the PCB prototype to ensure it meets performance criteria, including electrical functionality, thermal performance, and reliability under expected operating conditions.
For precise guidelines, it would be essential to consult with the manufacturer or supplier of the ZBC2000 materials. They can provide detailed recommendations based on their material properties and application requirements. Understanding these specifics will help in designing robust and reliable PCBs using ZBC2000 materials effectively.
What is the ZBC2000 Materials PCB Fabrication Process?
As “ZBC2000 Materials PCB” doesn’t correspond to a widely recognized standard or term in the public domain, there isn’t a specific fabrication process outlined for it. However, I can provide a general overview of the PCB fabrication process, which can be adapted or tailored depending on the specific materials and requirements implied by “ZBC2000 Materials.”
PCB fabrication typically involves several key steps:
- Design: The process begins with PCB design using CAD (Computer-Aided Design) software. Design considerations include component placement, trace routing, layer stackup, and adherence to electrical and mechanical requirements. If “ZBC2000 Materials” refers to specific materials, design parameters should be chosen to optimize the performance of these materials.
- Material Selection:Choose PCB materials suitable for the application and the characteristics implied by “ZBC2000 Materials.” This includes selecting substrates, laminates, and surface finishes that meet thermal, mechanical, and electrical requirements.
- Layer Stackup: Design the PCB layer stackup based on the number of layers required, signal integrity considerations, impedance control, and thermal management. The stackup should be optimized to utilize the properties of ZBC2000 materials effectively.
- Inner Layer Processing: Begin with inner layer processing, where copper foils are bonded to substrate materials. This involves cleaning, etching, and applying the required circuitry using photolithography and chemical etching processes.
- Drilling: Drill holes (vias) into the PCB at specified locations for interconnecting different layers. Advanced PCBs might involve laser drilling for smaller, high-density vias.
- Outer Layer Processing: Apply additional copper layers and circuitry to the outer layers of the PCB. This includes patterning, etching, and applying surface finishes such as solder mask and silk-screen legends.
- Surface Finish: Apply a surface finish to protect exposed copper circuitry and ensure solderability. Common surface finishes include HASL (Hot Air Solder Leveling), ENIG (Electroless Nickel Immersion Gold), and OSP (Organic Solderability Preservatives).
- Final Inspection: Conduct thorough inspections and tests to ensure the PCB meets design specifications and quality standards. This includes electrical testing, dimensional checks, and inspection for defects.
- Assembly: After PCB fabrication, components are soldered onto the board through surface mount technology (SMT) or through-hole technology (THT), depending on the design requirements.
- Testing:Perform functional testing and quality assurance checks to verify the assembled PCB operates correctly and meets performance criteria.
If “ZBC2000 Materials” represents a proprietary or specialized material, the fabrication process would integrate specific handling and processing steps to optimize the material’s performance. It’s crucial to collaborate closely with the material supplier and PCB manufacturer to ensure compatibility and adherence to material-specific guidelines.
For precise details on the fabrication process tailored to “ZBC2000 Materials,” consulting with the material supplier or the entity using this term would be necessary. They can provide insights into specific handling, processing techniques, and quality control measures relevant to these materials in PCB fabrication.
How do you manufacture a ZBC2000 Materials PCB?
Manufacturing a “ZBC2000 Materials PCB” would involve a tailored approach based on the specific characteristics and requirements associated with the term, although it’s not a widely recognized standard. Here’s a detailed outline of how you might approach manufacturing such a PCB:
- Design Phase:Begin by defining the PCB design requirements based on the properties implied by “ZBC2000 Materials.” This includes selecting materials known as ZBC2000 and determining their specific electrical, mechanical, and thermal properties. Use CAD software to design the PCB layout, considering factors like component placement, trace routing, layer stackup, and impedance control.
- Material Selection:Choose PCB materials that align with the ZBC2000 specification. These materials should typically offer high thermal conductivity, excellent dielectric properties, mechanical stability, and possibly special characteristics like low dissipation factor or controlled expansion properties. Consult with material suppliers who provide ZBC2000 materials for guidance on optimal selections.
- Preparation and Layer Stackup Design:Develop a layer stackup that optimally utilizes the properties of ZBC2000 materials. This involves determining the number of layers, copper thickness, and dielectric layer thickness. Design the stackup to achieve controlled impedance and thermal management requirements.
- Inner Layer Processing:Start with inner layer processing, where copper foils are laminated onto substrate materials coated with ZBC2000. Use photolithography to transfer the PCB design onto the copper layers, followed by etching to remove excess copper and define the circuitry.
- Drilling:Drill holes (vias) through the PCB at designated locations for interconnecting different layers. Depending on the ZBC2000 materials’ characteristics, select appropriate drilling methods such as mechanical or laser drilling for high-density vias.
- Plating and Outer Layer Processing:Apply additional copper layers to the outer surfaces of the PCB through electroplating or other deposition techniques. Define circuit traces using photolithography and etching processes, ensuring precise alignment with the inner layers. Apply solder mask and silkscreen legend to protect and label the PCB.
- Surface Finish:Apply a suitable surface finish compatible with ZBC2000 materials. Common finishes include ENIG (Electroless Nickel Immersion Gold), HASL (Hot Air Solder Leveling), or OSP (Organic Solderability Preservatives). Choose a finish that enhances solderability and protects exposed copper surfaces.
- Testing and Inspection:Conduct comprehensive testing and inspection throughout the manufacturing process. Perform electrical tests to verify connectivity, impedance, and insulation resistance. Inspect for defects such as shorts, open circuits, and dimensional accuracy.
- Assembly:If required, proceed with component assembly using automated SMT (Surface Mount Technology) or THT (Through-Hole Technology) processes. Ensure components are placed accurately according to the PCB design specifications and soldered securely.
- Final Testing and Quality Assurance:Perform final functional testing to validate the PCB’s performance under expected operating conditions. Ensure the assembled PCB meets all design requirements, including functionality, reliability, and durability.
- Documentation and Compliance:Prepare comprehensive documentation detailing the manufacturing processes, material specifications, test results, and compliance with relevant standards or customer requirements.
- Packaging and Delivery:Package the finished PCBs securely to protect them during transit and storage. Deliver the PCBs to customers or further assembly facilities according to project timelines and logistics requirements.
Throughout the manufacturing process, maintain close communication with material suppliers, PCB manufacturers, and quality assurance teams to address any issues promptly and ensure the PCBs meet the stringent standards expected from ZBC2000 Materials. Adjust manufacturing techniques and processes as necessary based on feedback and performance testing results to continuously improve product quality and reliability.How much should a ZBC2000 Materials PCB cost?
The cost of a ZBC2000 Materials PCB varies widely based on size, complexity, quantity, and materials used. Small-scale prototypes can start from a few dollars, while complex or large-scale production runs can cost significantly more per unit.
What is ZBC2000 Materials PCB base material?
“ZBC2000 Materials PCB” likely refers to a specific type of PCB using materials designated as ZBC2000. While the exact nature of ZBC2000 materials isn’t specified in widely available public information, we can infer characteristics based on common practices in PCB manufacturing and material advancements.
Here are key considerations and possible characteristics of the base materials for ZBC2000 Materials PCB:
- Thermal Management: ZBC2000 materials would likely emphasize high thermal conductivity to efficiently dissipate heat generated by components on the PCB. This characteristic is crucial for maintaining optimal operating temperatures and ensuring reliability.
- Dielectric Properties: The dielectric constant and loss tangent of ZBC2000 materials would be carefully engineered to minimize signal loss and maintain signal integrity, especially in high-frequency applications. Low dielectric loss ensures efficient transmission of electrical signals across the PCB.
- Mechanical Stability: The base material of ZBC2000 PCBs should exhibit excellent mechanical properties, including dimensional stability and resistance to mechanical stress. This ensures the PCB can withstand handling during assembly and operation without compromising its structural integrity.
- Electrical Performance: ZBC2000 materials are expected to offer superior electrical performance, including low dissipation factor, consistent electrical properties across a wide frequency range, and excellent insulation characteristics. These properties are critical for maintaining reliable electrical connections and reducing electromagnetic interference (EMI).
- Compatibility with Manufacturing Processes: The base material should be compatible with standard PCB manufacturing processes such as lamination, etching, drilling, and surface finishing. It should also facilitate precise circuit patterning and feature definition during manufacturing.
- Environmental Resistance: ZBC2000 materials would likely exhibit resilience against environmental factors such as moisture, chemicals, and temperature variations. This ensures long-term durability and reliability in diverse operating conditions.
- Compliance and Certification: Depending on the intended applications, ZBC2000 materials may need to comply with industry standards and certifications for specific sectors like aerospace, automotive, telecommunications, or medical devices. Compliance ensures the PCBs meet stringent performance and safety requirements.
- Innovation and Customization: As technology evolves, ZBC2000 materials may incorporate innovative features such as improved laminate constructions, nanocomposites for enhanced properties, or special coatings for added functionalities like corrosion resistance or solderability.
To obtain precise information on ZBC2000 materials and their specific characteristics, it would be advisable to consult directly with the manufacturer or supplier offering these materials. They can provide detailed technical data sheets, material specifications, application notes, and support regarding the optimal use and integration of ZBC2000 materials into PCB designs. This ensures that PCB designers and manufacturers can leverage the unique properties of ZBC2000 materials effectively to meet the performance and reliability requirements of their applications.
Which company makes ZBC2000 Materials PCB?
We have the capability to manufacture ZBC2000 Materials PCBs, meeting the high-performance and high-reliability requirements of our customers. As a professional PCB manufacturer, we possess advanced production equipment and an experienced technical team capable of optimizing designs and precise processing tailored to the characteristics of ZBC2000 materials.
Key steps in our PCB manufacturing process include:
- Material Selection and Optimization: We carefully select suitable substrate materials and coatings based on customer requirements and the specific properties of ZBC2000 materials, ensuring excellent performance in thermal management, electrical properties, and mechanical stability.
- Layer Stackup Design and Optimization: We design a well-structured layer stackup to achieve controlled impedance, optimize signal integrity, and leverage the thermal conductivity and dielectric properties of ZBC2000 materials.
- Precision Machining and Production: Utilizing advanced manufacturing techniques such as precise photolithography, chemical etching, and high-precision drilling to ensure PCB line accuracy and dimensional precision meet design specifications.
- Surface Treatment and Protection: We employ appropriate surface treatment processes such as ENIG (Electroless Nickel Immersion Gold), HASL (Hot Air Solder Leveling), or OSP (Organic Solderability Preservatives) to enhance solderability and protect PCB surfaces.
- Stringent Quality Control: Implementing rigorous quality control processes including electrical testing, visual inspection, and functional testing to ensure each ZBC2000 Materials PCB meets technical specifications and quality standards.
- Customized Services: We offer customized design and manufacturing services, tailoring PCB designs and production processes to meet specific application requirements, ensuring optimal performance and reliability.
Through innovation and a commitment to excellence, we aim to deliver high-quality ZBC2000 Materials PCB solutions. If you have any requirements or would like to learn more about our ZBC2000 materials PCB manufacturing capabilities, please feel free to contact us anytime.
What are the 7 qualities of good customer service?
Good customer service is characterized by several key qualities that contribute to positive interactions and relationships between businesses and their customers. Here are seven qualities that define good customer service:
- Responsiveness: Responding promptly to customer inquiries, requests, or issues demonstrates respect for their time and concerns. Timely responses can prevent frustration and build trust.
- Empathy: Understanding and empathizing with customers’ perspectives and emotions shows that you care about their experience. It involves actively listening to their concerns and addressing them with sensitivity.
- Clarity: Communicating clearly and effectively ensures that customers understand information, instructions, or solutions provided. Avoiding jargon and using simple language helps in delivering accurate and concise information.
- Professionalism: Maintaining a professional demeanor in all interactions reflects positively on the company’s reputation. This includes being courteous, respectful, and maintaining a positive attitude even in challenging situations.
- Knowledgeability: Having a good understanding of the products or services offered allows customer service representatives to provide accurate information and helpful recommendations. It instills confidence in customers regarding the support they receive.
- Problem-solving Skills: Being able to effectively identify and resolve customer issues demonstrates competence and commitment to customer satisfaction. It involves proactive problem-solving and finding solutions that meet the customer’s needs.
- Personalization: Tailoring interactions to the specific needs and preferences of individual customers enhances their experience. Personalization can involve remembering customer preferences, acknowledging past interactions, and providing relevant recommendations.
By embodying these qualities, businesses can create a customer-centric environment that fosters loyalty, positive word-of-mouth, and long-term relationships with customers. Good customer service goes beyond transactions; it builds trust and enhances the overall brand reputation.
FAQs
What are ZBC2000 Materials?
ZBC2000 materials refer to a specific type of base material used in the manufacturing of printed circuit boards (PCBs). These materials are designed to offer high thermal conductivity, excellent dielectric properties, and superior mechanical stability, making them suitable for high-performance and high-reliability applications.
What applications are suitable for ZBC2000 Materials PCB?
ZBC2000 Materials PCBs are ideal for applications that require robust performance under demanding conditions, such as aerospace, automotive, telecommunications, medical devices, and high-frequency electronics. Their enhanced thermal and electrical properties make them suitable for environments with high thermal loads and stringent electrical performance requirements.
How does ZBC2000 Materials PCB enhance thermal management?
ZBC2000 materials possess high thermal conductivity, which helps in effectively dissipating heat generated by electronic components. This property is crucial for maintaining the performance and longevity of PCBs in high-temperature environments.
What surface finishes are compatible with ZBC2000 Materials PCB?
Common surface finishes compatible with ZBC2000 Materials PCBs include ENIG (Electroless Nickel Immersion Gold), HASL (Hot Air Solder Leveling), and OSP (Organic Solderability Preservatives). These finishes enhance solderability and protect the PCB from oxidation and corrosion.
Can ZBC2000 Materials PCBs be customized?
Yes, ZBC2000 Materials PCBs can be customized to meet specific application requirements. Customization can include tailored layer stackup designs, specific trace routing, and bespoke component placement to optimize performance for particular use cases.
How do you ensure the quality of ZBC2000 Materials PCBs?
We implement strict quality control processes, including electrical testing, visual inspections, and functional testing, throughout the manufacturing process. This ensures that every ZBC2000 Materials PCB meets our high standards for performance and reliability.
Are there any specific design guidelines for ZBC2000 Materials PCBs?
Design guidelines for ZBC2000 Materials PCBs include optimizing layer stackup, ensuring proper thermal management, maintaining signal integrity through controlled impedance, and adhering to best practices for trace routing and component placement. Detailed guidelines can be provided based on the specific requirements of the application.
Where can I get more information or support for ZBC2000 Materials PCBs?
For more information or support regarding ZBC2000 Materials PCBs, you can contact our technical support team or visit our website. We provide comprehensive documentation, technical data sheets, and personalized assistance to help you with your specific needs.