Ultrathin SIP Package Substrate Manufacturer
Ultrathin SIP Package Substrate Manufacturer,Ultrathin SIP Package Substrates are advanced electronic packaging solutions characterized by their slim profile and multi-layered construction. These substrates enable the integration and interconnection of various electronic components within a compact package, facilitating miniaturization and enhancing device performance. Utilizing materials like FR-4, polyimide, or liquid crystal polymer, Ultrathin SIP Package Substrates offer advantages such as reduced size, improved thermal management, and enhanced signal integrity. They find applications across industries including consumer electronics, telecommunications, automotive, and medical devices, driving innovation in compact and efficient electronic systems.
What is an Ultrathin SIP Package Substrate?
An Ultrathin SIP (System-in-Package) Package Substrate is a substrate, or a base layer, used in electronic packaging technology. It’s designed to be extremely thin, often measuring just a fraction of a millimeter in thickness. This thinness allows for compact and space-efficient packaging of electronic components, making it ideal for applications where size and weight are critical factors, such as mobile devices, wearables, and IoT (Internet of Things) devices.
These substrates typically consist of multiple layers of materials, including insulating layers, conductive traces, and vias (plated-through holes for electrical connections between layers). They provide the structural support and electrical connectivity for mounting and interconnecting various electronic components, such as integrated circuits (ICs), microprocessors, memory chips, and sensors, within a single package.
The ultrathin nature of these substrates enables manufacturers to achieve higher levels of miniaturization and integration in electronic devices, allowing for more functionality in smaller form factors. Additionally, the reduced thickness contributes to improved thermal management and signal integrity, which are crucial for maintaining the performance and reliability of electronic systems.
Overall, Ultrathin SIP Package Substrates play a vital role in enabling the development of compact, lightweight, and high-performance electronic devices that meet the demands of modern technology trends.
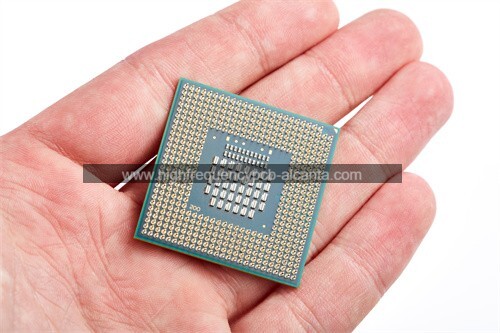
Ultrathin SIP Package Substrate Manufacturer
What are the Ultrathin SIP Package Substrate Design Guidelines?
Designing ultrathin SIP (System-in-Package) package substrates requires careful consideration of various factors to ensure optimal performance and reliability. Here are some general design guidelines:
- Thickness: The substrate thickness should be minimized to achieve the desired level of miniaturization while ensuring mechanical integrity. However, it should still provide sufficient support for the components mounted on it.
- Material Selection: Choose substrate materials with appropriate properties, such as high electrical conductivity, thermal conductivity, and mechanical strength. Common substrate materials include organic materials like FR-4 (fiberglass-reinforced epoxy) or more advanced materials like liquid crystal polymer (LCP) for their superior performance in high-frequency applications.
- Routing and Traces: Design the routing and traces on the substrate carefully to minimize signal interference, crosstalk, and impedance mismatch. Use controlled impedance routing techniques when necessary, especially for high-speed signal paths.
- Via Design: Optimize via design to ensure reliable electrical connections between different layers of the substrate. Consider factors such as via size, aspect ratio, and placement to minimize signal degradation and manufacturing challenges.
- Thermal Management: Implement effective thermal management techniques to dissipate heat generated by the components. This may include adding thermal vias, thermal pads, or heat spreaders to improve heat dissipation and prevent overheating.
- Assembly and Manufacturing: Consider manufacturability during the design phase to simplify assembly processes and reduce manufacturing costs. Design features like fiducial markers, solder mask openings, and component keep-out zones to facilitate accurate placement and soldering of components.
- Reliability and Durability: Ensure that the substrate design meets reliability and durability requirements for the intended application. Perform thorough mechanical and thermal stress analysis to identify potential failure modes and design accordingly.
- Signal Integrity Analysis: Conduct signal integrity analysis, such as simulations or modeling, to validate the substrate design and verify its performance under different operating conditions. Address any signal integrity issues early in the design process to avoid costly redesigns later.
By following these design guidelines, engineers can develop ultrathin SIP package substrates that meet the stringent requirements of modern electronic devices, including compact size, high performance, and reliability.
What is the Ultrathin SIP Package Substrate Fabrication Process?
The fabrication process for ultrathin SIP (System-in-Package) package substrates involves several steps to create the thin, multi-layered structures required for compact electronic packaging. Here’s a general overview of the fabrication process:
- Substrate Preparation: The process begins with preparing the base substrate material, which is typically a thin sheet of rigid or flexible material such as FR-4 (fiberglass-reinforced epoxy), polyimide, or liquid crystal polymer (LCP). The substrate is cleaned and treated to ensure proper adhesion of subsequent layers.
- Layer Deposition: Multiple layers of dielectric and conductive materials are deposited onto the substrate using various techniques such as sputtering, chemical vapor deposition (CVD), or electroplating. These layers form the insulating layers, conductive traces, and vias (plated-through holes) that make up the substrate’s structure.
- Pattern Formation: Photoresist material is applied to the substrate surface, and a photomask is used to define the desired patterns for the conductive traces and vias. The substrate is then exposed to UV light, which transfers the pattern onto the photoresist layer.
- Etching: The exposed areas of the substrate are etched away using chemical etchants, leaving behind the patterned conductive traces and vias. Multiple etching steps may be required to create the desired layer structure.
- Surface Finishing: After etching, the substrate surface may undergo surface finishing processes such as chemical treatment or mechanical polishing to improve surface smoothness and remove any residual contaminants.
- Lamination: If the substrate consists of multiple layers, they are assembled and laminated together using heat and pressure to form a single, cohesive structure. This process may also involve bonding additional layers of dielectric material between the conductive layers to create a multilayer stack.
- Drilling and Plating: Holes for vias are drilled through the substrate using precision drilling equipment. The vias are then plated with conductive material, such as copper, to provide electrical connections between different layers of the substrate.
- Final Inspection and Testing: The fabricated substrate undergoes thorough inspection and testing to ensure that it meets the required specifications for dimensional accuracy, electrical connectivity, and mechanical integrity. Any defects or inconsistencies are identified and addressed before the substrate is used in electronic assembly.
By following these fabrication steps, manufacturers can produce ultrathin SIP package substrates with the precision and reliability necessary for high-performance electronic applications. Each step in the process requires careful control and quality assurance to ensure that the final substrate meets the demanding requirements of modern electronic devices.
How do you manufacture an Ultrathin SIP Package Substrate?
Manufacturing ultrathin SIP (System-in-Package) package substrates involves several intricate processes aimed at creating thin, multi-layered structures that provide electrical connectivity and mechanical support for electronic components. Here’s a detailed overview of the manufacturing process:
- Substrate Material Selection: Choose a substrate material suitable for the desired application, such as FR-4, polyimide, or liquid crystal polymer (LCP). The material should possess the required mechanical, electrical, and thermal properties.
- Cleaning and Surface Preparation: The substrate material undergoes thorough cleaning and surface treatment to remove any contaminants and ensure proper adhesion of subsequent layers.
- Layer Deposition: Thin layers of dielectric and conductive materials are deposited onto the substrate using techniques like physical vapor deposition (PVD), chemical vapor deposition (CVD), or electroplating. These layers form the insulating layers, conductive traces, and vias of the substrate.
- Photolithography: Photoresist material is applied to the substrate surface, and a photomask is used to define the desired patterns for the conductive traces and vias. The substrate is then exposed to UV light, transferring the pattern onto the photoresist layer.
- Etching: The exposed areas of the substrate are etched away using chemical etchants, leaving behind the patterned conductive traces and vias. Multiple etching steps may be required to create the desired layer structure.
- Surface Finishing: After etching, the substrate surface may undergo surface finishing processes such as chemical treatment or mechanical polishing to improve smoothness and remove contaminants.
- Lamination: If the substrate consists of multiple layers, they are assembled and laminated together using heat and pressure to form a single, cohesive structure. This process may involve bonding additional layers of dielectric material between the conductive layers to create a multilayer stack.
- Drilling and Plating: Precision drilling equipment is used to create holes for vias through the substrate. The vias are then plated with a conductive material, such as copper, to provide electrical connections between different layers of the substrate.
- Testing and Inspection: The manufactured substrate undergoes rigorous testing and inspection to ensure that it meets the required specifications for dimensional accuracy, electrical connectivity, and mechanical integrity. Any defects or inconsistencies are identified and addressed.
- Packaging and Shipping: Once the substrate passes inspection, it is packaged and prepared for shipping to electronic assembly facilities, where it will be integrated into electronic devices.
Throughout the manufacturing process, strict quality control measures are implemented to ensure consistency and reliability in the production of ultrathin SIP package substrates. Each step requires precision and attention to detail to meet the demanding requirements of modern electronic applications.
How much should an Ultrathin SIP Package Substrate cost?
The cost of ultrathin SIP (System-in-Package) package substrates can vary depending on several factors, including the materials used, manufacturing processes, design complexity, and required specifications. However, it’s worth noting that ultrathin SIP substrates typically involve specialized manufacturing techniques and materials, which can lead to higher costs compared to traditional package substrates.
Here are some factors that can influence the cost of ultrathin SIP package substrates:
- Material Cost: The cost of the substrate material itself can vary depending on factors such as material type (e.g., FR-4, polyimide, LCP), thickness, and quality. Advanced materials with specific properties, such as high thermal conductivity or superior electrical performance, may come at a premium.
- Manufacturing Processes: The fabrication processes involved in manufacturing ultrathin SIP substrates, such as deposition, etching, lamination, and plating, can require specialized equipment and expertise. These processes may incur higher labor and equipment costs, contributing to the overall substrate cost.
- Complexity of Design: Substrates with intricate designs, dense routing patterns, and multiple layers may require more advanced manufacturing techniques and longer processing times, leading to increased costs.
- Quality and Reliability Requirements: Meeting stringent quality and reliability standards, such as ISO certifications or specific industry requirements, may necessitate additional testing, inspection, and quality control measures, adding to the overall cost.
- Volume and Scale: The economies of scale play a significant role in determining substrate costs. Larger production volumes generally result in lower per-unit costs due to optimized manufacturing processes and bulk material purchasing.
- Customization and Special Features: Substrates with custom specifications, special features (e.g., embedded components, advanced interconnect technologies), or unique requirements may incur additional development and manufacturing costs.
- Market Demand and Competition: Market dynamics, supply chain factors, and competition among substrate manufacturers can also influence pricing. Fluctuations in material prices, technological advancements, and industry trends may impact substrate costs over time.
Given these factors, it’s challenging to provide a precise cost estimate for ultrathin SIP package substrates without specific details about the substrate’s design, materials, and manufacturing requirements. Generally, ultrathin SIP substrates tend to be more expensive than conventional substrates due to their specialized nature and advanced manufacturing processes.
What is the Ultrathin SIP Package Substrate base material?
The base material used for Ultrathin SIP (System-in-Package) package substrates can vary depending on the specific requirements of the application and manufacturing preferences. However, several common materials are frequently utilized in the fabrication of these substrates:
- FR-4 (Flame Retardant-4): FR-4 is a widely used epoxy-based laminate material reinforced with woven fiberglass cloth. It offers good mechanical strength, dimensional stability, and electrical insulation properties. While FR-4 is commonly used in standard PCBs (Printed Circuit Boards), it can also serve as a base material for ultrathin SIP substrates.
- Polyimide (PI): Polyimide is a flexible and heat-resistant polymer material that is well-suited for applications requiring high-temperature operation and flexibility. It offers excellent thermal stability, chemical resistance, and low outgassing properties. Polyimide-based substrates are often used in flexible and bendable electronic devices.
- Liquid Crystal Polymer (LCP): LCP is an advanced thermoplastic material known for its exceptional electrical performance, dimensional stability, and low moisture absorption. It offers high dielectric strength, low dissipation factor, and excellent signal integrity, making it suitable for high-frequency and high-speed applications. LCP-based substrates are commonly used in demanding electronic applications such as RF (Radio Frequency) and microwave systems.
- Ceramic: Ceramic substrates, such as alumina (Al2O3) or aluminum nitride (AlN), offer excellent thermal conductivity, mechanical strength, and chemical stability. They are well-suited for applications requiring high power handling capabilities and thermal management, such as power electronics and LED packaging.
The choice of base material depends on factors such as the electrical performance requirements, thermal management needs, flexibility, and cost considerations of the specific application. Additionally, hybrid substrates combining different materials or composite structures may be utilized to achieve desired performance characteristics.
Which company manufactures Ultrathin SIP Package Substrates?
Currently, there are many companies specialized in manufacturing Ultrathin SIP (System-in-Package) package substrates, with some of them leading the field. For example, prominent electronic materials and packaging technology companies like Mitsui Chemicals and Panasonic in Japan, as well as American companies like Freescale and Texas Instruments, have rich experience and technical expertise in the research and production of Ultrathin SIP substrates.
Our company is also one of the manufacturers of Ultrathin SIP package substrates. As a company focusing on electronic materials and packaging technology, we possess advanced manufacturing equipment, a professional technical team, and extensive industry experience. Our Ultrathin SIP package substrates have the following characteristics:
- Advanced Material Technology: We employ the latest material technology and advanced manufacturing processes to ensure that our Ultrathin SIP substrates exhibit excellent electrical, thermal, and mechanical performance.
- Customized Design: We can customize Ultrathin SIP package substrates according to the specific requirements of our customers, including designing complex routing, embedded components, and special interconnect technologies to meet the demands of different application scenarios.
- Strict Quality Control: We strictly adhere to quality management systems, controlling and inspecting each production process rigorously to ensure that our products meet the quality requirements and standards of our customers.
- Fast Delivery:With efficient production capacity and flexible scheduling, we can promptly fulfill customer orders and ensure timely delivery.
As a professional manufacturer of Ultrathin SIP package substrates, we are committed to providing high-quality, high-performance products and excellent services to our customers. Our goal is to be a trusted partner for our customers, working together to create a better future.
What are the qualities of good customer service?
Good customer service is characterized by several key qualities that ensure customers feel valued, satisfied, and supported throughout their interactions with a company. Here are some of the qualities:
- Responsive: Good customer service involves promptly addressing customer inquiries, concerns, and issues. Being responsive demonstrates attentiveness and a commitment to meeting customer needs in a timely manner.
- Empathetic: Empathy is crucial in understanding and relating to customers’ perspectives and emotions. Customer service representatives should demonstrate empathy by listening actively, showing understanding, and expressing genuine concern for customers’ experiences and challenges.
- Knowledgeable: Customer service staff should possess comprehensive knowledge about the company’s products, services, policies, and procedures. Being knowledgeable enables them to provide accurate information, answer questions effectively, and offer helpful guidance or solutions.
- Professionalism: Professionalism entails maintaining a courteous, respectful, and professional demeanor in all interactions with customers. This includes using appropriate language, tone, and behavior, as well as adhering to company guidelines and standards.
- Effective Communication: Good customer service relies on clear and concise communication. Customer service representatives should communicate information effectively, listen actively to customers’ concerns, and ensure mutual understanding through active dialogue.
- Problem-solving Skills: Effective problem-solving skills are essential for addressing customer issues and resolving conflicts satisfactorily. Customer service representatives should be proactive in identifying solutions, taking ownership of problems, and following through until resolution is achieved.
- Flexibility: Flexibility involves adapting to customers’ unique needs and circumstances. Good customer service requires flexibility in accommodating special requests, finding creative solutions to challenges, and being open to feedback or suggestions for improvement.
- Consistency:Consistency in service delivery is vital for building trust and confidence with customers. Providing consistent levels of service quality, responsiveness, and support across all interactions and touchpoints reinforces the company’s reliability and credibility.
- Follow-up: Following up with customers after resolving an issue or completing a transaction demonstrates commitment to customer satisfaction. Follow-up communication can include checking in on customer satisfaction, providing additional assistance or resources, or seeking feedback for continuous improvement.
- Customer-centric Approach: Ultimately, good customer service revolves around prioritizing the needs and interests of customers. Adopting a customer-centric approach means placing emphasis on delivering positive experiences, building relationships, and fostering long-term loyalty and advocacy.
By embodying these qualities, companies can cultivate a reputation for providing exceptional customer service and foster positive relationships with their customers.
FAQs
What are Ultrathin SIP Package Substrates?
Ultrathin SIP Package Substrates are thin, multi-layered structures used in electronic packaging to mount and interconnect various components within a compact package. They enable miniaturization and integration of electronic devices, especially in applications where space is limited.
What materials are used in Ultrathin SIP Package Substrates?
Common materials used in Ultrathin SIP Package Substrates include FR-4, polyimide, and liquid crystal polymer (LCP). These materials offer different properties such as flexibility, thermal conductivity, and electrical performance to suit various application requirements.
What are the advantages of Ultrathin SIP Package Substrates?
Ultrathin SIP Package Substrates offer advantages such as reduced size and weight, improved thermal management, enhanced signal integrity, and increased design flexibility. They enable the development of smaller and more efficient electronic devices.
What types of electronic components can be mounted on Ultrathin SIP Package Substrates?
Various electronic components can be mounted on Ultrathin SIP Package Substrates, including integrated circuits (ICs), microprocessors, memory chips, sensors, and passive components like resistors and capacitors.
What manufacturing processes are involved in producing Ultrathin SIP Package Substrates?
The manufacturing processes for Ultrathin SIP Package Substrates typically include layer deposition, photolithography, etching, lamination, drilling, plating, and surface finishing. These processes create the thin, multi-layered structure required for electronic packaging.
What applications are Ultrathin SIP Package Substrates used in?
Ultrathin SIP Package Substrates find applications in various industries, including consumer electronics, telecommunications, automotive, aerospace, medical devices, and IoT (Internet of Things) devices. They are particularly suitable for portable devices, wearables, and miniaturized electronic systems.
How can I choose the right Ultrathin SIP Package Substrate for my application?
Choosing the right Ultrathin SIP Package Substrate involves considering factors such as material properties, electrical performance, thermal characteristics, design flexibility, and cost. Consulting with substrate manufacturers or experts in electronic packaging can help in selecting the most suitable substrate for specific application requirements.