Top 10 Packaging Substrate Manufacturer
Top 10 Packaging Substrate Manufacturer,The Top 10 Packaging Substrates encompass a range of cutting-edge materials and designs, tailored to meet the demands of modern electronic devices. These substrates feature advanced technologies such as flip chip, organic, and high-speed packaging, enabling superior performance and reliability. With precise manufacturing processes and optimized designs, they ensure efficient signal transmission, thermal management, and space utilization. The Top 10 Packaging Substrates play a crucial role in various industries including consumer electronics, automotive, and telecommunications, driving innovations in semiconductor packaging. Their versatility and quality make them essential for achieving optimal functionality and form factor in electronic products.
Nailing down the “top 10” packaging substrates can be a bit like navigating a labyrinth, with industry trends, application intricacies, and technological leaps shaping the landscape. Yet, let’s zoom in on some heavyweight packaging substrates that wield considerable influence in the electronics arena:
FR-4 (Flame Retardant 4): The workhorse of printed circuit boards (PCBs), FR-4 brings a combo of electrical insulation, mechanical brawn, and wallet-friendly vibes.
FR-5: Think FR-4, but with a heat-resistant upgrade. Ideal when things start sizzling.
High-Temperature Laminates: These substrates are the heat-resilient warriors, carving a niche in the realms of automotive, aerospace, and heavy-duty industrial applications.
Flex PCB (Flexible Printed Circuit Board): Picture this as the gymnast of electronics, bending and contorting for wearable tech, medical marvels, and vehicles that demand flexibility.
Metal Core PCB (MCPCB): Sporting a metal core (usually aluminum or copper), MCPCBs are the cool cats, adept at dissipating heat. They shine in high-power LED setups, power converters, and auto electronics.
Ceramic Substrates: The thermal champs, ceramics boast high conductivity and a resilience to extreme temperatures. They’re the VIPs of high-power electronics and RF/microwave applications.
HDI (High-Density Interconnect) PCBs: HDI PCBs play the smart card, using advanced manufacturing wizardry to pack in more wiring and shrink features. Think compact designs and pristine signal integrity.
Rigid-Flex PCBs: The shape-shifters of circuit boards, offering both backbone and flexibility. Perfect for tasks demanding a bit of both, like intricate geometries or devices with a penchant for movement.
Polyimide Films: Light on their feet yet tough as nails, polyimide films bring stability and chemical resistance to the table. Ideal for flexible circuits and the demanding realms of aerospace and auto applications.
COB (Chip-on-Board) Substrates: Skipping the packaging theatrics, COB substrates take the direct route, planting semiconductor chips right onto the substrate. They’re the unsung heroes behind the scenes of LED lighting and microelectronic assembly.
These substrates each carve out a niche, donning specific roles in the ever-evolving drama of the electronics world.
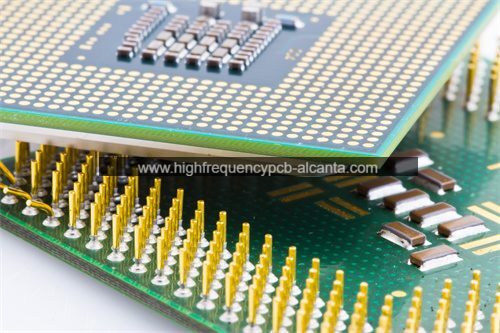
Top 10 Packaging Substrate Manufacturer
What is the Function of Top 10 Packaging Substrate?
The top 10 packaging substrates are akin to the unsung heroes in the electronic symphony, each wielding a distinctive prowess that contributes to the harmonious functioning of electronic devices. Let’s unravel the tapestry of their functionalities:
FR-4 (Flame Retardant 4): Serves as the stalwart cornerstone for printed circuit boards (PCBs), providing an amalgamation of electrical insulation, mechanical robustness, and a budget-friendly demeanor.
FR-5: A kin to FR-4 but with a flair for tackling higher temperatures, making it the go-to maestro for applications cranking up the heat.
High-Temperature Laminates: Stands as the resilient shield against extreme temperatures, carving its niche in the realms of automotive, aerospace, and industrial domains where thermal resistance takes center stage.
Flex PCB (Flexible Printed Circuit Board): Takes on the role of the electronic contortionist, allowing components to dance with flexibility. Found in the limelight of wearable tech, medical marvels, and automobiles embracing flexibility.
Metal Core PCB (MCPCB): The cool cat of heat dissipation, leading the charge in high-power realms like LED lighting, power converters, and the dynamic landscape of automotive electronics.
Ceramic Substrates: The thermal virtuosos, boasting high conductivity and a penchant for heat dissipation. They claim their spotlight in high-power electronics and RF/microwave spectacles.
HDI (High-Density Interconnect) PCBs: The savvy strategist, employing advanced manufacturing wizardry to cram in more wiring and shrink features. Think of them as the architects behind sleek designs and pristine signal integrity.
Rigid-Flex PCBs: The shape-shifters of circuit boards, offering a harmonious blend of structure and flexibility. Tailored for performances demanding intricate geometries or devices choreographed for movement.
Polyimide Films: Lightweight and flexible, these films bring stability and chemical resilience to the stage. Often cast in roles requiring flexibility, such as in aerospace and automotive applications.
COB (Chip-on-Board) Substrates: The minimalist performers, skipping the elaborate packaging drama to directly mount semiconductor chips onto the substrate. They play backstage heroes in the realms of LED lighting and microelectronic assembly.
Together, these substrates compose a symphony, each playing its unique tune to orchestrate the seamless functionality of electronic devices. The selection of these substrates dances to the specific rhythms dictated by the diverse demands of applications and industry standards.
What Are the Different Types of Top 10 Packaging Substrate?
Absolutely! The top 10 packaging substrates are like a diverse cast, each playing a unique role in the electronic stage. Let’s take a stroll through the characters within this esteemed lineup:
FR-4 (Flame Retardant 4): The solid foundation of printed circuit boards (PCBs), FR-4 brings a budget-friendly yet robust performance with top-notch electrical insulation and mechanical strength.
FR-5: Evolving from FR-4, FR-5 steps into the spotlight with a knack for handling higher temperatures, making it the go-to performer for applications with a thermal twist.
High-Temperature Laminates: Crafted to endure the heat, these laminates find their spotlight in arenas like automotive, aerospace, and industries where facing extreme temperatures is part of the daily script.
Flex PCB (Flexible Printed Circuit Board): The flexible virtuoso, this substrate dances to the rhythm of bending and shaping, perfect for wearable tech, medical marvels, and the dynamic world of automotive electronics.
Metal Core PCB (MCPCB): With a metal core, usually aluminum or copper, MCPCBs conduct the performance of efficient heat dissipation. They take center stage in high-power LED setups, power converters, and the intricate domain of automotive electronics.
Ceramic Substrates: The thermal conductors, ceramics shine in high-power electronics and the sophisticated world of RF/microwave applications.
HDI (High-Density Interconnect) PCBs: Precision masters, HDI PCBs weave intricate wiring densities and smaller features, orchestrating designs with finesse and ensuring impeccable signal integrity.
Rigid-Flex PCBs: Balancing structure and flexibility, these boards are the performers tailor-made for applications demanding both – be it intricate geometries or devices with a penchant for movement.
Polyimide Films: Lightweight and adaptable, polyimide films bring to the stage stellar thermal stability and chemical resistance. They play prominent roles in flexible circuits, aerospace ventures, and the dynamic realm of automotive applications.
COB (Chip-on-Board) Substrates: The minimalist contributors, COB substrates skip the elaborate packaging drama and dive straight into mounting semiconductor chips. They are the unsung heroes backstage, playing crucial roles in LED lighting and microelectronic assembly.
Each substrate type adds its unique flavor to the ensemble of materials available for crafting the electronic narrative. The selection choreography revolves around the specific demands of each application, embracing considerations of thermal dynamics, flexibility prerequisites, and the intricate nuances of electronic landscapes.
What is the Relationship Between Top 10 Packaging Substrate and IC Packaging?
The intricate dance between the top 10 packaging substrates and the realm of IC (Integrated Circuit) packaging is akin to a finely orchestrated performance, where each player contributes its unique notes to the symphony of electronic device creation. Here’s a reimagined exploration of their interconnected roles:
Substrate Foundations: Enter the stage, packaging substrates like FR-4, metal core PCBs, and ceramics, crafting the fundamental canvas for IC packaging. They lay the groundwork, providing the essential structural support and electrical connectivity for integrated circuits.
Thermal Maestros: Among the performers, metal core PCBs and ceramics emerge as the thermal maestros. Their ability to conduct the heat ballet ensures a harmonious temperature equilibrium, preventing the ICs from breaking into a feverish performance.
Electrical Isolation Elegance: FR-4, the virtuoso of electrical insulation, takes the lead in the IC packaging orchestra. It weaves an intricate layer of protection, shielding the electronic signals within integrated circuits from short circuits and maintaining a pristine performance.
Flexibility and Compact Choreography: On the flexible stage, flex PCBs and rigid-flex PCBs gracefully pirouette, allowing the creation of compact, adaptable IC packaging solutions. This choreography is especially captivating in the era of modern, miniaturized electronic devices.
Signal Purity (HDI): Enter the avant-garde HDI PCBs, the custodians of signal purity in the IC packaging realm. Their intricate techniques create a symphony of minimal interference, ensuring that the electronic signals within integrated circuits resonate with clarity.
Direct Artistry (COB): In a daring move, Chip-on-Board (COB) substrates rewrite the IC packaging script. They bypass the conventional packaging theatrics, directly mounting semiconductor chips and elevating the performance to a minimalist, yet powerful crescendo.
Application-Specific Ballet: The stage adapts to the demands of the performance – wearables demanding flexibility, high-temperature laminates performing an automotive ballet. Each substrate takes on a role crafted for the unique demands of the application.
Economic Ensemble: In the economic ensemble, substrates like FR-4 play a vital tune. Their cost-effectiveness adds a pragmatic note to the IC packaging symphony, resonating particularly well in the realm of consumer electronics.
In essence, the collaboration between the top 10 packaging substrates and IC packaging is a grand symphony. The selection of a substrate is a choreographed dance, dictated by the unique needs of the integrated circuit, the nuances of the application, and the desired harmonies of performance. Together, they create a tapestry of encapsulation, protection, and functionality, weaving the intricate story of electronic devices.
How Does Top 10 Packaging SubstrateDiffer from Regular PCBs?
Imagine the distinction between the top 10 packaging substrates and regular PCBs as a choice between custom-designed haute couture and ready-to-wear fashion. Each serves a unique purpose, tailored to meet the specific needs of diverse electronic scenarios.
Specialized Craftsmanship:
Top 10 Packaging Substrates: These substrates are the epitome of bespoke elegance in the electronic realm. Selected for their exceptional qualities, they cater to specific demands such as advanced thermal management, flexibility, or signal integrity. It’s akin to choosing a custom-tailored suit that fits the nuances of the occasion perfectly.
Regular PCBs: Regular PCBs are the reliable, off-the-rack wardrobe staples. Like everyday attire, they are versatile and suitable for a wide range of electronic applications but lack the specialized features found in their bespoke counterparts.
Material Palette:
Top 10 Packaging Substrates: This category showcases a diverse material gallery – FR-4, FR-5, metal core PCBs, ceramics – each selected for its unique role. It’s akin to choosing fabrics of distinct textures and qualities for a custom-designed ensemble.
Regular PCBs: In contrast, regular PCBs often rely on standard materials like FR-4, akin to opting for widely accepted fabrics that strike a balance between cost and functionality.
Niche Attributes:
Top 10 Packaging Substrates: These substrates boast niche attributes tailored for specific applications. Imagine flex PCBs gracefully adapting to dynamic environments or metal core PCBs conducting heat with the precision of a well-crafted accessory.
Regular PCBs: Regular PCBs lack these specialized features but are akin to timeless, classic pieces that serve well in a variety of scenarios.
Runway Presence:
Top 10 Packaging Substrates: Strutting down the industry runway, these substrates take the spotlight in high-tech sectors such as electronics, telecommunications, aerospace, and automotive, where a bespoke performance is a must.
Regular PCBs: Regular PCBs are the versatile ensembles that find a place in an array of electronic devices, much like reliable fashion pieces that never go out of style.
Cost Dynamics:
Top 10 Packaging Substrates: Some substrates, such as metal core PCBs or ceramics, command a higher price reflecting the craftsmanship and specialized features they bring to the electronic runway.
Regular PCBs: Regular PCBs, like affordable yet dependable fashion choices, meet the needs of electronic devices without a premium price tag.
In essence, while regular PCBs offer a wide array of utility, the top 10 packaging substrates are the haute couture designers, meticulously creating solutions to meet the exacting standards of advanced electronic devices. The choice between them is akin to deciding whether to opt for the tailored elegance of specialized features or the reliable versatility of off-the-shelf convenience.
What are the Main Structures and Production Technologies of Top 10 Packaging Substrate?
Embarking on a journey through the top 10 packaging substrates is akin to unraveling a diverse tapestry of structures and production technologies, where each substrate plays a unique role in the grand symphony of electronics. Let’s take a stroll through this electronic gallery, where architectural wonders and production techniques coalesce:
FR-4 (Flame Retardant 4):
Structural Canvas: FR-4 unfolds as a composite masterpiece, with layers of woven fiberglass cloth immersed in epoxy resin. A multilayer canvas that often features intricate copper traces.
Crafting Ballet: The production choreography involves layering fiberglass sheets, infusing them with epoxy, and a series of steps like etching and deposition to introduce the copper layers.
FR-5:
Structure Symphony: A close kin of FR-4, FR-5 joins the narrative with a twist – enhanced thermal properties. The dance continues with the epoxy-infused fiberglass waltz.
Production Tale: The production saga echoes FR-4 but adds an encore, tuning the resin system to harmonize with higher temperatures.
High-Temperature Laminates:
Structured Palette: A canvas that varies, often painted with high-temperature-resistant substrates like polyimide or PTFE.
Crafting Technique: Crafting involves layering and bonding, where the choice of substrate and resin systems choreograph a performance stable at elevated temperatures.
Flex PCB (Flexible Printed Circuit Board):
Flexible Composition: Crafted from flexible materials like polyimide or polyester, these boards showcase a composition that bends to the electronic melody.
Production Choreography: Techniques blend etching, layering, and a lamination ballet of flexible materials. The production stage may feature the avant-garde of additive manufacturing or the classic subtlety of subtractive methods.
Metal Core PCB (MCPCB):
Metallic Harmony: Featuring a metal core (aluminum or copper) that conducts the thermal symphony, accompanied by dielectric insulating layers and a top layer for circuit traces.
Production Ballet: Involves drilling, etching, and the bonding of metal cores with insulating layers. The narrative pivots around thermal management considerations.
Ceramic Substrates:
Ceramic Canvas: Composed of ceramics like alumina or aluminum nitride, these substrates paint a canvas of high thermal conductivity.
Crafting Saga: The journey involves sintering, where ceramic powders fuse into solid structures. Subsequent processes include the dance of machining, metallization, and etching.
HDI (High-Density Interconnect) PCBs:
Density Drama: The stage is set with high wiring densities, multiple layers, and microvias for a compact design spectacle.
Production Symphony: The narrative unfolds with advanced techniques – laser drilling for microvias, sequential lamination for layer buildup, and fine-line etching to amplify wiring density.
Rigid-Flex PCBs:
Hybrid Harmony: Marrying rigid and flexible substrates in a dynamic dance, allowing for 3D configurations.
Crafting Ensemble: Involves layering rigid and flexible materials, featuring additive manufacturing processes like flex additive circuitry and sequential lamination for layer buildup.
Polyimide Films:
Film Elegance: Thin, flexible films crafted from polyimide, the haute couture of high-temperature-resistant polymers.
Crafting Ballet: The film production unfolds through casting or extrusion, with subsequent acts involving etching, metallization, and layer lamination for the flexible circuit narrative.
COB (Chip-on-Board) Substrates:
Chip Integration Symphony: A minimalist canvas where semiconductor chips take center stage, skipping the traditional packaging theatrics.
Production Minimalism: The process includes die attachment, wire bonding or flip-chip bonding, and a finale of encapsulation. COB substrates are the maestros of miniaturization.
In this electronic symphony, each substrate contributes its unique notes, creating a harmonious blend of craftsmanship and functionality in the world of technology.
Frequently Asked Questions (FAQs)
What makes FR-4 a preferred choice for PCBs?
FR-4 stands out due to its composite excellence, seamlessly blending woven fiberglass cloth and epoxy resin to create a durable and electrically insulating canvas for intricate circuitry.
How does High-Temperature Laminates differ from standard substrates?
High-Temperature Laminates take center stage with a varied canvas, incorporating heat-resistant materials like polyimide or PTFE. This distinctive choice sets them apart in applications where temperature resilience is paramount.
Can you elaborate on the dance of flexibility in Flex PCBs?
Flex PCBs showcase a dynamic composition, akin to a flexible garment made from materials like polyimide or polyester. This allows them to elegantly bend and adapt to the electronic rhythm, ideal for applications demanding flexibility.
What role does the metal core play in Metal Core PCBs?
Metal Core PCBs take the stage with metallic harmony, featuring a robust metal core (aluminum or copper) that conducts the thermal symphony. This exceptional core, accompanied by insulating layers, sets the tone for efficient heat dissipation.
How do Ceramic Substrates contribute to electronic elegance?
Ceramic Substrates emerge as a canvas of ceramic elegance, composed of materials like alumina or aluminum nitride. This unique composition offers high thermal conductivity, making them the choice for applications demanding both style and substance.
What defines the density drama in HDI PCBs?
HDI PCBs take center stage with density drama, featuring high wiring densities, multiple layers, and microvias that amplify the design spectacle. Their intricate production techniques create a symphony of compact design possibilities.
How do Rigid-Flex PCBs gracefully navigate the design landscape?
Rigid-Flex PCBs waltz through the design landscape with hybrid harmony, seamlessly marrying rigid and flexible substrates. This dynamic dance allows for 3D configurations, adding a touch of flexibility to the rigid design world.
What sets Polyimide Films apart in the electronic fashion show?
Polyimide Films take the stage with film elegance, showcasing thin, flexible films crafted from the haute couture of high-temperature-resistant polymers. Their graceful performance includes casting, extrusion, and subsequent acts of etching and lamination.
How do Chip-on-Board (COB) Substrates redefine minimalism in chip integration?
COB Substrates step into the limelight with chip integration symphony, embodying a minimalist canvas where semiconductor chips take center stage. Their production minimalism involves die attachment, wire bonding or flip-chip bonding, and a finale of encapsulation.
Which substrate takes the lead in miniaturization in the electronic orchestra?
COB Substrates emerge as the maestros of miniaturization in the electronic orchestra. Their minimalist canvas and direct integration of chips without traditional packaging theatrics make them the avant-garde leaders in compact design.
Conclusion
In conclusion, the top 10 packaging substrates form a diverse ensemble, each contributing its unique notes to the symphony of electronic technology. From the composite excellence of FR-4 to the dynamic flexibility of Flex PCBs, and the metallic harmony of Metal Core PCBs, these substrates play pivotal roles in shaping the landscape of modern electronic devices.
High-Temperature Laminates and Ceramic Substrates showcase resilience and elegance, while HDI PCBs and Rigid-Flex PCBs amplify the design drama with high wiring densities and hybrid harmony, allowing for intricate configurations. Polyimide Films add a touch of haute couture, embodying thin, flexible elegance, while Chip-on-Board (COB) Substrates lead the way in miniaturization, redefining chip integration with minimalist precision.
As we navigate this electronic orchestra, it becomes clear that the choice of substrate is not just a technical decision but an artistic one, where craftsmanship and functionality intertwine. The constant evolution of production technologies ensures that these substrates continue to set the stage for innovative electronic solutions.
In this symphony of substrates, whether it’s the heat-resistant prowess of materials or the direct integration minimalism of COB Substrates, each element plays a crucial role in harmonizing form and function. As technology advances, these substrates will undoubtedly continue to compose the ever-evolving melody of electronic innovation.