Ultrathin RF Substrates Manufacturer
Ultrathin RF Substrates Manufacturer,Ultrathin RF Substrates are specialized materials designed for high-frequency applications requiring minimal thickness while ensuring optimal signal performance. These substrates are engineered to support the complex circuitry of RF (Radio Frequency) systems, such as in telecommunications, radar, and satellite communication. Their ultrathin profile allows for reduced signal loss and enhanced signal integrity, crucial for maintaining high performance in compact and space-constrained environments. Typically made from advanced materials like low-loss ceramics or high-frequency laminates, ultrathin RF substrates provide superior electrical characteristics and thermal stability, making them essential for cutting-edge RF technology and high-speed electronic devices.
What is Ultrathin RF Substrate?
Ultrathin RF substrates are specialized printed circuit board (PCB) materials designed to handle high-frequency signals with minimal signal loss and interference. These substrates are characterized by their exceptionally thin profiles, often in the range of a few hundred micrometers or less, which is significantly thinner than conventional PCBs.
The primary purpose of ultrathin RF substrates is to support the performance of high-frequency and high-speed electronic devices, such as those used in radio frequency (RF) applications, including smartphones, wireless communication devices, and radar systems. The thinness of these substrates helps in achieving better signal integrity by reducing the distance signals must travel, thereby minimizing signal attenuation and phase distortion.
These substrates are typically made from advanced materials such as low-loss ceramics or high-frequency laminates, which offer high dielectric constants and low loss tangents. This allows them to effectively support the rapid transmission of high-frequency signals. Additionally, their thin profiles contribute to the miniaturization of electronic devices, enabling the design of compact and lightweight RF components.
Ultrathin RF substrates are also essential for applications requiring high-density interconnections and high performance in constrained spaces. They play a crucial role in enabling the development of next-generation electronic devices by providing the necessary performance and reliability in compact, high-frequency circuits. Their advanced material properties and design make them ideal for maintaining signal integrity and enhancing overall system performance in demanding RF environments.
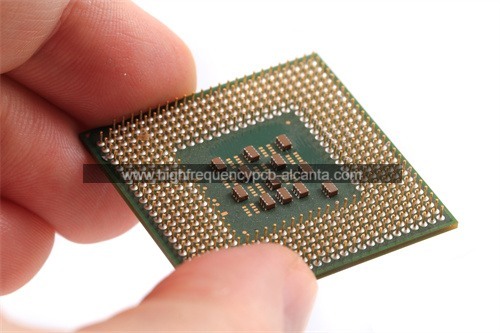
Ultrathin RF Substrates Manufacturer
What are the Design Guidelines for Ultrathin RF Substrates?
Designing ultrathin RF substrates requires careful consideration of several factors to ensure optimal performance and reliability in high-frequency applications. Here are some key design guidelines:
- Material Selection: Choose materials with low dielectric loss and high dielectric constant, such as specialized ceramics or advanced laminates. These materials minimize signal attenuation and maintain signal integrity over high frequencies. Ensure the material has a stable dielectric constant across the frequency range of interest.
- Substrate Thickness: Maintain a consistent and precise substrate thickness to ensure uniform electrical performance. Ultrathin substrates typically have thicknesses in the range of a few hundred micrometers or less, which necessitates tight manufacturing tolerances.
- Impedance Control: Design trace widths and spacing to match the characteristic impedance required for the RF application. Use advanced simulation tools to accurately model and control impedance, as deviations can lead to signal reflections and loss.
- Thermal Management: Consider thermal management solutions to address heat dissipation in high-frequency applications. Ultrathin substrates can be more susceptible to thermal issues, so integrating thermal vias or heat spreaders may be necessary.
- Signal Integrity:Implement proper grounding and shielding techniques to minimize electromagnetic interference (EMI) and cross-talk between signal traces. Use multi-layer designs with well-planned ground planes to ensure stable signal performance.
- Manufacturing Precision: Ensure high precision in manufacturing processes, such as etching and drilling, to avoid defects and ensure the reliability of the thin substrates. Quality control measures should be stringent to detect any deviations early.
- Mechanical Stability: Despite their thinness, ultrathin RF substrates must retain mechanical stability. Design for adequate support and handling during assembly to prevent warping or damage.
- Thermal Coefficient Matching: Match the thermal expansion coefficients of the substrate material with those of other components to avoid stress and potential failure due to thermal cycling.
- Design for Testability: Incorporate test points and measurement structures to facilitate the testing and validation of RF performance during the design and manufacturing stages.
By adhering to these guidelines, designers can effectively leverage ultrathin RF substrates to create high-performance, reliable, and compact RF components for advanced electronic systems.
What is the Fabrication Process for Ultrathin RF Substrates?
The fabrication process for ultrathin RF substrates involves several key steps designed to achieve the required thinness and performance characteristics while maintaining high precision. Here’s an overview of the typical process:
- Material Selection and Preparation: Begin with the selection of suitable base materials, such as low-loss ceramics or high-frequency laminates, that meet the required dielectric properties for RF applications. The raw materials are prepared and processed to form thin, uniform sheets or foils.
- Lamination: The chosen material is laminated into thin layers. This process involves applying heat and pressure to bond the layers together, ensuring a uniform thickness across the substrate. In some cases, a pre-preg material (a partially cured resin) may be used for lamination.
- Patterning: Apply a photolithographic process to create the necessary circuit patterns on the substrate. This involves coating the substrate with a light-sensitive photoresist, exposing it to UV light through a mask that defines the circuit layout, and then developing the photoresist to reveal the pattern.
- Etching: After patterning, use etching techniques to remove the unwanted copper or other conductive material from the exposed areas of the substrate. This step is critical for defining the circuit traces and components on the substrate.
- Drilling and Via Formation: Drill precision holes to create vias (vertical interconnections) between different layers or to connect components. For ultrathin substrates, this step requires high accuracy to avoid damaging the thin material.
- Plating: Apply a thin layer of metal, typically copper, to the drilled vias and the surface of the substrate. This step is essential for ensuring good electrical connectivity and mechanical stability.
- Layer Bonding (for Multilayer Designs): If the substrate design requires multiple layers, bond these layers together using additional lamination steps. Ensure that the alignment and bonding are precise to maintain electrical performance and structural integrity.
- Finishing: Perform final processing steps, such as cleaning, surface treatment, and applying protective coatings if necessary. These steps help to enhance the durability and reliability of the ultrathin RF substrate.
- Testing and Inspection: Conduct thorough testing and inspection to verify the performance and quality of the substrate. This includes checking electrical performance, dimensional accuracy, and mechanical properties to ensure compliance with design specifications.
- Cutting and Packaging: Finally, cut the finished substrates into the required sizes and package them for delivery. Proper handling and packaging are crucial to prevent damage during transportation and ensure the substrates arrive in optimal condition.
By carefully managing each step in this fabrication process, manufacturers can produce high-quality ultrathin RF substrates that meet the stringent requirements of high-frequency electronic applications.
How Do You Manufacture Ultrathin RF Substrates?
Manufacturing ultrathin RF substrates involves a series of precise and specialized steps to produce high-performance, thin substrates suitable for high-frequency applications. Here’s a detailed overview of the typical manufacturing process:
- Material Selection and Preparation: Choose high-quality base materials like low-loss ceramics or advanced laminates with desirable dielectric properties for RF applications. Prepare the materials in thin, uniform sheets or foils. Material selection is crucial for achieving the necessary performance and maintaining consistency in substrate thickness.
- Lamination: Laminate the base material into thin layers using a combination of heat and pressure. This process ensures that the layers bond together uniformly. In some cases, a pre-preg resin may be used to facilitate the lamination process. Control the lamination parameters carefully to achieve the required thickness and avoid defects.
- Patterning: Apply a photolithographic process to create the circuit patterns. Start by coating the substrate with a light-sensitive photoresist layer. Expose the photoresist to UV light through a mask that defines the circuit layout. Develop the photoresist to reveal the pattern, which will guide subsequent etching.
- Etching: Use chemical etching techniques to remove unwanted conductive material from the substrate’s surface. This step defines the circuit traces and features. Precision is critical to ensure accurate patterning and to prevent damage to the thin substrate.
- Drilling and Via Formation: Drill precise holes to form vias that connect different layers or components. This step is performed with high accuracy to avoid compromising the integrity of the thin substrate. Special drilling equipment and techniques are used to manage the challenges associated with thin materials.
- Plating: Apply a thin layer of metal, such as copper, to the surface and into the vias. This process is crucial for creating electrical connections and providing mechanical stability. Electroplating or other plating techniques are employed to deposit the metal evenly and precisely.
- Layer Bonding (for Multilayer Designs): If the design requires multiple layers, bond them together through additional lamination processes. Ensure precise alignment and bonding to maintain electrical performance and structural integrity. Multilayer bonding must be managed carefully to prevent delamination or misalignment.
- Finishing: Perform finishing operations to enhance the substrate’s durability and performance. This may include cleaning, surface treatments, and applying protective coatings. These steps help improve the substrate’s resistance to environmental factors and ensure long-term reliability.
- Testing and Quality Control: Conduct rigorous testing and quality control to verify that the ultrathin RF substrates meet design specifications. This includes electrical performance tests, dimensional checks, and mechanical inspections. Ensure that each substrate complies with the required standards for high-frequency applications.
- Cutting and Packaging: Cut the finished substrates to the desired sizes and package them for shipment. Proper handling and packaging are essential to protect the delicate ultrathin substrates from damage during transportation.
Each step in the manufacturing process is carefully controlled to produce high-quality ultrathin RF substrates that meet the demanding requirements of high-frequency and high-speed electronic applications.
How Much Should Ultrathin RF Substrates Cost?
The cost of ultrathin RF substrates can vary widely depending on several factors, including material type, substrate thickness, complexity of the design, and volume of production. Here are some key elements that influence the cost:
- Material Costs: High-frequency and low-loss materials, such as advanced ceramics or specialized laminates, generally cost more than standard PCB materials. The price of these materials can significantly impact the overall cost of the substrates.
- Thickness and Precision: Ultrathin RF substrates require precise manufacturing processes and tighter tolerances, which can increase production costs. The thinner the substrate, the more challenging and costly it is to fabricate.
- Design Complexity: More complex designs, such as multilayer configurations or substrates with intricate patterns and vias, will typically incur higher costs due to the increased processing time and complexity.
- Production Volume: Costs can vary based on the production volume. High-volume orders often benefit from economies of scale, which can lower the per-unit cost. Conversely, low-volume or prototype orders may have higher per-unit costs due to setup and tooling expenses.
- Manufacturing and Processing: The fabrication process for ultrathin RF substrates involves advanced techniques, including precise photolithography, etching, and plating. The cost of these processes can contribute to the overall expense.
- Testing and Quality Control: Rigorous testing and quality control are essential for ensuring the performance and reliability of ultrathin RF substrates. The cost of these procedures can be a significant factor, especially for high-frequency applications that demand high precision.
- Customization and Additional Features: Custom features, such as specific surface finishes, specialized coatings, or additional mechanical properties, can add to the cost.
As a rough estimate, ultrathin RF substrates can range from $100 to $500 or more per square meter, depending on the factors mentioned above. For highly specialized or low-volume applications, costs may be higher. It is advisable to consult with substrate manufacturers to get precise quotes based on specific requirements and project details.
What is the Base Material for Ultrathin RF Substrates?
The base material for ultrathin RF substrates plays a critical role in ensuring high-frequency performance and reliability. The choice of material influences the substrate’s dielectric properties, thermal management, and overall performance. Here’s a detailed overview of common base materials used for ultrathin RF substrates:
- Low-Loss Ceramics: Ceramics such as alumina (Al2O3), barium titanate (BaTiO3), and various proprietary ceramic blends are commonly used for ultrathin RF substrates. These materials offer low dielectric loss, high dielectric constant, and excellent thermal stability. Their inherent properties make them suitable for high-frequency and high-power applications.
- High-Frequency Laminates: Advanced laminate materials, such as those made from polytetrafluoroethylene (PTFE) composites (e.g., Rogers RO3000 or RO4000 series), are often used. These laminates have low dielectric loss and are designed specifically for high-frequency applications. They provide good electrical performance and can be manufactured in thin profiles.
- Polyimide Films: Polyimide-based materials, such as Kapton, are known for their high thermal stability and low dielectric loss. Polyimide films can be used as a base material for ultrathin substrates due to their flexibility and high-performance characteristics.
- Epoxy Glass Laminates:For applications requiring a balance between cost and performance, epoxy glass laminates can be used. These materials offer reasonable dielectric properties and are often used in less demanding RF applications. They can be processed into thin forms, although they might not offer the same level of performance as ceramics or high-frequency laminates.
- Hybrid Materials: In some cases, hybrid materials combining different substrates or layers may be used to achieve specific performance characteristics. These composites can offer enhanced properties tailored to particular applications.
- Metal-Backed Materials: For thermal management and additional mechanical support, some ultrathin RF substrates incorporate metal backing layers, such as copper or aluminum. These metals help dissipate heat and provide structural support, which is important in high-power RF applications.
When selecting the base material for ultrathin RF substrates, factors such as dielectric constant, loss tangent, thermal conductivity, and mechanical properties must be considered to meet the specific requirements of the application. Each material offers distinct advantages, and the choice will depend on the performance needs and design constraints of the RF system.
Which Company Makes Ultrathin RF Substrates?
Several companies manufacture ultrathin RF substrates, offering high-performance solutions for high-frequency electronic applications. Here are some notable companies and their characteristics:
- Rogers Corporation: Rogers is a leading provider of high-frequency materials, known especially for their RO4000 and RO3000 series. Although they primarily offer thicker substrates, Rogers’ technologies and materials are also suitable for producing ultrathin RF substrates.
- Taconic: Taconic offers a range of high-performance PCB materials, including those suitable for ultrathin RF substrates. Their products are known for excellent electrical performance and mechanical stability.
- Arlon Electronic Materials: Arlon manufactures high-frequency PCB materials such as ARLON 25N and ARLON 85N, widely used in RF and microwave applications. Their materials can be processed into ultrathin substrates to meet the needs of high-frequency electronic devices.
- Isola Group:Isola provides various high-frequency PCB materials capable of meeting the requirements for high-performance ultrathin RF substrates. Their materials feature low dielectric loss and stable electrical performance.
- Dielectric Laboratories: Dielectric Laboratories focuses on the development and manufacture of high-frequency PCB materials. Their materials can be used to produce ultrathin RF substrates, offering excellent electrical performance and stability.
- Laird Performance Materials: Laird produces a range of high-frequency PCB materials, including those used for manufacturing ultrathin RF substrates. Their materials are widely used in communication and electronic devices.
Our company also manufactures ultrathin RF substrates. Our ultrathin RF substrates are designed for high-frequency applications, featuring exceptional electrical performance and mechanical stability. We use advanced manufacturing technologies and high-quality materials to ensure that each substrate meets rigorous performance standards.
Our production process includes precision photolithography, etching, plating, and lamination to achieve the ultrathin characteristics and high-frequency stability of the substrates.
The ultrathin RF substrates we offer are suitable for various high-frequency electronic applications, including wireless communications, radar systems, and high-frequency microwave devices. We can customize substrates with different thicknesses, materials, and designs according to specific customer requirements, addressing a range of application scenarios. Our engineering team is dedicated to providing technical support and optimization solutions to ensure the success of each project.
If you have any needs or questions about ultrathin RF substrates, please feel free to contact us. We are committed to providing solutions tailored to your needs.
What are the 7 Qualities of Good Customer Service?
Good customer service is crucial for building strong relationships with clients and ensuring their satisfaction. Here are seven essential qualities of good customer service:
- Responsiveness: Quickly addressing customer inquiries and issues is key to providing excellent service. Being responsive demonstrates that you value the customer’s time and are committed to resolving their concerns efficiently.
- Empathy:Understanding and empathizing with the customer’s situation helps build trust and rapport. Showing genuine concern for their needs and emotions can lead to a more positive and personalized experience.
- Communication Skills: Clear, concise, and effective communication is vital. This includes listening actively, providing accurate information, and explaining solutions in a way that is easy for the customer to understand.
- Knowledge and Expertise:Providing knowledgeable and accurate answers to customer questions requires a deep understanding of the products or services offered. Expertise helps in resolving issues effectively and builds credibility with the customer.
- Patience:Handling customers with patience, especially in challenging situations, helps in managing stress and defusing potential conflicts. A calm and composed approach reassures customers and fosters a positive interaction.
- Attentiveness: Paying close attention to customer needs and details ensures that their concerns are fully understood and addressed. This includes following up on promises and ensuring that no aspect of the customer’s issue is overlooked.
- Positive Attitude: Maintaining a friendly and positive demeanor, even in difficult situations, creates a welcoming environment. A positive attitude helps in creating a pleasant experience and encourages customer loyalty.
By embodying these qualities, businesses can enhance customer satisfaction, build lasting relationships, and foster a reputation for exceptional service.
FAQs about Ultrathin RF Substrates
What is the difference between Ultrathin RF Substrates and standard PCBs?
Ultrathin RF Substrates are designed for high-frequency applications, offering better performance at high frequencies compared to standard PCBs.
How do I choose the right Ultrathin RF Substrate material?
Consider factors like dielectric loss, permittivity, and thermal management when selecting the material for your specific application.
Can Ultrathin RF Substrates be used in high-temperature environments?
Yes, but ensure the material you choose is rated for high temperatures and has appropriate thermal management properties.
What are common applications for Ultrathin RF Substrates?
They are commonly used in RF communication devices, microwave circuits, antennas, and other high-frequency electronic systems.
Where can I purchase ultrathin RF substrates?
Ultrathin RF substrates can be purchased from specialized PCB manufacturers and suppliers who offer high-frequency and advanced substrate materials. Consulting with manufacturers for customized solutions and technical support is also recommended.