Ultra Thin Multilayer Package Substrates Manufacturer
Ultra Thin Multilayer Package Substrates Manufacturer,Ultra Thin Multilayer Package Substrates (UTMPS) are advanced substrates used in electronic packaging, featuring an ultra-thin profile and multiple layers for mounting and interconnecting semiconductor devices. They offer compact size, high-density interconnects, and enhanced thermal management, making them ideal for applications with stringent space constraints. UTMPS enable the development of smaller, lighter, and more efficient electronic devices, including smartphones, wearables, automotive electronics, and medical devices. With their superior performance and reliability, UTMPS play a crucial role in driving innovation and miniaturization in the electronics industry.
What are Ultra Thin Multilayer Package Substrates (UTMPS)?
Ultra Thin Multilayer Package Substrates (UTMPS) are advanced substrates used in electronic packaging, particularly in the semiconductor industry. These substrates are characterized by their extremely thin profile and multiple layers, providing a compact and efficient solution for mounting and interconnecting semiconductor devices.
UTMPS typically consist of multiple layers of insulating materials such as organic or inorganic films, with conductive traces patterned on each layer to create complex wiring structures. These substrates offer high-density interconnects, enabling the integration of numerous semiconductor components in a small footprint.
The thin profile of UTMPS reduces the overall size and weight of electronic devices, making them ideal for applications where space constraints are critical, such as mobile devices, wearable electronics, and automotive electronics. Additionally, the multilayer design allows for enhanced signal integrity and thermal management, contributing to improved performance and reliability of electronic systems.
UTMPS fabrication involves advanced manufacturing techniques such as thin film deposition, photolithography, and etching processes. These substrates can be customized to meet specific design requirements, including different material compositions, layer thicknesses, and interconnect configurations.
Overall, Ultra Thin Multilayer Package Substrates play a vital role in enabling the development of compact, high-performance electronic devices across various industries, driving innovation and technological advancement.
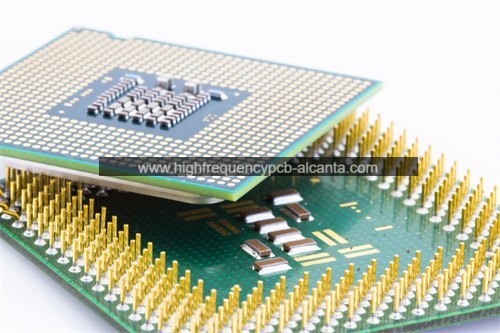
Ultra Thin Multilayer Package Substrates Manufacturer
What are the UTMPS Design Guidelines?
Designing Ultra Thin Multilayer Package Substrates (UTMPS) involves several key guidelines to ensure optimal performance and reliability. Some common design considerations include:
- Layer Stackup Design: Define the number of layers, material selection for each layer (dielectric and conductive), and their respective thicknesses. The layer stackup should balance electrical performance, thermal management, and mechanical integrity.
- Signal Integrity: Minimize signal loss, crosstalk, and electromagnetic interference (EMI) by carefully designing signal traces, vias, and ground/power planes. High-speed signal paths should be impedance-controlled to maintain signal integrity.
- Thermal Management: Incorporate thermal vias, thermal pads, and metal heatsinks to efficiently dissipate heat generated by semiconductor devices. Proper thermal management is crucial for preventing overheating and maintaining long-term reliability.
- Manufacturability: Design for manufacturability by considering the capabilities and limitations of the fabrication process. Ensure that design features such as trace widths, spacing, and via sizes are compatible with the chosen manufacturing technology.
- Package Size and Form Factor: Optimize the package size and form factor to meet the space constraints of the target application while accommodating all necessary components and interfaces. Compact designs are desirable for portable and miniaturized devices.
- Reliability Considerations: Enhance reliability by designing for mechanical robustness, thermal stability, and resistance to environmental factors such as moisture, humidity, and thermal cycling. Conduct thorough reliability assessments and testing during the design phase.
- Electrical Testing Provisions: Include test pads, test points, or built-in self-test (BIST) circuitry to facilitate electrical testing and debugging during manufacturing and assembly processes. Ensure accessibility to critical signals for functional testing and troubleshooting.
- Compliance and Standards: Ensure compliance with relevant industry standards and regulations governing electronic packaging, such as IPC (Association Connecting Electronics Industries) standards, JEDEC (Joint Electron Device Engineering Council) specifications, and RoHS (Restriction of Hazardous Substances) directives.
By adhering to these design guidelines, engineers can develop Ultra Thin Multilayer Package Substrates that meet the performance, reliability, and manufacturability requirements of advanced electronic systems.
What is the UTMPS Fabrication Process?
The fabrication process for Ultra Thin Multilayer Package Substrates (UTMPS) involves several key steps, including material selection, substrate preparation, layer deposition, patterning, and assembly. Here’s an overview of the typical fabrication process:
- Material Selection: Choose suitable materials for the substrate layers based on their electrical, thermal, and mechanical properties. Common materials include organic films (e.g., polyimide, BT resin) or inorganic materials (e.g., glass, ceramic).
- Substrate Preparation: Prepare the substrate material by cleaning and surface treatment to ensure proper adhesion and compatibility with subsequent processing steps.
- Layer Deposition: Deposit thin films of dielectric and conductive materials onto the substrate using techniques such as physical vapor deposition (PVD), chemical vapor deposition (CVD), or electroplating. Dielectric layers insulate conductive traces, while conductive layers form the wiring structure.
- Patterning: Define the desired circuit pattern and vias using photolithography and etching processes. Photolithography involves applying a photoresist layer, exposing it to UV light through a photomask, and developing it to create a patterned mask. Etching removes material from the exposed areas to define the circuit features and vias.
- Via Formation: Create vias (plated or non-plated) to establish electrical connections between different layers. Vias are typically formed using laser drilling or mechanical drilling followed by metallization and plating processes.
- Build-Up Process:Repeat the deposition, patterning, and via formation steps to build multiple layers of interconnects and dielectric insulation. Each iteration adds complexity and functionality to the substrate.
- Surface Finish: Apply surface finishes such as solder mask and surface treatment (e.g., ENIG – Electroless Nickel Immersion Gold) to protect the substrate and facilitate soldering of components during assembly.
- Quality Control and Testing: Perform rigorous quality control inspections and electrical testing to ensure the integrity, reliability, and functionality of the fabricated UTMPS. This may include electrical continuity testing, impedance measurements, and visual inspections.
- Assembly:Mount semiconductor devices, passive components, and other electronic elements onto the UTMPS using surface mount technology (SMT) or flip-chip bonding techniques. The assembled UTMPS can then be integrated into electronic systems or packages.
Overall, the fabrication process for UTMPS requires precise control of materials, deposition techniques, and patterning processes to achieve the desired electrical performance, thermal management, and mechanical reliability. Collaboration between design engineers and manufacturing experts is essential to optimize the fabrication process and meet the requirements of specific applications.
How do you manufacture UTMPS?
Manufacturing Ultra Thin Multilayer Package Substrates (UTMPS) involves a series of intricate steps and specialized equipment. Here’s a generalized overview of the manufacturing process:
- Design and Layout: The manufacturing process begins with the design of the UTMPS layout. Engineers use computer-aided design (CAD) software to create the layout, specifying the arrangement of conductive traces, vias, and component mounting areas.
- Material Selection: Select appropriate substrate materials based on the desired electrical, thermal, and mechanical properties. Common materials include organic films (such as polyimide or BT resin) or inorganic materials (like glass or ceramic).
- Substrate Preparation: Clean and prepare the substrate material to ensure proper adhesion and surface smoothness. Surface treatments may include plasma cleaning, chemical treatments, or mechanical polishing.
- Layer Deposition: Deposit thin films of dielectric and conductive materials onto the substrate using deposition techniques such as physical vapor deposition (PVD), chemical vapor deposition (CVD), or electroplating. These layers form the basis of the substrate’s wiring structure.
- Patterning:Define the circuit pattern and via locations using photolithography and etching processes. Photolithography involves applying a photosensitive resist layer, exposing it to UV light through a photomask, and developing it to create a patterned mask. Etching removes material from the exposed areas to define the circuit features and vias.
- Via Formation: Create vias to establish electrical connections between different layers. Vias can be formed using techniques like laser drilling or mechanical drilling, followed by metallization and plating processes to ensure conductivity.
- Build-Up Process: Repeat the layer deposition, patterning, and via formation steps to build multiple layers of interconnects and dielectric insulation. Each iteration adds complexity and functionality to the substrate.
- Surface Finish: Apply surface finishes such as solder mask and surface treatment (e.g., Electroless Nickel Immersion Gold – ENIG) to protect the substrate and facilitate soldering of components during assembly.
- Quality Control and Testing: Conduct rigorous quality control inspections and electrical testing to ensure the integrity and reliability of the fabricated UTMPS. This may include visual inspections, electrical continuity testing, impedance measurements, and other tests to verify performance.
- Assembly: Mount semiconductor devices, passive components, and other electronic elements onto the UTMPS using surface mount technology (SMT) or flip-chip bonding techniques. The assembled UTMPS can then be integrated into electronic systems or packages.
Throughout the manufacturing process, strict quality control measures and adherence to design specifications are essential to ensure the reliability and functionality of the UTMPS. Collaboration between design engineers, manufacturing specialists, and quality assurance teams is crucial for optimizing the manufacturing process and meeting the requirements of specific applications.
How much should UTMPS cost?
The cost of Ultra Thin Multilayer Package Substrates (UTMPS) can vary significantly depending on several factors, including:
- Material Costs: The cost of the substrate materials, including dielectric films, conductive layers, surface finishes, and other components used in the manufacturing process, can greatly influence the overall cost.
- Manufacturing Complexity: The complexity of the UTMPS design and the manufacturing process required to produce it will impact the cost. More intricate designs with higher layer counts, finer features, and tighter tolerances may require more time and resources, thus increasing manufacturing costs.
- Volume and Scale: Economies of scale play a significant role in determining the cost of UTMPS. Larger production volumes typically result in lower per-unit manufacturing costs due to efficiencies in material procurement, equipment utilization, and labor.
- Technology and Equipment: The use of advanced manufacturing technologies and equipment, such as high-resolution lithography systems, precision etching machines, and automated assembly lines, can contribute to higher upfront capital costs, which may be reflected in the final product price.
- Quality and Reliability Requirements: Meeting stringent quality and reliability standards, such as automotive or aerospace specifications, may necessitate additional testing, inspection, and quality control measures, adding to the overall cost.
- Customization and Specialized Features: Customized designs, special features, or unique requirements specified by the customer can increase the cost of UTMPS production due to additional engineering efforts, tooling costs, and manufacturing complexities.
- Market Dynamics: Market demand, competition, and supply chain factors can also influence pricing. Prices may fluctuate based on market conditions, industry trends, and competitive pressures.
Given these factors, it’s challenging to provide a specific cost estimate for UTMPS without detailed information about the specific requirements, volume, and manufacturing process. Generally, UTMPS costs can range from a few dollars per unit for simpler designs and smaller quantities to tens or hundreds of dollars per unit for complex designs and larger volumes. Collaborating with manufacturers to assess your specific needs and obtain customized quotes is essential for determining accurate cost estimates.
What is UTMPS base material?
The base material for Ultra Thin Multilayer Package Substrates (UTMPS) can vary depending on the specific requirements of the application and the desired properties of the substrate. However, some common base materials used in UTMPS manufacturing include:
- Polyimide (PI): Polyimide films are a popular choice for UTMPS due to their excellent thermal stability, chemical resistance, and flexibility. PI substrates can withstand high temperatures encountered during fabrication processes and offer good electrical insulation properties.
- Bismaleimide Triazine (BT) Resin: BT resin-based substrates are known for their low dielectric constant, low moisture absorption, and good mechanical strength. They are often used in high-frequency applications requiring stable electrical performance.
- Liquid Crystal Polymer (LCP):LCP substrates offer exceptional dimensional stability, low moisture absorption, and high-temperature resistance. They are suitable for demanding applications where reliability and miniaturization are critical.
- Rigid-Flex Substrates: Some UTMPS designs incorporate rigid-flex substrates, which combine rigid sections (typically made of materials like FR-4 or BT resin) with flexible sections (such as polyimide or LCP). Rigid-flex UTMPS offer the advantages of both rigid and flexible substrates, enabling complex designs and space-saving configurations.
- Glass or Ceramic Substrates: In certain applications requiring high thermal conductivity, mechanical strength, and dimensional stability, glass or ceramic-based substrates may be used. These materials offer excellent thermal management capabilities but may be more challenging to fabricate due to their brittleness.
The choice of base material depends on various factors such as electrical performance requirements, thermal management needs, mechanical properties, cost considerations, and compatibility with manufacturing processes. Design engineers typically evaluate these factors to select the most suitable base material for a given UTMPS application.
Which company manufactures UTMPS?
Manufacturers of UTMPS include numerous companies such as Hitachi Chemical, Murata Manufacturing, Foxconn, Samsung Electronics, and China Electric Corporation. These companies have rich experience and advanced manufacturing technologies in the field of UTMPS, providing high-quality products for the electronics industry.
For our company, as a company specializing in the electronics manufacturing field, we have the capability to produce UTMPS. We have advanced manufacturing equipment and a skilled technical team to meet various requirements for UTMPS from our customers.
Firstly, we have advanced process technology and rich experience to design and manufacture high-performance UTMPS that meet customer requirements. Our technical team possesses deep professional knowledge and can customize designs according to customer specifications and ensure product quality and reliability.
Secondly, we have advanced production equipment and precision processing technology to efficiently manufacture UTMPS. Our production lines are equipped with the latest automation equipment and quality control systems to ensure the accuracy and consistency of products during the manufacturing process.
Furthermore, we emphasize quality management and customer service, always putting customer needs first. We strictly implement a quality management system, conducting strict checks at every stage from raw material procurement to finished product delivery, ensuring that products meet customer requirements and industry standards.
Finally, we have flexible production capabilities and rapid response capabilities to provide customized solutions according to customer needs and deliver high-quality products in a timely manner. We maintain close communication and cooperation with customers to meet their evolving needs.
In summary, as a professional electronics manufacturing company, we have the technical strength and production capabilities to produce UTMPS. We will adhere to the principle of quality first and customer foremost, providing customers with high-quality products and services to create a better future together.
What are the 7 qualities of good customer service?
Good customer service is essential for building strong relationships with customers and fostering loyalty. Here are seven qualities that characterize good customer service:
- Responsiveness: Good customer service involves being prompt and responsive to customer inquiries, requests, and concerns. Whether through phone, email, or in-person interactions, customers appreciate quick and efficient assistance.
- Empathy: Empathy is the ability to understand and relate to the emotions and experiences of customers. Good customer service representatives listen actively, demonstrate empathy, and show genuine concern for the customer’s needs and feelings.
- Knowledgeability: Customers expect customer service representatives to be knowledgeable about the products or services offered by the company. Good customer service involves having a deep understanding of the company’s offerings and being able to provide accurate and helpful information to customers.
- Professionalism: Professionalism encompasses traits such as courtesy, politeness, and professionalism in communication and behavior. Good customer service representatives maintain a professional demeanor at all times and strive to uphold the company’s reputation.
- Problem-solving skills: Good customer service involves effectively addressing and resolving customer issues and complaints. Customer service representatives should have strong problem-solving skills, the ability to think critically, and the initiative to find solutions that satisfy the customer.
- Consistency: Consistency is key to delivering good customer service across all interactions and touchpoints. Customers expect consistent levels of service quality, regardless of the channel or representative they interact with. Consistency builds trust and confidence in the company.
- Personalization: Personalization involves tailoring the customer service experience to the individual preferences and needs of each customer. Good customer service representatives take the time to understand the customer’s unique situation and provide personalized assistance and recommendations.
By embodying these qualities, companies can deliver exceptional customer service experiences that leave a positive impression on customers and drive loyalty and satisfaction.
FAQs
What are the advantages of UTMPS?
UTMPS offer several advantages, including compact size, high-density interconnects, enhanced signal integrity, improved thermal management, and reliability. They are well-suited for applications with space constraints, such as mobile devices, wearables, and automotive electronics.
What materials are used in UTMPS?
Common materials used in UTMPS include polyimide, bismaleimide triazine (BT) resin, liquid crystal polymer (LCP), and glass or ceramic substrates. These materials offer different electrical, thermal, and mechanical properties to meet various application requirements.
How are UTMPS manufactured?
The manufacturing process for UTMPS involves steps such as material selection, substrate preparation, layer deposition, patterning, via formation, build-up process, surface finish, quality control, and assembly. It requires advanced fabrication techniques and equipment.
What are the applications of UTMPS?
UTMPS find applications in a wide range of electronic devices and systems, including smartphones, tablets, laptops, IoT devices, automotive electronics, medical devices, and aerospace systems. They enable the miniaturization and high performance of electronic components.
How can I order or inquire about UTMPS?
To order or inquire about UTMPS, you can contact manufacturers or suppliers specializing in electronic packaging solutions. Provide details about your requirements, such as substrate specifications, quantity, and delivery timeline, to receive quotes and assistance.
What are the considerations when designing with UTMPS?
When designing with UTMPS, considerations include layer stackup design, signal integrity, thermal management, manufacturability, package size and form factor, reliability, compliance with standards, and electrical testing provisions. Collaboration with experienced designers and manufacturers is recommended.