Transparent Substrate Manufacturer
Transparent Substrate Manufacturer,Transparent substrates are materials that allow light to pass through without significant distortion or absorption, widely used in optics, electronics, and engineering. Common transparent substrate materials include glass, quartz, plastic films (such as PET and PC), and transparent conductive oxides (such as ITO and FTO). These materials are chosen for their excellent optical clarity, mechanical strength, and chemical resistance. Transparent substrates play a crucial role in LCDs, OLEDs, solar cells, touchscreens, and optical components. They can be customized in terms of size, shape, and surface treatment to meet specific application requirements.
What is a Transparent Substrate?
A transparent substrate is a material that allows light to pass through without significant distortion or absorption. It forms the base or foundation for various applications in optics, electronics, and engineering. Common transparent substrates include glass, quartz, plastic films like polyethylene terephthalate (PET), and transparent conductive oxides (TCOs) such as indium tin oxide (ITO).
In optics, transparent substrates serve as the foundation for lenses, windows, and mirrors. They provide structural support while maintaining optical clarity, enabling the manipulation and control of light in devices like cameras, microscopes, and telescopes.
In electronics, transparent substrates are essential for applications such as liquid crystal displays (LCDs), organic light-emitting diodes (OLEDs), and photovoltaic cells (solar panels). They allow for the integration of electronic components while ensuring visibility through the substrate.
Transparent substrates also find use in various industrial and scientific applications, including coatings, sensors, and protective layers. Their transparency allows for observation or measurement of processes occurring beneath the substrate, making them valuable in research and development.
Overall, transparent substrates play a crucial role in numerous technologies where optical clarity, durability, and functionality are essential. Their properties make them indispensable in a wide range of applications across different fields.
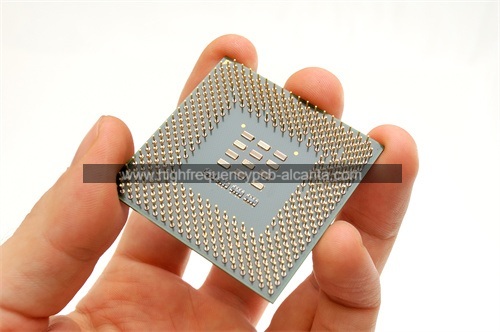
Transparent Substrate Manufacturer
What are the Transparent Substrate Design Guidelines?
Designing with transparent substrates involves several key considerations to ensure optimal performance and functionality. Here are some essential guidelines:
- Material Selection: Choose a substrate material that meets the specific requirements of your application, such as optical clarity, mechanical strength, thermal stability, and chemical resistance. Common choices include glass, quartz, plastics, and transparent conductive oxides (TCOs).
- Surface Quality: Ensure the substrate surface is free from defects, such as scratches, pits, or contamination, which can affect optical performance. Surface polishing or coating may be necessary to achieve the desired smoothness and cleanliness.
- Thickness: Determine the appropriate substrate thickness based on mechanical requirements and optical properties. Thicker substrates offer better mechanical strength but may introduce more optical distortion. Thinner substrates provide higher optical clarity but may be more susceptible to damage.
- Coating Considerations: If additional functionalities are required, such as anti-reflective coatings, scratch-resistant coatings, or conductive layers for electronics, select compatible coating materials and deposition methods. Coatings should enhance the substrate’s performance without sacrificing transparency.
- Alignment and Assembly: When integrating transparent substrates into devices or systems, ensure precise alignment and assembly to avoid optical misalignment or distortion. Use suitable adhesives or bonding techniques that do not introduce optical artifacts or degrade transparency.
- Environmental Considerations: Consider the operating environment of the application, including temperature, humidity, and exposure to chemicals or UV radiation. Choose substrate materials and coatings that can withstand environmental stresses without degradation.
- Testing and Quality Control: Implement rigorous testing protocols to verify the optical and mechanical properties of transparent substrates, both during manufacturing and after assembly into final products. Ensure consistency and reliability through quality control measures.
- Safety: Transparent substrates, especially glass, can pose safety hazards if broken or mishandled. Incorporate safety features such as shatter-resistant coatings or protective enclosures to mitigate risks, particularly in applications where human interaction is involved.
By following these design guidelines, engineers and designers can effectively harness the potential of transparent substrates in various applications while ensuring optimal performance, reliability, and safety.
What is the Transparent Substrate Fabrication Process?
The fabrication process for transparent substrates varies depending on the material and specific requirements of the application. However, here is a generalized overview of the fabrication process for glass substrates, which is one of the most common transparent substrate materials:
- Raw Material Selection: High-quality raw materials, typically silica sand, limestone, and soda ash, are selected based on their purity and composition to ensure the desired optical and mechanical properties of the glass substrate.
- Batch Mixing: The raw materials are mixed in precise proportions and then melted in a furnace at temperatures exceeding 1500°C (2700°F). This melting process removes impurities and homogenizes the glass mixture.
- Forming: The molten glass is shaped into the desired form, such as sheets or rods, through various forming techniques like floating, rolling, or drawing. The choice of forming method depends on the desired substrate thickness and surface finish.
- Annealing: The formed glass substrate undergoes an annealing process, where it is slowly cooled in a controlled manner to relieve internal stresses and improve its mechanical strength and thermal stability. This step is crucial for minimizing optical distortion and ensuring uniformity across the substrate.
- Cutting and Finishing: The annealed glass is cut into individual substrates of the desired size and shape using precision cutting tools. The edges may be polished to remove any sharp edges or imperfections that could affect handling or optical performance.
- Surface Treatment: Depending on the application, the glass substrate may undergo additional surface treatments or coatings to enhance its functionality. This could include applying anti-reflective coatings, scratch-resistant coatings, or conductive layers for electronics.
- Quality Control: Throughout the fabrication process, rigorous quality control measures are implemented to ensure the optical, mechanical, and dimensional properties of the transparent substrates meet the specified requirements. This may involve various testing techniques such as optical inspection, mechanical testing, and surface analysis.
- Packaging and Shipping: The finished transparent substrates are carefully packaged to protect them from damage during transportation and storage. Proper packaging materials and handling procedures are employed to ensure the substrates reach their destination in pristine condition.
Overall, the fabrication process for transparent substrates involves multiple steps aimed at producing high-quality materials with the desired optical clarity, mechanical strength, and surface characteristics required for a wide range of applications.
How do you manufacture a Transparent Substrate?
Manufacturing transparent substrates involves several steps tailored to the specific material and application requirements. Here’s a generalized outline of the manufacturing process:
- Material Preparation: The first step involves sourcing high-quality raw materials appropriate for the desired substrate material. For example, if making glass substrates, silica sand, limestone, and soda ash are commonly used. These materials are carefully selected for purity and consistency.
- Batching and Mixing: The raw materials are weighed and mixed in precise proportions according to the desired composition of the substrate. This mixture, known as the batch, is thoroughly homogenized to ensure uniformity.
- Melting:The batch is then fed into a furnace where it is melted at high temperatures, typically exceeding 1500°C (2700°F). The molten material is maintained at a consistent temperature to achieve proper homogenization and removal of impurities.
- Shaping: Once melted, the material is formed into the desired shape. This can be done through various methods such as casting, pressing, rolling, or drawing, depending on the material and substrate thickness required.
- Cooling and Annealing: After shaping, the substrate undergoes a controlled cooling process called annealing. This relieves internal stresses and enhances the substrate’s mechanical strength and thermal stability. Proper annealing is crucial for minimizing optical distortion and ensuring uniformity.
- Cutting and Sizing: The annealed substrate is cut into individual pieces of the desired size and shape using precision cutting tools. This step ensures that the substrates meet the dimensional requirements of the intended application.
- Surface Treatment: Depending on the application, the substrate may undergo surface treatments or coatings to enhance its properties. For example, anti-reflective coatings can improve optical transmission, while scratch-resistant coatings can increase durability.
- Quality Control: Throughout the manufacturing process, stringent quality control measures are employed to ensure the substrates meet the specified requirements. This may include optical inspection, mechanical testing, and surface analysis to verify the substrate’s optical clarity, mechanical strength, and surface finish.
- Packaging and Shipping: Finally, the finished substrates are carefully packaged to protect them from damage during transportation and storage. Proper packaging materials and handling procedures are employed to ensure the substrates arrive at their destination in optimal condition.
By following these manufacturing steps and adhering to strict quality control protocols, manufacturers can produce transparent substrates with the desired properties for a wide range of applications in optics, electronics, and other industries.
How much should a Transparent Substrate cost?
The cost of a transparent substrate can vary widely depending on several factors:
- Material:The type of material used for the substrate significantly influences its cost. Glass substrates, for example, can vary in price depending on factors such as thickness, optical clarity, and specialty coatings. Other materials like quartz or specialized polymers may have different cost structures.
- Size and Thickness: Larger or thicker substrates typically require more material and may involve additional processing steps, leading to higher costs. The dimensions and thickness of the substrate needed for a particular application will impact its price.
- Surface Quality: Substrates with higher surface quality, such as those with polished or optically coated surfaces, may command a higher price due to the additional processing involved in achieving these specifications.
- Customization: Customization options, such as specific dimensions, shapes, or specialized coatings tailored to unique application requirements, can increase the cost of the substrate.
- Volume and Quantity: Like many manufactured products, the cost per unit of transparent substrates often decreases with increasing order volume. Bulk orders may be eligible for volume discounts, reducing the overall cost.
- Supplier and Market Dynamics: Prices can vary between suppliers based on factors such as manufacturing capabilities, location, and market demand. Additionally, market conditions, including material availability and fluctuations in raw material costs, can influence substrate prices over time.
- Additional Services: Additional services such as surface treatment, quality assurance testing, or specialized packaging may incur extra costs depending on the supplier’s offerings.
Given these factors, it’s challenging to provide a specific cost without knowing the details of the substrate’s requirements and the supplier’s pricing structure. However, transparent substrates are typically priced based on factors such as material, size, thickness, customization, and market dynamics. Customers should obtain quotes from multiple suppliers and consider various factors to determine the most cost-effective option for their specific application.
What is Transparent Substrate base material?
Transparent substrates can be made from a variety of materials, each offering different properties and characteristics suitable for various applications. Some common base materials for transparent substrates include:
- Glass: Glass is one of the most widely used materials for transparent substrates due to its excellent optical clarity, high chemical resistance, and mechanical durability. It can be produced in various compositions and forms, such as soda-lime glass, borosilicate glass, or quartz glass, to meet specific application requirements.
- Quartz: Quartz, or fused silica, is a type of glass known for its exceptional purity, high thermal stability, and resistance to thermal shock. It is often used in applications requiring high transmission of ultraviolet (UV) light, such as in optics, semiconductor manufacturing, and UV curing processes.
- Plastic Films: Transparent plastic films, such as polyethylene terephthalate (PET), polycarbonate (PC), or acrylic (PMMA), are lightweight and flexible substrates commonly used in displays, packaging, and electronics. They offer advantages such as low cost, ease of fabrication, and compatibility with roll-to-roll manufacturing processes.
- Transparent Conductive Oxides (TCOs): TCOs, such as indium tin oxide (ITO), fluorine-doped tin oxide (FTO), or zinc oxide (ZnO), combine transparency with electrical conductivity, making them ideal for applications like touchscreens, solar cells, and flat-panel displays.
- Sapphire: Sapphire is a single-crystal form of aluminum oxide (Al2O3) known for its exceptional hardness, scratch resistance, and optical transparency across a broad spectrum. It is commonly used as a substrate material in high-performance optical windows, lenses, and electronic devices.
- Silicon: While silicon is not naturally transparent in the visible spectrum, it can be processed into transparent substrates through techniques such as thinning or microfabrication. Silicon substrates are widely used in applications such as microelectromechanical systems (MEMS), sensors, and photonic devices.
The choice of base material for a transparent substrate depends on factors such as optical requirements, mechanical properties, cost considerations, and specific application needs. Each material offers distinct advantages and limitations, and selecting the most suitable substrate material is essential for achieving optimal performance in various applications.
Which company makes Transparent Substrates?
Many companies produce transparent substrates, focusing on manufacturing different types to meet the needs of various industries and applications. Some well-known manufacturers of transparent substrates include tech giants such as Corning, Epson, Borosil, AGC, Sony, Samsung, LG Display, and more. These companies have extensive experience and technological expertise in glass, plastic films, transparent conductive oxides, and other materials.
Our company is also one of the manufacturers of transparent substrates, specializing in producing high-quality, customized substrates to meet specific customer requirements. We have advanced production equipment and a skilled technical team capable of providing various material and processing options, including glass, plastic films, transparent conductive oxides, and more. Our production processes strictly adhere to quality management systems and have passed various certifications and testing standards to ensure that our products meet customer requirements and industry standards.
Our strengths include:
- Customization: We can customize transparent substrates according to customer-specific requirements, including dimensions, shapes, materials, and special coatings.
- Quality Assurance:We strictly control the production process to ensure stable and reliable product quality that meets industry standards and customer requirements.
- Technical Support:We have a professional technical team capable of providing technical support and solutions to help customers achieve project success.
- Timely Delivery: We prioritize delivery times, ensuring that orders are completed on time and products are delivered to customers promptly.
In summary, our company is committed to providing customers with high-quality, customized transparent substrate products. Through professional technical support and high-quality service, we aim to establish long-term and stable cooperative relationships with our customers.
What are the 7 qualities of good customer service?
Good customer service is characterized by several key qualities that contribute to positive interactions and customer satisfaction. Here are seven qualities:
- Responsiveness: A good customer service representative responds promptly to customer inquiries, concerns, and requests. They acknowledge customers’ needs in a timely manner and provide assistance or information promptly.
- Empathy: Empathy involves understanding and acknowledging the customer’s feelings, perspectives, and needs. A good customer service representative demonstrates empathy by listening attentively, showing understanding, and expressing genuine concern for the customer’s situation.
- Professionalism: Professionalism entails maintaining a courteous and respectful demeanor, adhering to company policies and standards, and conducting oneself with integrity and reliability. Good customer service representatives maintain professionalism in their interactions with customers, regardless of the situation.
- Knowledgeability: Knowledgeability refers to possessing a thorough understanding of the company’s products, services, policies, and processes. Good customer service representatives are well-informed and can provide accurate and helpful information to address customer inquiries and resolve issues effectively.
- Problem-Solving Skills: Good customer service involves the ability to identify and resolve customer problems or issues efficiently and effectively. Customer service representatives should be resourceful, proactive, and creative in finding solutions that meet the customer’s needs and expectations.
- Adaptability: Adaptability involves being flexible and responsive to changing customer needs, preferences, and situations. Good customer service representatives can adapt their approach and communication style to accommodate different customer personalities, preferences, and communication channels.
- Follow-Up and Follow-Through:Good customer service extends beyond the initial interaction. It involves following up with customers to ensure their needs have been met satisfactorily and following through on any promises or commitments made during the interaction. This demonstrates accountability and reinforces trust and confidence in the company.
By embodying these qualities, companies can deliver exceptional customer service experiences that foster loyalty, satisfaction, and positive brand perception.
FAQS
What are transparent substrates?
Transparent substrates are materials that allow light to pass through them with minimal distortion or absorption. They serve as the base or foundation for various applications in optics, electronics, and engineering. Common examples include glass, quartz, plastic films, and transparent conductive oxides.
What are the typical thicknesses available for transparent substrates?
The thickness of transparent substrates can vary widely based on the material and application. Common thicknesses range from a few micrometers (for thin plastic films) to several millimeters (for glass or quartz substrates). Custom thicknesses can also be produced to meet specific requirements.
Can transparent substrates be customized?
Yes, transparent substrates can be customized in terms of size, shape, thickness, and surface treatments. Customization options may include specific coatings (anti-reflective, scratch-resistant), patterning, and tailored optical or electrical properties.
How do you ensure the quality of transparent substrates?
Quality assurance involves rigorous testing and inspection at various stages of the manufacturing process. This includes optical inspections, mechanical strength testing, surface quality assessments, and adherence to industry standards and certifications.
What are the key considerations for storing and handling transparent substrates?
Transparent substrates should be stored in a clean, dry environment to prevent contamination and damage. Handling should be done with care to avoid scratches, cracks, and other physical damage. Protective packaging is often used to ensure safe transportation and storage.