370HR Materials PCB Manufacturer
370HR Materials PCB Manufacturer,The 370HR Materials PCB is a high-performance printed circuit board (PCB) made with 370HR base material. This base material is composed of an epoxy resin system reinforced with woven glass fabric, offering excellent thermal stability, mechanical strength, and electrical insulation properties. Widely utilized in industries demanding exceptional reliability and performance, such as aerospace, automotive, telecommunications, and medical devices, the 370HR Materials PCB maintains stability even in high-temperature environments and exhibits remarkable resilience against mechanical stress and harsh operating conditions. Its outstanding electrical insulation ensures reliable signal transmission. Thus, the 370HR Materials PCB stands as an ideal choice for electronic applications requiring high reliability and superior performance.
What is a 370HR Materials PCB?
A 370HR materials PCB refers to a type of printed circuit board (PCB) constructed using 370HR laminate material. This material is known for its high-performance characteristics, particularly in demanding electronic applications.
370HR laminate is a type of epoxy resin system reinforced with woven glass fabric. It offers excellent thermal stability, high mechanical strength, and good electrical insulation properties. These attributes make it suitable for use in high-temperature environments and applications where reliability and durability are paramount.
PCBs made from 370HR materials are commonly used in industries such as aerospace, automotive, telecommunications, and medical devices, where they can withstand harsh operating conditions and provide consistent performance over time. The “370HR” designation typically indicates the grade or specification of the laminate material, ensuring uniformity and reliability in manufacturing processes.
In summary, 370HR materials PCBs offer a combination of high temperature resistance, mechanical strength, and electrical insulation, making them ideal for critical electronic applications where reliability is crucial.
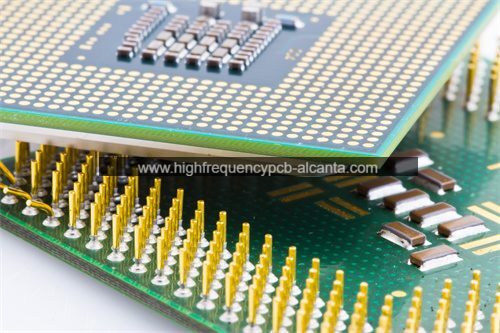
370HR Materials PCB Manufacturer
What are the 370HR Materials PCB Design Guidelines?
Designing a PCB using 370HR materials requires careful consideration of various factors to ensure optimal performance and reliability. Here are some general guidelines:
- Thermal Management: 370HR materials have good thermal stability, but it’s still essential to consider heat dissipation. Place components that generate heat strategically on the board, and ensure proper airflow within the enclosure. Additionally, consider adding thermal vias to conduct heat away from critical components.
- Signal Integrity: Maintain controlled impedance for high-speed signals to minimize reflections and signal degradation. Follow best practices for routing high-speed traces, such as minimizing trace length, avoiding sharp corners, and maintaining consistent trace widths.
- Mechanical Strength: 370HR laminate provides good mechanical strength, but it’s essential to avoid placing heavy components or connectors near the board edges, as this could lead to mechanical stress during handling or assembly.
- Electromagnetic Compatibility (EMC): Design the PCB layout to minimize electromagnetic interference (EMI) by keeping sensitive traces away from noise sources and ensuring proper grounding. Use ground planes and shielding techniques where necessary to reduce EMI.
- Layer Stackup: Design an appropriate layer stackup considering factors such as signal integrity, power distribution, and manufacturing constraints. Consult with your PCB manufacturer for recommendations on the optimal layer configuration for your specific application.
- Component Placement: Place components strategically to minimize signal path lengths, reduce crosstalk, and optimize thermal performance. Follow industry-standard practices for component placement, such as grouping related components and keeping high-speed traces short and direct.
- Design for Manufacturability (DFM): Consider manufacturability during the design phase by adhering to the manufacturer’s DFM guidelines. Ensure that your design complies with the manufacturer’s capabilities regarding minimum trace widths, minimum annular ring sizes, and other manufacturing constraints.
- Environmental Considerations: If your PCB will be exposed to harsh environments, such as high humidity or corrosive chemicals, select components and materials with appropriate environmental ratings. Consider conformal coating or encapsulation to protect the board from moisture and contaminants.
- Testing and Validation: Implement a comprehensive testing and validation process to verify the functionality and reliability of the PCB design. Perform signal integrity analysis, thermal analysis, and EMC testing to ensure that the design meets performance requirements.
By following these guidelines and collaborating closely with your PCB manufacturer, you can design a high-quality PCB using 370HR materials that meets your performance, reliability, and manufacturability requirements.
What is the 370HR Materials PCB Fabrication Process?
The fabrication process for a PCB using 370HR materials is similar to that of other PCBs but requires specific considerations to accommodate the characteristics of the laminate material. Here’s a general overview of the fabrication process:
- Preparation of Design Files: The process begins with the preparation of design files using PCB design software. These files contain information about the layout, traces, components, and other features of the PCB.
- Material Selection: Choose the appropriate grade of 370HR laminate material based on the specific requirements of the application. Ensure that the material meets the necessary specifications for thermal, mechanical, and electrical properties.
- Panelization: Arrange multiple PCB designs into a panel layout to maximize efficiency during manufacturing. Panelization involves positioning multiple PCBs within a single panel to optimize material usage and facilitate handling during the fabrication process.
- Preparation of Substrate:Cut the 370HR laminate material into the desired panel size, ensuring proper alignment and cleanliness to prevent contamination during subsequent processing steps.
- Copper Cladding: Apply a thin layer of copper to both sides of the laminate material using a process called electroplating or lamination. The copper layer serves as the conductive surface for routing electrical signals on the PCB.
- Laser Drilling or Mechanical Drilling: Create holes for through-hole components, vias, and mounting holes using either laser drilling or mechanical drilling techniques. Laser drilling offers higher precision and is preferred for smaller hole sizes and higher density PCBs.
- Through-hole Plating: Plate the drilled holes with copper to establish electrical connections between different layers of the PCB. This process, known as through-hole plating, ensures continuity of electrical signals throughout the board.
- Circuit Patterning: Apply a layer of photoresist material to the copper-clad substrate and expose it to UV light through a photomask containing the PCB traces and features. Develop and etch the exposed areas to remove unwanted copper and define the circuit pattern.
- Surface Finish: Apply a surface finish to protect the exposed copper traces and pads from oxidation and ensure solderability during assembly. Common surface finish options include HASL (Hot Air Solder Leveling), ENIG (Electroless Nickel Immersion Gold), and OSP (Organic Solderability Preservative).
- Silkscreen Printing:Print component designators, logos, and other markings onto the PCB surface using silkscreen printing. This step provides visual identification and assembly guidance for components.
- Final Inspection and Testing: Conduct a thorough inspection of the fabricated PCBs to ensure that they meet the required quality standards and specifications. Perform electrical testing, visual inspection, and dimensional verification to validate the integrity and functionality of the boards.
- Routing and Separation: After fabrication and testing, separate the individual PCBs from the panel using routing or depanelization techniques. Clean the boards to remove any residues or contaminants accumulated during the fabrication process.
By following these steps and adhering to best practices for PCB fabrication, manufacturers can produce high-quality PCBs using 370HR materials that meet the performance, reliability, and quality requirements of diverse electronic applications.
How do you manufacture a 370HR Materials PCB?
Manufacturing a PCB using 370HR materials involves several steps, similar to the fabrication process of other PCBs. Here’s a detailed guide to manufacturing a PCB with 370HR materials:
- Preparation of Design Files: Begin by creating the design files for the PCB using PCB design software. These files contain information about the layout, traces, components, and other features of the PCB.
- Material Selection: Choose the appropriate grade of 370HR laminate material based on the specific requirements of the application. Ensure that the material meets the necessary specifications for thermal, mechanical, and electrical properties.
- Panelization: Arrange multiple PCB designs into a panel layout to maximize efficiency during manufacturing. Panelization involves positioning multiple PCBs within a single panel to optimize material usage and facilitate handling during the manufacturing process.
- Preparation of Substrate: Cut the 370HR laminate material into the desired panel size, ensuring proper alignment and cleanliness to prevent contamination during subsequent processing steps.
- Copper Cladding: Apply a thin layer of copper foil to both sides of the laminate material using an adhesive or lamination process. The copper layer serves as the conductive surface for routing electrical signals on the PCB.
- Drilling: Create holes for through-hole components, vias, and mounting holes using mechanical drilling or laser drilling techniques. Laser drilling offers higher precision and is preferred for smaller hole sizes and higher density PCBs.
- Through-hole Plating: Plate the drilled holes with copper to establish electrical connections between different layers of the PCB. This process, known as through-hole plating, ensures continuity of electrical signals throughout the board.
- Circuit Patterning: Apply a layer of photoresist material to the copper-clad substrate and expose it to UV light through a photomask containing the PCB traces and features. Develop and etch the exposed areas to remove unwanted copper and define the circuit pattern.
- Surface Finish: Apply a surface finish to protect the exposed copper traces and pads from oxidation and ensure solderability during assembly. Common surface finish options include HASL (Hot Air Solder Leveling), ENIG (Electroless Nickel Immersion Gold), and OSP (Organic Solderability Preservative).
- Silkscreen Printing: Print component designators, logos, and other markings onto the PCB surface using silkscreen printing. This step provides visual identification and assembly guidance for components.
- Final Inspection and Testing: Conduct a thorough inspection of the manufactured PCBs to ensure that they meet the required quality standards and specifications. Perform electrical testing, visual inspection, and dimensional verification to validate the integrity and functionality of the boards.
- Routing and Separation: After manufacturing and testing, separate the individual PCBs from the panel using routing or depanelization techniques. Clean the boards to remove any residues or contaminants accumulated during the manufacturing process.
By following these steps and adhering to best practices for PCB manufacturing, manufacturers can produce high-quality PCBs using 370HR materials that meet the performance, reliability, and quality requirements of diverse electronic applications.
How much should a 370HR Materials PCB cost?
The cost of a 370HR materials PCB can vary significantly depending on various factors such as the complexity of the design, the size of the board, the number of layers, the quantity ordered, and the specific requirements of the application.
As a rough estimate, the cost of manufacturing a basic single-layer PCB using 370HR laminate material could range from a few dollars to tens of dollars per board, depending on factors such as size and quantity. However, for more complex designs with multiple layers, finer trace widths, tighter tolerances, and additional features such as impedance control or blind/buried vias, the cost per board would typically increase.
To obtain an accurate cost estimate for a specific PCB project, it’s best to consult with PCB manufacturers or suppliers. They can provide detailed quotes based on your design specifications, quantity requirements, and any additional services or features needed. Additionally, factors such as lead time, shipping costs, and any special requirements for testing or certification may also impact the overall cost of the PCBs.
What is 370HR Materials PCB base material?
The base material for a 370HR Materials PCB is a type of epoxy resin system reinforced with woven glass fabric. This composite material provides the substrate or foundation upon which the copper traces and components are mounted to create a printed circuit board (PCB).
370HR laminate material is specifically engineered for high-performance applications, offering a balance of thermal stability, mechanical strength, and electrical insulation properties. The “370HR” designation typically refers to a specific grade or specification of the laminate material, indicating its composition and performance characteristics.
Key properties of the base material for 370HR Materials PCBs include:
- Thermal Stability: The material exhibits good resistance to heat and maintains its dimensional stability over a wide temperature range, making it suitable for applications where thermal management is critical.
- Mechanical Strength: The woven glass reinforcement provides excellent mechanical strength and dimensional stability, ensuring the integrity of the PCB under mechanical stress, such as during handling, assembly, or operation.
- Electrical Insulation: The epoxy resin system offers high electrical insulation properties, preventing unintended electrical conductivity between adjacent traces or components on the PCB.
- Dielectric Constant and Loss Tangent: The material’s dielectric constant and loss tangent are important parameters for high-frequency applications, affecting signal integrity and transmission line behavior.
- Chemical Resistance: 370HR laminate material typically exhibits good resistance to chemicals and environmental factors, ensuring long-term reliability in various operating environments.
Overall, the base material used in 370HR Materials PCBs provides a stable and reliable foundation for the construction of high-performance electronic circuits, meeting the demanding requirements of industries such as aerospace, automotive, telecommunications, and medical devices.
Which company makes 370HR Materials PCB?
370HR Materials PCB is a high-performance printed circuit board (PCB) made with a specific 370HR base material. Currently, several well-known PCB material manufacturers produce 370HR base materials, including Rogers Corporation, Hitachi Chemical, Shin-Etsu Chemical Co., Ltd., and others.
Our company is a professional PCB manufacturer with advanced production equipment and extensive experience, capable of producing various types of PCBs, including those using 370HR materials. Our production processes and quality control procedures comply with international standards, ensuring that the 370HR Materials PCBs we produce have excellent performance and reliability.
As a PCB manufacturer, our company has the following capabilities and advantages:
- Professional Team: We have an experienced engineering team and technical personnel who can provide comprehensive technical support and solutions to meet customers’ specific needs and requirements.
- Advanced Production Equipment: We use state-of-the-art production equipment and processes, including automated production lines and precision control equipment, to efficiently and accurately manufacture 370HR Materials PCBs.
- Strict Quality Control: We implement strict quality management systems, conducting rigorous quality control and inspection at every stage from raw material procurement to finished product delivery, ensuring stable and reliable product quality.
- Flexible Production Capacity: We have flexible production capabilities and fast delivery cycles to meet customers’ requirements for different quantities and delivery times, ensuring timely delivery.
- Customized Services: We provide customized services, designing and manufacturing 370HR Materials PCBs according to customers’ specific requirements and application scenarios, ensuring that the products fully meet their needs.
In summary, as a professional PCB manufacturer, we have the capability and experience to produce 370HR Materials PCBs and are committed to providing customers with high-quality, reliable, and customized PCB solutions.
What are the 7 qualities of good customer service?
Good customer service is essential for building positive relationships with customers and ensuring their satisfaction. Here are seven qualities that contribute to good customer service:
- Empathy:Empathy involves understanding and sharing the feelings of customers. Good customer service representatives listen attentively to customers’ concerns, validate their emotions, and demonstrate empathy by showing that they genuinely care about resolving issues and meeting their needs.
- Communication Skills: Effective communication is crucial for providing good customer service. Customer service representatives should communicate clearly and politely, using appropriate language and tone. They should be able to explain products or services, answer questions, and provide assistance in a way that is easy for customers to understand.
- Patience: Patience is essential when dealing with customers, especially those who may be upset or frustrated. Customer service representatives should remain calm and composed, even in challenging situations, and take the time to address customers’ concerns thoroughly and thoughtfully.
- Problem-Solving Skills:Good customer service involves being proactive in resolving issues and finding solutions to customers’ problems. Customer service representatives should be resourceful, analytical, and able to think critically to identify the root cause of problems and implement effective solutions.
- Product Knowledge: Customer service representatives should have a deep understanding of the products or services they are supporting. They should be knowledgeable about product features, specifications, pricing, and troubleshooting procedures, enabling them to provide accurate information and assistance to customers.
- Responsiveness: Prompt and timely responses are key to good customer service. Customers appreciate quick assistance and expect timely resolution of their inquiries or issues. Customer service representatives should be responsive to customer inquiries, whether through phone, email, chat, or other communication channels, and strive to provide timely updates and follow-ups.
- Professionalism: Professionalism encompasses various aspects of behavior, including reliability, integrity, and respectfulness. Good customer service representatives maintain a professional demeanor at all times, adhere to company policies and procedures, and treat customers with courtesy, respect, and fairness.
By embodying these qualities, businesses can deliver excellent customer service experiences that foster loyalty, satisfaction, and positive word-of-mouth recommendations.
FAQs
What is 370HR laminate material?
370HR laminate material is a type of epoxy resin system reinforced with woven glass fabric, commonly used as the base material for high-performance printed circuit boards (PCBs).
What are the key properties of 370HR Materials PCBs?
Key properties of 370HR Materials PCBs include excellent thermal stability, mechanical strength, electrical insulation, and resistance to chemicals and environmental factors.
What are the typical applications of 370HR Materials PCBs?
370HR Materials PCBs are used in various industries and applications requiring high reliability and performance, such as aerospace, automotive, telecommunications, medical devices, and industrial equipment.
What are the advantages of using 370HR Materials PCBs?
Advantages of using 370HR Materials PCBs include their ability to withstand high temperatures, mechanical stress, and harsh operating conditions, as well as their excellent electrical insulation properties and reliability.
What manufacturing processes are involved in producing 370HR Materials PCBs?
The manufacturing process for 370HR Materials PCBs involves steps such as material selection, panelization, copper cladding, drilling, through-hole plating, circuit patterning, surface finishing, silkscreen printing, final inspection, and routing/separation.
Where can I purchase 370HR Materials PCBs?
370HR Materials PCBs can be purchased from various PCB manufacturers or suppliers who specialize in producing high-performance PCBs using 370HR laminate material. It’s essential to choose a reputable supplier with experience and expertise in manufacturing these types of PCBs.
What factors should I consider when designing a PCB using 370HR laminate material?
When designing a PCB using 370HR laminate material, it’s essential to consider factors such as thermal management, signal integrity, mechanical strength, electromagnetic compatibility (EMC), layer stackup, component placement, environmental considerations, testing, and validation.