WBLGA Substrates Manufacturer
WBLGA Substrates Manufacturer,WBLGA substrates are advanced components used in semiconductor packaging, featuring a grid of metal pads for wire bonding ICs to external circuits. They excel in compactness, efficient heat dissipation, and high-density interconnections, making them ideal for modern electronics requiring superior performance and reliability. Manufactured from materials like ceramics or organic laminates, WBLGA substrates undergo precise metallization, dielectric layer deposition, and rigorous quality control to ensure optimal electrical and mechanical properties. They are pivotal in applications such as microprocessors, memory modules, and RF devices, where space efficiency and robust interconnection capabilities are paramount.
What is a WBLGA Substrate?
A WBLGA substrate refers to a type of substrate used in semiconductor packaging technology, specifically in Wire Bonded Land Grid Array (WBLGA) packages. These packages are used for integrated circuits (ICs) and microchips where compact size, thermal management, and electrical performance are crucial. The WBLGA substrate typically consists of a thin, flat piece of material, often ceramic or laminate, with a grid of metal pads arranged in a specific pattern. These pads serve as connection points for the wire bonds that link the IC die to the package substrate.
The choice of substrate material is critical as it affects the thermal dissipation capabilities, electrical performance, and overall reliability of the packaged IC. Ceramic substrates, for instance, offer excellent thermal conductivity and mechanical strength, making them suitable for high-power applications. On the other hand, laminate substrates may be more cost-effective and offer good electrical performance for moderate-power ICs.
In summary, a WBLGA substrate is an integral part of semiconductor packaging, providing a platform for connecting the IC die to external circuitry through wire bonds, while also facilitating efficient heat dissipation and ensuring reliable electrical connections. Its design and material choice are tailored to meet the specific requirements of the packaged IC in terms of performance, reliability, and size constraints.
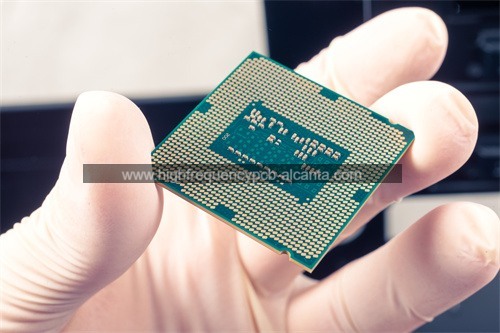
WBLGA Substrates Manufacturer
What are WBLGA Substrate Design Guidelines?
Design guidelines for WBLGA (Wire Bonded Land Grid Array) substrates are critical to ensure optimal performance and reliability of semiconductor packages. Here are some key guidelines typically considered:
- Substrate Material Selection: Choose a substrate material based on the specific requirements of the IC, considering factors such as thermal conductivity, coefficient of thermal expansion (CTE) matching with the IC and the package materials, mechanical strength, and cost.
- Substrate Layout and Dimensions:Design the substrate layout to accommodate the IC die size and the pitch of wire bond pads. Ensure adequate spacing between pads to prevent electrical shorting and facilitate wire bonding.
- Pad and Trace Design:Optimize the design of bonding pads and traces for electrical performance and reliability. This includes ensuring proper pad dimensions, spacing, and routing to minimize impedance and signal degradation.
- Via Design: Use appropriate via structures to connect different layers of the substrate. Ensure via size, spacing, and placement are optimized for electrical integrity and mechanical strength.
- Thermal Management:Incorporate thermal vias and thermal pads in the substrate design to enhance heat dissipation from the IC. Consider the thermal conductivity of the substrate material and the thermal path from the IC to the package’s external environment.
- Signal Integrity: Minimize signal distortion and noise by carefully designing signal trace routing, impedance matching, and minimizing signal path lengths. This is crucial for maintaining signal integrity at high frequencies.
- Mechanical Reliability:Ensure the substrate design can withstand mechanical stresses during handling, assembly, and operation. This includes considering the mechanical properties of the substrate material and the robustness of bonding interfaces.
- Assembly and Manufacturing Considerations:Design for manufacturability by considering process capabilities of substrate fabrication, wire bonding, and assembly processes. Ensure alignment marks and fiducials are included for accurate assembly.
- Package Size and Form Factor:Optimize the overall package size and form factor to meet application requirements, while considering space constraints and compatibility with existing assembly and mounting processes.
- Reliability Testing:Perform reliability testing to validate the substrate design under various environmental conditions (thermal cycling, humidity, mechanical shock, etc.) to ensure long-term performance and reliability of the packaged IC.
By adhering to these design guidelines, semiconductor manufacturers can develop WBLGA substrates that meet the stringent requirements of modern electronic devices in terms of performance, reliability, and manufacturability. Each guideline plays a crucial role in optimizing the substrate design to achieve these goals effectively.
What is the WBLGA Substrate Fabrication Process?
The fabrication process of WBLGA (Wire Bonded Land Grid Array) substrates involves several key steps to create a robust platform for mounting and connecting integrated circuits (ICs). Here’s an overview of the typical fabrication process:
- Substrate Material Selection:Substrates for WBLGA packages are often made from ceramic materials (such as alumina or aluminum nitride) or organic laminates (such as FR4). The choice depends on factors like thermal conductivity, mechanical strength, electrical properties, and cost.
- Substrate Preparation:The fabrication begins with preparing the substrate material in large sheets or panels. This may involve cutting or shearing the material to the desired size depending on the final package dimensions.
- Surface Preparation:The substrate surface is prepared to ensure it is clean and free from contaminants. This typically involves cleaning processes such as degreasing, solvent cleaning, and sometimes plasma treatment to improve adhesion of subsequent layers.
- Layer Build-Up:Depending on the complexity of the substrate design, multiple layers of conductive and insulating materials may be deposited or laminated onto the substrate. This includes:
– Conductor Deposition: Conductive traces and pads are patterned onto the substrate using methods like screen printing, thin-film deposition (such as sputtering or evaporation), or additive processes like electroplating.
– Dielectric Layer Deposition: Insulating layers (dielectrics) are deposited or laminated between conductor layers to separate and isolate electrical pathways.
- Via Formation:Vias are small holes drilled or etched through the substrate layers to provide vertical electrical connections between different conductor layers. Vias may be formed using mechanical drilling, laser drilling, or chemical etching depending on the substrate material and design requirements.
- Surface Finish:The substrate surface is finished to enhance solderability and ensure proper wire bonding capability. Common surface finishes include electroless nickel immersion gold (ENIG), organic solderability preservative (OSP), or hot air solder leveling (HASL).
- Solder Mask Application:A solder mask is applied over the substrate surface except where electrical contacts (pads) are located. The solder mask protects the substrate and defines the areas where solder connections will be made during assembly.
- Final Inspection and Testing:After fabrication, the substrates undergo rigorous inspection and testing to ensure they meet quality standards and design specifications. This includes dimensional inspection, electrical continuity checks, and sometimes automated optical inspection (AOI) to detect defects.
- Packaging and Shipping:Once substrates pass inspection, they are typically packaged in protective containers and shipped to semiconductor assembly facilities where ICs are mounted and wire bonded onto the substrates.
The fabrication process of WBLGA substrates requires precision in material handling, patterning, and quality control to ensure reliable performance of the packaged ICs. Advances in manufacturing technology continue to improve substrate design and fabrication techniques, allowing for higher density, improved thermal management, and enhanced electrical performance in modern semiconductor packages.
How do you manufacture WBLGA Substrates?
The fabrication process of WBLGA (Wire Bonded Land Grid Array) substrates involves a series of meticulous steps to create a robust platform for connecting integrated circuits (ICs) to external circuitry. Here’s a detailed overview of the typical fabrication process:
- Substrate Material Selection: Begin by selecting the substrate material based on the IC package requirements, considering factors like thermal conductivity, CTE (Coefficient of Thermal Expansion), mechanical strength, and cost.
- Substrate Preparation: Cut the substrate material into the desired size and shape using precision machining techniques to meet dimensional tolerances.
- Surface Preparation: Clean and possibly treat the substrate surfaces to ensure proper adhesion of subsequent layers or metallization.
- Metallization: Deposit thin layers of metals (e.g., copper or aluminum) onto the substrate surfaces through techniques like sputtering, evaporation, or electroplating. Form bonding pads, signal traces, ground planes, and via structures for electrical connectivity.
- Dielectric Layer Deposition: Deposit insulating dielectric layers over the metallized substrate to electrically isolate different conductive layers and provide mechanical support. Use techniques such as spin coating, CVD, or screen printing.
- Via Formation: Create vias to establish electrical connections between different metallization layers. This involves drilling or laser ablation, followed by metallization of the via walls for electrical continuity. Optionally, fill vias with conductive material to enhance reliability.
- Surface Finish: Treat exposed metallization surfaces with a surface finish (e.g., immersion tin, immersion silver, ENIG, OSP) to protect against oxidation and facilitate wire bonding.
- Quality Control: Implement stringent quality control measures throughout the process to ensure dimensional accuracy, metallization quality, and electrical performance. Conduct inspections, electrical tests, and dimensional measurements.
- Final Testing and Packaging: Perform final testing to verify electrical functionality, reliability, and thermal performance of the fabricated substrates. Prepare substrates for assembly into semiconductor packages, where IC dies are mounted and wire bonded.
- Documentation and Traceability: Maintain comprehensive documentation of the fabrication process, materials used, and test results for traceability and quality assurance purposes. Document procedures for troubleshooting, process improvement, and compliance with regulatory standards.
In summary, the WBLGA substrate fabrication process demands precision and adherence to strict quality standards to ensure the substrates meet the rigorous requirements of modern semiconductor packaging. Each step—from material selection to final testing—is crucial in achieving optimal electrical connectivity, thermal management, mechanical stability, and overall reliability of the packaged ICs.
How much should WBLGA Substrates cost?
The cost of WBLGA (Wire Bonded Land Grid Array) substrates can vary widely depending on several factors related to materials, complexity of design, manufacturing processes, and market conditions. Here are key factors that influence the cost:
- Substrate Material: The choice of substrate material significantly impacts cost. Ceramic substrates (e.g., alumina, aluminum nitride) are typically more expensive than organic substrates (e.g., FR4, polyimide) due to their superior thermal conductivity and mechanical properties.
- Substrate Size and Complexity: Larger substrates or those with intricate designs requiring more layers, finer features, and tighter tolerances tend to cost more to manufacture. Complex designs with multiple vias, fine pitch bonding pads, and special surface finishes can also increase costs.
- Metallization and Surface Finish: The metallization process, which involves depositing metal layers and applying surface finishes (e.g., immersion tin, ENIG), adds to the substrate cost. Higher quality surface finishes for better electrical performance may come at a premium.
- Manufacturing Volume: Economies of scale play a significant role in substrate cost. Larger production volumes generally lead to lower per-unit costs due to efficiencies in materials procurement, manufacturing processes, and overhead expenses.
- Quality and Reliability Requirements: Meeting stringent quality standards and reliability specifications (e.g., thermal cycling, electrical testing) may require additional process steps and testing, which can impact cost.
- Market Dynamics: Market conditions, including supply and demand fluctuations, can influence substrate costs. Prices of raw materials (e.g., metals, ceramics) and global economic factors also play a role.
- Supplier and Location: The choice of substrate supplier and their geographic location can affect costs due to labor rates, regulatory requirements, and shipping expenses.
As a rough estimate, WBLGA substrates can range from several dollars to tens of dollars per unit, depending on the above factors. For high-performance applications requiring advanced materials and stringent specifications, costs can be higher. Conversely, for simpler designs and larger production runs, costs may be more economical.
To get an accurate cost estimate for WBLGA substrates, it’s essential to consult with substrate manufacturers or suppliers who can provide quotes based on specific design requirements, quantities, and quality standards needed for your application.
What is WBLGA Substrate base material?
The base material used for WBLGA (Wire Bonded Land Grid Array) substrates can vary depending on the specific requirements of the semiconductor package and the performance characteristics desired. Here are some common materials used as base substrates for WBLGA packages:
- Ceramics:
– Alumina (Al2O3): Alumina is a widely used ceramic substrate material due to its excellent thermal conductivity, mechanical strength, and reliability. It is suitable for applications requiring good heat dissipation and high electrical insulation.
– Aluminum Nitride (AlN): Aluminum nitride offers even higher thermal conductivity than alumina, making it ideal for applications requiring superior heat dissipation capabilities. It also exhibits good electrical insulation properties.
- Laminates:
– FR4 (Flame Retardant 4): FR4 is a popular epoxy-based laminate substrate material. It is cost-effective and widely used in PCB (Printed Circuit Board) manufacturing due to its good electrical insulation properties and ease of fabrication.
– Polyimide: Polyimide substrates offer excellent thermal stability, flexibility, and low dielectric constant. They are suitable for applications requiring high-temperature operation and reliability.
- Other Materials:
– Copper (Metal Core Substrates): Some substrates use copper as a base material, especially in metal core substrates where a thin layer of copper provides good thermal conductivity while maintaining electrical insulation properties through dielectric layers.
The choice of substrate base material depends on various factors such as thermal management requirements, electrical performance needs, mechanical stability, cost considerations, and specific application requirements (e.g., high-frequency operation, high-power applications). Manufacturers select the substrate material that best balances these factors to achieve optimal performance and reliability in WBLGA semiconductor packages. Each material offers different advantages in terms of thermal conductivity, mechanical strength, dimensional stability, and electrical insulation, catering to diverse needs across various industries and applications in electronics.
Which company manufactures WBLGA Substrates?
There are many companies currently manufacturing WBLGA (Wire Bonded Land Grid Array) substrates, primarily concentrated in the semiconductor packaging and electronic components manufacturing sectors. These companies include internationally renowned semiconductor materials and manufacturers such as Mitsui Chemicals and Toray Industries from Japan, Murata Manufacturing, Rogers Corporation from the United States, and Schott AG from Germany. These companies provide high-performance and reliable semiconductor packaging solutions to the global electronics industry through their advanced manufacturing technologies and materials science expertise.
If our company has the capability to manufacture WBLGA substrates, we would need to possess the following key capabilities and resources:
- Advanced Material Selection and Process Technology: Our company must have the capability to select and process various substrate materials, including ceramics (such as alumina, aluminum nitride) and organic substrates (such as FR4, polyimide). We should be able to flexibly choose the most suitable substrate materials according to customer requirements and application needs.
- Precision Machining and Manufacturing Capability: We need advanced machining equipment and techniques to accurately cut, drill, metallize, and surface treat substrates, ensuring high quality and precision during the manufacturing process.
- Electrical Performance and Thermal Management Design Capability: Capability to design and optimize substrate electrical performance, including optimal routing for signal transmission and thermal management in packaging, ensuring reliability and stability under various operating conditions.
- Quality Control and Testing Capability: Establish a robust quality management system for strict quality control and testing, including comprehensive inspection and testing of dimensions, surface smoothness, metallization quality, and electrical performance for each batch of substrates.
- Customization Services and Technical Support: Ability to provide customized solutions and technical support according to customer needs, including design optimization, prototype manufacturing, mass production, and after-sales service.
If our company is able to manufacture WBLGA substrates, we will leverage these key capabilities and resources to deliver high-quality, highly reliable semiconductor packaging solutions to our customers. We will work closely with customers to understand their needs and provide customized technical support, ensuring their success in the competitive market.
What are the 7 qualities of good customer service?
Good customer service is characterized by several key qualities that contribute to a positive customer experience and build customer loyalty. Here are seven qualities that define good customer service:
- Responsiveness: Responding promptly to customer inquiries, requests, or issues demonstrates attentiveness and respect for their time. Whether it’s answering phone calls, replying to emails, or addressing concerns on social media, prompt responsiveness is crucial.
- Empathy: Showing empathy means understanding and sharing the feelings of the customer. It involves listening actively to their concerns, acknowledging their emotions, and demonstrating genuine concern for their situation.
- Clarity: Communicating clearly and effectively is essential in customer service. This includes using simple language, providing accurate information, and ensuring that the customer understands any explanations or instructions given.
- Professionalism: Maintaining a professional demeanor and attitude at all times contributes to a positive customer experience. This involves being courteous, respectful, and knowledgeable about products or services.
- Problem-solving Skills: Being able to resolve customer issues efficiently and effectively is a hallmark of good customer service. This may involve understanding the problem, offering viable solutions, and taking ownership until the issue is fully resolved to the customer’s satisfaction.
- Personalization:Tailoring interactions to the specific needs and preferences of each customer can significantly enhance their experience. Personalization involves recognizing repeat customers, remembering their preferences, and making them feel valued and appreciated.
- Follow-up: Following up with customers after resolving an issue or completing a transaction shows dedication to their satisfaction. This may include checking if the solution met their expectations, offering additional assistance if needed, or seeking feedback for continuous improvement.
By embodying these qualities, businesses can create positive interactions with customers, foster loyalty, and build a reputation for exceptional customer service. These qualities not only satisfy immediate needs but also contribute to long-term relationships and customer retention.
FAQs (Frequently Asked Questions)
What materials are used for WBLGA substrates?
Common materials for WBLGA substrates include ceramics (e.g., alumina, aluminum nitride) and organic substrates (e.g., FR4, polyimide), chosen based on thermal management, electrical performance, and cost considerations.
How are WBLGA substrates manufactured?
The manufacturing process involves substrate material selection, metallization to create bonding pads and traces, dielectric layer deposition, via formation for interconnections, surface finish application, and rigorous quality control measures.
What are the applications of WBLGA substrates?
WBLGA substrates are used in various applications such as microprocessors, memory modules, RF devices, and other integrated circuits where compact size, high performance, and reliable interconnection are critical.
How do WBLGA substrates compare to other packaging technologies?
Compared to other technologies like flip chip or ball grid array (BGA), WBLGA substrates offer specific advantages such as easier inspection, repairability, and flexibility in design configurations.
What factors should be considered when choosing WBLGA substrates?
Factors to consider include thermal conductivity of the substrate material, CTE (Coefficient of Thermal Expansion) matching with IC and package materials, mechanical strength, electrical performance, and cost-effectiveness.
What are the reliability considerations for WBLGA substrates?
Reliability considerations include thermal cycling performance, mechanical stress resilience, wire bond integrity, and long-term stability under various operating conditions.
Can WBLGA substrates be customized for specific applications?
Yes, WBLGA substrates can be customized in terms of substrate material, dimensions, metallization patterns, and surface finishes to meet the specific requirements of different semiconductor applications.