Ultrathin CPU Substrates Manufacturer
Ultrathin CPU Substrates Manufacturer,An ultrathin CPU substrate is an extremely thin platform used for mounting central processing units (CPUs), typically made of silicon. It provides mechanical support and electrical connections, linking the CPU with other parts of the system. Ultrathin CPU substrates are especially important in modern electronic devices, such as smartphones, tablets, and ultra-thin laptops. By reducing the overall thickness and weight of devices, improving thermal management, and allowing for the integration of more advanced features within a smaller form factor, ultrathin CPU substrates significantly enhance device performance and efficiency. This technology requires precise manufacturing processes to ensure the structural integrity and electrical performance of the substrate.
What is an Ultrathin CPU Substrate?
An Ultrathin CPU Substrate refers to a slim, typically silicon-based platform upon which the central processing unit (CPU) of a computer or other electronic device is mounted. This substrate serves as a foundation for the CPU, providing mechanical support and electrical connections between the CPU and the rest of the system.
The term “ultrathin” implies that the substrate is exceptionally thin, often to enable compact designs and to reduce the overall thickness of the device. Ultrathin CPU substrates are commonly used in thin and lightweight laptops, tablets, smartphones, and other portable electronic devices where space is at a premium and slim form factors are desired.
These substrates undergo precise manufacturing processes to ensure high levels of flatness, durability, and electrical performance. They are engineered to efficiently dissipate heat generated by the CPU to prevent overheating and maintain reliable operation. Additionally, ultrathin CPU substrates often incorporate advanced materials and technologies to enhance electrical connectivity and signal transmission between the CPU and other components of the device.
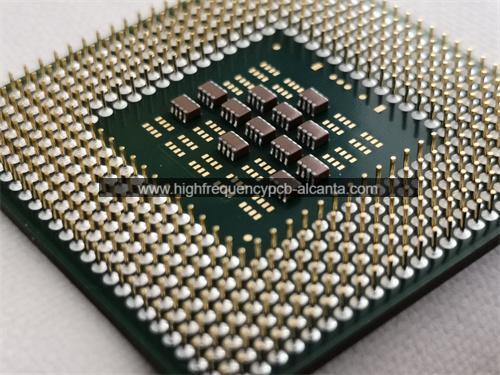
Ultrathin CPU Substrates Manufacturer
What are the Ultrathin CPU Substrate Design Guidelines?
Ultrathin CPU substrate design guidelines encompass a range of considerations aimed at optimizing the performance, reliability, and manufacturability of the substrate. While specific guidelines can vary depending on the manufacturer and intended application, some common principles include:
- Thickness: Ultrathin substrates are typically designed to be as thin as possible while still providing adequate mechanical support and electrical connectivity. Guidelines specify target thickness ranges based on factors such as the size of the CPU package, thermal requirements, and structural integrity.
- Material Selection: The choice of substrate material is critical for achieving desired electrical and mechanical properties. Common materials include silicon, glass, and various types of ceramics. Guidelines may specify material properties such as thermal conductivity, coefficient of thermal expansion, and dielectric constant.
- Thermal Management: Efficient heat dissipation is essential for maintaining CPU performance and reliability. Design guidelines address thermal management strategies such as the incorporation of thermal vias, heat spreaders, and thermal interface materials to facilitate the transfer of heat away from the CPU.
- Electrical Connectivity: Ultrathin substrates must provide reliable electrical connections between the CPU and other components of the system. Guidelines may include recommendations for routing high-speed signals, minimizing signal loss, and optimizing signal integrity through controlled impedance and signal routing techniques.
- Mechanical Stability: Despite their thinness, ultrathin substrates must exhibit sufficient mechanical stability to withstand mechanical stresses during handling, assembly, and operation. Design guidelines may specify requirements for substrate flatness, flexural rigidity, and resistance to warping or bending.
- Manufacturability: Design guidelines should account for the capabilities and limitations of manufacturing processes used to fabricate ultrathin substrates. Considerations may include minimum feature sizes, tolerances, surface finish requirements, and compatibility with standard semiconductor fabrication techniques.
- Reliability and Durability: Ultrathin CPU substrates must meet stringent reliability and durability standards to ensure long-term performance in demanding environments. Guidelines may address factors such as material fatigue, mechanical shock resistance, and resistance to environmental factors such as moisture and chemical exposure.
- Cost Optimization: Design guidelines often aim to strike a balance between performance and cost-effectiveness by identifying opportunities to streamline manufacturing processes, minimize material usage, and reduce waste while still meeting performance requirements.
Overall, adherence to ultrathin CPU substrate design guidelines is essential for achieving optimal performance, reliability, and manufacturability in modern electronic devices. These guidelines evolve over time in response to advances in materials science, manufacturing technology, and the ever-changing demands of the electronics industry.
What is the Ultrathin CPU Substrate Fabrication Process?
The fabrication process for ultrathin CPU substrates involves several steps, each aimed at creating a thin, flat, and mechanically stable platform for mounting the CPU. While specific processes can vary depending on factors such as substrate material, design complexity, and manufacturing capabilities, a generalized overview of the fabrication process might include the following steps:
- Material Selection: The fabrication process begins with the selection of a suitable substrate material based on the desired electrical, mechanical, and thermal properties. Common materials include silicon, glass, and ceramics.
- Substrate Preparation: The chosen substrate material is prepared for processing by cleaning and surface treatment to remove contaminants and improve adhesion for subsequent layers.
- Thin Film Deposition: Thin films of materials such as silicon dioxide (SiO2), silicon nitride (Si3N4), or metals may be deposited onto the substrate using techniques such as chemical vapor deposition (CVD), physical vapor deposition (PVD), or sputtering. These films serve various purposes, such as providing insulation, enhancing electrical conductivity, or serving as etch masks for subsequent patterning steps.
- Photolithography: Photolithography is used to define the patterns and features on the substrate. A photoresist material is applied to the substrate surface, exposed to UV light through a photomask containing the desired pattern, and then developed to selectively remove the photoresist, leaving behind a patterned mask on the substrate.
- Etching: The exposed areas of the substrate are etched away using wet or dry etching techniques, depending on the material and desired feature geometry. This step transfers the pattern from the photoresist mask to the underlying substrate, creating features such as vias, trenches, and interconnects.
- Thin-Film Removal and Planarization: Any remaining photoresist and unwanted thin films are removed from the substrate surface, typically using chemical etching or plasma ashing processes. Planarization techniques such as chemical mechanical polishing (CMP) may be employed to achieve a flat and smooth surface topography.
- Dicing and Singulation: The processed substrate is diced into individual die or chips using sawing or laser cutting techniques. This step separates the substrate into discrete units for further assembly and packaging.
- Quality Control and Testing: The fabricated ultrathin CPU substrates undergo rigorous quality control inspections and electrical testing to ensure that they meet specified performance criteria and reliability standards.
- Packaging and Assembly: The ultrathin CPU substrates are packaged and assembled into electronic devices, typically by mounting the CPU and other components onto the substrate, connecting them with wire bonds or flip-chip interconnects, and encapsulating the assembly with protective materials.
- Final Testing and Inspection: The assembled electronic devices undergo final testing and inspection to verify functionality, performance, and reliability before being shipped to customers.
Throughout the fabrication process, strict process control measures are employed to ensure consistent quality, dimensional accuracy, and reliability of the ultrathin CPU substrates. Advanced manufacturing technologies and equipment are often utilized to achieve high precision and yield rates in the production of these critical components for modern electronic devices.
How do you manufacture an Ultrathin CPU Substrate?
Manufacturing an ultrathin CPU substrate involves a series of intricate steps, leveraging advanced fabrication techniques and precise control measures. Here’s a general overview of the manufacturing process:
- Substrate Selection: Begin by selecting a suitable substrate material based on the required electrical, mechanical, and thermal properties. Common materials include silicon, glass, and various types of ceramics.
- Substrate Preparation: Clean the substrate surface thoroughly to remove any contaminants that could affect subsequent processing steps. Surface treatment techniques may also be applied to enhance adhesion and promote uniform film deposition.
- Thin Film Deposition: Utilize techniques such as chemical vapor deposition (CVD), physical vapor deposition (PVD), or sputtering to deposit thin films onto the substrate surface. These films may include insulating layers (e.g., silicon dioxide), conductive layers (e.g., metals), or other materials tailored to the specific requirements of the CPU substrate design.
- Photolithography:Apply a layer of photoresist onto the substrate surface and use photolithography to define the desired patterns and features. UV light is directed through a photomask containing the desired pattern, selectively exposing the photoresist. After exposure, the photoresist is developed to remove the unexposed areas, leaving behind a patterned mask on the substrate.
- Etching: Etch away the exposed areas of the substrate using wet or dry etching techniques. This step transfers the pattern from the photoresist mask to the underlying substrate, creating features such as vias, trenches, and interconnects.
- Thin-Film Removal and Planarization: Remove any remaining photoresist and unwanted thin films from the substrate surface. Planarization techniques such as chemical mechanical polishing (CMP) may be employed to achieve a flat and smooth surface topography, essential for subsequent processing steps and overall substrate quality.
- Dicing and Singulation: Use sawing or laser cutting techniques to dice the processed substrate into individual die or chips. This step separates the substrate into discrete units for further assembly and packaging.
- Quality Control and Testing: Conduct rigorous quality control inspections and electrical testing to verify that the fabricated substrates meet specified performance criteria and reliability standards. Any defects or deviations from the desired specifications are identified and addressed to ensure consistent quality.
- Packaging and Assembly: Assemble the ultrathin CPU substrates into electronic devices by mounting the CPU and other components onto the substrate, connecting them with wire bonds or flip-chip interconnects, and encapsulating the assembly with protective materials.
- Final Testing and Inspection: Perform final testing and inspection on the assembled electronic devices to validate functionality, performance, and reliability. This ensures that the manufactured products meet customer requirements and industry standards before being released to the market.
Throughout the manufacturing process, stringent process control measures are implemented to maintain high levels of precision, repeatability, and yield. Advanced manufacturing equipment, cleanroom environments, and quality management systems are commonly employed to achieve these goals and produce ultrathin CPU substrates of superior quality and reliability.
How much should an Ultrathin CPU Substrate cost?
The cost of an ultrathin CPU substrate can vary significantly depending on various factors such as the substrate material, manufacturing complexity, size, thickness, and quantity ordered. Generally, ultrathin CPU substrates tend to be more expensive than thicker substrates due to the increased precision and specialized manufacturing processes required to produce them.
Here are some factors that can influence the cost of an ultrathin CPU substrate:
- Material Cost: The cost of the substrate material itself can vary based on factors such as material type (e.g., silicon, glass, ceramics), purity, and availability.
- Manufacturing Complexity: Complex designs with intricate patterns, tight tolerances, and advanced features may require more sophisticated manufacturing processes, driving up production costs.
- Thin-Film Deposition Techniques: Certain thin-film deposition techniques, such as chemical vapor deposition (CVD) or sputtering, can be more expensive due to equipment costs, consumables, and process complexity.
- Photolithography and Etching: Photolithography and etching processes involve expensive equipment, chemicals, and masks, which can contribute to the overall cost of substrate fabrication.
- Quality Control and Testing: Rigorous quality control measures and testing procedures are necessary to ensure that ultrathin CPU substrates meet stringent performance and reliability standards. These additional steps can add to the overall manufacturing cost.
- Volume and Economy of Scale: Larger production volumes typically result in lower per-unit manufacturing costs due to economies of scale. However, initial setup costs and tooling expenses may offset some of these savings for smaller production runs.
- Supplier and Market Dynamics: Pricing can also be influenced by factors such as supplier relationships, market demand, competition, and regional manufacturing costs.
Given these factors, it’s challenging to provide a specific cost estimate for an ultrathin CPU substrate without knowing the detailed specifications and manufacturing requirements. However, it’s not uncommon for ultrathin CPU substrates to cost significantly more than standard thickness substrates due to the specialized nature of their fabrication processes and materials. Generally, customers should expect to pay a premium for the benefits of ultrathin substrates, such as reduced weight, space-saving designs, and enhanced thermal performance.
What is Ultrathin CPU Substrate base material?
The base material for ultrathin CPU substrates can vary depending on the specific requirements of the application and manufacturing process. Some common materials used as the base substrate for ultrathin CPU substrates include:
- Silicon: Silicon is a widely used material for semiconductor substrates due to its excellent electrical properties, mechanical strength, and compatibility with semiconductor manufacturing processes. Silicon substrates can be fabricated into ultrathin layers while maintaining high levels of structural integrity and electrical performance.
- Glass: Glass substrates offer advantages such as transparency, smooth surface finish, and excellent thermal stability. Glass can be processed into ultrathin layers using techniques such as chemical etching or laser ablation, making it suitable for applications where optical transparency or lightweight construction is desired.
- Ceramics: Various types of ceramics, such as alumina (aluminum oxide) or alumina-based ceramics, are used as substrate materials in electronic devices. Ceramics offer high thermal conductivity, chemical resistance, and mechanical strength, making them suitable for ultrathin substrate applications requiring robust performance in harsh environments.
- Polymer Films: Thin polymer films, such as polyimide or liquid crystal polymer (LCP), can be used as flexible substrate materials for ultrathin CPU substrates in applications where flexibility, lightweight construction, or conformal mounting are required. Polymer films can be processed using techniques such as spin coating or lamination to achieve ultrathin thicknesses.
- Metal Foils: In some cases, metal foils such as copper or aluminum may be used as substrate materials for ultrathin CPU substrates. Metal foils offer advantages such as high thermal conductivity, excellent electrical conductivity, and compatibility with soldering processes.
The choice of base material for an ultrathin CPU substrate depends on factors such as electrical performance requirements, thermal management considerations, mechanical stability, and manufacturability. Each material has its own unique properties and characteristics that make it suitable for specific applications and manufacturing processes.
Which company makes Ultrathin CPU Substrate?
Currently, many companies manufacture ultrathin CPU substrates, including major manufacturers such as Intel, TSMC, Samsung Electronics, and UMC. These companies possess advanced manufacturing technologies and equipment, enabling them to produce high-performance, reliable ultrathin CPU substrates to meet the needs of various devices.
For our company, if we have the corresponding manufacturing capabilities and technical expertise, we can also produce ultrathin CPU substrates. Our company can demonstrate our production capabilities in the following ways:
- Advanced Manufacturing Equipment: Our company has advanced semiconductor manufacturing equipment, including chemical vapor deposition (CVD), physical vapor deposition (PVD), photolithography, and etching equipment. These devices allow for precise processing and manufacturing of ultrathin substrates.
- Technical Expertise: Our company has a team of experienced engineers and technical personnel with professional knowledge and skills in design, process development, and production management. They can design and produce ultrathin CPU substrates that meet customer requirements and industry standards.
- Quality Control: Our company places great emphasis on quality control and implements a strict quality management system to ensure product stability and reliability. Through stringent process control, monitoring, and product testing, we can ensure that the quality of ultrathin CPU substrates meets the standards.
- Customer Customization: Our company can carry out custom production based on customer requirements, providing ultrathin CPU substrates that meet specific customer needs. We can produce according to the design specifications and technical requirements provided by customers, ensuring that product performance and quality meet expectations.
In summary, although our company may not have the global leading scale and technical strength of companies like Intel or TSMC, if we have advanced manufacturing equipment, technical expertise, and a quality management system, we can also produce high-quality ultrathin CPU substrates to meet customer needs.
What are the 7 qualities of good customer service?
Good customer service is essential for building and maintaining strong customer relationships, fostering loyalty, and enhancing the overall reputation of a business. Here are seven key qualities of good customer service:
- Responsiveness: Quick and efficient responses to customer inquiries and issues are crucial. Customers appreciate timely answers and solutions to their problems. Being responsive demonstrates that the company values their time and is committed to addressing their needs promptly.
- Empathy: Understanding and acknowledging the customer’s feelings and perspectives can greatly enhance their experience. Empathy involves actively listening to customers, showing genuine concern for their issues, and responding in a way that makes them feel heard and valued.
- Knowledgeability: Customers expect service representatives to be well-informed about the company’s products, services, and policies. Knowledgeable staff can provide accurate information, solve problems effectively, and build trust with customers.
- Professionalism: Maintaining a high level of professionalism in all interactions is vital. This includes being polite, respectful, and courteous, as well as communicating clearly and effectively. Professionalism helps establish credibility and fosters a positive impression of the company.
- Patience: Dealing with customers, especially those who are upset or confused, requires patience. Taking the time to listen carefully, avoid interrupting, and calmly address their concerns can turn a potentially negative experience into a positive one.
- Problem-Solving Skills: Good customer service representatives are adept at identifying problems, exploring potential solutions, and implementing the best course of action. They are resourceful, can think on their feet, and are committed to resolving issues to the customer’s satisfaction.
- Positive Attitude: A positive and friendly demeanor can greatly influence a customer’s experience. Enthusiasm, a can-do attitude, and a willingness to go the extra mile can leave a lasting impression and encourage customers to return.
By embodying these qualities, companies can provide exceptional customer service that not only meets but exceeds customer expectations, leading to increased satisfaction and loyalty.
FAQs
Why are ultrathin CPU substrates important?
Ultrathin CPU substrates are crucial for modern electronic devices, especially portable ones like smartphones, tablets, and ultra-thin laptops. They help reduce the overall thickness of devices, improve thermal management, and enable the integration of more advanced features within a smaller form factor.
What materials are used for ultrathin CPU substrates?
Common materials include silicon, glass, ceramics, and sometimes polymer films. Each material offers different advantages in terms of electrical performance, thermal conductivity, and mechanical strength.
How are ultrathin CPU substrates manufactured?
The manufacturing process typically involves substrate preparation, thin film deposition, photolithography, etching, thin-film removal, planarization, dicing, quality control, and final testing. Advanced techniques such as chemical vapor deposition (CVD) and physical vapor deposition (PVD) are often used.
What are the challenges in manufacturing ultrathin CPU substrates?
Manufacturing challenges include maintaining mechanical stability despite thinness, ensuring efficient thermal management, achieving precise patterning through photolithography and etching, and maintaining high yields despite the complexity of the processes involved.
How does the thickness of the substrate impact device performance?
Thinner substrates help reduce the overall thickness and weight of electronic devices, improve heat dissipation, and allow for more compact and efficient designs. However, they also require precise manufacturing to maintain structural integrity and electrical performance.
What applications benefit most from ultrathin CPU substrates?
Applications that benefit include high-performance computing devices, mobile devices (smartphones, tablets), ultra-thin laptops, wearable technology, and other compact electronic devices where space is at a premium and performance is critical.
How does an ultrathin CPU substrate improve thermal management?
Ultrathin CPU substrates improve thermal management by reducing the distance heat must travel to be dissipated, allowing for more efficient heat transfer away from the CPU. This helps maintain optimal operating temperatures and improves device performance and longevity.
What is the typical cost of an ultrathin CPU substrate?
The cost can vary widely based on material, manufacturing complexity, size, thickness, and order volume. Generally, ultrathin CPU substrates are more expensive than standard ones due to the advanced processes and materials required.
Can ultrathin CPU substrates be customized?
Yes, many manufacturers offer customization options to meet specific customer requirements, including tailored thickness, material choices, and specific design features to optimize performance for particular applications.