Ultrathin IC/BGA Substrate Manufacturer
Ultrathin IC/BGA Substrate Manufacturer,Ultrathin IC/BGA substrates are compact interconnection platforms designed for high-density packaging in electronic devices. With exceptional thinness, they enable miniaturization, optimizing space in gadgets like smartphones and wearables. These substrates enhance electrical performance, support thermal dissipation, and ensure reliability. Manufactured using advanced processes like thin film deposition and precise lithography, they feature intricate circuitry and vias for seamless connectivity. From smartphones to automotive electronics, their versatility fuels innovation in modern technology, offering sleeker designs and improved functionality. Ultrathin IC/BGA substrates epitomize the fusion of cutting-edge engineering and practical design, driving the evolution of electronic devices.
What is an Ultrathin IC/BGA Substrate?
An ultrathin IC/BGA substrate refers to a highly compact and slim interconnection platform used in integrated circuit (IC) packaging. These substrates are engineered to be incredibly thin, typically ranging from tens to a few hundred micrometers thick. They serve as a crucial interface between the IC chip and the rest of the electronic system, facilitating signal transmission, power distribution, and thermal management.
The term “BGA” stands for Ball Grid Array, a type of packaging where solder balls are arranged in a grid pattern on the bottom of the IC package for mounting onto a circuit board. The ultrathin nature of these substrates allows for miniaturization of electronic devices, enabling the development of thinner and lighter products such as smartphones, tablets, wearables, and other portable gadgets.
These substrates are often made using advanced materials like silicon, glass, or laminate materials, and they undergo intricate manufacturing processes such as thin-film deposition, etching, and lithography to achieve their desired thickness and electrical properties.
In addition to their slim profile, ultrathin IC/BGA substrates offer advantages such as improved electrical performance, enhanced thermal dissipation, and increased reliability due to reduced package size and shorter signal paths. These attributes make them ideal for high-density packaging applications where space and weight are critical considerations.
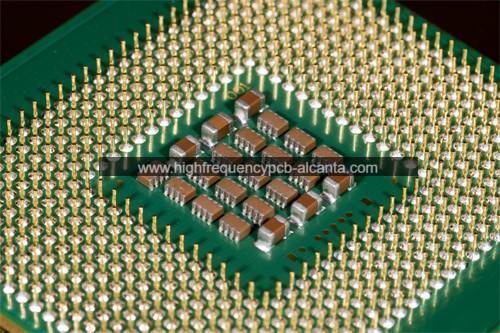
Ultrathin IC/BGA Substrate Manufacturer
What are the Ultrathin IC/BGA Substrate Design Guidelines?
Designing with ultrathin IC/BGA substrates requires careful consideration of various factors to ensure optimal performance and reliability. Here are some key design guidelines:
- Signal Integrity: Maintain controlled impedance for high-speed signal traces to minimize signal degradation and reflections. Design proper signal routing with controlled spacing, trace width, and impedance matching.
- Thermal Management: Incorporate thermal vias and thermal pads to efficiently dissipate heat from the IC chip to the substrate and then to the PCB. Ensure proper placement of thermal vias to avoid signal interference.
- Power Delivery: Design power distribution networks (PDNs) with low impedance paths to deliver stable power to the IC chip. Use multiple power and ground planes to minimize voltage drops and noise.
- Package Size and Layout: Optimize the package size and layout to maximize space utilization while maintaining signal integrity and thermal performance. Consider the placement of components, routing channels, and keep-out zones.
- Stackup Design: Choose an appropriate substrate stackup with the right number of layers and materials to meet electrical, thermal, and mechanical requirements. Balance layer thickness, dielectric constant, and material properties for optimal performance.
- Mechanical Stability: Ensure the substrate design provides adequate mechanical support and stiffness to withstand handling and assembly processes without deformation or damage. Consider factors like material selection, thickness, and reinforcement structures.
- Manufacturability: Design for manufacturability by adhering to fabrication capabilities and limitations of the chosen substrate materials and processes. Minimize complex features that could increase production costs or yield issues.
- Reliability and Durability: Perform stress analysis and reliability simulations to assess the structural integrity and long-term reliability of the substrate design under various operating conditions, including thermal cycling and mechanical stress.
- EMI/EMC Considerations: Implement techniques such as shielding, ground planes, and signal isolation to mitigate electromagnetic interference (EMI) and ensure compliance with electromagnetic compatibility (EMC) standards.
- Testing and Validation: Plan for comprehensive testing and validation of the substrate design to verify electrical performance, thermal behavior, and mechanical robustness. Conduct signal integrity analysis, thermal simulations, and reliability testing to validate the design against specifications and requirements.
By following these design guidelines, engineers can develop ultrathin IC/BGA substrate designs that meet the stringent requirements of modern electronic devices, balancing performance, reliability, and manufacturability.
What is the Ultrathin IC/BGA Substrate Fabrication Process?
The fabrication process of ultrathin IC/BGA substrates involves several intricate steps to create a compact and reliable interconnection platform. While specific processes may vary depending on the substrate material and design requirements, here’s a general overview:
- Substrate Material Selection: Choose a suitable substrate material based on electrical, thermal, and mechanical properties. Common materials include silicon, glass, and laminate materials like FR-4 or polyimide.
- Substrate Preparation:Begin with a clean substrate surface free from contaminants. Depending on the material, this may involve cleaning, polishing, or surface treatment to ensure proper adhesion of subsequent layers.
- Thin Film Deposition: Deposit thin film layers of conductive and insulating materials onto the substrate surface using techniques such as physical vapor deposition (PVD) or chemical vapor deposition (CVD). These thin films form the basis for creating circuitry and interconnects.
- Lithography: Use photolithography or electron beam lithography to pattern the deposited thin films with the desired circuitry layout. This involves applying a photoresist layer, exposing it to light or electron beams through a mask, and developing the pattern.
- Etching: Employ wet or dry etching processes to selectively remove unwanted thin film material, leaving behind the desired circuit patterns and interconnect structures defined by the lithography step.
- Dielectric Layer Deposition: Deposit dielectric layers to insulate the conductive traces and provide mechanical support. These layers may also serve as substrates for additional circuit layers in multilayer designs.
- Via Formation:Create vias (interconnect holes) through the dielectric layers using techniques like laser drilling or chemical etching. Vias establish electrical connections between different circuit layers and facilitate thermal dissipation.
- Conductor Plating: Deposit conductor material (typically copper) into the vias and over the surface to establish electrical continuity and build up the thickness of the conductive traces. Electroplating or electroless plating processes are commonly used for this step.
- Surface Finish: Apply a surface finish to protect the conductive traces, enhance solderability, and improve reliability. Common surface finishes include solder mask, immersion gold, or electroless nickel immersion gold (ENIG).
- Quality Control and Testing: Perform rigorous inspection, quality control, and testing throughout the fabrication process to ensure the substrate meets specifications and standards for electrical performance, dimensional accuracy, and reliability.
- Packaging and Assembly: After fabrication, the ultrathin IC/BGA substrates are typically assembled with semiconductor chips, encapsulated, and packaged into final IC packages ready for integration into electronic devices.
By following these fabrication steps with precision and care, manufacturers can produce ultrathin IC/BGA substrates with high performance, reliability, and miniaturization capabilities to meet the demands of modern electronic applications.
How do you manufacture an Ultrathin IC/BGA Substrate?
Manufacturing an ultrathin IC/BGA substrate involves a series of sophisticated processes to create a compact and reliable interconnection platform. Here’s a step-by-step guide to the manufacturing process:
- Substrate Selection: Choose a suitable substrate material based on the specific requirements of the application. Common materials include silicon, glass, and laminate materials such as polyimide or FR-4.
- Substrate Preparation: Begin with a clean substrate surface. Depending on the material, this may involve cleaning, polishing, or surface treatment to ensure proper adhesion of subsequent layers.
- Thin Film Deposition: Deposit thin film layers of conductive and insulating materials onto the substrate surface. Techniques like physical vapor deposition (PVD) or chemical vapor deposition (CVD) are used to create these layers.
- Lithography: Use lithography techniques such as photolithography or electron beam lithography to pattern the deposited thin films with the desired circuitry layout. A photoresist layer is applied, exposed to light or electron beams through a mask, and then developed to define the circuit patterns.
- Etching: Employ wet or dry etching processes to selectively remove unwanted thin film material, leaving behind the desired circuit patterns and interconnect structures defined by the lithography step.
- Dielectric Layer Deposition: Deposit dielectric layers onto the substrate surface to insulate the conductive traces and provide mechanical support. These layers may also serve as substrates for additional circuit layers in multilayer designs.
- Via Formation: Create vias (interconnect holes) through the dielectric layers using techniques like laser drilling or chemical etching. Vias establish electrical connections between different circuit layers and facilitate thermal dissipation.
- Conductor Plating: Deposit conductor material (typically copper) into the vias and over the surface to establish electrical continuity and build up the thickness of the conductive traces. Electroplating or electroless plating processes are commonly used for this step.
- Surface Finish: Apply a surface finish to protect the conductive traces, enhance solderability, and improve reliability. Common surface finishes include solder mask, immersion gold, or electroless nickel immersion gold (ENIG).
- Quality Control and Testing: Perform rigorous inspection, quality control, and testing throughout the manufacturing process to ensure the substrate meets specifications and standards for electrical performance, dimensional accuracy, and reliability.
- Packaging and Assembly: After manufacturing, the ultrathin IC/BGA substrates are typically assembled with semiconductor chips, encapsulated, and packaged into final IC packages ready for integration into electronic devices.
By meticulously following these manufacturing steps and employing advanced technologies and quality control measures, manufacturers can produce ultrathin IC/BGA substrates with high performance, reliability, and miniaturization capabilities to meet the demands of modern electronic applications.
How much should an Ultrathin IC/BGA Substrate cost?
The cost of an ultrathin IC/BGA substrate can vary significantly depending on various factors such as substrate material, complexity of design, manufacturing processes involved, dimensions, and volume of production. However, these substrates generally tend to be more expensive compared to conventional substrates due to their specialized nature and advanced manufacturing techniques required for their production.
Here are some factors that can influence the cost of an ultrathin IC/BGA substrate:
- Material Cost:The choice of substrate material can greatly impact the overall cost. Silicon substrates, for example, tend to be more expensive compared to laminate materials like polyimide or FR-4.
- Manufacturing Processes: The complexity of manufacturing processes involved, such as thin film deposition, lithography, etching, and plating, can affect the cost. Advanced processes and equipment may incur higher production expenses.
- Design Complexity: The complexity of the substrate design, including the number of layers, density of circuitry, and sophistication of features such as vias and fine-pitch routing, can influence the manufacturing cost.
- Size and Thickness:Larger and thinner substrates may require additional processing steps and precision, which can contribute to higher costs.
- Volume of Production: Economies of scale play a significant role in determining the cost. Higher volumes typically lead to lower per-unit costs due to optimized manufacturing processes and bulk purchasing of materials.
- Quality and Reliability Requirements: Meeting stringent quality and reliability standards may necessitate additional testing and quality control measures, which can add to the overall cost.
- Customization and Special Requirements: Customized features, special surface finishes, and specific customer requirements can increase the cost of production.
Due to the variability in these factors, it’s challenging to provide a specific cost figure for an ultrathin IC/BGA substrate without detailed information about the substrate’s specifications and manufacturing parameters. Generally, these substrates are considered high-value components in electronic systems, and their cost is often justified by their performance, miniaturization capabilities, and reliability. Companies typically work closely with substrate manufacturers to optimize designs and processes to achieve the desired balance between cost and performance for their specific applications.
What is Ultrathin IC/BGA Substrate base material?
The base material for ultrathin IC/BGA substrates can vary depending on the specific requirements of the application and the desired properties of the substrate. Some common base materials used in the manufacturing of ultrathin substrates include:
- Silicon: Silicon substrates are commonly used for ultrathin IC substrates, particularly in applications where high performance, precision, and integration with semiconductor devices are critical. Silicon offers excellent thermal conductivity, dimensional stability, and compatibility with semiconductor manufacturing processes.
- Glass: Glass substrates are preferred for applications requiring transparency, high electrical insulation, and compatibility with high-temperature processes. Borosilicate glass and quartz glass are commonly used for ultrathin substrates in applications such as displays, sensors, and optoelectronic devices.
- Laminate Materials: Laminate materials like polyimide (PI) or FR-4 (a type of epoxy-glass laminate) are widely used for flexible and rigid-flex ultrathin substrates. These materials offer flexibility, lightweight, and compatibility with standard PCB manufacturing processes, making them suitable for applications where mechanical flexibility and miniaturization are required.
- Metal Foils: Thin metal foils such as copper or aluminum can be used as base materials for ultrathin substrates in applications where high electrical conductivity, thermal dissipation, and mechanical strength are essential. Metal foils are often laminated with dielectric materials to create multilayer structures for high-density interconnects.
- Ceramics: Ceramics such as alumina (aluminum oxide) or aluminum nitride (AlN) are utilized in ultrathin substrates for their excellent thermal conductivity, mechanical strength, and compatibility with high-temperature processes. Ceramic substrates are commonly used in power electronics, RF/microwave applications, and high-power LED packaging.
The choice of base material depends on various factors including electrical and thermal requirements, mechanical properties, dimensional stability, compatibility with manufacturing processes, and cost considerations. Substrate manufacturers select the most suitable base material and customize the substrate design and fabrication process to meet the specific needs of each application.
Which company makes Ultrathin IC/BGA Substrates?
Many companies play an important role in manufacturing ultrathin IC/BGA substrates. Some well-known companies include Intel, Samsung Electronics, TSMC, Huawei, Lenovo, Qualcomm, and others. These companies have advanced technology and manufacturing capabilities to design and produce ultrathin IC/BGA substrates that meet high-performance and high-density requirements for various electronic products such as smartphones, tablets, computers, IoT devices, and more.
For our company, we also have extensive experience and advanced technology to manufacture high-quality ultrathin IC/BGA substrates. We have a professional engineering team capable of providing comprehensive solutions, from design to manufacturing to testing, to ensure that our products meet the needs and specifications of our customers.
Our manufacturing process utilizes advanced techniques and equipment, including thin film deposition, lithography, etching, plating, and more. We can select suitable substrate materials such as silicon, glass, polyimide, etc., according to customer requirements to meet the needs of different application scenarios.
We emphasize quality control and quality management, and all products undergo rigorous inspection and testing to ensure compliance with international standards and customer requirements. We are committed to providing reliable and high-performance ultrathin IC/BGA substrates to support our customers’ products.
Additionally, we can customize products according to customer requirements and provide personalized solutions to meet specific needs. Our goal is to become a trusted partner for customers, driving the development and innovation of electronic technology together.
What are the 7 qualities of good customer service?
Good customer service is essential for building positive relationships with customers and ensuring satisfaction. Seven qualities of good customer service include:
- Responsiveness: Being prompt and attentive to customer inquiries, concerns, and requests. Responding quickly to customer needs demonstrates that their time is valued and that their issues are taken seriously.
- Empathy: Showing understanding and empathy towards customers’ feelings, concerns, and experiences. Empathizing with customers helps build rapport and trust, and it makes them feel heard and valued.
- Clarity: Communicating clearly and effectively to ensure that customers understand information, instructions, and solutions provided. Clear communication helps avoid misunderstandings and confusion, leading to smoother interactions and resolutions.
- Professionalism: Maintaining a professional demeanor and attitude in all interactions with customers. Professionalism involves being courteous, respectful, and knowledgeable while handling customer inquiries or resolving issues.
- Problem-solving skills: Demonstrating effective problem-solving skills to address customer issues and concerns. Being proactive in finding solutions and resolving problems efficiently contributes to customer satisfaction and loyalty.
- Flexibility: Being adaptable and flexible in addressing customer needs and accommodating their preferences whenever possible. Flexibility involves being open to different approaches and solutions to meet diverse customer requirements.
- Follow-up: Following up with customers to ensure that their issues have been resolved satisfactorily and to gather feedback on their experience. Following up demonstrates care and commitment to customer satisfaction, and it provides an opportunity to address any remaining concerns or questions.
By embodying these qualities, businesses can deliver exceptional customer service experiences that foster loyalty, positive word-of-mouth, and long-term success.
FAQs
What are ultrathin IC/BGA substrates?
Ultrathin IC/BGA substrates are highly compact interconnection platforms used in integrated circuit (IC) packaging. They are engineered to be exceptionally thin, enabling miniaturization of electronic devices.
What are the advantages of ultrathin IC/BGA substrates?
Ultrathin substrates offer advantages such as reduced form factor, improved electrical performance, enhanced thermal dissipation, increased reliability, and support for high-density packaging.
What materials are used in ultrathin IC/BGA substrates?
Common materials include silicon, glass, laminate materials like polyimide or FR-4, and metal foils such as copper or aluminum, depending on the specific requirements of the application.
How are ultrathin IC/BGA substrates manufactured?
The manufacturing process involves steps such as thin film deposition, lithography, etching, dielectric layer deposition, via formation, conductor plating, surface finishing, and quality control/testing.
What are the design considerations for ultrathin IC/BGA substrates?
Design considerations include signal integrity, thermal management, power delivery, package size/layout, stackup design, mechanical stability, manufacturability, reliability, and EMI/EMC considerations.
What are the applications of ultrathin IC/BGA substrates?
Ultrathin substrates are used in various electronic devices such as smartphones, tablets, wearables, IoT devices, high-performance computing systems, and automotive electronics.
How much do ultrathin IC/BGA substrates cost?
The cost varies depending on factors like substrate material, design complexity, manufacturing processes, size/thickness, volume of production, quality/reliability requirements, and customization/special requirements.
Where can I find suppliers of ultrathin IC/BGA substrates?
Suppliers include semiconductor companies, substrate manufacturers, and electronics component distributors. Researching online or contacting industry associations can help identify potential suppliers.