Ultrathin LED PCB Manufacturer
Ultrathin LED PCB Manufacturer,Ultrathin LED PCBs are cutting-edge printed circuit boards designed specifically for LED lighting applications. Characterized by their incredibly slim profile and lightweight construction, these PCBs offer unparalleled flexibility and versatility in various lighting projects. With thicknesses ranging from mere fractions of a millimeter to a few millimeters, Ultrathin LED PCBs are ideal for applications where space is limited, such as slim-profile luminaires, edge-lit LED panels, and compact backlight modules for displays.
Constructed using high-quality materials like FR-4, polyimide, or metal core substrates, Ultrathin LED PCBs ensure excellent thermal management and electrical performance, ensuring optimal functionality and longevity of LED lighting systems. These PCBs can be fully customized to meet specific design requirements, allowing for flexibility in dimensions, shapes, layer configurations, and surface finishes. Whether in residential, commercial, or industrial settings, Ultrathin LED PCBs offer efficient, reliable, and aesthetically pleasing lighting solutions tailored to the needs of modern lighting applications.
What is an Ultrathin LED PCB?
An Ultrathin LED PCB (Printed Circuit Board) is a type of circuit board specifically designed for applications where thinness and lightness are crucial factors. These PCBs are commonly used in products such as flat-panel displays, backlighting systems for LCD screens, and various lighting fixtures.
The “ultrathin” aspect refers to the slim profile of the PCB, which is achieved by using thinner materials and innovative manufacturing techniques. These PCBs typically have a thickness ranging from fractions of a millimeter to a few millimeters.
LEDs (Light Emitting Diodes) are integrated into these PCBs to provide illumination. The LEDs are mounted onto the surface of the PCB and connected through conductive traces etched onto the board. The thinness of the PCB allows for compact and lightweight designs, making it ideal for applications where space is limited or weight needs to be minimized.
Ultrathin LED PCBs offer advantages such as energy efficiency, durability, and flexibility in design. They can be customized to fit specific shapes and sizes, making them suitable for a wide range of applications in industries such as consumer electronics, automotive, signage, and architectural lighting.
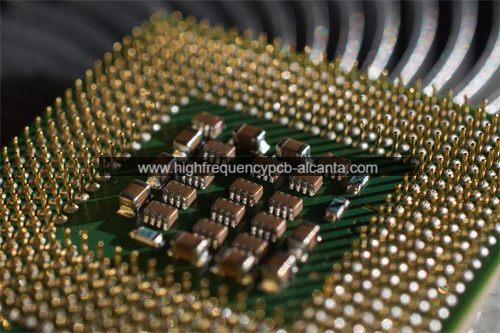
Ultrathin LED PCB Manufacturer
What are Ultrathin LED PCB Design Guidelines?
Designing ultrathin LED PCBs requires careful consideration of several factors to ensure optimal performance and reliability. Here are some general guidelines:
- Thinness: The PCB should be as thin as possible while still providing adequate mechanical support and electrical conductivity. Choose materials with low thickness and high flexibility, such as flexible PCB substrates or thin rigid substrates like FR-4.
- Heat Dissipation: Adequate heat dissipation is crucial to prevent overheating of the LEDs, which can reduce their lifespan and affect performance. Ensure that the PCB design includes sufficient thermal vias, heatsinks, or other heat dissipation mechanisms to effectively dissipate heat generated by the LEDs.
- Component Placement: Place the LEDs strategically on the PCB to achieve uniform illumination and maximize light output. Consider factors such as spacing between LEDs, orientation, and alignment to optimize light distribution.
- Trace Routing: Design the traces on the PCB to minimize electrical resistance and maximize current-carrying capacity. Use wide traces for power lines and minimize trace lengths to reduce voltage drop and power losses.
- Power Supply: Ensure that the power supply design can provide stable and sufficient power to the LEDs. Consider factors such as voltage regulation, current capacity, and protection mechanisms to prevent overloading or voltage spikes.
- Flexibility: If the PCB needs to bend or conform to a curved surface, choose flexible PCB materials and design the layout to accommodate bending without damaging the components or traces.
- Environmental Considerations: Consider the operating environment of the LED PCB, including temperature, humidity, and exposure to dust or moisture. Choose materials and coatings that provide protection against environmental factors to ensure long-term reliability.
- Manufacturability: Design the PCB with manufacturability in mind, considering factors such as ease of assembly, solderability, and compatibility with standard fabrication processes. Minimize complex features that could increase manufacturing costs or lead to production issues.
- Testing and Quality Control: Implement testing procedures to ensure the quality and reliability of the LED PCBs. Perform electrical testing, thermal testing, and reliability testing to identify any defects or weaknesses in the design.
By following these guidelines, designers can create ultrathin LED PCBs that meet the requirements for performance, reliability, and manufacturability in various applications.
What is the Ultrathin LED PCB Fabrication Process?
The fabrication process for ultrathin LED PCBs involves several steps, from design to assembly. Here’s a general overview of the process:
- Design: The process starts with the design of the PCB layout using computer-aided design (CAD) software. Designers determine the placement of components, routing of traces, and any special features required for the application.
- Material Selection: Choose appropriate materials for the PCB substrate, considering factors such as thickness, flexibility, thermal conductivity, and electrical properties. Flexible materials like polyimide or thin rigid materials like FR-4 can be used for ultrathin LED PCBs.
- Preparation of Substrate: The selected substrate material is prepared by cleaning and coating it with a layer of copper foil. The thickness of the copper foil depends on the electrical requirements of the PCB.
- Laser Drilling and Etching: Holes for through-hole components and vias are drilled using laser drilling technology. After drilling, the PCB is chemically etched to remove excess copper and define the traces according to the design.
- Additive Processes (Optional): In some cases, additive processes such as electroplating may be used to selectively deposit additional layers of metal onto the PCB to enhance conductivity or provide features like edge connectors.
- Solder Mask Application: A solder mask layer is applied to the PCB surface, leaving openings for component pads and vias. The solder mask protects the PCB from environmental factors and prevents solder bridges during assembly.
- Silkscreen Printing: Component designators, logos, and other markings are printed onto the PCB surface using a silkscreen printing process. This step helps with component placement and identification during assembly.
- Surface Finish: A surface finish is applied to the exposed copper pads to protect them from oxidation and facilitate soldering during assembly. Common surface finishes include HASL (Hot Air Solder Leveling), ENIG (Electroless Nickel Immersion Gold), and OSP (Organic Solderability Preservative).
- Component Placement: Surface-mount components, including LEDs, resistors, capacitors, and integrated circuits, are placed onto the PCB using automated pick-and-place machines. The components are positioned according to the design layout and secured temporarily with solder paste.
- Reflow Soldering: The assembled PCB is passed through a reflow oven, where the solder paste is melted, forming a permanent bond between the components and the PCB pads. The reflow process also ensures proper electrical connections between the components and the PCB traces.
- Inspection and Testing: The finished PCBs undergo visual inspection, electrical testing, and functional testing to verify quality and performance. Defective PCBs are repaired or discarded, depending on the severity of the issues.
- Packaging and Shipping: Once tested and approved, the ultrathin LED PCBs are packaged according to customer specifications and shipped to the assembly line for integration into final products.
Throughout the fabrication process, strict quality control measures are implemented to ensure that the ultrathin LED PCBs meet the required specifications for performance, reliability, and manufacturability. Collaboration between designers, engineers, and manufacturers is essential to optimize the fabrication process and achieve desired outcomes.
How do you manufacture an Ultrathin LED PCB?
Manufacturing an ultrathin LED PCB involves specialized processes tailored to meet the requirements of thinness, flexibility, and performance. Here’s a step-by-step guide to the manufacturing process:
- Material Selection: Choose a substrate material suitable for ultrathin PCBs. Flexible materials like polyimide (PI) or thin rigid materials like FR-4 with reduced thickness are commonly used. The choice of material depends on factors such as flexibility, thermal conductivity, and electrical properties.
- Cleaning and Surface Preparation: Clean the substrate material to remove any contaminants that could affect adhesion or conductivity. Then, apply a layer of copper foil to the substrate surface. The thickness of the copper foil depends on the electrical requirements of the PCB.
- Laser Drilling and Etching: Use laser drilling technology to create holes for through-hole components and vias. Then, chemically etch the substrate to remove excess copper and define the traces according to the PCB design. Precision is crucial in this step to ensure accurate trace patterns and hole placement.
- Additive Processes (Optional): Implement additive processes if additional metal layers are required for specific features or enhanced conductivity. Electroplating may be used to selectively deposit metal onto the PCB surface to create features like edge connectors.
- Solder Mask Application: Apply a solder mask layer to the PCB surface, leaving openings for component pads and vias. The solder mask protects the PCB from environmental factors and prevents solder bridges during assembly.
- Silkscreen Printing: Print component designators, logos, and other markings onto the PCB surface using a silkscreen printing process. This step assists with component placement and identification during assembly.
- Surface Finish: Apply a surface finish to the exposed copper pads to protect them from oxidation and facilitate soldering during assembly. Common surface finishes include HASL (Hot Air Solder Leveling), ENIG (Electroless Nickel Immersion Gold), and OSP (Organic Solderability Preservative).
- Component Placement: Use automated pick-and-place machines to accurately place surface-mount components, including LEDs, resistors, capacitors, and integrated circuits, onto the PCB. Components are positioned according to the design layout and temporarily secured with solder paste.
- Reflow Soldering: Pass the assembled PCBs through a reflow oven to melt the solder paste, forming a permanent bond between the components and the PCB pads. The reflow process ensures proper electrical connections and solder joints between components and traces.
- Inspection and Testing: Conduct visual inspection, electrical testing, and functional testing to verify the quality and performance of the manufactured PCBs. Defective PCBs are repaired or discarded, depending on the severity of the issues.
- Packaging and Shipping: Once tested and approved, package the ultrathin LED PCBs according to customer specifications and ship them to the assembly line for integration into final products.
Throughout the manufacturing process, strict quality control measures are implemented to ensure that the ultrathin LED PCBs meet the required specifications for performance, reliability, and manufacturability. Collaboration between designers, engineers, and manufacturers is essential to optimize the manufacturing process and achieve desired outcomes.
How much should an Ultrathin LED PCB cost?
The cost of an ultrathin LED PCB can vary widely depending on several factors, including the following:
- Size and Complexity: Larger and more complex PCBs with intricate designs, multiple layers, and densely packed components will typically cost more to manufacture due to increased material and labor costs.
- Material Selection: The choice of materials for the PCB substrate, copper layers, surface finish, and solder mask can significantly impact the cost. High-quality materials with special properties such as flexibility or high thermal conductivity may incur higher costs.
- Manufacturing Process: The manufacturing process used to produce the PCB, including specialized techniques such as laser drilling, additive processes, and surface finishing, can affect the overall cost. Some processes may require additional equipment or labor, adding to the manufacturing cost.
- Quantity: Economies of scale apply to PCB manufacturing, meaning that larger production runs generally result in lower per-unit costs. Ordering larger quantities of ultrathin LED PCBs can help reduce the cost per unit.
- Customization and Specifications: Customization options such as unique shapes, special features, or specific performance requirements may increase the cost of the PCB. Meeting certain specifications such as tight tolerances or strict quality standards can also affect the overall cost.
- Supplier and Location: PCB manufacturing costs can vary depending on the supplier’s pricing structure, location, and manufacturing capabilities. Offshore suppliers may offer lower labor costs but may incur higher shipping expenses and longer lead times.
- Additional Services: Additional services such as design assistance, prototyping, assembly, testing, and quality assurance may incur extra costs but can contribute to overall project success and efficiency.
As a rough estimate, ultrathin LED PCBs can range in cost from a few dollars to several tens of dollars per unit, with the actual cost depending on the factors mentioned above. It’s essential to obtain quotes from multiple PCB manufacturers and consider various factors to determine the most cost-effective solution for your specific project requirements.
What is Ultrathin LED PCB base material?
The base material for ultrathin LED PCBs can vary depending on the specific requirements of the application. However, there are several common materials used as substrates for ultrathin LED PCBs:
- Polyimide (PI): Polyimide is a popular choice for flexible PCB substrates due to its excellent flexibility, heat resistance, and electrical insulation properties. It can withstand high temperatures during manufacturing processes like reflow soldering and is well-suited for applications where flexibility is required, such as curved displays or wearable electronics.
- FR-4: FR-4 is a commonly used substrate material for rigid PCBs, but it can also be manufactured in thinner versions suitable for ultrathin LED PCBs. It offers good mechanical strength, thermal stability, and electrical insulation properties. Thin FR-4 substrates are more rigid compared to polyimide but provide greater dimensional stability.
- PET (Polyethylene Terephthalate): PET is another flexible substrate material used for ultrathin LED PCBs. It offers good flexibility, chemical resistance, and dimensional stability. PET substrates are often used in applications where cost-effectiveness and moderate flexibility are desired.
- Copper Foil: Copper foil is laminated onto the substrate material to provide the conductive traces and pads for the PCB. The thickness of the copper foil can vary depending on the electrical requirements of the PCB, with thinner foils used for ultrathin designs.
- Aluminum or Metal Core: In some cases, ultrathin LED PCBs may utilize metal core substrates such as aluminum or copper for improved thermal management. These substrates provide better heat dissipation, making them suitable for high-power LED applications where thermal performance is critical.
The choice of base material depends on factors such as flexibility, thermal performance, electrical properties, cost, and specific application requirements. Designers carefully evaluate these factors to select the most suitable substrate material for ultrathin LED PCBs to ensure optimal performance and reliability.
Which company makes Ultrathin LED PCB?
There are many companies that manufacture Ultrathin LED PCBs, including internationally renowned PCB manufacturers such as Advanced Circuits in the United States, Nippon Mektron in Japan, and AT&S (Austria Technologie & Systemtechnik AG) in China. These companies have extensive experience and advanced production technologies in the field of PCB manufacturing, capable of producing Ultrathin LED PCBs of various specifications and requirements.
In our company, we also produce Ultrathin LED PCBs. We have advanced manufacturing equipment and a skilled technical team capable of meeting various customer needs. Our manufacturing process strictly follows international standards and quality management systems to ensure reliable and stable product quality.
Firstly, we communicate with the customer to understand their needs and specifications. Then, our design team utilizes advanced CAD software to design the PCB layout customized to the customer’s requirements. Next, we select appropriate base materials such as flexible polyimide (PI) or FR-4 for the PCB substrate. During the manufacturing process, we employ advanced production equipment and processes such as laser drilling, chemical etching, and automated assembly to ensure the precision and stability of the PCB.
We also prioritize product quality and performance testing, conducting rigorous quality control during the production process to ensure that each PCB meets specification requirements. Our products can be applied in various fields such as electronics, lighting equipment, automotive industry, etc.
In summary, our company has the capability to produce high-quality Ultrathin LED PCBs. We are committed to providing customers with the highest quality products and services to meet their needs and expectations.
What are the 7 qualities of good customer service?
Good customer service is characterized by several key qualities that contribute to positive experiences and customer satisfaction. Here are seven qualities of good customer service:
- Responsiveness: Good customer service involves being prompt and proactive in addressing customer inquiries, concerns, and requests. Responding promptly to customer inquiries demonstrates attentiveness and a commitment to meeting their needs in a timely manner.
- Empathy: Empathy is essential in understanding and acknowledging customers’ emotions, concerns, and perspectives. Good customer service representatives listen actively, show genuine concern for customers’ issues, and strive to empathize with their situations, building rapport and trust.
- Professionalism: Professionalism encompasses maintaining a courteous, respectful, and professional demeanor in all interactions with customers. Good customer service representatives exhibit professionalism by adhering to company policies, maintaining confidentiality, and handling difficult situations with grace and composure.
- Knowledgeability: Good customer service requires having thorough knowledge of the products or services offered by the company. Customer service representatives should be well-trained and equipped to provide accurate information, answer questions, and offer solutions to customer problems effectively.
- Problem-Solving Skills: Effective problem-solving skills are crucial in resolving customer issues and addressing their concerns satisfactorily. Good customer service representatives demonstrate creativity, resourcefulness, and persistence in finding solutions to customer problems, even in challenging situations.
- Adaptability: Good customer service involves being adaptable and flexible in responding to diverse customer needs and preferences. Customer service representatives should be able to adjust their communication style, approach, and solutions to accommodate different personalities, situations, and customer expectations.
- Follow-Up and Follow-Through: Good customer service doesn’t end with resolving a customer’s immediate issue. It involves following up with customers to ensure their satisfaction, as well as following through on any promises or commitments made during the interaction. Following up demonstrates care and commitment to customer relationships, fostering loyalty and long-term satisfaction.
By embodying these qualities, companies can deliver exceptional customer service experiences that not only meet but exceed customer expectations, leading to increased customer loyalty, positive word-of-mouth, and business success.
FAQs
What are Ultrathin LED PCBs?
Ultrathin LED PCBs are printed circuit boards specifically designed for LED lighting applications. They are characterized by their exceptionally thin profile, making them suitable for applications where space is limited.
What are the benefits of Ultrathin LED PCBs?
Ultrathin LED PCBs offer several benefits, including space-saving design, excellent thermal management, flexibility, and high customizability. They are ideal for use in slim LED lighting fixtures, backlighting applications, and other space-constrained environments.
How thin are Ultrathin LED PCBs?
The thickness of Ultrathin LED PCBs can vary depending on the specific design and application requirements. However, they typically have a thickness ranging from a fraction of a millimeter to a few millimeters, allowing for compact and slim-profile lighting solutions.
What materials are used in Ultrathin LED PCBs?
Ultrathin LED PCBs are typically constructed using materials such as FR-4, polyimide, or metal core substrates. These materials offer excellent thermal conductivity, flexibility, and mechanical strength, making them suitable for LED lighting applications.
What types of LED lighting applications are Ultrathin LED PCBs used for?
Ultrathin LED PCBs are used in a wide range of lighting applications, including LED backlight modules for displays, edge-lit LED panels for signage and architectural lighting, and slim-profile luminaires for residential, commercial, and industrial lighting.
Can Ultrathin LED PCBs support high-power LEDs?
Yes, Ultrathin LED PCBs can support high-power LEDs, provided that proper thermal management measures are implemented. These may include thermal vias, metal core substrates, and heat sinks to dissipate heat effectively and prevent overheating of the LEDs.
Are Ultrathin LED PCBs customizable?
Yes, Ultrathin LED PCBs can be customized to meet specific application requirements. This includes customizing the dimensions, shape, layer configuration, surface finish, and other features to suit the needs of different LED lighting projects.
What are the design considerations for Ultrathin LED PCBs?
When designing Ultrathin LED PCBs, factors such as thermal management, electrical performance, mechanical stability, and compatibility with LED components must be carefully considered. Additionally, attention should be paid to the overall form factor and integration with the lighting fixture or device.
Where can I purchase Ultrathin LED PCBs?
Ultrathin LED PCBs can be purchased from specialized PCB manufacturers, LED lighting suppliers, and distributors. It’s essential to work with a reputable supplier that can provide high-quality, reliable PCBs tailored to your specific requirements.