Ultra Thin Multilayer High Speed PCBs Manufacturer
Ultra Thin Multilayer High Speed PCBs Manufacturer,Ultra Thin Multilayer High Speed PCBs are cutting-edge electronic circuit boards engineered with multiple ultra-thin layers of conducting material and insulating substrate. These PCBs excel in transmitting high-frequency signals with minimal loss and distortion, crucial for compact electronic devices requiring rapid data transfer. Utilizing advanced materials and precise manufacturing techniques, they enable the seamless integration of complex electronic components in space-constrained applications like smartphones, wearable technology, and high-performance computing systems. Ultra Thin Multilayer High Speed PCBs represent the pinnacle of modern electronic engineering, driving innovation in industries reliant on speed, efficiency, and reliability.
What is an Ultra Thin Multilayer High Speed PCB?
An Ultra Thin Multilayer High Speed PCB (Printed Circuit Board) refers to a highly sophisticated circuit board designed with multiple layers of conducting material and insulating substrate, manufactured to be exceptionally thin and capable of supporting high-speed electronic signals. These PCBs are crucial in advanced electronic devices where space is limited and performance demands are high, such as in smartphones, wearable technology, and high-performance computing systems.
The “ultra thin” aspect of these PCBs usually implies a thickness that can be significantly less than the standard 1.6 mm, often around 0.4 mm or even less. This reduced thickness helps in minimizing the space taken by electronic assemblies, enabling more compact and sleek device designs.
“Multilayer” indicates that the PCB comprises multiple layers of copper sheets separated by insulating material, which are laminated together. Each layer can carry different parts of the electronic circuit, such as power, ground, and signal layers, allowing for complex circuit designs that can handle multiple functions in a very compact area.
The “high speed” component of these PCBs addresses their capability to handle high-speed electronic signals, which is essential for the performance of modern electronic devices. This is achieved through careful design of the trace layout to minimize signal degradation and interference, as well as the use of materials that maintain signal integrity at high frequencies.
Overall, Ultra Thin Multilayer High Speed PCBs are critical in today’s electronic industry, pushing the limits of how small and efficient electronic devices can be while enhancing their functionality and connectivity.
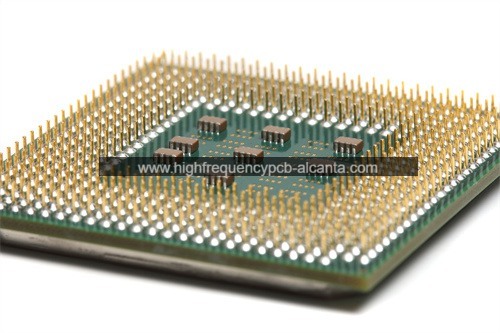
Ultra Thin Multilayer High Speed PCBs Manufacturer
What are the Ultra Thin Multilayer High Speed PCB Design Guidelines?
Designing Ultra Thin Multilayer High Speed PCBs involves complex considerations to ensure functionality, reliability, and manufacturability. Here are key guidelines for designing these sophisticated PCBs:
- Material Selection:Choose materials that have good dielectric properties and are stable under thermal stress. For high-speed applications, low-loss materials help maintain signal integrity. The choice of core and prepreg materials needs to address both electrical performance and mechanical stability in ultra-thin configurations.
- Stackup Design: A well-planned stackup is crucial for controlling impedance and reducing cross-talk. The stackup should optimize the distribution of signal, ground, and power planes to shield high-speed traces and minimize loop areas, which helps in reducing electromagnetic interference (EMI).
- Trace Geometry: Control of impedance is crucial in high-speed circuits, which involves precise calculations and adjustments of trace width and spacing according to the board’s dielectric properties and thickness. The use of differential pairs for high-speed signal transmission should be carefully designed to maintain consistent impedance and minimize crosstalk and noise.
- Signal Integrity Analysis: Use simulation tools to analyze signal integrity issues like reflection, crosstalk, and ground bounce. This is particularly important in ultra-thin multilayer boards where the proximity of layers can influence signal paths and integrity.
- Thermal Management: Managing heat in ultra-thin PCBs is challenging due to the reduced volume for heat dissipation. Thermal vias, adequate spacing for heat-producing components, and possibly the integration of heat sinks or thermal pads should be considered.
- Via Design:Utilize microvias and buried vias to save space and reduce signal path distances. In high-speed design, the impact of vias on signal integrity (such as via stubs causing reflection and distortion) must be minimized. This can involve back-drilling techniques to remove unused portions of vias.
- Component Placement and Routing: Minimize the length of high-speed signal paths to reduce delays and potential for interference. Place critical components first, such as CPUs or high-speed transceivers, and route their connections with minimal lengths and bends. Maintain consistent return paths to avoid signal integrity problems.
- EMI Considerations: Shielding and grounding are pivotal. Design techniques like surrounding sensitive traces with ground and using guard traces can help mitigate EMI. Additionally, careful placement of decoupling capacitors close to IC power pins is essential.
- Manufacturing Constraints: Consult with PCB manufacturers early in the design process to understand their capabilities and limitations, particularly concerning layer alignment, trace and space tolerances, and via placement. Ultra-thin boards are more susceptible to warping and handling issues during manufacturing.
- Testing and Prototyping: Given the complexity and cost associated with ultra-thin multilayer high-speed PCBs, extensive testing and iterative prototyping are necessary to address unforeseen design challenges and ensure performance specifications are met.
Following these guidelines helps in achieving a reliable, functional, and manufacturable ultra-thin multilayer high-speed PCB, essential for today’s compact and high-performance electronic devices.
What is the Ultra Thin Multilayer High Speed PCB Fabrication Process?
The fabrication process for Ultra Thin Multilayer High Speed PCBs involves several steps, each critical for achieving the desired electrical performance, mechanical stability, and reliability. Here’s an overview of the typical fabrication process:
- Design Preparation: This phase involves creating the PCB layout using specialized PCB design software. Design considerations include stackup definition, trace routing, component placement, and signal integrity analysis. Design files are then generated, including Gerber files, drill files, and NC drill files.
- Material Selection: Select appropriate materials for the PCB stackup based on electrical and mechanical requirements. This includes choosing thin laminates with controlled dielectric constants and low-loss tangent properties suitable for high-speed signals.
- Prepreg and Core Preparation: Prepreg (pre-impregnated resin) and core materials are cut to size according to the PCB stackup design. These materials are typically thin and require precise cutting to ensure uniformity and accuracy during lamination.
- Drilling: Precision drilling is performed to create holes for vias, through-hole components, and interconnections between layers. For ultra-thin PCBs, microvia drilling techniques are commonly used to create small-diameter holes with high aspect ratios.
- Through-hole Plating: Through-hole plating involves depositing conductive material (typically copper) inside the drilled holes to establish electrical connections between layers. This step is crucial for ensuring continuity and conductivity throughout the PCB.
- Lamination:The individual layers of prepreg and core materials are stacked together with copper foils and laminated under heat and pressure. This process bonds the layers together to form a multilayer PCB structure.
- Etching: Copper traces and pads are defined on each layer using a chemical etching process or subtractive manufacturing technique. This involves applying a protective mask (usually photoresist) to the copper surface, exposing it to UV light through the PCB artwork, and then etching away the unprotected copper using an appropriate etchant solution.
- Surface Finish: Surface finish options such as HASL (Hot Air Solder Leveling), ENIG (Electroless Nickel Immersion Gold), or OSP (Organic Solderability Preservatives) are applied to protect exposed copper surfaces, provide solderability, and enhance reliability during assembly.
- Solder Mask Application: A solder mask layer is applied over the PCB surface to insulate copper traces, prevent solder bridges during assembly, and protect the board from environmental factors such as moisture and contamination. Openings are created in the solder mask to expose component pads and vias.
- Silkscreen Printing: Component designators, polarity markings, and other identifying information are printed onto the PCB surface using a silkscreen printing process. This step helps facilitate assembly and troubleshooting of the PCB.
- Testing and Inspection: The fabricated PCB undergoes electrical testing, including continuity checks, impedance measurements, and signal integrity testing, to ensure it meets design specifications. Visual inspection is also performed to identify any defects or irregularities in the fabrication process.
- Final Processing: After testing and inspection, the PCBs are routed and separated from the panel, and any remaining processing steps, such as edge profiling or surface coating, are completed. The finished PCBs are then ready for assembly into electronic products.
Throughout the fabrication process, strict quality control measures are implemented to ensure the integrity and reliability of the Ultra Thin Multilayer High Speed PCBs, meeting the demanding requirements of modern electronic devices.
How do you Manufacture an Ultra Thin Multilayer High Speed PCB?
Manufacturing an Ultra Thin Multilayer High Speed PCB involves a series of specialized processes tailored to meet the stringent requirements of thinness, high-speed signal transmission, and multilayer complexity. Here’s a detailed outline of the typical manufacturing steps:
- Design Preparation: Begin with the PCB layout design phase using specialized software. Ensure the design accounts for stackup configuration, trace routing for high-speed signals, and component placement considerations.
- Material Selection: Choose thin laminate materials with controlled dielectric properties suitable for high-speed signals. Also, select appropriate core materials and prepregs that provide mechanical stability and facilitate multilayer construction.
- Panelization: Arrange multiple PCB designs onto a larger panel to optimize material usage and facilitate manufacturing efficiency. Panelization also helps ensure uniformity across multiple PCBs during fabrication.
- Drilling: Precision drill small-diameter holes for vias and interconnections between layers. Use advanced drilling techniques such as laser drilling or mechanical drilling with high aspect ratios to accommodate the ultra-thin nature of the PCB.
- Through-hole Plating: Plate the drilled holes with conductive material to establish electrical connections between layers. Electroplating or electroless plating methods are commonly used to deposit copper or other conductive metals inside the vias.
- Layer Lamination:Stack the drilled and plated layers together with prepregs and copper foils according to the stackup configuration. Apply heat and pressure to laminate the layers into a unified multilayer structure, ensuring proper bonding and registration.
- Etching: Define copper traces and pads on each layer using chemical etching or subtractive manufacturing techniques. Protect the desired copper features with a photoresist mask and selectively etch away the excess copper using an etchant solution.
- Surface Finish: Apply surface finish coatings such as ENIG (Electroless Nickel Immersion Gold), HASL (Hot Air Solder Leveling), or OSP (Organic Solderability Preservatives) to protect exposed copper surfaces, enhance solderability, and improve reliability during assembly.
- Solder Mask Application: Apply solder mask ink over the PCB surface, leaving openings for exposed copper features. The solder mask protects copper traces from oxidation, prevents solder bridging during assembly, and provides insulation.
- Silkscreen Printing: Print component designators, polarity markings, and other identification information onto the PCB surface using a silkscreen printing process. This step aids in component assembly and PCB troubleshooting.
- Testing and Inspection: Perform electrical testing, including continuity checks, impedance measurements, and signal integrity testing, to verify the PCB meets design specifications. Conduct visual inspection to identify any defects or irregularities in the manufacturing process.
- Routing and Separation: After testing and inspection, rout individual PCBs from the panel and separate them. Trim excess material and perform final processing steps such as edge profiling or surface coating as necessary.
- Quality Assurance:Implement rigorous quality control measures throughout the manufacturing process to ensure the integrity and reliability of the Ultra Thin Multilayer High Speed PCBs. Adhere to industry standards and customer specifications to deliver high-quality products.
By following these manufacturing steps with precision and attention to detail, you can produce Ultra Thin Multilayer High Speed PCBs that meet the demanding requirements of modern electronic applications.
How much should an Ultra Thin Multilayer High Speed PCB cost?
The cost of an Ultra Thin Multilayer High Speed PCB can vary widely depending on several factors, including:
- Complexity of Design: The complexity of the PCB design, including the number of layers, density of components, and intricacy of the routing, significantly influences the cost. More complex designs require advanced manufacturing processes and may involve higher material and labor costs.
- Materials Used: The choice of materials, such as laminate types, copper thickness, and surface finish options, affects the overall cost. High-performance materials designed for high-speed applications typically come at a premium price compared to standard materials.
- Manufacturing Process: Advanced manufacturing processes, such as laser drilling for microvias or sequential lamination for multilayer construction, incur additional costs compared to conventional techniques. The use of specialized equipment and expertise contributes to the overall manufacturing cost.
- Quantities Ordered: Economies of scale apply to PCB manufacturing, meaning larger production quantities often result in lower per-unit costs due to optimized manufacturing efficiency and material utilization.
- Turnaround Time: Expedited or rush orders typically incur higher costs to accommodate accelerated production schedules and prioritize resources accordingly.
- Additional Services: Additional services such as design validation, electrical testing, and quality assurance measures may add to the overall cost but are essential for ensuring the reliability and functionality of the PCB.
- Supplier and Location: PCB manufacturing costs can vary based on the chosen supplier and their location. Factors such as labor rates, overhead costs, and shipping expenses can influence the final price.
As a rough estimate, the cost of an Ultra Thin Multilayer High Speed PCB can range from a few dollars to several hundred dollars or more per square inch, depending on the aforementioned factors. For accurate pricing, it’s advisable to consult with PCB manufacturers and provide detailed specifications of your design requirements. Additionally, obtaining quotes from multiple suppliers allows for comparison and helps identify the most cost-effective option while meeting quality standards.
What is Ultra Thin Multilayer High Speed PCB Base Material?
The choice of base material for Ultra Thin Multilayer High Speed PCBs is critical for achieving the desired electrical performance, mechanical stability, and reliability. Several materials are commonly used in the construction of these PCBs:
- Thin Core Laminates: These are thin dielectric substrates made of reinforced epoxy resin with woven glass fabric (FR-4) or other materials. They provide mechanical support and insulation between copper layers. Thin core laminates are available in various thicknesses to accommodate ultra-thin PCB designs.
- Prepregs: Prepregs are layers of uncured resin with reinforcing materials such as woven glass or aramid fibers. They are used to bond copper layers together during lamination. Prepregs contribute to the overall thickness and mechanical strength of the PCB.
- High-Speed Laminate Materials: Specialized laminate materials engineered for high-speed applications offer low dielectric constant (Dk) and low dissipation factor (Df) to minimize signal loss and distortion at high frequencies. Examples include materials based on polytetrafluoroethylene (PTFE) or liquid crystal polymer (LCP).
- Rogers Corporation Materials: Rogers Corporation offers a range of high-frequency laminates suitable for high-speed PCBs, such as RO4000® series and RO3000® series. These materials feature low-loss properties and consistent electrical performance across a wide frequency range.
- DuPont™ Pyralux® Materials: DuPont™ Pyralux® flexible laminates are used in flexible and rigid-flex PCB applications. These materials offer excellent flexibility, thermal stability, and reliability, making them suitable for ultra-thin multilayer PCBs in compact electronic devices.
- Polyimide Films: Polyimide films are used as substrates in flexible PCBs and rigid-flex PCBs. They offer high-temperature resistance, excellent dimensional stability, and good electrical properties, making them suitable for applications requiring flexibility and thinness.
When selecting a base material for Ultra Thin Multilayer High Speed PCBs, consider factors such as dielectric properties, thermal performance, mechanical strength, dimensional stability, and cost. Collaboration with PCB manufacturers and material suppliers can help identify the most suitable base material for your specific application requirements.
Which Company Makes Ultra Thin Multilayer High Speed PCBs?
Our company has the capability to manufacture Ultra Thin Multilayer High Speed PCBs. Here are our advantages and capabilities:
- Advanced Manufacturing Technology: We employ state-of-the-art manufacturing technology, including laser drilling, microvia, and sequential lamination techniques, to produce high-density interconnect (HDI) and ultra-thin multilayer PCBs. Our production equipment and processes ensure high precision and reliability.
- High-Quality Raw Materials: We select high-performance base materials such as FR-4, Rogers high-frequency materials, and DuPont™ Pyralux® flexible materials to meet high-speed signal transmission and strict electrical performance requirements. These materials have low dielectric constants and low dissipation factors, helping to reduce signal loss and distortion.
- Strict Quality Control:We implement rigorous quality control measures to ensure every PCB undergoes comprehensive electrical testing and visual inspection. We use advanced testing equipment such as flying probe testers and automated optical inspection (AOI) systems to ensure products meet customer specifications and standards.
- Flexible Production Capacity: We have flexible production capacity to handle small or large volume production according to customer needs. Whether it’s rapid prototyping or mass production, we provide high-quality products and timely delivery.
- Customized Services:We offer customized services, working closely with customers to understand their specific requirements and application scenarios. We can provide optimized PCB designs and manufacturing solutions tailored to customer design requirements to ensure product performance and reliability.
In summary, we not only have the technical expertise and capability to manufacture Ultra Thin Multilayer High Speed PCBs, but also offer high-quality materials, strict quality control, and flexible production services to meet various high-demand electronic application requirements. If you have any related needs, please feel free to contact us, and we will provide professional solutions.
What are the 7 Qualities of Good Customer Service?
Good customer service is crucial for business success, fostering customer loyalty and enhancing overall satisfaction. Here are seven key qualities that define good customer service:
- Empathy: Understanding and genuinely sharing the feelings of another person is central to good customer service. It involves recognizing the customer’s perspective and responding to their needs and frustrations with sensitivity and understanding.
- Responsiveness:Customers expect timely and efficient service. Responsiveness means addressing customer inquiries, concerns, and complaints quickly and effectively. This not only solves problems but also shows that the business values customer time and satisfaction.
- Communication: Clear and effective communication is essential. This includes not only the ability to listen actively but also to convey information in a straightforward and understandable manner. It’s important for service representatives to avoid jargon and be concise yet thorough in their interactions.
- Knowledge: A deep understanding of the product or service is necessary to answer questions and resolve issues effectively. Customers rely on customer service for accurate information and expect representatives to be well-informed and competent.
- Patience: Dealing with a wide range of customer personalities and issues requires patience. Good customer service professionals stay calm and collected, even when handling difficult or irate customers, showing that they respect and value customer concerns.
- Problem-solving skills: Effective problem-solving involves understanding the issue, identifying solutions, and implementing them efficiently. Good customer service means not just addressing the symptoms of a problem but finding and fixing the root cause.
- Proactivity: Anticipating customer needs and addressing them before they turn into problems is a hallmark of exceptional customer service. Being proactive can also mean following up with customers to ensure their satisfaction after a query has been resolved.
Together, these qualities ensure a positive, productive, and memorable customer service experience that can significantly impact customer loyalty and your brand’s reputation.
FAQs
What materials are used to make these PCBs?
Common materials include high-performance laminates like FR-4, polyimide, and specialized high-speed materials such as Rogers or DuPont laminates. These materials are chosen for their low dielectric losses and reliable performance at high frequencies.
What challenges are involved in manufacturing these PCBs?
The manufacturing of ultra-thin multilayer high-speed PCBs involves several challenges, including precise layer alignment, avoiding material warpage, ensuring adequate thermal management, and maintaining integrity of very fine features during production processes such as drilling, etching, and plating.
How are these PCBs tested for quality and performance?
Testing methods include electrical tests like time-domain reflectometry (TDR) for impedance matching, automated optical inspection (AOI) for checking layer alignment and etching quality, as well as various stress tests to ensure long-term reliability under different environmental conditions.
What are the key design considerations for these PCBs?
Key design considerations include the selection of appropriate materials to manage dielectric properties and thermal expansion, placement and routing of high-speed signal paths to minimize cross-talk and impedance mismatches, and ensuring robust power integrity and ground plane management.
How do you ensure signal integrity in these PCBs?
Maintaining signal integrity involves careful design of the PCB stackup, controlled impedance lines, differential signaling where possible, and the use of shielding and ground planes to minimize interference from external and internal sources.
Can these PCBs be repaired or modified after manufacturing?
Repair and modification are more challenging for ultra-thin multilayer high-speed PCBs due to their compact and densely packed nature. Repairs, if feasible, must be performed by specialists to avoid damaging the delicate structures and maintaining performance specifications.
What future trends are influencing the development of these PCBs?
Trends include further miniaturization, increased layer counts in even thinner profiles, and the integration of more functionalities such as embedded components and passive devices. Advances in materials science and manufacturing technologies are also driving the evolution of these complex PCBs.