Ultrathin GPU Substrate Manufacturer
Ultrathin GPU Substrate Manufacturer,Ultrathin GPU substrates are specialized platforms upon which graphics processing units (GPUs) are constructed, designed to be exceptionally thin while maintaining structural integrity and performance. These substrates enable the development of sleek and lightweight electronic devices without compromising on graphics capabilities. Typically made from materials like specialized ceramics or composite materials, ultrathin GPU substrates offer high thermal conductivity, electrical insulation, and mechanical strength.
Manufacturing ultrathin GPU substrates involves advanced processes such as thin film deposition, photolithography, and via formation. These substrates undergo rigorous quality control measures to ensure precise alignment, electrical connectivity, and reliability. By reducing the thickness of the substrate, manufacturers can enhance heat dissipation and improve power efficiency, contributing to longer battery life in portable devices.
Overall, ultrathin GPU substrates represent a technological advancement that enables the creation of more compact and efficient electronic devices, meeting the demands of modern computing while maintaining high performance and reliability.
What is an Ultrathin GPU Substrate?
An Ultrathin GPU Substrate refers to a specialized platform or base upon which a graphics processing unit (GPU) is built. It’s designed to be exceptionally thin, usually thinner than conventional substrates, allowing for more compact and lightweight GPU designs. This ultrathin construction enables the creation of slimmer devices like laptops, tablets, and even smartphones without sacrificing the performance of the GPU.
The substrate serves as a foundation for the GPU’s circuitry, providing structural support and facilitating the electrical connections between the GPU and other components of the device, such as the motherboard and memory modules. By reducing the thickness of the substrate, manufacturers can shrink the overall size of the GPU package, making it easier to integrate into increasingly compact electronic devices.
In addition to saving space, ultrathin GPU substrates can also offer advantages in terms of thermal management and power efficiency. The reduced thickness can enhance heat dissipation, helping to prevent overheating and improve the longevity of the GPU. Moreover, a thinner substrate may contribute to lower power consumption, contributing to better battery life in portable devices.
Overall, ultrathin GPU substrates represent a technological advancement that enables the creation of smaller, lighter, and more power-efficient devices without compromising on graphics performance. This innovation is particularly valuable in the realm of mobile computing, where thinness, portability, and performance are highly sought after.
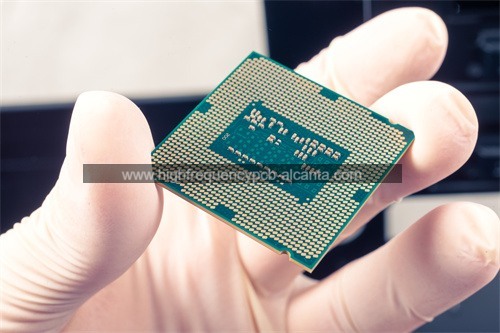
Ultrathin GPU Substrate Manufacturer
What are the Ultrathin GPU Substrate Design Guidelines?
Designing ultrathin GPU substrates requires careful consideration of several key factors to ensure optimal performance, reliability, and manufacturability. While specific guidelines may vary depending on the manufacturer and the intended application, some common design principles include:
- Material Selection: Choosing appropriate materials for the substrate is crucial. These materials should offer high electrical conductivity, good thermal properties for heat dissipation, and mechanical strength to support the GPU and withstand environmental stresses. Common substrate materials include various types of ceramics and specialized composite materials.
- Thickness Optimization: The primary objective of an ultrathin GPU substrate is to minimize thickness while maintaining structural integrity and electrical performance. Designers must strike a balance between thinness and rigidity to prevent bending or warping that could affect the GPU’s functionality.
- Layer Configuration: The substrate typically consists of multiple layers, including conductive traces, insulating layers, and possibly additional components such as capacitors or resistors. Optimizing the arrangement and thickness of these layers is essential to ensure efficient signal transmission, minimal interference, and reliable operation.
- Signal Integrity: Maintaining signal integrity is critical for high-performance GPUs. Design guidelines may include specifications for trace widths, spacing, and routing techniques to minimize signal degradation, crosstalk, and electromagnetic interference (EMI).
- Thermal Management: Efficient heat dissipation is essential to prevent overheating and maintain optimal GPU performance. Designers may incorporate features such as thermal vias, heat spreaders, and thermal pads to facilitate heat transfer away from the GPU die and dissipate it effectively into the surrounding environment.
- Manufacturability: Design guidelines should consider the practical aspects of substrate fabrication and assembly processes. This includes considerations such as feature size limitations, material compatibility, alignment accuracy, and yield optimization to ensure cost-effective production and reliable quality control.
- Compatibility with Packaging: Ultrathin GPU substrates must be compatible with the packaging and interconnect technologies used in the overall GPU assembly. Designers must ensure proper alignment, electrical connectivity, and mechanical stability when integrating the substrate with other components such as the GPU die, memory modules, and interface connectors.
By adhering to these design guidelines, engineers can develop ultrathin GPU substrates that meet the stringent requirements of modern computing devices, enabling thinner, lighter, and more powerful products without compromising on performance or reliability.
What is the Ultrathin GPU Substrate Fabrication Process?
The fabrication process for ultrathin GPU substrates involves several sequential steps, each contributing to the creation of a high-performance, compact, and reliable substrate. While specific details may vary depending on the manufacturer and the substrate’s design, here is a generalized overview of the fabrication process:
- Substrate Material Preparation: The process begins with preparing the substrate material, which is typically a specialized composite or ceramic material with specific electrical, thermal, and mechanical properties. The material may be sourced in the form of sheets or blocks and undergoes preprocessing steps such as cleaning and surface treatment to ensure optimal adhesion and compatibility with subsequent fabrication processes.
- Layer Deposition: Thin film deposition techniques are employed to create the various layers that comprise the substrate. These layers may include conductive traces, insulating layers, and possibly additional components such as capacitors or resistors. Common deposition methods include physical vapor deposition (PVD), chemical vapor deposition (CVD), sputtering, and electrochemical deposition.
- Photolithography and Etching: Photolithography is used to define the intricate patterns of conductive traces and other features on the substrate’s surface. A photoresist material is applied to the substrate, exposed to ultraviolet (UV) light through a photomask, and then developed to selectively remove portions of the photoresist. The exposed areas are etched away using wet or dry etching processes, leaving behind the desired pattern of conductive traces and features.
- Layer Stacking and Lamination: Once the individual layers have been fabricated, they are stacked and laminated together to form a multilayered structure. This process may involve bonding the layers using adhesives, thermal compression, or other bonding techniques. Careful alignment and stacking are crucial to ensure proper electrical connectivity and structural integrity.
- Via Formation: Vias are small holes drilled or etched through the substrate to establish electrical connections between different layers. Through-hole vias penetrate the entire thickness of the substrate, while blind vias only extend partway through. Vias are typically formed using laser drilling, mechanical drilling, or chemical etching processes.
- Surface Finishing: Surface finishing processes may be employed to improve the substrate’s electrical performance, corrosion resistance, and solderability. This may involve applying thin metal layers such as gold or solder to the substrate’s surface through electroplating or other deposition techniques.
- Quality Control and Testing:Throughout the fabrication process, quality control measures are implemented to ensure the substrate meets the required specifications for dimensional accuracy, electrical connectivity, signal integrity, and reliability. Various testing methods, including visual inspection, electrical testing, and thermal analysis, are conducted to identify and rectify any defects or inconsistencies.
By following these fabrication steps with precision and attention to detail, manufacturers can produce ultrathin GPU substrates that meet the demanding performance and reliability requirements of modern computing devices.
How do you manufacture an Ultrathin GPU Substrate?
Manufacturing an ultrathin GPU substrate involves a series of intricate processes aimed at creating a thin, lightweight, and high-performance platform for the graphics processing unit (GPU). Here’s an overview of the typical manufacturing process:
- Material Selection: The process begins with selecting suitable substrate materials with properties like high thermal conductivity, electrical insulation, and mechanical strength. Common materials include specialized ceramics or composite materials.
- Material Preparation: The selected material is prepared in the desired form, often in the form of thin sheets or blocks. It undergoes preprocessing steps such as cleaning, surface treatment, and possibly thinning processes to achieve the desired thickness.
- Layer Deposition: Thin film deposition techniques are used to create the various layers that form the substrate. This may involve depositing conductive materials for traces, insulating layers, and possibly additional components like capacitors or resistors. Techniques such as physical vapor deposition (PVD), chemical vapor deposition (CVD), sputtering, or electrochemical deposition are utilized.
- Photolithography and Etching: Photolithography is employed to define the intricate patterns of conductive traces and features on the substrate’s surface. A photoresist material is applied, patterned using UV light through a photomask, and then developed to selectively remove portions of the photoresist. The exposed areas are etched away using wet or dry etching processes, leaving behind the desired pattern.
- Layer Stacking and Bonding: Once the individual layers are fabricated, they are stacked and bonded together to form a multilayered structure. Bonding techniques such as thermal compression or adhesives are used to ensure proper alignment and connectivity between layers.
- Via Formation: Vias are created to establish electrical connections between different layers of the substrate. This involves drilling or etching small holes through the substrate material. Laser drilling, mechanical drilling, or chemical etching processes may be used to create vias.
- Surface Finishing:Surface finishing processes are applied to improve the substrate’s electrical performance, corrosion resistance, and solderability. This may include applying thin metal layers like gold or solder through electroplating or other deposition techniques.
- Quality Control and Testing: Throughout the manufacturing process, quality control measures are implemented to ensure the substrate meets specifications for dimensional accuracy, electrical connectivity, signal integrity, and reliability. Various testing methods, including visual inspection, electrical testing, and thermal analysis, are conducted to identify and rectify any defects.
By carefully executing these manufacturing steps, manufacturers can produce ultrathin GPU substrates that meet the stringent requirements of modern computing devices, enabling thinner, lighter, and more powerful products without sacrificing performance or reliability.
How much should an Ultrathin GPU Substrate cost?
The cost of an ultrathin GPU substrate can vary widely depending on several factors, including the materials used, the complexity of the design, the manufacturing processes involved, and the scale of production. Here are some factors that can influence the cost:
- Materials: The cost of substrate materials can vary significantly based on factors such as purity, availability, and special properties required for the application. Specialized ceramics or composite materials with high thermal conductivity and electrical insulation properties may be more expensive than conventional substrates.
- Manufacturing Processes: The fabrication processes involved in creating an ultrathin GPU substrate can also impact the cost. Processes such as thin film deposition, photolithography, etching, and via formation require specialized equipment and skilled labor, which can contribute to the overall cost.
- Complexity of Design: The complexity of the substrate design, including the number of layers, the density of features, and the precision required for alignment and connectivity, can affect manufacturing costs. More complex designs may require additional fabrication steps and higher levels of quality control, increasing the overall cost.
- Scale of Production: The scale of production can also influence the cost of ultrathin GPU substrates. Larger production volumes typically benefit from economies of scale, leading to lower per-unit costs. Conversely, low-volume production runs may incur higher costs due to setup and tooling expenses.
- Quality and Reliability Requirements: Meeting stringent quality and reliability standards may require additional testing, inspection, and quality control measures, which can add to the overall cost of production.
Given these factors, it’s challenging to provide a specific cost estimate for an ultrathin GPU substrate without knowing the details of the substrate’s design and manufacturing requirements. However, it’s safe to say that ultrathin GPU substrates are likely to be more expensive than conventional substrates due to the specialized materials and manufacturing processes involved.
What is Ultrathin GPU Substrate base material?
The base material used for ultrathin GPU substrates can vary depending on the manufacturer, specific design requirements, and desired performance characteristics. However, common materials used for ultrathin GPU substrates include:
- Specialized Ceramics:Certain types of ceramics are popular choices for ultrathin GPU substrates due to their excellent thermal conductivity, electrical insulation properties, and mechanical strength. Alumina (Al2O3) and aluminum nitride (AlN) are examples of ceramics commonly used in substrate applications.
- Composite Materials: Some manufacturers use composite materials composed of a combination of ceramics, polymers, and other additives to achieve specific properties such as enhanced thermal performance, reduced weight, or improved mechanical flexibility.
- Flexible Substrates: In certain applications where flexibility is essential, flexible substrate materials such as polyimide (PI) or polyester (PET) films may be used. These materials offer flexibility while still providing adequate electrical insulation and thermal properties.
- Metal Core Substrates: Metal core substrates, typically consisting of a thin layer of metal (such as aluminum or copper) sandwiched between insulating layers, are sometimes used for ultrathin GPU substrates. These substrates offer excellent thermal conductivity and can help dissipate heat generated by the GPU more efficiently.
The choice of base material depends on various factors, including thermal management requirements, electrical performance, mechanical stability, and cost considerations. Manufacturers carefully select the substrate material that best suits the specific needs of the GPU design and the target application, aiming to achieve optimal performance, reliability, and manufacturability.
Which company makes Ultrathin GPU Substrates?
Currently, there are many companies manufacturing ultrathin GPU substrates. Some major manufacturers include Intel, NVIDIA, AMD, TSMC, Samsung, Huawei, Lenovo, and others. These companies have extensive experience and advanced manufacturing technologies in the GPU field, capable of producing high-performance ultrathin GPU substrates to meet the requirements of different devices.
As for our company, we can also produce ultrathin GPU substrates. We have advanced manufacturing equipment and a skilled technical team with the capability to design, manufacture, and test ultrathin GPU substrates. We focus on technological innovation and quality control, committed to providing customers with high-performance and reliable products.
Our manufacturing process includes several key steps:
- Material Selection: We choose high-quality substrate materials such as special ceramics, composite materials, or metal substrates to meet the requirements of ultrathin GPU substrates.
- Design Optimization:Our engineering team optimizes the design to ensure that the ultrathin GPU substrate achieves the best performance in terms of size, electrical properties, and heat dissipation.
- Manufacturing Processes:We employ advanced manufacturing processes, including thin film deposition, lithography, etching, stacking and bonding, via formation, etc., to ensure the precision and stability of the substrate.
- Quality Control: We implement strict quality control measures, conducting rigorous inspections and tests at every stage from raw material procurement to manufacturing, ensuring that the products meet customer requirements and standards.
- Technical Support and After-sales Service: We provide comprehensive technical support and after-sales service to ensure that any issues encountered by customers during use are promptly addressed. We continuously improve product performance and quality.
Through these measures, we are confident in producing high-quality ultrathin GPU substrates and providing customers with satisfactory solutions.
What are the 7 qualities of good customer service?
Good customer service is characterized by several key qualities that contribute to a positive and satisfying experience for customers. Here are seven qualities:
- Responsiveness:Good customer service involves being prompt and responsive to customers’ inquiries, concerns, and needs. This includes timely communication, acknowledging customer queries promptly, and providing quick resolutions to issues.
- Empathy: Empathy is the ability to understand and relate to customers’ emotions and perspectives. Good customer service representatives listen actively, show empathy towards customers’ concerns, and strive to address their needs with compassion and understanding.
- Clarity and Communication: Effective communication is essential for good customer service. Customer service representatives should communicate clearly, using language that is easy to understand, and provide accurate information to address customers’ questions and concerns.
- Knowledge and Expertise: Good customer service requires a thorough understanding of the products or services offered. Customer service representatives should be knowledgeable about the company’s offerings, policies, and procedures, enabling them to provide accurate and helpful assistance to customers.
- Problem-solving Skills: Good customer service involves effectively resolving customers’ issues and concerns. Customer service representatives should possess strong problem-solving skills, identify root causes of problems, and offer appropriate solutions to meet customers’ needs.
- Professionalism: Professionalism is essential in customer service interactions. This includes maintaining a courteous and respectful demeanor, adhering to company policies and procedures, and handling challenging situations with diplomacy and professionalism.
- Follow-up and Feedback: Good customer service extends beyond the initial interaction. Following up with customers to ensure their issues have been resolved satisfactorily and seeking feedback to improve service quality are essential aspects of good customer service. This demonstrates a commitment to customer satisfaction and continuous improvement.
By embodying these qualities, businesses can foster positive relationships with customers, enhance brand loyalty, and differentiate themselves in the marketplace through exceptional customer service.
FAQs
What is an ultrathin GPU substrate?
An ultrathin GPU substrate is a specialized platform or base upon which a graphics processing unit (GPU) is built. It is designed to be exceptionally thin, allowing for more compact and lightweight GPU designs.
What are the benefits of ultrathin GPU substrates?
Ultrathin GPU substrates enable the creation of thinner and lighter electronic devices, such as laptops, tablets, and smartphones, without compromising on graphics performance. They also contribute to better thermal management and power efficiency.
What materials are used in ultrathin GPU substrates?
Common materials used in ultrathin GPU substrates include specialized ceramics, composite materials, and metal core substrates. These materials offer properties such as high thermal conductivity, electrical insulation, and mechanical strength.
How are ultrathin GPU substrates manufactured?
The manufacturing process for ultrathin GPU substrates involves steps such as material preparation, layer deposition, photolithography and etching, layer stacking and bonding, via formation, surface finishing, and quality control and testing.
What factors affect the cost of ultrathin GPU substrates?
The cost of ultrathin GPU substrates can vary depending on factors such as the materials used, complexity of design, manufacturing processes involved, scale of production, and quality and reliability requirements.
What companies produce ultrathin GPU substrates?
Several companies, including Intel, NVIDIA, AMD, TSMC, Samsung, Huawei, and Lenovo, produce ultrathin GPU substrates. These companies have advanced manufacturing capabilities and expertise in GPU technology.
What are the design guidelines for ultrathin GPU substrates?
Design guidelines for ultrathin GPU substrates include considerations such as material selection, thickness optimization, layer configuration, signal integrity, thermal management, manufacturability, and compatibility with packaging.