Ultra-thin Hard PCB Manufacturer
Ultra-thin Hard PCB Manufacturer,Ultra-thin hard PCBs represent a cutting-edge advancement in printed circuit board technology, characterized by their exceptionally slim profile and rigid construction. These PCBs are engineered with precision to achieve thicknesses of less than 0.6mm, making them ideal for applications where space constraints and weight reduction are paramount concerns. Despite their thinness, ultra-thin hard PCBs maintain robust structural integrity, providing a stable platform for mounting electronic components. They are crafted using high-quality rigid substrate materials, such as fiberglass reinforced epoxy resin (FR-4), which offer excellent mechanical strength and electrical insulation properties. With their compact form factor and reliability, ultra-thin hard PCBs find widespread use in various industries, including consumer electronics, medical devices, aerospace, and automotive electronics. From smartphones and wearables to advanced medical equipment and aerospace systems, these PCBs play a critical role in enabling the development of innovative and compact electronic devices that push the boundaries of technology.
What is an Ultra-thin Hard PCB?
An ultra-thin hard PCB (Printed Circuit Board) refers to a type of circuit board that is exceptionally thin while still maintaining rigidity. These PCBs are designed to be very slim, often with a thickness of less than 0.6mm, making them suitable for applications where space is limited or weight reduction is critical.
The “hard” aspect of the PCB indicates that it is made of a rigid substrate material, such as fiberglass reinforced epoxy resin (FR-4), rather than a flexible material like polyimide (PI) commonly used in flexible PCBs. This rigidity provides stability and support to the components mounted on the board.
Ultra-thin hard PCBs find applications in various industries, including consumer electronics, medical devices, aerospace, and automotive electronics, where compactness and lightweight design are essential requirements. These PCBs are often used in smartphones, tablets, wearable devices, and other portable electronics where space is at a premium.
What are Ultra-thin Hard PCB Design Guidelines?
Design guidelines for ultra-thin hard PCBs typically include specifications for thickness, layer stackup, trace width and spacing, material selection, and manufacturing tolerances to ensure the integrity and performance of the PCB.
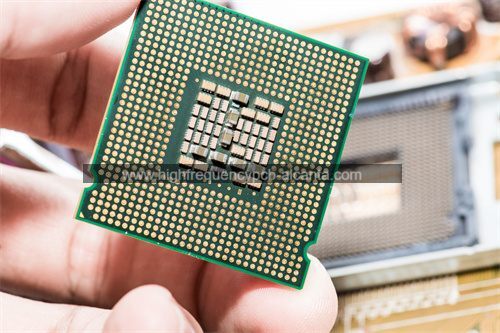
Ultra-thin Hard PCB Manufacturer
What is the Ultra-thin Hard PCB Fabrication Process?
The fabrication process for ultra-thin hard PCBs is similar to that of standard rigid PCBs but involves additional steps to achieve the desired thinness. Here’s a general overview of the fabrication process:
- Design: The process begins with the design of the PCB using Computer-Aided Design (CAD) software. Design considerations include component placement, routing of traces, and ensuring that the board meets the required thickness specifications.
- Substrate Selection: Selecting a suitable substrate material is crucial for ultra-thin PCBs. Typically, a high-performance rigid substrate such as FR-4 with a thin copper foil layer is chosen. The thickness of the substrate is reduced to achieve the desired thinness.
- Preparation of Substrate:The substrate material is cleaned and prepared for the next steps, which may involve surface treatment to enhance adhesion and improve solderability.
- Copper Foil Application: A thin layer of copper foil is laminated onto the substrate. The copper foil is typically etched to create the desired circuit pattern.
- Etching: Chemical etching is used to remove unwanted copper from the foil, leaving behind the desired circuit traces. The etching process is carefully controlled to achieve the required trace width and spacing.
- Drilling: Small holes are drilled into the PCB to accommodate component leads and vias for interconnecting different layers of the board.
- Plating: Through-hole plating or electroplating is performed to add metal plating to the drilled holes, which improves conductivity and solderability.
- Lamination: Multiple layers of substrate and copper foil may be laminated together to create a multi-layer PCB, depending on the complexity of the circuit design.
- Solder Mask Application: A solder mask is applied over the copper traces to protect them from oxidation and facilitate soldering. Openings are left in the solder mask for soldering components.
- Silkscreen Printing: Identifying markings, such as component designators and logos, are printed onto the PCB using a silkscreening process.
- Surface Finish: The PCB’s surface finish is applied to protect the copper traces and ensure reliable solder joints during assembly. Common surface finishes include HASL (Hot Air Solder Leveling), ENIG (Electroless Nickel Immersion Gold), and OSP (Organic Solderability Preservatives).
- Testing and Inspection: The fabricated PCB undergoes various tests and inspections to ensure that it meets quality standards and that there are no defects in the circuitry.
Once the fabrication process is complete, the ultra-thin hard PCB is ready for assembly with electronic components, leading to the creation of functional electronic devices.
How do you Manufacture an Ultra-thin Hard PCB?
Manufacturing an ultra-thin hard PCB involves a specialized process to achieve the desired thinness while maintaining structural integrity. Here’s a step-by-step guide to manufacturing an ultra-thin hard PCB:
- Substrate Selection: Choose a high-quality rigid substrate material suitable for ultra-thin PCBs. Common options include fiberglass reinforced epoxy resin (FR-4) or similar rigid materials.
- Substrate Preparation: Clean the substrate thoroughly to remove any contaminants that could affect the PCB manufacturing process. Surface treatment may be applied to enhance adhesion and solderability.
- Copper Foil Lamination: Apply a thin layer of copper foil onto the substrate using a lamination process. The thickness of the copper foil should be carefully controlled to achieve the desired conductivity while keeping the PCB thin.
- Circuit Patterning: Use photolithography or a similar process to transfer the circuit pattern onto the copper foil layer. This involves applying a photosensitive resist material, exposing it to UV light through a photomask, and then developing and etching away the unexposed areas of the resist to create the circuit traces.
- Etching: Use a chemical etching process to remove the unwanted copper from the foil, leaving behind the desired circuit traces. The etching process must be carefully controlled to ensure that the traces have the correct dimensions and spacing.
- Drilling: Drill small holes into the PCB for through-hole components and vias. Precision drilling is crucial to ensure that the holes are accurately placed and have the correct diameter.
- Plating: Apply metal plating to the drilled holes to improve conductivity and facilitate soldering. This may involve electroplating or other plating processes.
- Layer Lamination (if applicable): If the PCB requires multiple layers, laminate the layers together using heat and pressure. Each layer should be carefully aligned to ensure proper electrical connections between them.
- Solder Mask Application: Apply a solder mask over the copper traces to protect them from oxidation and facilitate soldering. The solder mask should be applied uniformly and accurately, leaving openings for component pads and vias.
- Silkscreen Printing: Print identifying markings, such as component designators and logos, onto the PCB using a silkscreening process. This step helps with component placement and identification during assembly.
- Surface Finish: Apply a surface finish to protect the exposed copper traces and ensure reliable solder joints. Common surface finishes include HASL (Hot Air Solder Leveling), ENIG (Electroless Nickel Immersion Gold), and OSP (Organic Solderability Preservatives).
- Testing and Inspection:Conduct electrical testing and visual inspection to ensure that the fabricated PCB meets quality standards and that there are no defects in the circuitry.
By following these steps, you can manufacture ultra-thin hard PCBs that meet the requirements for compact and lightweight electronic devices.
How much should an Ultra-thin Hard PCB cost?
The cost of an ultra-thin hard PCB can vary widely depending on several factors, including the size, complexity, number of layers, materials used, and manufacturing volume. Here are some factors that can influence the cost:
- Size and Complexity: Larger PCBs with intricate designs and densely packed components will generally cost more to manufacture than smaller, simpler boards.
- Number of Layers: Ultra-thin PCBs may have multiple layers to accommodate complex circuitry. The more layers required, the higher the cost, as each additional layer adds complexity to the manufacturing process.
- Materials: The choice of materials for the substrate, copper foil, and surface finish can impact the cost. High-performance materials may cost more but offer better performance and reliability.
- Manufacturing Volume: Economies of scale come into play with PCB manufacturing. Larger production runs typically result in lower per-unit costs compared to small batches.
- Lead Time: Urgent orders or expedited manufacturing may incur additional costs due to rush fees or premium shipping charges.
- Additional Services: Extra services such as design assistance, prototype testing, and assembly can add to the overall cost of the PCB.
As a rough estimate, ultra-thin hard PCBs can range in cost from a few dollars for simple, small-scale production to several hundred dollars or more for complex, high-volume orders with advanced features. It’s best to consult with PCB manufacturers and provide detailed specifications to get accurate quotes for your specific project.
What is Ultra-thin Hard PCB Base Material?
The base material for ultra-thin hard PCBs typically consists of rigid substrates that provide structural integrity and support to the circuitry. The choice of base material depends on factors such as mechanical strength, thermal properties, electrical performance, and compatibility with the manufacturing process. Here are some common base materials used for ultra-thin hard PCBs:
- Fiberglass Reinforced Epoxy Resin (FR-4): FR-4 is one of the most widely used substrate materials for PCBs. It offers excellent mechanical strength, dimensional stability, and electrical insulation properties. FR-4 is composed of woven fiberglass cloth impregnated with epoxy resin, making it suitable for ultra-thin hard PCBs where rigidity is required.
- High-Temperature FR-4:For applications that involve high operating temperatures or thermal cycling, high-temperature FR-4 variants with enhanced thermal stability may be used. These materials can withstand elevated temperatures without compromising performance.
- Composite Materials: Some advanced composite materials, such as ceramic-filled epoxy laminates or resin systems reinforced with materials like glass or aramid fibers, may be used for ultra-thin hard PCBs. These materials offer specific advantages such as improved thermal conductivity or reduced dielectric loss.
- Rigid-Flex PCB Materials: In cases where the PCB requires both flexibility and rigidity, rigid-flex materials can be used. These materials typically consist of a combination of flexible polyimide (PI) layers and rigid FR-4 layers bonded together. The rigid sections provide support for components and connectors, while the flexible sections allow the PCB to bend or fold as needed.
- Metal Core Materials: For applications that require high thermal conductivity or heat dissipation, metal core materials such as aluminum or copper can be used as the base material for ultra-thin hard PCBs. These materials provide efficient heat transfer away from heat-generating components, improving overall reliability and performance.
When selecting a base material for ultra-thin hard PCBs, it’s essential to consider factors such as dimensional stability, thermal management, electrical properties, and compatibility with the manufacturing process to ensure the reliability and performance of the final PCB design.
Which company makes Ultra-thin Hard PCB?
Many companies offer manufacturing services for ultra-thin hard PCBs. Some well-known companies include Sanmina, Molex, Mouser Electronics in the United States; Jiangsu Solartech Electronics, Shenzhen Relitech Technology, Shenzhen Sawei Electronics in China; and various other PCB manufacturers worldwide. These companies have advanced manufacturing equipment and technology to produce ultra-thin hard PCBs of various sizes, complexities, and materials according to customer requirements.
Our company also provides manufacturing services for ultra-thin hard PCBs, and we also have the capability to produce Mixed Dielectric Rogers PCBs. Rogers PCBs use high-performance materials from Rogers Corporation, featuring excellent high-frequency performance, low loss, and high reliability, making them suitable for RF and microwave applications. With our experienced engineering team, we can customize and produce Mixed Dielectric Rogers PCBs according to customer design requirements and technical specifications. We ensure that each PCB meets high-quality standards through strict quality control and inspection processes, delivering them to customers on time. If you have any requirements for ultra-thin hard PCBs or Mixed Dielectric Rogers PCBs, please feel free to contact us, and we will provide you with high-quality service and products.
What are the 7 qualities of good customer service?
Good customer service is characterized by several key qualities that contribute to positive interactions and customer satisfaction. Here are seven qualities of good customer service:
- Responsiveness: Good customer service involves promptly addressing customer inquiries, concerns, and issues. Customers appreciate receiving timely responses to their questions and having their needs attended to without unnecessary delays.
- Empathy: Empathy involves understanding and relating to the customer’s emotions, concerns, and perspectives. Good customer service representatives listen actively, show genuine concern for the customer’s situation, and strive to put themselves in the customer’s shoes.
- Clarity: Providing clear and concise communication is essential for effective customer service. This includes explaining products or services, policies, procedures, and resolutions in a straightforward manner that customers can easily understand.
- Professionalism: Professionalism encompasses displaying courtesy, respect, and professionalism in all interactions with customers. Good customer service representatives maintain a positive attitude, remain calm under pressure, and conduct themselves professionally at all times.
- Problem-solving skills: Effective problem-solving skills are crucial for resolving customer issues and complaints efficiently. Good customer service representatives are resourceful, proactive, and capable of finding creative solutions to address customer concerns.
- Consistency: Consistency in service delivery builds trust and confidence with customers. Good customer service is reliable and consistent across all touchpoints, ensuring that customers receive the same level of service excellence every time they interact with the company.
- Personalization: Tailoring the customer experience to individual preferences and needs demonstrates a commitment to personalized service. Good customer service involves recognizing and appreciating each customer as a unique individual, providing personalized recommendations, and anticipating their needs.
By embodying these qualities, businesses can deliver exceptional customer service experiences that foster loyalty, satisfaction, and positive word-of-mouth referrals.
FAQs
What are Mixed Dielectric Rogers PCBs?
Mixed Dielectric Rogers PCBs are printed circuit boards that incorporate multiple types of dielectric materials from Rogers Corporation. These materials typically have different dielectric constants and are used in specific areas of the PCB to achieve desired electrical properties.
What are the advantages of Mixed Dielectric Rogers PCBs?
Mixed Dielectric Rogers PCBs offer several advantages, including improved signal integrity, reduced signal loss, enhanced impedance control, and better thermal management. By strategically using different dielectric materials, designers can optimize the performance of high-frequency and microwave circuits.
What applications are suitable for Mixed Dielectric Rogers PCBs?
Mixed Dielectric Rogers PCBs are commonly used in RF (radio frequency) and microwave applications, such as telecommunications, aerospace, defense, automotive radar systems, medical devices, and wireless communication systems. They are particularly beneficial for applications that require precise impedance matching, minimal signal loss, and high reliability.
How are Mixed Dielectric Rogers PCBs manufactured?
Manufacturing Mixed Dielectric Rogers PCBs involves similar processes to standard PCB fabrication, including substrate preparation, copper foil lamination, circuit patterning, etching, drilling, plating, solder mask application, silkscreen printing, surface finish, and testing. However, additional care is taken during material selection and lamination to ensure proper integration of different dielectric materials.
What factors should be considered when designing Mixed Dielectric Rogers PCBs?
When designing Mixed Dielectric Rogers PCBs, designers should consider factors such as dielectric constant, loss tangent, thickness, layer stackup, impedance matching, signal routing, thermal management, and compatibility with manufacturing processes. Collaboration with experienced PCB designers and manufacturers is essential to optimize the design for performance and reliability.
Are Mixed Dielectric Rogers PCBs more expensive than standard PCBs?
Yes, Mixed Dielectric Rogers PCBs tend to be more expensive than standard PCBs due to the higher cost of Rogers Corporation’s high-performance dielectric materials and the complexity of manufacturing processes. However, the benefits in terms of performance and reliability often justify the investment, especially for critical RF and microwave applications.
Where can I find a manufacturer for Mixed Dielectric Rogers PCBs?
Many PCB manufacturers offer fabrication services for Mixed Dielectric Rogers PCBs. It’s essential to choose a reputable manufacturer with experience in high-frequency PCBs and a track record of delivering quality products. You can search online, consult industry directories, or ask for recommendations from colleagues to find a suitable manufacturer for your specific requirements.