TU933 Materials PCB Manufacturer
TU933 Materials PCB Manufacturer,A PCB made with TU933 material is a high-performance circuit board highly regarded for its exceptional electrical properties, particularly suited for high-frequency and high-speed applications. TU933 material boasts low dielectric loss, high thermal conductivity, and excellent mechanical strength, making it an ideal choice for telecommunications equipment, aerospace technology, medical devices, and high-speed computing systems. Its outstanding signal integrity and thermal management ensure reliability and stability in circuits, whether in multilayer designs or complex circuits, meeting stringent technical requirements with excellence.
What is TU933 Materials PCB?
TU933 is a type of PCB (Printed Circuit Board) material known for its exceptional performance characteristics in electronic applications. It’s often used in high-frequency and high-speed circuits due to its excellent electrical properties, such as low dielectric loss, high thermal conductivity, and good mechanical strength.
The acronym “TU” might denote a specific manufacturer or brand, though it’s not a universally recognized designation in the PCB industry. PCB materials like TU933 typically consist of layers of fiberglass cloth impregnated with epoxy resin, with copper foil bonded to one or both sides.
In addition to its electrical properties, TU933 may offer benefits such as good solderability, resistance to environmental factors like moisture and temperature extremes, and compatibility with various manufacturing processes including etching, drilling, and solder mask application.
Engineers and designers often choose materials like TU933 for applications where reliability, signal integrity, and performance are critical, such as telecommunications equipment, aerospace technology, medical devices, and high-speed computing systems. Its properties make it suitable for use in RF (Radio Frequency) and microwave circuits, where signal loss and interference must be minimized to ensure optimal performance.
Overall, TU933 materials play a vital role in the development of advanced electronic devices, offering a balance of electrical performance, mechanical stability, and manufacturability essential for modern PCB designs.
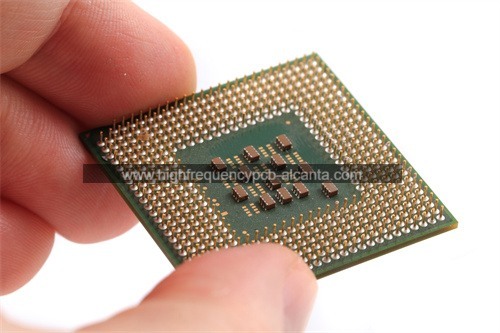
TU933 Materials PCB Manufacturer
What are the TU933 Materials PCB Design Guidelines?
Specific design guidelines for TU933 materials might vary depending on the manufacturer or supplier, as well as the intended application and performance requirements. However, here are some general design considerations that are typically important when working with PCB materials like TU933:
- Dielectric Constant (Dk): TU933 likely has a specific dielectric constant that influences signal propagation characteristics. Designers should consider the Dk value when calculating trace widths and spacing to achieve desired impedance matching for high-frequency signals.
- Copper Thickness: The thickness of copper layers on the PCB can affect both electrical performance and manufacturability. Design guidelines may specify minimum and maximum copper thicknesses to ensure adequate current carrying capacity, thermal management, and compatibility with fabrication processes like etching.
- Thermal Management: TU933 may have good thermal conductivity properties, but efficient heat dissipation is still important, especially in high-power applications or environments with elevated temperatures. Designers should incorporate features like thermal vias, heatsinks, and adequate spacing between components to manage heat effectively.
- Signal Integrity: Maintaining signal integrity is crucial for reliable operation of high-speed circuits. Design guidelines may include recommendations for controlled impedance routing, signal layer stackup configurations, and minimizing signal reflections and crosstalk.
- Mechanical Considerations: TU933 likely offers good mechanical strength, but designers should still consider factors like board thickness, mounting hole sizes, and component placement to ensure mechanical stability and compatibility with assembly processes.
- Environmental Factors: If the PCB will be exposed to harsh environmental conditions, design guidelines may include recommendations for conformal coating, sealing vias, and selecting components with appropriate environmental ratings (e.g., temperature, humidity, vibration resistance).
- Manufacturability: Designers should ensure that their PCB layouts are manufacturable using standard fabrication processes. This includes adhering to minimum feature sizes, avoiding overly complex designs that may increase manufacturing cost or lead time, and following industry best practices for layout and routing.
It’s essential for designers to consult with the manufacturer or supplier of TU933 materials to obtain detailed design guidelines and recommendations specific to their application and fabrication processes. Additionally, using simulation tools and performing thorough testing during the design process can help verify performance and reliability before moving to production.
What is the TU933 Materials PCB Fabrication Process?
The fabrication process for PCBs using TU933 materials generally follows standard procedures for manufacturing printed circuit boards, with some variations and considerations specific to the properties of TU933 material. Here’s an overview of the typical fabrication process:
- Design: The process begins with PCB design using CAD (Computer-Aided Design) software. Designers create the layout of the circuit, including component placement, trace routing, and layer stackup, adhering to design guidelines specific to TU933 materials.
- Material Preparation: TU933 material is selected and prepared for the fabrication process. This involves cutting the substrate to the desired size, cleaning the surfaces to remove any contaminants, and possibly applying a protective coating or surface treatment to enhance solderability or improve adhesion of copper foil.
- Layer Stackup: Multiple layers of TU933 material may be laminated together to create the final PCB stackup. Copper foil is typically bonded to one or both sides of the substrate, forming the conductive traces and signal layers of the PCB.
- Copper Patterning: A photolithography process is used to create the desired copper patterns on the PCB layers. This involves applying a photoresist material to the copper foil, exposing it to UV light through a photomask, and developing the resist to reveal the copper traces and pads.
- Etching: The exposed copper is then chemically etched away, leaving behind the desired circuit traces and patterns. Etching removes the copper material not protected by the developed photoresist, defining the conductive pathways of the PCB.
- Drilling: Holes are drilled into the PCB for through-hole components and vias. High-precision drilling machines are used to create holes with the required diameter and alignment according to the PCB design.
- Plating: After drilling, the walls of the drilled holes are plated with a conductive material, typically copper, to establish electrical connections between different layers of the PCB. This process is called electroplating or through-hole plating.
- Surface Finishing: The exposed copper surfaces of the PCB are coated with a surface finish to protect them from oxidation and ensure solderability. Common surface finishes include HASL (Hot Air Solder Leveling), ENIG (Electroless Nickel Immersion Gold), and OSP (Organic Solderability Preservatives).
- Solder Mask Application: A solder mask is applied over the PCB surface, leaving only the areas for component mounting and soldering exposed. Solder mask helps prevent solder bridges and ensures proper solder joint formation during assembly.
- Silkscreen Printing: Identification labels, component outlines, and other markings are printed onto the PCB surface using silkscreen printing. This step provides visual indicators and reference points for component placement and assembly.
- Testing and Inspection: The finished PCB undergoes electrical testing and visual inspection to ensure it meets the required quality standards and specifications. Testing may include checks for continuity, impedance, insulation resistance, and functionality.
- Final Assembly: Once the PCB passes testing, it is ready for final assembly. Components are soldered onto the board using automated assembly equipment or by hand, depending on the complexity and volume of production.
By following these steps, manufacturers can produce high-quality PCBs using TU933 materials, meeting the performance and reliability requirements of various electronic applications.
How do you manufacture a TU933 Materials PCB?
Manufacturing a PCB using TU933 materials involves a series of steps similar to the general PCB fabrication process, but with specific considerations for the properties of TU933 material. Here’s a detailed outline of the manufacturing process:
- Material Selection: Choose TU933 material sheets of the appropriate thickness and specifications based on the requirements of the PCB design and application.
- Preparation of Substrate: Cut the TU933 material sheets to the required size using cutting tools. Ensure that the substrate surfaces are clean and free from contaminants that could affect adhesion or electrical properties.
- Copper Foil Lamination: If necessary, laminate copper foil onto one or both sides of the TU933 substrate. This is typically done using heat and pressure in a lamination press, ensuring strong adhesion between the copper and substrate.
- Circuit Design and Layout: Design the circuit layout using CAD software, following design guidelines specific to TU933 materials. This includes component placement, trace routing, and defining layer stackup.
- Artwork Generation: Generate the artwork files for the PCB design, including Gerber files for copper traces, solder mask, and silkscreen layers.
- Photoresist Application: Apply a layer of photoresist material onto the copper-clad TU933 substrate using a spin coater or similar equipment. Ensure an even coating thickness across the entire surface.
- Exposure and Development: Expose the photoresist-coated substrate to UV light through a photomask containing the desired circuit pattern. Develop the exposed photoresist to reveal the copper traces and pads.
- Etching: Use chemical etching to remove the exposed copper from the substrate, leaving behind the desired circuit traces and patterns. Rinse the PCB thoroughly after etching to remove any etchant residue.
- Drilling: Drill holes in the PCB for through-hole components and vias using precision drilling equipment. Control the drilling parameters to achieve the required hole sizes and alignment.
- Plating: Plate the drilled holes with a conductive material, typically copper, to establish electrical connections between different layers of the PCB. This may involve electroplating or other plating techniques.
- Surface Finishing: Apply a surface finish to protect the exposed copper surfaces and ensure solderability. Common surface finishes for TU933 PCBs include HASL, ENIG, and OSP.
- Solder Mask Application: Apply a solder mask over the PCB surface to define solderable areas and protect the copper traces from oxidation. Cure the solder mask using heat or UV light.
- Silkscreen Printing: Print component outlines, identification labels, and other markings onto the PCB surface using silkscreen printing techniques.
- Testing and Inspection: Conduct electrical testing and visual inspection of the finished PCB to ensure it meets quality standards and specifications. Test for continuity, impedance, insulation resistance, and functionality.
- Final Assembly: Populate the PCB with components using automated assembly equipment or manual soldering techniques. Ensure proper component placement and solder joint quality.
- Quality Assurance: Perform final inspection and testing of assembled PCBs to verify functionality and reliability before packaging and shipment.
By following these steps with careful attention to detail and adherence to TU933 material specifications, manufacturers can produce high-quality PCBs suitable for a wide range of electronic applications.
How much should a TU933 Materials PCB cost?
The cost of a TU933 materials PCB can vary significantly depending on several factors:
- Board Size: Larger PCBs require more material and may involve additional manufacturing steps, such as multiple lamination cycles or increased drilling complexity, which can increase costs.
- Layer Count: PCBs with more layers typically cost more to manufacture due to the increased complexity of the fabrication process and the use of additional materials.
- Trace Density: Higher trace density, finer pitch components, and tighter tolerances in the design can increase manufacturing complexity and thus raise the cost of the PCB.
- Material Quality: The quality and performance characteristics of TU933 material can vary among different manufacturers or suppliers, affecting the cost of the PCB.
- Surface Finish: The choice of surface finish, such as HASL, ENIG, or OSP, can influence the cost of the PCB due to differences in material and processing requirements.
- Production Volume: Economies of scale apply to PCB manufacturing, so larger production volumes typically result in lower per-unit costs. However, setup costs for small production runs can offset these savings.
- Additional Services: Additional services such as assembly, testing, conformal coating, and customization may incur extra costs.
- Supplier and Location: The pricing policies of PCB manufacturers and suppliers, as well as their geographical location, can impact the overall cost.
Without specific details about the size, complexity, and quantity of PCBs needed, it’s challenging to provide an exact cost estimate. However, for a rough estimate, the cost of a standard TU933 materials PCB could range from a few dollars for simple single-layer boards to several hundred dollars or more for complex multilayer boards with advanced features. For precise pricing, it’s best to request quotes from PCB manufacturers or suppliers based on your specific requirements.
What is TU933 Materials PCB base material?
TU933 is likely a designation or code for a specific type of PCB material, but without further context or information about its composition, it’s difficult to provide a definitive answer. PCB materials typically consist of a substrate material combined with copper foil for conducting traces and forming circuit patterns.
Common substrate materials used in PCB manufacturing include:
- FR-4: The most widely used substrate material, FR-4 is a glass-reinforced epoxy laminate known for its good electrical insulation properties, mechanical strength, and affordability.
- FR-408: A higher-performance version of FR-4, FR-408 offers improved electrical characteristics such as lower dielectric loss and better signal integrity for high-speed applications.
- Polyimide (PI): PI is a flexible substrate material suitable for applications requiring bendability or resistance to high temperatures. It’s commonly used in flexible PCBs and in applications where thermal stability is crucial.
- Rogers Materials: Rogers Corporation manufactures a range of high-performance PCB materials with specific dielectric constants (Dk) and loss tangents (Df), optimized for RF/microwave applications.
- Isola Materials: Isola Group produces various PCB materials including high-speed laminates, low-loss laminates, and materials tailored for specific applications such as automotive or aerospace.
- DuPont Materials: DuPont offers a variety of advanced materials for PCBs, including high-temperature laminates, low-loss laminates, and materials designed for high-frequency applications.
TU933 may belong to a specific product line or series offered by a PCB material manufacturer, and its composition would likely be proprietary information. To determine the exact base material used in TU933 PCBs, it would be necessary to consult the manufacturer or supplier for detailed specifications.
Which company makes TU933 Materials PCB?
The TU933 PCB material may be a product line or series from a specific manufacturer, but without specific context, it’s difficult to determine which company produces it. Generally, PCB materials are manufactured by various companies, such as FR-4, Rogers, Isola, DuPont, and others.
As for our company, we can provide PCB manufacturing services using TU933 material. As a professional PCB manufacturer, we have the following advantages:
- Technical Strength: We have advanced production equipment and a skilled technical team capable of providing professional support in design, process, and manufacturing. Our engineering team has extensive experience and can provide customized solutions according to customer requirements.
- Quality Assurance: We strictly adhere to ISO quality management systems, implementing rigorous quality control and testing from raw material procurement to production. Our goal is to deliver high-quality products that meet customer requirements and expectations.
- Flexible Production: We have flexible production lines and capabilities to produce PCBs of different types and specifications according to customer needs. Whether it’s sample orders or large volume orders, we can meet customer requirements.
- Timely Delivery: We are committed to providing timely delivery services to ensure customers receive their orders on time. Our efficient production process and comprehensive logistics management enable us to respond quickly to customer needs.
- Service Support: We provide comprehensive pre-sales and after-sales service support, including technical consultation, design advice, sample production, and production tracking. Our customer service team is available to assist and support customers at all times.
In summary, as a professional PCB manufacturer, we have the capability to produce PCBs using TU933 material and provide high-quality products and services to meet various customer needs.
What are the 7 qualities of good customer service?
Good customer service is crucial for building and maintaining strong customer relationships. Here are seven essential qualities that define excellent customer service:
- Responsiveness: Quick and efficient responses to customer inquiries and issues are fundamental. Customers appreciate timely resolutions and proactive communication, which show that their needs are prioritized.
- Empathy: Understanding and acknowledging the customer’s feelings and concerns are vital. Empathy helps in building a connection and assures the customer that their problems are being taken seriously.
- Knowledgeability: A deep understanding of the product or service being offered is essential. This includes being able to provide accurate information, troubleshoot issues, and offer relevant advice or solutions.
- Patience: Handling customer queries and complaints with patience is crucial. Not all customers will be easy to deal with, and taking the time to listen and address their concerns calmly can lead to better outcomes.
- Clear Communication: Being able to convey information clearly and concisely is important. This means avoiding jargon, ensuring the customer understands the information provided, and confirming that their issues are resolved.
- Professionalism: Maintaining a professional demeanor in all interactions builds trust and respect. This includes being courteous, respectful, and keeping promises and commitments.
- Problem-Solving Skills: The ability to quickly identify issues and come up with effective solutions is a key quality. This requires creativity, resourcefulness, and a positive attitude towards resolving customer problems.
By embodying these qualities, customer service representatives can significantly enhance customer satisfaction and loyalty, leading to long-term business success.
FAQs
What is TU933 material in PCB manufacturing?
TU933 is a high-performance PCB material known for its excellent electrical properties, including low dielectric loss, high thermal conductivity, and good mechanical strength. It is commonly used in high-frequency and high-speed circuit applications.
What are the typical applications for PCBs made with TU933 material?
PCBs made with TU933 material are often used in telecommunications equipment, aerospace technology, medical devices, and high-speed computing systems. They are particularly suitable for RF (Radio Frequency) and microwave circuits where signal integrity is critical.
How does TU933 material compare to standard FR-4 material?
While FR-4 is a general-purpose material widely used in the PCB industry, TU933 offers superior electrical performance, particularly at high frequencies. It has lower dielectric loss and higher thermal conductivity, making it better suited for advanced and high-speed applications.
Can TU933 material be used for multilayer PCBs?
Yes, TU933 material can be used for multilayer PCBs. Its properties make it ideal for complex, multilayer designs that require excellent signal integrity and thermal management.
What are the design considerations when using TU933 material?
When designing PCBs with TU933 material, consider the dielectric constant (Dk), copper thickness, trace width and spacing, thermal management, and signal integrity. Adhering to these guidelines ensures optimal performance and reliability.
What surface finishes are compatible with TU933 material?
Common surface finishes compatible with TU933 material include HASL (Hot Air Solder Leveling), ENIG (Electroless Nickel Immersion Gold), and OSP (Organic Solderability Preservatives). The choice of finish depends on the specific application and requirements.
How do I ensure the quality of a PCB made with TU933 material?
To ensure the quality of a TU933 material PCB, work with a reputable manufacturer, follow industry-standard design and fabrication guidelines, and perform thorough testing and inspection, including electrical testing, impedance control, and visual inspection.
Are there any special handling or storage requirements for TU933 material?
TU933 material should be stored in a clean, dry environment to prevent moisture absorption and contamination. Handle the material carefully to avoid physical damage and follow the manufacturer’s recommendations for storage and handling.
What are the cost considerations for using TU933 material in PCB manufacturing?
The cost of TU933 material PCBs can vary based on factors such as board size, layer count, trace density, and production volume. While TU933 material may be more expensive than standard FR-4, its superior performance can justify the cost in high-frequency and high-speed applications.