Ultrathin PCB manufacturing
Ultrathin PCB Manufacturing,Ultrathin PCBs, or Printed Circuit Boards, represent a technological marvel in the realm of electronics. These remarkably thin substrates, typically measuring less than 0.4mm in thickness, have revolutionized the design and functionality of modern electronic devices. Characterized by their lightweight and compact form factors, ultrathin PCBs find widespread applications in smartphones, tablets, wearable gadgets, medical equipment, and aerospace technology.
Crafted from specialized materials such as polyimide (PI) or liquid crystal polymer (LCP), ultrathin PCBs offer exceptional flexibility, thermal stability, and electrical performance. Their reduced thickness enables manufacturers to create sleek and lightweight devices without compromising on functionality or durability. Despite their delicate appearance, ultrathin PCBs undergo rigorous manufacturing processes to ensure reliability, including precision lamination, controlled copper cladding, and meticulous assembly techniques.
In an era where miniaturization and portability are paramount, ultrathin PCBs play a pivotal role in pushing the boundaries of innovation, allowing engineers and designers to create cutting-edge electronics that seamlessly integrate into our daily lives.
What is an Ultrathin PCB?
An Ultrathin PCB (Printed Circuit Board) refers to a type of PCB that is exceptionally thin compared to standard PCBs. These boards are typically designed for applications where space is at a premium or where weight reduction is critical. Ultrathin PCBs are commonly used in various electronic devices such as smartphones, tablets, wearable devices, and medical devices.
The thickness of an Ultrathin PCB can vary depending on the specific application requirements, but they are generally defined as having a thickness of less than 0.4mm. Some Ultrathin PCBs can be as thin as 0.1mm or even less.
Designing and manufacturing Ultrathin PCBs require special techniques and materials to ensure the board’s integrity and reliability despite its reduced thickness. These techniques may include the use of thinner copper layers, special laminates, advanced surface finishes, and precise manufacturing processes.
Ultrathin PCBs offer advantages such as reduced weight, smaller form factors, and improved flexibility, making them ideal for applications where space and weight are critical considerations. However, they also present challenges in terms of handling, assembly, and durability, requiring careful design and manufacturing processes to ensure proper functionality and reliability.
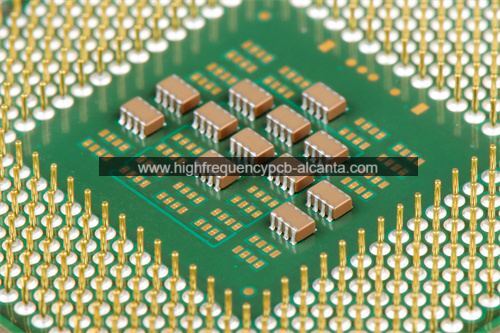
Ultrathin PCB Manufacturing
What are Ultrathin PCB Design Guidelines?
Ultrathin PCB design guidelines are a set of principles and recommendations aimed at ensuring the successful design and manufacture of PCBs with extremely thin profiles. Here are some common guidelines for designing ultrathin PCBs:
- Material Selection: Choose materials suitable for ultrathin PCBs, including thin laminates with high dielectric strength and low thermal expansion coefficients.
- Layer Thickness: Keep the copper layer thickness minimal to reduce overall thickness while maintaining electrical conductivity requirements.
- Minimum Trace Width and Spacing: Design traces and spaces to be as narrow as possible while still meeting electrical and manufacturing tolerances. However, ensure that the design allows for proper etching and plating processes.
- Via Placement and Size: Optimize via placement and size to minimize signal distortion and ensure proper electrical connections while considering the thinness of the PCB substrate.
- Component Placement: Carefully plan component placement to maximize space utilization and minimize signal interference. Consider the potential impact of heat dissipation on components due to the reduced thickness of the PCB.
- Flexibility and Bending Considerations: If the ultrathin PCB needs to be flexible or bendable, design it with appropriate materials and geometries to withstand bending without compromising electrical integrity.
- Surface Finish: Choose surface finishes suitable for ultrathin PCBs, considering factors such as solderability, flatness, and compatibility with assembly processes.
- Stack-up Design: Design the PCB stack-up with consideration for signal integrity, impedance control, and thermal management while accommodating the thinness of the PCB.
- Thermal Management: Implement thermal management techniques such as heat sinks, thermal vias, and copper pours to dissipate heat effectively, especially in densely packed designs.
- Testing and Inspection: Develop testing and inspection procedures specific to ultrathin PCBs to ensure quality and reliability, considering the challenges associated with their reduced thickness.
By following these guidelines, designers can create ultrathin PCBs that meet the requirements of their specific applications while maintaining reliability and performance. Additionally, collaboration with PCB manufacturers early in the design process can help address manufacturing challenges and optimize the design for efficient production.
What is the Ultrathin PCB Fabrication Process?
The fabrication process for ultrathin PCBs involves several stages, including design, material selection, fabrication, and testing. Here’s a general overview of the fabrication process:
- Design: The design phase involves creating the layout of the PCB, including component placement, routing of traces, and defining the stack-up configuration. Design software is used to create the PCB layout, ensuring that it meets the requirements of the specific application and adheres to ultrathin PCB design guidelines.
- Material Selection: Selecting appropriate materials is crucial for ultrathin PCB fabrication. Thin laminates with high dielectric strength and low thermal expansion coefficients are typically chosen to achieve the desired thinness while maintaining mechanical and electrical properties. Copper foil with reduced thickness may also be selected to minimize the overall thickness of the PCB.
- Preparation of Substrate: The selected substrate material is prepared by cleaning and smoothing its surface to ensure proper adhesion of the copper foil and other layers during the lamination process.
- Copper Cladding: Thin copper foil is laminated onto the substrate surface using heat and pressure. The copper foil is etched to remove excess copper and define the traces and pads according to the PCB design.
- Layer Lamination: Multiple layers of substrate and copper foil are laminated together to form the multilayer structure of the PCB. Each layer is carefully aligned to ensure proper registration of the circuitry.
- Drilling: Small holes called vias are drilled into the PCB to establish electrical connections between different layers. Microvia drilling techniques may be used to create extremely small vias suitable for ultrathin PCBs.
- Through-hole Plating: After drilling, the vias are plated with conductive material to establish electrical continuity between the layers.
- Surface Finishing: Surface finishes such as immersion gold, immersion silver, or organic solderability preservatives (OSP) are applied to protect exposed copper surfaces and improve solderability.
- Etching and Masking: Unwanted copper is etched away from the PCB using chemical processes, leaving behind the desired circuit traces and pads. A solder mask is applied to protect the exposed copper and define areas for soldering components.
- Final Inspection and Testing: The completed ultrathin PCB undergoes thorough inspection and testing to ensure that it meets the specified electrical and mechanical requirements. Testing may include checks for continuity, impedance, and dimensional accuracy.
By following these steps and employing specialized techniques for handling thin materials, manufacturers can produce ultrathin PCBs that meet the stringent requirements of modern electronic devices.
How do you manufacture Ultrathin PCBs?
Manufacturing ultrathin PCBs involves specialized processes and careful handling of thin materials to ensure the integrity and reliability of the final product. Here’s a step-by-step overview of how ultrathin PCBs are manufactured:
- Design: The process begins with the design of the PCB layout using computer-aided design (CAD) software. Designers take into account the specific requirements of the application, such as size, shape, and electrical characteristics, while adhering to ultrathin PCB design guidelines.
- Material Selection: Ultrathin PCBs require specialized materials that can provide the necessary electrical and mechanical properties while maintaining a thin profile. This includes selecting thin laminates with high dielectric strength and low thermal expansion coefficients, as well as thin copper foils for the conductive layers.
- Substrate Preparation: The selected substrate material is prepared by cleaning and smoothing its surface to ensure proper adhesion of the copper foil and other layers during lamination.
- Copper Cladding: Thin copper foil is laminated onto the substrate surface using heat and pressure. The thickness of the copper foil is carefully controlled to achieve the desired conductivity while minimizing the overall thickness of the PCB.
- Layer Lamination: Multiple layers of substrate and copper foil are laminated together to form the multilayer structure of the PCB. Each layer is aligned and bonded together using heat and pressure to ensure proper registration of the circuitry.
- Drilling: Small holes called vias are drilled into the PCB to establish electrical connections between different layers. Specialized drilling techniques may be used to create extremely small vias suitable for ultrathin PCBs.
- Through-hole Plating: After drilling, the vias are plated with conductive material to establish electrical continuity between the layers. This is typically done using electroplating processes.
- Etching and Masking: Unwanted copper is etched away from the PCB using chemical processes, leaving behind the desired circuit traces and pads. A solder mask is applied to protect the exposed copper and define areas for soldering components.
- Surface Finishing: Surface finishes such as immersion gold, immersion silver, or organic solderability preservatives (OSP) are applied to protect exposed copper surfaces and improve solderability.
- Final Inspection and Testing: The completed ultrathin PCB undergoes thorough inspection and testing to ensure that it meets the specified electrical and mechanical requirements. This may include checks for continuity, impedance, and dimensional accuracy.
By following these steps and utilizing specialized equipment and techniques, manufacturers can produce ultrathin PCBs that meet the demanding requirements of modern electronic devices.
How much should Ultrathin PCBs cost?
The cost of ultrathin PCBs can vary depending on several factors, including the complexity of the design, the number of layers, the materials used, the manufacturing processes involved, and the quantity ordered. Generally, ultrathin PCBs tend to be more expensive than standard PCBs due to the specialized materials and manufacturing techniques required.
Here are some factors that can influence the cost of ultrathin PCBs:
- Material Cost: Thin laminates and copper foils used in ultrathin PCBs may be more expensive than standard materials.
- Manufacturing Processes: Specialized processes such as thin copper cladding, microvia drilling, and precision etching may increase manufacturing costs.
- Layer Count: Ultrathin PCBs with multiple layers will generally cost more than single or double-sided PCBs due to the additional manufacturing complexity.
- Quality and Reliability Requirements: Meeting high-quality standards and reliability requirements may necessitate additional testing and inspection procedures, which can increase costs.
- Order Quantity: Larger order quantities often result in lower per-unit costs due to economies of scale. However, ultrathin PCBs may have higher minimum order quantities due to the specialized manufacturing processes involved.
- Lead Time: Expedited production schedules or shorter lead times may incur additional costs.
As a rough estimate, the cost of ultrathin PCBs can range from a few dollars to several tens or even hundreds of dollars per square inch, depending on the factors mentioned above. For accurate pricing, it’s best to consult with PCB manufacturers or suppliers, providing them with detailed specifications of the required ultrathin PCBs. They can then provide a customized quote based on the specific requirements of the project.
What is Ultrathin PCB base material?
The choice of base material for ultrathin PCBs is critical for ensuring the desired mechanical and electrical properties while maintaining a thin profile. Some common base materials used for ultrathin PCBs include:
- Polyimide (PI): Polyimide is a popular choice for ultrathin PCBs due to its excellent thermal stability, flexibility, and low dielectric constant. It can withstand high temperatures, making it suitable for applications with demanding thermal requirements. Polyimide-based PCBs are often used in flexible circuits and applications where weight and space are critical.
- Liquid Crystal Polymer (LCP): LCP is another material commonly used for ultrathin PCBs. It offers excellent electrical performance, low moisture absorption, and high thermal stability. LCP-based PCBs are often used in high-frequency applications, such as RF/microwave circuits and antennas, where signal integrity is critical.
- Rogers Ultralam 2000/XT/XTD: Rogers Ultralam is a series of laminates specifically designed for ultrathin PCB applications. These laminates offer low dielectric constant and low loss characteristics, making them suitable for high-speed digital and RF/microwave circuits.
- Flexible Copper Clad Laminate (FCCL): FCCL consists of a thin layer of copper laminated between layers of flexible substrate material, such as polyimide or LCP. It offers excellent flexibility and bendability, making it ideal for flexible and bendable ultrathin PCBs used in wearable devices and other flexible electronics applications.
- Thinner Variants of Standard Substrates: Some manufacturers offer thinner variants of standard PCB substrates, such as FR-4, for ultrathin PCB applications. These substrates may be suitable for less demanding applications where flexibility and thermal stability are not critical requirements.
When selecting a base material for ultrathin PCBs, it’s essential to consider factors such as mechanical flexibility, thermal performance, electrical properties, and compatibility with manufacturing processes. Additionally, collaborating with experienced PCB manufacturers or material suppliers can help ensure the chosen material meets the specific requirements of the application.
Which company makes Ultrathin PCBs?
There are many companies specialized in manufacturing Ultrathin PCBs (Printed Circuit Boards), some of the well-known manufacturers include Taiwan’s Rigid PCB, Taiwan’s Flexium Interconnect, and the United States’ Multek. These companies have rich experience and technology in the field of Ultrathin PCBs and can provide high-quality Ultrathin PCB solutions for various applications.
Our company also manufactures Ultrathin PCBs. We have advanced manufacturing equipment and technology, as well as an experienced team of engineers, capable of meeting customers’ customized requirements while ensuring product quality and reliability. Our manufacturing process strictly follows international standards, from material selection to production processing, all carefully designed and strictly controlled to produce Ultrathin PCBs that meet customer requirements.
We can produce single-sided, double-sided, and multilayer Ultrathin PCBs suitable for various applications such as smartphones, tablets, wearable devices, medical equipment, etc. We can also provide Ultrathin PCB solutions with different materials, thicknesses, layers, and special processes according to customer requirements, and offer customized services to meet specific needs and application scenarios.
With strong production capacity, we can meet the needs of large-scale orders, and we also attach great importance to small-batch orders and sample orders, providing flexible production solutions for customers. Whether it is mass production or customized production, we are committed to providing customers with high-quality, high-performance Ultrathin PCB products, promoting the development and application of electronic technology together with customers.
What are the 7 qualities of good customer service?
Good customer service is characterized by several key qualities that help build positive relationships with customers and ensure their satisfaction. Here are seven qualities of good customer service:
- Responsiveness: A good customer service team is responsive to customers’ needs and inquiries in a timely manner. This includes promptly answering phone calls, emails, and messages, as well as addressing customer concerns or complaints without delay.
- Empathy: Empathy is essential for understanding customers’ perspectives and feelings. Good customer service representatives listen attentively to customers, show genuine concern for their issues, and strive to empathize with their situations, fostering a sense of trust and rapport.
- Professionalism: Good customer service is delivered with professionalism and courtesy. Representatives should maintain a positive and respectful demeanor at all times, regardless of the nature of the customer interaction, and adhere to company policies and standards.
- Knowledgeability: Customers expect to receive accurate and helpful information from customer service representatives. Therefore, good customer service teams possess thorough knowledge about the company’s products or services, policies, procedures, and industry trends, enabling them to provide relevant assistance and guidance to customers.
- Problem-solving skills: Effective problem-solving is a crucial aspect of good customer service. Representatives should be equipped with strong analytical and problem-solving skills to identify root causes of issues, propose appropriate solutions, and follow through until the customer’s concerns are resolved satisfactorily.
- Consistency: Consistency in service delivery is key to building trust and loyalty with customers. Good customer service teams strive to maintain consistent standards of service across all channels and interactions, ensuring that every customer receives a consistently positive experience.
- Proactivity: Good customer service goes beyond merely reacting to customer inquiries or issues; it also involves being proactive in anticipating and addressing customers’ needs. Proactive customer service involves reaching out to customers to offer assistance, providing relevant information or recommendations before customers ask, and actively seeking feedback to improve the overall customer experience.
By embodying these qualities, companies can deliver exceptional customer service that not only meets but exceeds customers’ expectations, leading to increased satisfaction, loyalty, and advocacy.
FAQs (Frequently Asked Questions)
What are ultrathin PCBs?
Ultrathin PCBs are printed circuit boards with exceptionally thin profiles, typically less than 0.4mm in thickness. They are designed for applications where space and weight are critical, such as smartphones, wearable devices, and medical equipment.
What materials are used to make ultrathin PCBs?
Common materials used for ultrathin PCBs include polyimide (PI), liquid crystal polymer (LCP), and thinner variants of standard substrates. These materials offer flexibility, thermal stability, and low dielectric constants suitable for ultrathin applications.
What are the advantages of ultrathin PCBs?
Ultrathin PCBs offer advantages such as reduced weight, smaller form factors, improved flexibility, and enhanced thermal management. They enable the design of compact and lightweight electronic devices with high performance.
What are the challenges in manufacturing ultrathin PCBs?
Manufacturing ultrathin PCBs poses challenges such as handling delicate materials, ensuring proper adhesion and lamination, controlling thickness variations, and maintaining reliability despite the reduced thickness.
How are ultrathin PCBs different from standard PCBs?
Ultrathin PCBs differ from standard PCBs primarily in their thickness and the materials used. Ultrathin PCBs are significantly thinner and often use specialized materials to achieve the desired mechanical and electrical properties.
What are some applications of ultrathin PCBs?
Ultrathin PCBs are used in a wide range of applications, including smartphones, tablets, wearable devices, medical equipment, aerospace and defense systems, automotive electronics, and IoT devices.
What factors should be considered when designing ultrathin PCBs?
When designing ultrathin PCBs, factors such as material selection, layer thickness, trace width and spacing, component placement, flexibility, thermal management, and manufacturing processes must be carefully considered to ensure proper functionality and reliability.
Are there any special considerations for assembling components on ultrathin PCBs?
Yes, assembling components on ultrathin PCBs requires special care due to their delicate nature. Techniques such as controlled soldering temperatures, adhesive underfilling, and surface mount technology (SMT) may be used to ensure proper assembly and reliability.
Can ultrathin PCBs support high-frequency signals?
Yes, ultrathin PCBs can support high-frequency signals, provided that proper design techniques and materials are used to maintain signal integrity and minimize signal loss. Specialized materials and impedance control techniques may be employed for high-frequency applications.
What are the cost considerations for ultrathin PCBs?
The cost of ultrathin PCBs depends on factors such as materials used, manufacturing processes, complexity of the design, and order quantity. Ultrathin PCBs may be more expensive than standard PCBs due to the specialized materials and processes involved. However, economies of scale and optimized designs can help mitigate costs.