WBFCCSP Substrate Manufacturer
WBFCCSP Substrate Manufacturer,The WBFCCSP (Wafer-Bonded Flip Chip Chip Scale Package) substrate is a cutting-edge packaging solution designed for miniaturized electronic devices. It combines the benefits of wafer-bonded technology and flip chip assembly to deliver superior electrical performance and thermal management in a compact form factor. This substrate is ideal for high-density applications, providing enhanced signal integrity and reduced parasitic effects. The WBFCCSP substrate supports advanced integration and reliability, making it suitable for smartphones, tablets, wearables, and other portable electronics. Its efficient heat dissipation capabilities and excellent mechanical stability ensure optimal performance in demanding environments.
What is a WBFCCSP Substrate?
WBFCCSP (Wafer-Level Ball Grid Array with Fused Core Ceramic Substrate) is an advanced semiconductor packaging technology that combines the advantages of wafer-level packaging (WLCSP) with a fused core ceramic substrate. This technology utilizes a specialized ceramic substrate to enhance the electrical performance and mechanical strength of the package.
The core material of the WBFCCSP substrate is fused core ceramic, which offers excellent thermal conductivity and high-temperature stability, making it suitable for high-power and high-frequency applications. The ceramic substrate surface is finely processed to ensure good contact with the chip and supports high-density ball grid array (BGA) arrangements. The BGA array provides electrical connections to the main board while effectively dissipating heat from the chip.
One of the key benefits of this technology is its improved heat dissipation and electrical performance. Due to the ceramic material’s low thermal expansion coefficient and high thermal conductivity, WBFCCSP packages perform more stably under high thermal loads. Additionally, it helps reduce the package size and increase integration density, making it ideal for applications with strict size and performance requirements, such as smartphones, computers, and communication devices.
Overall, WBFCCSP is a high-performance packaging solution that meets the demands of modern electronic devices for high power and high frequency while maintaining a compact package size and excellent heat dissipation capabilities.
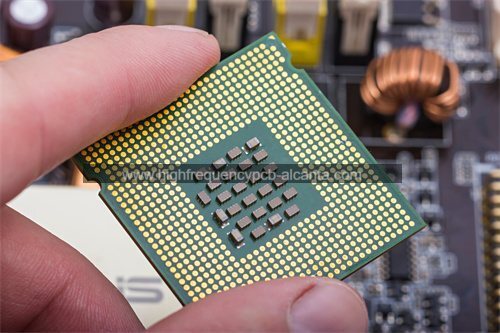
WBFCCSP Substrate Manufacturer
What is the WBFCCSP Substrate Design Guidelines?
The WBFCCSP (Wafer-Level Ball Grid Array with Fused Core Ceramic Substrate) design guidelines are essential for optimizing the performance and reliability of this advanced packaging technology. These guidelines ensure that the substrate design meets the requirements for high power, high frequency, and compact size applications. Here are the key design considerations:
- Material Selection:Use high-quality fused core ceramic materials with excellent thermal conductivity and low thermal expansion coefficients. This enhances heat dissipation and thermal stability.
- Thermal Management: Design the substrate with effective thermal pathways to ensure efficient heat dissipation from the chip. Integrate heat spreaders or thermal vias if necessary.
- Pad and Ball Layout: Ensure precise alignment of the BGA balls and pad layout. The pad size and ball pitch should accommodate high-density connections while maintaining reliability.
- Layer Structure: Optimize the substrate layer structure to balance mechanical strength and electrical performance. Consider using multiple layers to support complex routing and signal integrity.
- Signal Integrity: Implement controlled impedance traces and appropriate grounding techniques to minimize signal interference and maintain signal integrity at high frequencies.
- Mechanical Strength: Design for mechanical robustness to withstand thermal cycling and mechanical stress. Use reinforcement techniques if needed to prevent warping or delamination.
- Manufacturing Tolerances: Account for manufacturing tolerances in the design to ensure reliable assembly and functionality. Precision in fabrication is critical for high-density designs.
- Testing and Validation: Incorporate testing features into the design to facilitate quality control and reliability testing. This includes design for test (DFT) considerations and test access points.
- Environmental Considerations: Design for durability in various environmental conditions, including moisture resistance and temperature extremes.
- Compliance and Standards: Ensure that the design complies with industry standards and regulations relevant to semiconductor packaging and electronics.
By adhering to these design guidelines, the WBFCCSP substrate can achieve optimal performance and reliability for demanding electronic applications.
What is the WBFCCSP Substrate Fabrication Process?
The fabrication process for a WBFCCSP (Wafer-Level Ball Grid Array with Fused Core Ceramic Substrate) involves several critical steps to ensure high performance and reliability. Here’s an overview of the process:
- Substrate Preparation:Start with a high-quality fused core ceramic material. The ceramic substrate is prepared to meet the required dimensions and specifications.
- Deposition of Metallization Layers: Apply thin metal layers onto the ceramic substrate. This typically involves sputtering or evaporation techniques to create a conductive layer that will form the circuit pathways.
- Patterning: Use photolithography to define the circuit patterns on the metal layers. This process involves applying a photoresist layer, exposing it to UV light through a mask, and developing the resist to create the desired pattern.
- Etching: Remove unwanted metal from the substrate using chemical or plasma etching techniques. This leaves behind the circuit patterns necessary for electrical connections.
- Via Formation: Create vias (vertical interconnects) in the ceramic substrate where necessary. These vias are filled with conductive material, such as copper, to connect different layers of the substrate.
- Solder Mask Application:Apply a solder mask layer to protect areas of the substrate that should not be coated with solder. This helps prevent short circuits and ensures proper solder ball placement.
- Ball Grid Array (BGA) Solder Ball Placement: Place solder balls onto the designated pads on the substrate. This is typically done using automated placement equipment. The solder balls will later be reflowed to form the final electrical connections.
- Reflow Soldering: Heat the substrate to melt the solder balls, forming solid electrical connections between the substrate and the chip. This process also involves careful temperature control to prevent damage to the ceramic and other components.
- Inspection and Testing: Inspect the substrate for defects such as misaligned solder balls or faulty metallization. Perform electrical testing to ensure all connections are functional and meet performance specifications.
- Backgrinding and Dicing: For wafer-level packaging, the wafer is backgrinded to reduce its thickness. It is then diced into individual chips, each with its own WBFCCSP substrate.
- Packaging and Assembly: Assemble the chips onto the final product or board, ensuring proper alignment and connection. Conduct final testing to confirm the performance and reliability of the completed assembly.
- Quality Control:Throughout the fabrication process, maintain strict quality control to ensure each substrate meets the required specifications and performance standards.
By following these fabrication steps, the WBFCCSP substrates achieve high reliability and performance, suitable for demanding electronic applications.
How do you Manufacture a WBFCCSP Substrate?
Manufacturing a WBFCCSP (Wafer-Level Ball Grid Array with Fused Core Ceramic Substrate) involves a series of precise and complex steps to ensure high performance and reliability. Here is an overview of the manufacturing process:
- Material Selection and Preparation: Start with high-quality fused core ceramic material. Prepare the ceramic substrate by cutting it to the required dimensions and ensuring it meets the specified material properties.
- Metallization Deposition: Apply a thin layer of metal, typically copper, onto the ceramic substrate. This is usually achieved through sputtering or evaporation techniques to form the conductive pathways needed for circuit connections.
- Photolithography: Coat the metallized substrate with a photoresist layer. Use photolithography to project circuit patterns onto the photoresist through a mask. Develop the photoresist to create the desired circuit patterns on the metal layer.
- Etching: Remove the unwanted metal from the substrate using etching processes (chemical or plasma etching). This step defines the electrical pathways and connections on the substrate.
- Via Formation: Create vias in the ceramic substrate where vertical interconnects are needed. Fill these vias with conductive materials like copper to establish connections between different layers of the substrate.
- Solder Mask Application: Apply a solder mask to protect areas of the substrate that should not be covered with solder. This mask ensures that solder balls adhere only to the designated pads and helps prevent short circuits.
- Solder Ball Placement: Place solder balls onto the pads using automated placement equipment. Ensure precise alignment to maintain high-density connections.
- Reflow Soldering: Heat the substrate to reflow the solder balls. This process melts the solder balls to form solid electrical connections between the substrate and the chip. Proper temperature control is crucial to avoid damage to the ceramic and other components.
- Inspection and Testing: Inspect the substrate for defects such as misaligned solder balls or faulty metallization. Perform electrical testing to ensure that all connections are functional and meet performance standards.
- Backgrinding and Dicing: For wafer-level packaging, backgrind the wafer to reduce its thickness. Dice the wafer into individual substrates, each with its own WBFCCSP.
- Packaging and Assembly: Assemble the diced substrates onto the final product or circuit board. Ensure proper alignment and secure connections during assembly.
- Final Testing and Quality Control: Conduct comprehensive testing to verify the performance and reliability of the WBFCCSP substrates. Implement quality control measures throughout the process to ensure compliance with industry standards and specifications.
By following these detailed manufacturing steps, WBFCCSP substrates are produced to meet high performance and reliability requirements for advanced electronic applications.
How Much Should a WBFCCSP Substrate Cost?
The cost of a WBFCCSP (Wafer-Level Ball Grid Array with Fused Core Ceramic Substrate) can vary widely based on several factors. Here’s a breakdown of the key elements that influence the cost:
- Material Costs: High-quality fused core ceramic materials are expensive. The choice of ceramic and any additional processing required can significantly impact costs.
- Complexity of Design: The more complex the design (e.g., high-density ball grid array, intricate vias, or multiple layers), the higher the fabrication cost. Custom designs with advanced features can be more costly.
- Wafer Size and Yield: The size of the wafer used in production affects the cost. Larger wafers may have higher material costs, and lower yield due to defects can increase the overall cost per unit.
- Manufacturing Process: Advanced processes like photolithography, etching, and reflow soldering involve significant equipment and operational costs. The more advanced the technology, the higher the manufacturing cost.
- Volume of Production: Higher production volumes typically reduce the cost per unit due to economies of scale. Lower volumes or prototype runs can be significantly more expensive.
- Testing and Quality Control: Comprehensive testing and quality control measures add to the cost. Ensuring that each substrate meets performance and reliability standards requires additional resources.
- Lead Time: Shorter lead times may result in higher costs due to expedited production and shipping processes.
- Geographic Location: Manufacturing costs can vary based on location due to differences in labor costs, overhead, and regional economic factors.
On average, the cost of a WBFCCSP substrate can range from $2 to $50 per unit. This broad range reflects the influence of the factors mentioned above. For precise pricing, it’s essential to contact manufacturers or suppliers with specific details about the design, volume, and additional requirements.
What is WBFCCSP Substrate Base Material?
The base material of a WBFCCSP (Wafer-Level Ball Grid Array with Fused Core Ceramic Substrate) is a crucial component that affects the substrate’s performance and reliability. Here’s an overview of the base material used in WBFCCSP substrates:
- Fused Core Ceramic: The primary base material for WBFCCSP substrates is fused core ceramic. This material is known for its excellent thermal conductivity and stability. Fused core ceramics are specifically chosen for their ability to handle high temperatures and provide good heat dissipation.
- Ceramic Types: Various types of ceramics can be used, including alumina (Al₂O₃) and beryllia (BeO). Alumina is commonly used due to its cost-effectiveness and good electrical insulation properties, while beryllia offers superior thermal conductivity but is more expensive and requires careful handling.
- Thermal Properties: Fused core ceramics are selected for their low thermal expansion coefficient and high thermal conductivity. These properties ensure effective heat dissipation from the chip and help maintain stability under thermal cycling conditions.
- Electrical Properties: The ceramic base material provides excellent electrical insulation, which is essential for preventing short circuits and ensuring signal integrity. The dielectric constant of the ceramic material must be suitable for the application to ensure proper electrical performance.
- Mechanical Strength: The ceramic material must have sufficient mechanical strength to support the chip and withstand stresses during manufacturing and operation. Fused core ceramics are designed to be robust and durable.
- Surface Treatment: The ceramic base material often undergoes surface treatments to enhance adhesion with metal layers and solder balls. These treatments ensure good electrical contact and reliable soldering.
- Layer Structure: In some cases, the ceramic base may be layered with additional materials or have integrated metal layers to support complex circuit designs. This layer structure is crucial for high-density applications and maintaining electrical performance.
In summary, the base material of a WBFCCSP substrate is primarily fused core ceramic, chosen for its thermal and electrical properties. The selection of specific ceramic types and additional treatments depends on the performance requirements of the final application.
Which Company Makes WBFCCSP Substrates?
WBFCCSP (Wafer-Level Ball Grid Array with Fused Core Ceramic Substrate) is an advanced packaging technology, and several companies worldwide produce this type of substrate. Here are some major manufacturers of WBFCCSP substrates:
- Taiwan Semiconductor Manufacturing Company (TSMC): TSMC is a global leader in semiconductor manufacturing and also offers advanced packaging solutions, including WBFCCSP substrates. Their expertise in semiconductor technology and production capabilities enable them to produce high-quality WBFCCSP substrates to meet the demands for high-frequency and high-power applications.
- Hitachi Chemical: Hitachi Chemical has extensive experience in advanced packaging materials and technologies. They provide a range of high-performance substrate solutions, including WBFCCSP, focusing on ceramics with high thermal conductivity and stability.
- Samsung Electronics: Samsung Electronics is a leading global player in integrated circuit manufacturing and has advanced packaging technologies. They offer WBFCCSP substrates suitable for high-density and high-performance electronic products.
- Kyocera:Kyocera is a globally recognized ceramic materials manufacturer and also produces high-performance WBFCCSP substrates. Kyocera’s products are known for their excellent thermal conductivity and electrical performance, widely used in various high-tech electronic devices.
- ASE Group (Advanced Semiconductor Engineering): ASE Group is a professional provider of semiconductor packaging and testing services, and they also manufacture WBFCCSP substrates. ASE has deep expertise in packaging technology and can deliver high-quality packaging solutions.
Our company also manufactures WBFCCSP substrates. We utilize advanced manufacturing technologies and high-quality materials to ensure the production of substrates that meet high-performance requirements. Our manufacturing process includes precise ceramic substrate processing, advanced metallization techniques, accurate photolithography and etching, and stringent quality control and testing. We are committed to providing high-reliability and high-performance WBFCCSP solutions, addressing the needs of high-frequency and high-power applications. Through continuous innovation and optimization of production processes, we deliver WBFCCSP solutions that meet customer expectations for performance and reliability.
What Are the 7 Qualities of Good Customer Service?
Good customer service is crucial for building strong relationships with customers and ensuring their satisfaction. Here are seven key qualities that define excellent customer service:
- Responsiveness: Quick and efficient responses to customer inquiries and issues are essential. Good customer service involves addressing concerns promptly, minimizing wait times, and providing timely solutions.
- Empathy: Understanding and relating to customers’ feelings and perspectives is vital. Empathetic customer service representatives listen actively, acknowledge customers’ emotions, and show genuine concern for their issues.
- Knowledgeability: Providing accurate and relevant information is crucial. Customer service representatives should have a deep understanding of the products or services they support and be able to offer expert guidance and solutions.
- Patience:Handling customers with patience, especially in challenging or complex situations, is important. Good customer service representatives remain calm and composed, allowing customers to express their concerns without feeling rushed.
- Communication Skills: Clear, concise, and effective communication is essential. Representatives should be able to explain information in an understandable manner, use appropriate language, and ensure that customers feel heard and valued.
- Professionalism: Maintaining a professional demeanor at all times helps build trust and respect. This includes being polite, respectful, and courteous, and adhering to company policies and procedures.
- Follow-Up: Ensuring that customer issues are resolved satisfactorily and following up to confirm resolution demonstrates commitment to customer satisfaction. This involves checking in with customers to ensure their needs were met and addressing any remaining concerns.
By embodying these qualities, customer service teams can enhance customer experiences, build loyalty, and contribute to overall business success.
FAQs
What is a WBFCCSP Substrate?
A WBFCCSP Substrate is a platform used for mounting and connecting integrated circuits in electronic devices.
What are the main steps in WBFCCSP Substrate fabrication?
The main steps include material selection, layer deposition, photolithography, etching, lamination, via formation, and testing.
How do I choose the right base material for WBFCCSP Substrates?
Base materials are chosen based on the required electrical and thermal properties. Ceramics and composites are commonly used.
How can I determine the cost of a WBFCCSP Substrate?
The cost depends on design complexity, material used, production volume, and manufacturing process.
Which companies manufacture WBFCCSP Substrates?
Various companies produce WBFCCSP Substrates, including ours, which offers high-quality solutions tailored to specific needs.