Ultra-small Size BGA Substrates Manufacturer
Ultra-small Size BGA Substrates Manufacturer,Ultra-small Size BGA Substrates (USBGS) are cutting-edge packaging solutions revolutionizing microelectronics. With their compact form factor and advanced materials like silicon or alumina, USBGS provide a sturdy foundation for mounting integrated circuits (ICs) in electronic devices. Offering improved electrical performance, enhanced thermal management, and increased reliability, these substrates cater to applications demanding space efficiency and high functionality. USBGS enable the design of smaller, sleeker electronic devices without compromising performance. Their manufacturing involves intricate processes, ensuring precision and quality, making USBGS a cornerstone of modern electronics.
What are Ultra-small Size BGA Substrates (USBGS)?
Ultra-small Size BGA Substrates (USBGS) are advanced packaging solutions used in microelectronics. These substrates, typically made of a ceramic material like silicon or alumina, serve as the foundation for mounting and interconnecting integrated circuits (ICs) in electronic devices. USBGS offers a compact form factor, making them ideal for applications where space is at a premium, such as mobile devices, wearables, and IoT gadgets.
USBGS substrates feature a Ball Grid Array (BGA) configuration, where solder balls are arranged in a grid pattern on the underside of the substrate. This design allows for efficient electrical connections between the ICs and the printed circuit board (PCB) while minimizing the footprint required on the PCB.
The “ultra-small” aspect of USBGS refers to the miniaturized size of these substrates compared to traditional BGA packages. This reduction in size is achieved through advancements in manufacturing technologies, including finer pitch interconnections and thinner substrate materials.
USBGS substrates offer several advantages, including improved electrical performance, enhanced thermal management, and increased reliability due to shorter interconnection lengths. Additionally, their smaller size contributes to overall system miniaturization, enabling manufacturers to design smaller and more compact electronic devices without sacrificing performance.
In summary, Ultra-small Size BGA Substrates (USBGS) are cutting-edge packaging solutions that enable the development of compact and high-performance electronic devices for various applications.
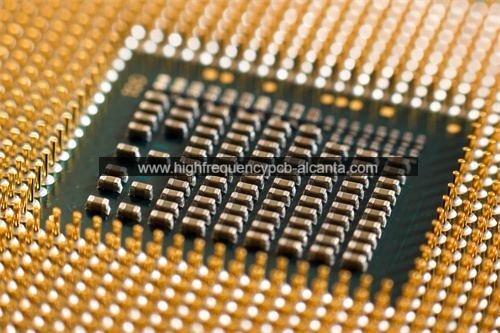
Ultra-small Size BGA Substrates Manufacturer
What are the Ultra-small Size BGA Substrates Design Guidelines?
Designing with Ultra-small Size BGA Substrates (USBGS) requires careful consideration of several key guidelines to ensure optimal performance and reliability:
- Pitch and Pad Layout: USBGS typically have a very fine pitch between solder balls, so it’s crucial to adhere to manufacturer-recommended pitch guidelines. The layout of the pads on the PCB should match the pitch of the USBGS to ensure proper alignment and soldering.
- Thermal Management: USBGS packages may have limited thermal dissipation capabilities due to their compact size. Designers should implement effective thermal management techniques such as heat sinks, thermal vias, and proper airflow to prevent overheating and maintain device reliability.
- Signal Integrity: High-speed signals routed on USBGS substrates are susceptible to signal integrity issues such as crosstalk and signal attenuation. Design guidelines for signal routing, impedance matching, and minimizing signal reflections should be followed to ensure reliable data transmission.
- Power Delivery: Proper power delivery network (PDN) design is critical to ensure stable voltage regulation and minimize power noise. This includes optimizing power plane distribution, decoupling capacitor placement, and minimizing loop inductance in power delivery paths.
- Manufacturability: USBGS substrates may have specific manufacturing requirements due to their miniaturized size and fine-pitch interconnections. Designers should collaborate closely with manufacturing partners to ensure that the design is manufacturable and meets quality standards.
- Assembly Considerations: Specialized assembly techniques may be required for soldering USBGS packages onto the PCB, such as reflow soldering or underfill encapsulation. Design guidelines for solder paste application, solder joint inspection, and assembly process parameters should be followed to achieve reliable solder connections.
- Reliability Testing:USBGS designs should undergo rigorous reliability testing to ensure long-term performance under various environmental conditions and operational stresses. This may include thermal cycling, mechanical shock, vibration testing, and accelerated aging tests.
By adhering to these design guidelines, engineers can maximize the performance, reliability, and manufacturability of electronic devices utilizing Ultra-small Size BGA Substrates (USBGS).
What is the Ultra-small Size BGA Substrates Fabrication Process?
The fabrication process of Ultra-small Size BGA Substrates (USBGS) involves several intricate steps to create the compact and high-performance packages used in microelectronics. While specific details may vary depending on the manufacturer and substrate material, here’s a general overview of the USBGS fabrication process:
- Substrate Material Selection: USBGS substrates are typically made from advanced materials such as silicon, alumina, or other ceramics with excellent thermal and electrical properties. The choice of substrate material depends on the application requirements and desired performance characteristics.
- Substrate Preparation:The substrate material undergoes a series of preparation steps, including cleaning and surface treatment, to remove contaminants and improve adhesion during subsequent processing steps.
- Thin Film Deposition: Thin films of conductive and insulating materials are deposited onto the substrate using techniques such as physical vapor deposition (PVD) or chemical vapor deposition (CVD). These thin films form the conductive traces, vias, and insulation layers necessary for interconnecting the integrated circuits (ICs) mounted on the USBGS.
- Photolithography: Photolithography is used to define the intricate patterns of conductive traces and insulating layers on the substrate. A photoresist material is applied to the substrate, exposed to ultraviolet (UV) light through a photomask, and developed to selectively remove the photoresist and expose the underlying substrate for subsequent processing steps.
- Etching: Chemical or plasma etching is used to selectively remove the exposed areas of the substrate material, creating the desired patterns of conductive traces and insulating layers. This step defines the electrical interconnections and isolation regions on the USBGS substrate.
- Metallization: Metal layers such as copper or gold are deposited onto the substrate to form the conductive traces and pads for solder attachment. These metal layers are typically deposited using techniques such as sputtering or electroplating.
- Solder Mask Application: A solder mask material is applied to the substrate to protect the exposed metal traces and pads from oxidation and contamination during subsequent assembly processes. The solder mask is selectively patterned to expose the solder attachment points on the USBGS.
- Solder Ball Attachment: Solder balls are attached to the exposed pads on the underside of the USBGS substrate using techniques such as solder ball placement or solder paste stencil printing followed by reflow soldering. These solder balls provide the electrical and mechanical connections between the USBGS and the printed circuit board (PCB) of the electronic device.
- Quality Control and Testing: The finished USBGS substrates undergo rigorous quality control and testing procedures to ensure conformance to specifications and reliability standards. This may include electrical testing, visual inspection, and mechanical reliability testing.
By following these fabrication steps with precision and care, manufacturers can produce USBGS substrates that meet the demanding requirements of modern microelectronics applications.
How do you manufacture Ultra-small Size BGA Substrates?
Manufacturing Ultra-small Size BGA Substrates (USBGS) involves a series of intricate processes aimed at producing compact and high-performance packaging solutions for microelectronics. Here’s a step-by-step overview of the USBGS manufacturing process:
- Substrate Material Selection: USBGS substrates are typically made from advanced materials such as silicon, alumina, or other ceramics with excellent thermal and electrical properties. The choice of substrate material depends on factors like thermal conductivity, electrical insulation, and mechanical strength required for the specific application.
- Substrate Preparation: The selected substrate material undergoes preparation steps such as cleaning and surface treatment to remove impurities and contaminants. This ensures proper adhesion of subsequent layers and improves overall substrate quality.
- Thin Film Deposition: Thin films of conductive and insulating materials are deposited onto the substrate surface using techniques like physical vapor deposition (PVD) or chemical vapor deposition (CVD). These thin films form the basis for creating the conductive traces, vias, and insulation layers necessary for interconnecting integrated circuits (ICs).
- Photolithography: Photolithography is employed to define the intricate patterns of conductive traces and insulating layers on the substrate. A layer of photoresist material is applied to the substrate surface, exposed to UV light through a photomask containing the desired circuit patterns, and developed to selectively remove the photoresist and expose the underlying substrate for further processing.
- Etching: Chemical or plasma etching is used to selectively remove the exposed areas of the substrate material, following the patterns defined by the photolithography process. This step creates the desired circuit patterns, including conductive traces and insulation layers, on the USBGS substrate.
- Metallization: Metal layers such as copper or gold are deposited onto the substrate surface to form the conductive traces, pads, and solder attachment points. These metal layers are typically deposited using techniques like sputtering or electroplating, and they provide the electrical pathways for interconnecting ICs mounted on the USBGS.
- Solder Mask Application: A solder mask material is applied to the substrate surface to protect the exposed metal traces and pads from oxidation and contamination during subsequent assembly processes. The solder mask is selectively patterned to expose the solder attachment points, ensuring proper soldering during assembly.
- Solder Ball Attachment: Solder balls are attached to the exposed solder pads on the underside of the USBGS substrate. This is typically achieved through processes like solder ball placement or solder paste stencil printing followed by reflow soldering. The solder balls provide the electrical and mechanical connections between the USBGS and the printed circuit board (PCB) of the electronic device.
- Quality Control and Testing: The finished USBGS substrates undergo comprehensive quality control and testing procedures to ensure conformance to specifications and reliability standards. This includes electrical testing, visual inspection, and mechanical reliability testing to verify the integrity and performance of the manufactured USBGS substrates.
By meticulously following these manufacturing processes, manufacturers can produce USBGS substrates that meet the demanding requirements of modern microelectronics applications, including compact size, high performance, and reliability.
How much should Ultra-small Size BGA Substrates cost?
The cost of Ultra-small Size BGA Substrates (USBGS) can vary significantly depending on various factors such as substrate material, size, complexity of the design, manufacturing volume, and vendor pricing strategies. Generally, USBGS tend to be more expensive than traditional BGA substrates due to their miniaturized size and advanced manufacturing processes. Here are some key factors that influence the cost of USBGS:
- Substrate Material: The choice of substrate material can impact the cost of USBGS. Advanced materials with superior thermal and electrical properties may be more expensive than standard materials.
- Manufacturing Complexity: USBGS with intricate circuit patterns, fine pitch interconnections, and multiple layers may require more advanced manufacturing processes, which can contribute to higher manufacturing costs.
- Size and Density: Smaller USBGS with higher circuit density tend to be more expensive to manufacture due to the precision and accuracy required in fabrication processes.
- Volume Production: Economies of scale play a significant role in determining the cost of USBGS. Higher production volumes typically result in lower per-unit manufacturing costs due to optimized manufacturing processes and bulk material purchasing.
- Vendor Pricing:Different vendors may offer USBGS at varying price points based on their manufacturing capabilities, technology expertise, and market positioning. It’s essential to consider quotes from multiple vendors to find a competitive price for USBGS.
- Additional Features: USBGS with additional features such as advanced thermal management solutions, integrated passive components, or specialized coatings may command a higher price.
- Quality and Reliability: USBGS manufactured to higher quality and reliability standards may incur additional costs for quality control measures, testing procedures, and compliance certifications.
Given these factors, it’s challenging to provide a specific cost for USBGS without detailed information about the specific requirements and quantities involved. However, USBGS are typically considered a premium packaging solution and may cost more than conventional BGA substrates due to their advanced features and manufacturing processes.
What is Ultra-small Size BGA Substrates base material?
Ultra-small Size BGA Substrates (USBGS) can be made from various base materials, each offering different properties suited to specific applications. Some common base materials used for USBGS include:
- Silicon: Silicon substrates are widely used in semiconductor manufacturing due to their excellent thermal conductivity, mechanical stability, and compatibility with integrated circuits (ICs). Silicon-based USBGS are well-suited for high-performance applications where thermal management is critical.
- Alumina (Aluminum Oxide): Alumina substrates offer good electrical insulation properties and thermal conductivity, making them suitable for USBGS used in power electronics, RF applications, and high-temperature environments. Alumina-based USBGS are also known for their durability and reliability.
- Aluminum Nitride (AlN): Aluminum nitride substrates possess excellent thermal conductivity and coefficient of thermal expansion (CTE) matching that of silicon, making them ideal for USBGS used in high-power applications and microwave devices. AlN-based USBGS offer superior thermal performance and reliability.
- Ceramic Composites: Some USBGS may be fabricated using ceramic composites, which combine the properties of different ceramic materials to achieve specific performance requirements. Ceramic composites can offer a balance of electrical insulation, thermal conductivity, and mechanical strength tailored to the application.
- Polyimide: Polyimide substrates, also known as flexible substrates, are used in USBGS applications where flexibility and bendability are required, such as in wearable devices and flexible electronics. Polyimide-based USBGS offer lightweight construction and conformability to irregular shapes.
- Glass: Glass substrates are utilized in USBGS for applications requiring high optical transparency, such as display technologies and optical sensors. Glass-based USBGS offer excellent dimensional stability and chemical resistance.
The choice of base material for USBGS depends on factors such as thermal requirements, electrical properties, mechanical stability, and cost considerations. Designers select the most appropriate substrate material based on the specific needs of the application and the desired performance characteristics of the USBGS.
Which company manufactures Ultra-small Size BGA Substrates?
Currently, there are many companies manufacturing Ultra-small Size BGA Substrates (USBGS), and some major manufacturers include: Micron Technology, Intel, TSMC, Samsung Electronics, Epson, Panasonic, Ericsson, and others. These companies have rich experience in the field of microelectronics and advanced manufacturing technologies to produce USBGS of various sizes and materials to meet the needs of different applications.
For our company, we can also manufacture Ultra-small Size BGA Substrates to meet customers’ demands for high-performance and miniaturized packaging. With advanced manufacturing equipment and a skilled technical team, we have the capability to design, process, and test USBGS through a series of production processes. Our manufacturing process includes:
- Material Selection and Preparation: We select high-quality substrate materials such as silicon, alumina, aluminum nitride (AlN), etc., according to customers’ requirements and application scenarios.
- Manufacturing Process: We employ advanced manufacturing processes such as thin film deposition, photolithography, etching, metallization, etc., to precisely control each step and ensure the quality and performance of USBGS meet customers’ requirements.
- Quality Control and Testing: We strictly implement quality management systems and conduct comprehensive quality control and testing on each batch of products, including electrical performance testing, reliability testing, etc., to ensure product stability and reliability.
- Customization Services: We provide customized USBGS solutions according to customers’ needs, including customization of size, material, layout, etc., to meet specific requirements of different customers.
As a professional manufacturer, we are committed to providing customers with high-quality, reliable, and cost-effective Ultra-small Size BGA Substrates, helping customers succeed in the design and manufacturing of electronic products. Our team will provide customers with high-quality products and services and work together with customers to develop and create a better future.
What are the 7 qualities of good customer service?
Good customer service is essential for building strong relationships with customers and fostering loyalty. Here are seven qualities that contribute to excellent customer service:
- Responsiveness: Being responsive means promptly addressing customer inquiries, concerns, and requests. Whether it’s answering phone calls, responding to emails, or interacting on social media, customers appreciate timely and attentive service.
- Empathy: Empathy involves understanding and acknowledging the customer’s feelings, concerns, and perspectives. By demonstrating empathy, customer service representatives can build rapport, create a positive experience, and effectively resolve issues.
- Clear Communication: Clear communication is vital for ensuring that customers understand the information, instructions, or solutions provided. Customer service representatives should use simple language, active listening techniques, and avoid jargon to facilitate effective communication.
- Knowledgeability: Knowledgeable customer service representatives possess a deep understanding of the products, services, policies, and procedures of the company. They can provide accurate information, offer relevant recommendations, and troubleshoot issues effectively, instilling confidence in customers.
- Professionalism: Professionalism involves maintaining a courteous, respectful, and professional demeanor in all interactions with customers. This includes being patient, maintaining composure, and resolving conflicts calmly and diplomatically.
- Flexibility:Flexibility entails adapting to the unique needs and preferences of each customer. Customer service representatives should be willing to accommodate special requests, offer personalized solutions, and be open to feedback to enhance the customer experience.
- Problem-solving Skills: Strong problem-solving skills are crucial for addressing customer concerns and resolving issues efficiently. Customer service representatives should be proactive, resourceful, and creative in finding solutions that meet the customer’s needs and exceed expectations.
By embodying these qualities, organizations can deliver exceptional customer service experiences that foster loyalty, satisfaction, and positive word-of-mouth referrals.
FAQs
What are Ultra-small Size BGA Substrates (USBGS)?
USBGS are advanced packaging solutions used in microelectronics. They serve as the foundation for mounting and interconnecting integrated circuits (ICs) in electronic devices, offering a compact form factor ideal for applications where space is limited.
What are the advantages of USBGS?
USBGS offer several advantages, including compact size, improved electrical performance, enhanced thermal management, increased reliability, and the ability to design smaller and more compact electronic devices without sacrificing performance.
What materials are used to make USBGS?
USBGS can be made from various materials, including silicon, alumina, aluminum nitride (AlN), polyimide, and ceramic composites. The choice of material depends on factors such as thermal conductivity, electrical insulation, mechanical strength, and specific application requirements.
What are the typical applications of USBGS?
USBGS are used in a wide range of applications, including mobile devices, wearables, IoT gadgets, consumer electronics, automotive electronics, medical devices, aerospace, and defense systems.
What factors should be considered when designing with USBGS?
Designing with USBGS requires considerations such as pitch and pad layout, thermal management, signal integrity, power delivery, manufacturability, assembly techniques, and reliability testing to ensure optimal performance and reliability.
How are USBGS manufactured?
The manufacturing process of USBGS involves several steps, including substrate material selection, preparation, thin film deposition, photolithography, etching, metallization, solder mask application, solder ball attachment, quality control, and testing.
What is the cost of USBGS?
The cost of USBGS varies depending on factors such as substrate material, size, complexity of the design, manufacturing volume, and vendor pricing strategies. USBGS are typically considered a premium packaging solution and may cost more than traditional BGA substrates due to their advanced features and manufacturing processes.