Wire Bonding BGA substrates Manufacturer
Wire Bonding BGA Substrates Manufacturer,Wire Bonding BGA Substrates are crucial components in modern semiconductor packaging, facilitating the connection between the silicon die and the package. These substrates employ wire bonding technology, where thin wires made of materials like gold or aluminum are used to create electrical connections between the semiconductor die and the substrate’s bonding pads.
These substrates offer several advantages, including high electrical performance, reliability, and flexibility in design. They are compatible with fine pitch connections, making them suitable for high-density integrated circuits. The fabrication process involves precise patterning, etching, and bonding techniques to ensure optimal performance.
With their ability to handle high-frequency signals and power distribution efficiently, Wire Bonding BGA Substrates find applications in a wide range of industries, including consumer electronics, telecommunications, automotive, and aerospace. Their cost-effectiveness and reliability make them a popular choice for semiconductor packaging solutions.
Overall, Wire Bonding BGA Substrates play a critical role in enabling the functionality and performance of integrated circuits, contributing to the advancement of technology in various fields.
What is a Wire Bonding BGA substrate?
A Wire Bonding BGA (Ball Grid Array) substrate refers to a type of integrated circuit packaging technology where wire bonding is used to connect the silicon die to the substrate of a BGA package.
In this context:
- BGA: It’s a type of surface-mount packaging used for integrated circuits. The BGA package has an array of solder balls on its underside, which connect it to the printed circuit board (PCB) or substrate.
- Wire Bonding: This is a method used in semiconductor manufacturing to make electrical connections between the silicon die of a semiconductor device and the package or substrate it’s mounted on. In wire bonding, thin wires (usually made of gold or aluminum) are connected from pads on the die to corresponding pads on the package or substrate.
- Substrate:In this context, the substrate is the material upon which the semiconductor die is mounted, and it provides electrical connections between the die and the package. It’s usually made of a material like ceramic or laminate.
So, a Wire Bonding BGA substrate is a BGA package where the electrical connections between the silicon die and the package substrate are made using wire bonding technology. This approach is often used in situations where fine pitch connections or other factors make it more suitable than other bonding methods like flip-chip bonding.
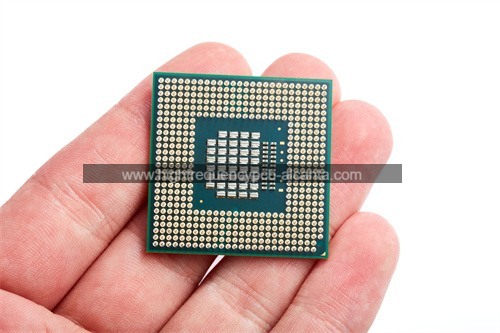
Wire Bonding BGA Substrates Manufacturer
What are the Wire Bonding BGA substrate Design Guidelines?
Design guidelines for Wire Bonding BGA substrates aim to ensure the reliability and performance of the integrated circuit package. Here are some common guidelines:
- Pad Layout: The layout of pads on the substrate should adhere to the specifications provided by the semiconductor manufacturer. These specifications typically include pad dimensions, pitch, and spacing to ensure proper alignment and bonding.
- Wire Routing: Design the substrate layout to allow efficient routing of bonding wires between the die and the substrate pads. Minimize wire lengths and avoid sharp bends to prevent wire damage during bonding and operation.
- Signal Integrity: Maintain signal integrity by minimizing the length and impedance of signal traces on the substrate. Signal traces should be routed away from high-speed clock signals, power lines, and other noise sources to minimize interference.
- Power and Ground Distribution: Ensure adequate power and ground distribution on the substrate to minimize voltage drops and ground bounce. Use multiple vias or power planes to distribute power and ground evenly across the substrate.
- Thermal Management:Design the substrate layout to facilitate efficient heat dissipation from the die to the PCB. Place thermal vias or copper pads under the die to enhance thermal conductivity and dissipate heat effectively.
- Package Size and Thickness: Consider the overall size and thickness of the package when designing the substrate. Optimize the package dimensions to meet the requirements of the application while ensuring mechanical stability and compatibility with assembly processes.
- Materials Selection: Choose substrate materials that offer good electrical performance, thermal conductivity, and mechanical strength. Common substrate materials include ceramic and laminate substrates, each with its advantages and limitations.
- Alignment and Registration:Ensure accurate alignment and registration between the die, substrate pads, and bonding wires to prevent misalignment or shorts during wire bonding.
- Reliability Testing: Perform reliability testing, such as thermal cycling, mechanical shock, and vibration testing, to validate the design and ensure the long-term reliability of the Wire Bonding BGA package.
- Documentation and Standards Compliance: Document the design specifications and ensure compliance with industry standards and specifications, such as JEDEC standards, to facilitate manufacturing and assembly processes.
These guidelines help ensure the successful design and manufacturing of Wire Bonding BGA substrates that meet the performance, reliability, and manufacturability requirements of the intended application.
What is the Wire Bonding BGA substrate Fabrication Process?
The fabrication process for a Wire Bonding BGA (Ball Grid Array) substrate involves several steps to manufacture the substrate that will host the integrated circuit die and provide the electrical connections between the die and the package. Here’s a general overview of the fabrication process:
- Substrate Preparation: The process begins with the preparation of the substrate material, which is typically a ceramic or laminate material. This involves cutting the substrate material to the desired size and shape, as well as cleaning and preparing the surface for subsequent processing.
- Layer Deposition: Depending on the substrate design, multiple layers of conductive and insulating materials may be deposited onto the substrate surface. This can include thin film deposition techniques such as sputtering, evaporation, or chemical vapor deposition (CVD).
- Patterning: Photolithography or other patterning techniques are used to define the patterns of conductive traces, vias, and bonding pads on the substrate surface. A photoresist material is applied to the substrate, exposed to light through a mask, and then developed to selectively remove material, leaving behind the desired patterns.
- Etching: After patterning, etching processes are used to remove unwanted material from the substrate surface. Wet etching or dry etching techniques may be employed to selectively remove the exposed material while preserving the patterned features.
- Surface Finish: The substrate surface is prepared with a suitable finish to facilitate wire bonding and ensure good electrical contact. This may involve applying a thin layer of metal such as gold or aluminum to the bonding pads and vias.
- Die Attachment: Once the substrate is prepared, the semiconductor die is attached to the substrate surface using adhesive materials or soldering techniques. The die is aligned and placed onto the substrate, and then bonded in place using heat and pressure.
- Wire Bonding: Wire bonding machines are used to connect the bond pads on the semiconductor die to the corresponding bond pads on the substrate. Thin wires made of gold or aluminum are bonded using heat, pressure, and ultrasonic energy to create electrical connections.
- Encapsulation: After wire bonding, the substrate and die assembly may be encapsulated with a protective material such as epoxy resin or molding compound. Encapsulation helps protect the die and wire bonds from mechanical damage, moisture, and contaminants.
- Testing and Inspection:The fabricated Wire Bonding BGA substrates undergo rigorous testing and inspection to ensure they meet the required electrical and mechanical specifications. This may include electrical testing, visual inspection, and reliability testing under various environmental conditions.
- Final Packaging: Once the substrates pass testing and inspection, they are ready for final packaging. This typically involves attaching the substrate to a BGA package, which includes the soldering of solder balls to the substrate underside for surface mounting onto a printed circuit board (PCB).
By following these fabrication steps, manufacturers can produce Wire Bonding BGA substrates with the necessary electrical connectivity, reliability, and performance for a wide range of semiconductor applications.
How do you manufacture a Wire Bonding BGA substrate?
Manufacturing a Wire Bonding BGA (Ball Grid Array) substrate involves several detailed steps. Here’s a comprehensive overview of the process:
- Design Preparation: The process starts with the design of the substrate layout. This involves determining the arrangement of bonding pads, signal traces, vias, and other features on the substrate based on the specifications of the integrated circuit and the desired performance characteristics.
- Substrate Material Selection: Choose the appropriate substrate material based on factors such as electrical performance, thermal conductivity, mechanical strength, and cost. Common substrate materials include ceramic (alumina or aluminum nitride) and laminate (FR-4 or polyimide).
- Substrate Fabrication:
- Substrate Preparation: Cut the substrate material to the required size and shape. Clean the substrate surface to remove contaminants and ensure proper adhesion of subsequent layers.
- Layer Deposition: Deposit thin films of conductive and insulating materials onto the substrate surface using techniques such as sputtering, evaporation, or chemical vapor deposition (CVD). These layers form the basis for the substrate’s conductive traces and insulating layers.
- Patterning: Use photolithography or other patterning techniques to define the patterns of conductive traces, vias, bonding pads, and other features on the substrate surface. Apply photoresist, expose it to light through a mask, and then develop it to selectively remove material, leaving behind the desired patterns.
- Etching: Use wet or dry etching processes to remove unwanted material from the substrate surface, leaving behind the patterned features defined in the previous step.
- Surface Finish: Apply a suitable surface finish to the substrate to facilitate wire bonding and ensure good electrical contact. This may involve depositing a thin layer of metal such as gold or aluminum onto the bonding pads and vias.
- Die Attachment: Attach the semiconductor die to the substrate surface using adhesive materials or soldering techniques. The die is aligned and placed onto the substrate, then bonded in place using heat and pressure.
- Wire Bonding: Use wire bonding machines to connect the bond pads on the semiconductor die to the corresponding bond pads on the substrate. Thin wires made of gold or aluminum are bonded using heat, pressure, and ultrasonic energy to create electrical connections.
- Encapsulation: After wire bonding, encapsulate the substrate and die assembly with a protective material such as epoxy resin or molding compound. Encapsulation helps protect the die and wire bonds from mechanical damage, moisture, and contaminants.
- Testing and Inspection: Perform rigorous testing and inspection on the fabricated Wire Bonding BGA substrates to ensure they meet the required electrical and mechanical specifications. This may include electrical testing, visual inspection, and reliability testing under various environmental conditions.
- Final Packaging: Attach the substrate to a BGA package by soldering solder balls to the substrate underside for surface mounting onto a printed circuit board (PCB).
By following these steps carefully, manufacturers can produce Wire Bonding BGA substrates with the necessary electrical connectivity, reliability, and performance for a wide range of semiconductor applications.
How much should a Wire Bonding BGA substrate cost?
The cost of a Wire Bonding BGA (Ball Grid Array) substrate can vary significantly depending on several factors, including:
- Substrate Material: The choice of substrate material, such as ceramic or laminate, can have a significant impact on cost. Ceramic substrates tend to be more expensive due to their higher material and manufacturing costs compared to laminate substrates.
- Complexity of Design: The complexity of the substrate design, including the number of layers, the density of features (such as bonding pads, vias, and traces), and the precision required for alignment and patterning, can influence the manufacturing cost.
- Manufacturing Volume: Economies of scale typically apply in manufacturing, so larger production volumes generally result in lower per-unit costs. Smaller production runs may incur higher costs due to setup and tooling expenses.
- Quality and Reliability Requirements: Meeting stringent quality and reliability standards may require additional testing, inspection, and quality control measures, which can add to the overall cost.
- Additional Processes: Additional processes such as surface finishing, die attachment, wire bonding, encapsulation, and final packaging contribute to the overall cost of manufacturing Wire Bonding BGA substrates.
- Supplier and Location: The choice of supplier and manufacturing location can also affect costs. Suppliers with advanced technology and capabilities may charge higher prices, while offshore manufacturing may offer cost savings but could incur additional logistics expenses.
Without specific details about the substrate’s design requirements, manufacturing volume, quality standards, and other factors, it’s challenging to provide an exact cost estimate. However, Wire Bonding BGA substrates typically range in cost from a few dollars to tens or even hundreds of dollars per unit, depending on the factors mentioned above.
What is Wire Bonding BGA substrate base material?
The base material for a Wire Bonding BGA (Ball Grid Array) substrate can vary depending on the specific requirements of the application, but commonly used materials include:
- Ceramic Substrates: Ceramic materials such as alumina (Al2O3) or aluminum nitride (AlN) are frequently used for high-performance applications that require excellent thermal conductivity, electrical insulation, and mechanical strength. Ceramic substrates offer superior thermal dissipation properties compared to other materials, making them suitable for applications with high-power components or operating in harsh environments.
- Laminate Substrates: Laminate materials, such as fiberglass-reinforced epoxy (FR-4) or polyimide, are commonly used for cost-effective solutions in applications where thermal performance and mechanical strength requirements are less stringent. Laminate substrates offer good electrical insulation and can be manufactured with fine pitch traces and vias suitable for high-density applications.
The choice between ceramic and laminate substrates depends on factors such as thermal management requirements, electrical performance, mechanical stability, cost considerations, and the specific demands of the application. Each material has its advantages and limitations, so the selection should be based on a thorough assessment of these factors.
Which company makes Wire Bonding BGA substrates?
There are many companies that manufacture Wire Bonding BGA (Ball Grid Array) substrates, including Amkor Technology, STATS ChipPAC, ASE Group, Powertech Technology Inc. (PTI), Chipbond Technology Corporation, JCET Group (Jiangsu Changjiang Electronics Technology), and others. These companies have rich experience and technology in semiconductor packaging and advanced manufacturing fields, providing various types and specifications of BGA substrates to meet the needs of different industries and applications.
As for our company, if we have the appropriate equipment and technology, we can also produce Wire Bonding BGA substrates. Firstly, we need advanced semiconductor manufacturing equipment, including equipment for substrate processing, metal thin film deposition, photolithography, etching, and other processes. Secondly, we need a team of experienced engineers who can design and optimize the layout, routing, layer stacking, and other aspects of BGA substrates to ensure they meet customer requirements and standards. Additionally, we need to establish a strict quality control system to ensure that the produced BGA substrates have good electrical performance, thermal performance, and reliability.
When producing Wire Bonding BGA substrates, we also need to consider market demand and competition. We can flexibly adjust production capacity and process flow according to customer needs to provide customized solutions. Furthermore, we can continuously improve technology and processes to reduce production costs, enhance product quality and performance, and strengthen our competitiveness in the market.
In summary, while producing Wire Bonding BGA substrates requires certain technology and equipment, as long as we have the appropriate resources and capabilities, our company can also participate and provide customers with high-quality products and services.
What are the 7 qualities of good customer service?
Good customer service is essential for building strong relationships with customers and fostering loyalty. Here are seven qualities that characterize excellent customer service:
- Responsiveness: A good customer service team responds promptly to customer inquiries, concerns, and feedback. This includes acknowledging messages and requests in a timely manner and providing timely resolutions to issues.
- Empathy: Empathy involves understanding and relating to the customer’s feelings, concerns, and perspectives. Good customer service representatives listen actively, demonstrate empathy, and strive to put themselves in the customer’s shoes to provide personalized assistance.
- Clarity: Effective communication is key to providing good customer service. Customer service representatives should communicate clearly and concisely, avoiding technical jargon and ensuring that customers understand the information provided.
- Knowledgeability: Good customer service requires having a deep understanding of the products or services offered, as well as the company’s policies, procedures, and processes. Customer service representatives should be knowledgeable and well-trained to address customer inquiries and resolve issues effectively.
- Professionalism: Professionalism encompasses maintaining a positive and courteous demeanor, even in challenging situations. Customer service representatives should conduct themselves professionally, treat customers with respect, and uphold the company’s values and standards.
- Proactivity: Anticipating customer needs and taking proactive measures to address them demonstrates a commitment to excellent customer service. Proactive customer service involves offering assistance, providing relevant information, and resolving issues before they escalate.
- Follow-up: Following up with customers after resolving an issue or completing a transaction shows that you value their feedback and satisfaction. Good customer service representatives follow up with customers to ensure that their needs have been met and to address any remaining concerns.
By embodying these qualities, companies can deliver exceptional customer service experiences that build trust, loyalty, and long-term relationships with their customers.
FAQs
What is a Wire Bonding BGA substrate?
A Wire Bonding BGA substrate is a type of integrated circuit packaging technology where wire bonding is used to connect the silicon die to the substrate of a BGA package. It provides the electrical connections between the semiconductor die and the package.
What are the advantages of Wire Bonding BGA substrates?
Wire Bonding BGA substrates offer several advantages, including high electrical performance, flexibility in design, compatibility with fine pitch connections, and cost-effectiveness compared to other bonding methods.
What materials are used to make Wire Bonding BGA substrates?
The base materials for Wire Bonding BGA substrates include ceramic materials such as alumina or aluminum nitride, as well as laminate materials such as fiberglass-reinforced epoxy (FR-4) or polyimide.
What is the fabrication process for Wire Bonding BGA substrates?
The fabrication process involves steps such as substrate preparation, layer deposition, patterning, etching, die attachment, wire bonding, encapsulation, testing, and final packaging. Each step is essential for producing high-quality Wire Bonding BGA substrates.
What are the design guidelines for Wire Bonding BGA substrates?
Design guidelines include considerations such as pad layout, wire routing, signal integrity, power and ground distribution, thermal management, package size and thickness, materials selection, alignment and registration, reliability testing, and compliance with industry standards.
What is the cost of Wire Bonding BGA substrates?
The cost of Wire Bonding BGA substrates varies depending on factors such as substrate material, complexity of design, manufacturing volume, quality and reliability requirements, additional processes, supplier, and location. Costs typically range from a few dollars to tens or hundreds of dollars per unit.
Which companies manufacture Wire Bonding BGA substrates?
Companies that manufacture Wire Bonding BGA substrates include Amkor Technology, STATS ChipPAC, ASE Group, Powertech Technology Inc. (PTI), Chipbond Technology Corporation, JCET Group, and others. These companies have expertise in semiconductor packaging and advanced manufacturing.