Thin Film Substrate Manufacturers
Thin Film Substrate Manufacturers,Thin film substrates serve as the foundation for depositing thin films in various electronic, optical, and sensor devices. These substrates, made from materials like silicon, glass, or ceramics, provide a stable surface for precise thin film deposition processes such as PVD or CVD. Tailored to specific applications, thin film substrates enable the creation of advanced integrated circuits, photovoltaic cells, and MEMS devices. Their properties, including thermal stability, electrical conductivity, and optical transparency, play a critical role in determining the performance and functionality of the final product.
What is a Thin Film Substrate?
A Thin Film Substrate refers to a material layer upon which thin films are deposited or grown for various applications in electronics, optics, and other fields. These substrates are typically flat surfaces made from materials like silicon, glass, or various types of ceramics. The thin film deposition process involves techniques such as physical vapor deposition (PVD) or chemical vapor deposition (CVD), where atoms or molecules from a source material are deposited onto the substrate surface, forming a thin film.
Thin film substrates are crucial in the manufacturing of electronic devices such as integrated circuits (ICs), photovoltaic cells, and thin-film transistors. They provide a stable platform for the growth of thin films with controlled properties like thickness, composition, and crystal structure, which are essential for the performance and functionality of the final device.
These substrates can also be engineered to have specific properties such as high thermal conductivity, low electrical resistance, or optical transparency, depending on the requirements of the thin film application. Additionally, the choice of substrate material can influence factors like film adhesion, mechanical stability, and compatibility with other materials in the device structure.
In summary, thin film substrates play a critical role in the fabrication of various electronic and optical devices by providing a foundation for the deposition of thin films with tailored properties to meet specific performance criteria.
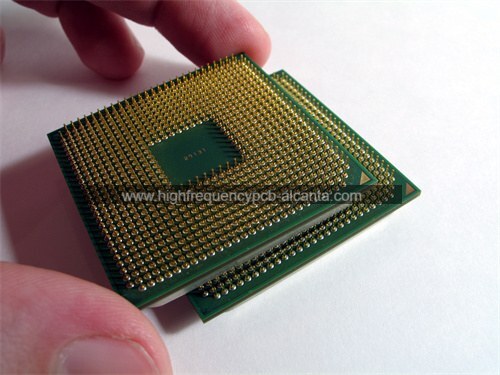
Thin Film Substrate Manufacturers
What are Thin Film Substrate Design Guidelines?
Thin film substrate design guidelines are principles and recommendations aimed at optimizing the performance and reliability of thin film-based devices. These guidelines encompass various aspects of substrate selection, preparation, and handling to ensure successful thin film deposition and device fabrication. Here are some key design guidelines:
- Material Selection: Choose substrate materials compatible with the thin film deposition technique and the intended application. Common substrate materials include silicon, glass, quartz, and specialized ceramics.
- Surface Preparation: Ensure the substrate surface is clean, smooth, and free from contaminants or defects that could adversely affect thin film quality. Cleaning methods may include solvent cleaning, plasma treatment, or chemical etching.
- Surface Roughness: Minimize surface roughness to promote uniform thin film growth and adherence. Smooth substrates facilitate the formation of defect-free thin films with improved electrical and optical properties.
- Temperature Stability:Select substrates with thermal properties that match the requirements of the thin film deposition process. Stable temperature control is crucial to achieve consistent film growth and avoid thermal stress-induced defects.
- Chemical Compatibility: Consider the chemical compatibility between the substrate material and thin film materials, deposition precursors, and processing environments. Incompatible materials may lead to film delamination, reaction, or degradation.
- Dimensional Stability:Choose substrates with low thermal expansion coefficients to minimize dimensional changes during temperature cycling, which can cause mechanical strain and reliability issues in thin film devices.
- Electrical Properties: Optimize substrate electrical properties such as resistivity, dielectric constant, and conductivity to meet the requirements of the thin film device design. Substrate conductivity can influence device performance and signal integrity.
- Optical Transparency: For optoelectronic applications, select substrates with high optical transparency in the desired wavelength range to minimize light absorption and maximize device efficiency.
- Adhesion Promotion: Employ surface treatments or adhesion layers to enhance the adhesion between the substrate and thin film. Proper adhesion promotes mechanical stability and prevents delamination or peeling of the thin film.
- Handling and Packaging: Implement proper handling procedures and packaging techniques to protect substrates from damage or contamination during transportation, storage, and processing.
By following these thin film substrate design guidelines, engineers and researchers can optimize thin film device performance, reliability, and yield, leading to successful fabrication of advanced electronic, optical, and microelectromechanical systems (MEMS) devices.
What is the Thin Film Substrate Fabrication Process?
The thin film substrate fabrication process involves several steps aimed at preparing a suitable substrate for the deposition of thin films. Here’s a general overview of the process:
- Substrate Selection: Choose a substrate material based on the requirements of the thin film application. Common substrate materials include silicon, glass, quartz, and various ceramics. Consider factors such as thermal properties, electrical conductivity, optical transparency, and chemical compatibility.
- Cleaning and Surface Preparation: Thoroughly clean the substrate surface to remove contaminants, oils, and particles that could interfere with thin film deposition or affect film quality. Cleaning methods may include solvent cleaning, ultrasonic cleaning, or plasma treatment. Surface roughness may also be controlled through mechanical polishing or chemical etching.
- Deposition of Adhesion Layers (if needed): In some cases, adhesion layers may be deposited on the substrate surface to promote strong bonding between the substrate and the subsequent thin film layers. Adhesion layers are particularly important when using substrates with low surface energy or when depositing thin films with different crystal structures.
- Thin Film Deposition:Once the substrate is prepared, thin film deposition techniques such as physical vapor deposition (PVD), chemical vapor deposition (CVD), atomic layer deposition (ALD), or sputtering are employed to deposit thin films onto the substrate surface. These techniques involve the deposition of atoms or molecules from a vapor phase onto the substrate, forming a thin film with controlled thickness, composition, and structure.
- Annealing or Post-Processing (optional): After thin film deposition, the substrate may undergo annealing or post-processing steps to improve film crystallinity, remove defects, or induce desired structural changes. Annealing is commonly performed in a controlled atmosphere at elevated temperatures to enhance film properties and relieve internal stresses.
- Characterization and Quality Control: Perform various characterization techniques such as scanning electron microscopy (SEM), atomic force microscopy (AFM), X-ray diffraction (XRD), and spectroscopic analysis to assess thin film quality, thickness, morphology, and structural properties. Quality control measures ensure that the fabricated thin film substrates meet the desired specifications and performance criteria.
- Packaging and Protection: Once the thin film substrate fabrication process is complete, the substrates may be packaged and protected using appropriate materials to prevent contamination, oxidation, or physical damage during handling, storage, and transportation.
By following these steps, researchers and engineers can fabricate thin film substrates tailored to specific applications, ranging from electronic devices and photovoltaic cells to sensors, optical coatings, and microelectromechanical systems (MEMS). Each step in the fabrication process is carefully controlled to achieve the desired thin film properties and performance characteristics.
How do you manufacture a Thin Film Substrate?
Manufacturing a thin film substrate involves several key steps, from selecting the base material to depositing the thin film layers. Here’s a detailed overview of the manufacturing process:
- Substrate Selection: Choose a substrate material that suits the requirements of the thin film application. Common substrate materials include silicon, glass, quartz, sapphire, and various ceramics. Consider factors such as thermal stability, mechanical strength, electrical properties, and compatibility with the thin film materials.
- Cleaning and Surface Preparation: Thoroughly clean the substrate surface to remove any contaminants, oils, or particles that could interfere with thin film deposition or affect film quality. Cleaning methods may include solvent cleaning, ultrasonic cleaning, or plasma treatment. Surface roughness may also be controlled through mechanical polishing or chemical etching.
- Deposition of Adhesion Layers (if needed): In some cases, adhesion layers may be deposited on the substrate surface to promote strong bonding between the substrate and the subsequent thin film layers. Adhesion layers are particularly important when using substrates with low surface energy or when depositing thin films with different crystal structures.
- Thin Film Deposition: Utilize thin film deposition techniques such as physical vapor deposition (PVD), chemical vapor deposition (CVD), atomic layer deposition (ALD), or sputtering to deposit thin films onto the substrate surface. These techniques involve the deposition of atoms or molecules from a vapor phase onto the substrate, forming a thin film with controlled thickness, composition, and structure.
- Annealing or Post-Processing (optional):After thin film deposition, the substrate may undergo annealing or post-processing steps to improve film crystallinity, remove defects, or induce desired structural changes. Annealing is commonly performed in a controlled atmosphere at elevated temperatures to enhance film properties and relieve internal stresses.
- Characterization and Quality Control: Perform various characterization techniques such as scanning electron microscopy (SEM), atomic force microscopy (AFM), X-ray diffraction (XRD), and spectroscopic analysis to assess thin film quality, thickness, morphology, and structural properties. Quality control measures ensure that the fabricated thin film substrates meet the desired specifications and performance criteria.
- Packaging and Protection: Once the thin film substrate manufacturing process is complete, the substrates may be packaged and protected using appropriate materials to prevent contamination, oxidation, or physical damage during handling, storage, and transportation.
By following these steps, manufacturers can produce thin film substrates tailored to specific applications, including electronic devices, photovoltaic cells, sensors, optical coatings, and microelectromechanical systems (MEMS). Each step in the manufacturing process is carefully controlled to achieve the desired thin film properties and performance characteristics.
How much should a Thin Film Substrate cost?
The cost of a thin film substrate can vary significantly depending on several factors such as substrate material, size, thickness, surface quality, and any additional processing or customization required. Here are some key factors that influence the cost:
- Substrate Material: Different substrate materials have varying costs. Silicon substrates are commonly used and relatively affordable, while substrates made from specialized materials like sapphire or quartz may be more expensive.
- Size and Thickness: Larger substrates or substrates with greater thickness typically cost more due to the increased material usage and processing requirements.
- Surface Quality: Substrates with higher surface quality, smoother surfaces, and lower defect densities may command a premium price due to the additional processing steps involved in achieving these properties.
- Customization: If the substrate requires specific customization such as patterned surfaces, specialized coatings, or unique geometries, the cost may increase to accommodate these additional manufacturing steps.
- Quantity: Bulk purchasing or ordering large quantities of substrates may result in volume discounts, reducing the cost per unit.
- Supplier and Manufacturing Process:The choice of supplier and the manufacturing process used can also impact the cost. Substrates produced using advanced manufacturing techniques or by reputable suppliers may have higher price points.
- Additional Processing: Any additional processing steps such as deposition of adhesion layers, thin film deposition, annealing, or post-processing may add to the overall cost of the thin film substrate.
It’s essential to consider the specific requirements of your application and balance the cost with the desired substrate properties and performance. Additionally, obtaining quotes from multiple suppliers and comparing prices can help in identifying the most cost-effective option while ensuring the quality and reliability of the thin film substrate.
What is Thin Film Substrate base material?
The base material for a thin film substrate is the underlying layer upon which thin films are deposited or grown. These base materials must possess specific properties suitable for the intended application and deposition process. Here are some common base materials used for thin film substrates:
- Silicon (Si): Silicon is the most widely used substrate material in the semiconductor industry. It is valued for its excellent mechanical properties, thermal conductivity, and well-understood processing techniques. Silicon substrates are commonly used in the fabrication of integrated circuits, photovoltaic cells, and MEMS devices.
- Glass: Glass substrates are used for applications requiring transparency and optical clarity, such as displays, optical coatings, and solar panels. Glass is also electrically insulating and chemically stable, making it suitable for various electronic and optoelectronic applications.
- Quartz (Fused Silica): Quartz substrates offer high thermal stability, excellent optical transparency across a wide range of wavelengths, and low thermal expansion. They are used in applications such as optical devices, high-frequency electronics, and photolithography.
- Sapphire (Al₂O₃): Sapphire substrates are known for their exceptional hardness, high thermal conductivity, and excellent optical properties. They are commonly used in optoelectronic devices, LEDs, and high-power electronics due to their ability to withstand harsh environments and high temperatures.
- Ceramics: Various ceramic materials such as alumina (Al₂O₃), silicon carbide (SiC), and zirconia (ZrO₂) are used as substrates for thin films. These materials are chosen for their high-temperature stability, mechanical strength, and electrical insulation properties. They are often used in high-temperature electronics, sensors, and protective coatings.
- Polymers: Flexible polymer substrates, such as polyethylene terephthalate (PET) and polyimide (PI), are used for flexible electronics, wearable devices, and roll-to-roll processing. Polymers are lightweight, flexible, and can be processed at lower temperatures, making them suitable for applications where flexibility and lightweight are crucial.
- Metals: Metal substrates like aluminum, copper, and stainless steel are used when high electrical conductivity and thermal management are required. They are commonly used in power electronics, flexible electronics, and certain types of sensors.
Each base material offers distinct advantages and limitations, so the choice of substrate material depends on factors such as the desired electrical, optical, thermal, and mechanical properties, as well as the compatibility with the thin film deposition process and the specific requirements of the application.
Which company makes Thin Film Substrates?
There are many companies that manufacture thin film substrates, and some of the major manufacturers include Micron Technology, Intel, AGC Inc. (formerly Asahi Glass), Epson, Panasonic, and others. These companies have extensive experience and expertise in various fields such as semiconductors, optoelectronics, display devices, solar cells, and more, providing a wide range of thin film substrate products with different materials and specifications.
As for our company, we also have the capability to produce thin film substrates, offering high-quality customized solutions to our customers. With advanced production equipment and a skilled technical team, we can meet the diverse needs of different application areas.
Firstly, our company has years of experience and expertise, providing comprehensive technical support and consulting services to customers. Our team possesses rich experience in thin film preparation and can customize substrates with various materials, thicknesses, and surface properties according to customer requirements.
Secondly, we employ advanced production processes and quality control systems to ensure stable and reliable product quality. We strictly adhere to the ISO quality management system and regularly inspect and adjust the production process to ensure that our products meet customer specifications.
Additionally, we focus on innovation and continuous improvement, constantly introducing new technologies and equipment to enhance production efficiency and product quality. We collaborate with customers to develop new materials and processes, providing solutions to meet the changing market demands.
In conclusion, our company has the capability and experience to produce thin film substrates, offering customized solutions to meet customer needs while ensuring product quality and delivery time. We are committed to establishing long-term and stable cooperation with customers, achieving mutual success.
What are the 7 qualities of good customer service?
Good customer service is characterized by several key qualities that contribute to positive experiences for customers. Here are seven essential qualities:
- Responsiveness: Good customer service involves being prompt and proactive in addressing customer inquiries, concerns, and requests. Responding to customer needs in a timely manner demonstrates attentiveness and a commitment to customer satisfaction.
- Empathy: Empathy involves understanding and acknowledging the customer’s emotions, concerns, and perspectives. Customer service representatives who demonstrate empathy can establish rapport with customers, build trust, and provide personalized assistance that meets the customer’s needs.
- Professionalism: Professionalism encompasses maintaining a courteous, respectful, and professional demeanor when interacting with customers. It involves effective communication, active listening, and adherence to company policies and standards.
- Knowledgeability: Good customer service representatives are knowledgeable about the products or services offered by the company. They possess a deep understanding of the features, benefits, and usage of the products/services, allowing them to provide accurate information and guidance to customers.
- Problem-solving skills: Effective problem-solving skills are crucial in resolving customer issues and concerns efficiently and effectively. Customer service representatives should be able to identify problems, analyze situations, and offer appropriate solutions or alternatives to address customer needs.
- Consistency: Consistency in service delivery is essential for building trust and loyalty with customers. Consistent service standards, policies, and procedures ensure that customers receive a uniform experience across different interactions and touchpoints with the company.
- Follow-up and feedback:Good customer service involves following up with customers after resolving their inquiries or issues to ensure satisfaction and gather feedback. Following up demonstrates care and concern for the customer’s experience and provides an opportunity to improve service quality based on customer input.
By embodying these qualities, companies can deliver exceptional customer service experiences that foster customer loyalty, retention, and positive word-of-mouth recommendations.
FAQs (Frequently Asked Questions)
What are the common materials used for thin film substrates?
Common materials include silicon, glass, quartz, sapphire, various ceramics, and flexible polymers.
What are thin film substrates used for?
Thin film substrates are used in a wide range of applications, including integrated circuits (ICs), photovoltaic cells, sensors, optical coatings, and microelectromechanical systems (MEMS).
What deposition techniques are used to deposit thin films onto substrates?
Deposition techniques include physical vapor deposition (PVD), chemical vapor deposition (CVD), atomic layer deposition (ALD), sputtering, and others.
How do I choose the right thin film substrate for my application?
Consider factors such as material properties (e.g., thermal conductivity, electrical conductivity, optical transparency), compatibility with the deposition process, mechanical stability, and cost.
What are some common challenges in thin film substrate fabrication?
Challenges include achieving uniform film deposition, controlling film thickness and morphology, minimizing defects, ensuring good adhesion between the film and substrate, and optimizing substrate properties for specific applications.
How can I characterize the quality of thin film substrates?
Characterization techniques include scanning electron microscopy (SEM), atomic force microscopy (AFM), X-ray diffraction (XRD), spectroscopic analysis, and electrical testing.
What are some best practices for handling and storing thin film substrates?
Handle substrates with care to avoid contamination or damage. Store substrates in a clean, dry environment away from direct sunlight and extreme temperatures.