Thick Film Substrates Manufacturer
Thick Film Substrates Manufacturer,Thick film substrates serve as the sturdy foundation for electronic circuits, facilitating the deposition of conductive, resistive, and dielectric materials. Composed of ceramic materials like alumina or aluminum nitride, these substrates enable the integration of various components for diverse applications. Through a meticulous manufacturing process involving screen printing and firing, thick film substrates ensure reliable performance in automotive electronics, consumer gadgets, and aerospace systems. Their versatility, cost-effectiveness, and thermal stability make them indispensable in modern electronics, embodying the backbone of countless electronic devices worldwide.
What is a Thick Film Substrate?
A thick film substrate refers to a type of material base used primarily in the manufacture of electronic circuits, where electronic components such as resistors, capacitors, and conductors are applied onto a non-conductive substrate material using thick film technology. This technique involves the deposition of a paste-like mixture of glass and electronic components onto the substrate, followed by high-temperature firing to create the final electronic circuit.
The substrates used in thick film technology are typically made from ceramics such as alumina, aluminum nitride, or beryllium oxide. These materials are chosen for their excellent electrical insulation properties, high thermal conductivity, and stability under varying environmental conditions. The thickness of the films applied onto these substrates generally ranges from a few micrometers to several tens of micrometers, which is significantly thicker than the films used in thin film technology.
In the manufacturing process, the conductive, resistive, and dielectric materials are typically prepared as pastes, which include a mixture of functional particles, a glass frit (for binding the particles upon firing), and an organic vehicle (for screen printing application). These pastes are then deposited onto the substrate using screen printing techniques. Once printed, the substrate is fired at temperatures that can reach up to 850°C, which causes the glass frit to melt and bond the particles to the substrate, thus forming robust electronic circuits.
Thick film substrates are widely used in various applications, including automotive electronics, consumer electronics, and aerospace components, due to their reliability, cost-effectiveness, and versatility in design.
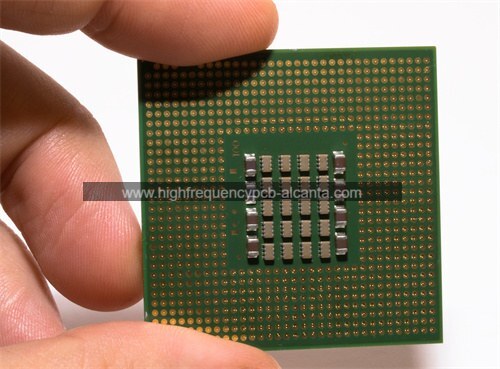
Thick Film Substrates Manufacturer
What are Thick Film Substrate Design Guidelines?
Designing with thick film substrates requires adherence to certain guidelines to ensure optimal performance and reliability of the electronic circuits. Here are some key design guidelines:
- Substrate Material Selection: Choose a substrate material that meets the requirements of the specific application in terms of thermal conductivity, electrical insulation, mechanical strength, and compatibility with the intended fabrication process.
- Layer Thickness: Determine the appropriate thickness of the thick film layers based on the electrical and mechanical requirements of the circuit. This includes considerations for conductor trace width, resistor thickness, and dielectric layer thickness.
- Layer Alignment and Registration: Ensure precise alignment and registration of different layers during fabrication to prevent short circuits or open circuits. Misalignment can lead to electrical discontinuities or reduced reliability.
- Conductor Width and Spacing: Design conductor traces with appropriate width and spacing to meet the electrical performance requirements, such as impedance control, signal integrity, and current-carrying capacity. Consider the manufacturing capabilities and tolerances of the fabrication process.
- Resistor Design: Design resistors with the desired resistance value and power rating, taking into account factors such as resistor material, dimensions, and temperature coefficient of resistance (TCR). Optimize resistor geometries for accuracy, stability, and thermal performance.
- Dielectric Layer Design: Specify the dielectric material properties, thickness, and layout to achieve the desired electrical insulation between conductive traces and components. Consider dielectric constant, breakdown voltage, and thermal conductivity of the dielectric material.
- Component Placement and Layout: Plan the placement and layout of components on the substrate to minimize signal interference, thermal gradients, and mechanical stress. Optimize component placement for efficient routing of traces and signal integrity.
- Thermal Management:Incorporate thermal vias, heat sinks, or other thermal management techniques to dissipate heat generated by high-power components or operating conditions. Ensure adequate thermal conductivity and dissipation paths to prevent overheating and performance degradation.
- Environmental Considerations: Design the substrate and components to withstand environmental stresses such as temperature extremes, humidity, vibration, and mechanical shock. Use materials and coatings that provide protection against corrosion, moisture ingress, and other environmental factors.
- Testing and Quality Assurance: Implement testing and quality assurance protocols to validate the performance and reliability of the thick film substrate design. Conduct electrical testing, thermal cycling, and reliability testing to verify compliance with specifications and standards.
By following these design guidelines, engineers can create thick film substrate designs that meet the requirements for a wide range of electronic applications while ensuring robust performance and reliability.
What is the Thick Film Substrate Fabrication Process?
The fabrication process of thick film substrates involves several steps to deposit and pattern thick film layers onto a substrate material. Here’s a general overview of the process:
- Substrate Preparation: The process begins with preparing the substrate material, typically a ceramic such as alumina or aluminum nitride. The substrate is cleaned and inspected to ensure its surface is free from contaminants and defects.
- Thick Film Paste Preparation: Next, thick film pastes are prepared for the deposition of conductive, resistive, and dielectric layers. These pastes consist of finely dispersed functional materials (such as conductive particles for conductors, resistive materials for resistors, and dielectric materials for insulating layers), along with a binder and solvent.
- Screen Printing: The thick film pastes are deposited onto the substrate using screen printing techniques. A stencil or screen with the desired pattern is placed over the substrate, and the paste is forced through the openings onto the substrate surface using a squeegee. This process defines the layout of conductive traces, resistors, and dielectric layers on the substrate.
- Drying: After screen printing, the substrate is dried to remove the solvent from the thick film paste. This step is typically done using a conveyor oven or infrared heating to evaporate the solvent and bind the functional materials to the substrate.
- Firing: The dried substrate with the deposited thick film layers is then fired in a high-temperature furnace. During firing, the substrate is heated to temperatures typically ranging from 600°C to 900°C, depending on the materials and process requirements. The firing process sinters the functional materials, fuses them to the substrate, and removes the organic binder, resulting in a dense and stable thick film layer.
- Post-Fire Processing: After firing, the substrate may undergo additional processing steps, such as laser trimming of resistors to achieve precise resistance values or applying protective coatings to enhance durability and reliability.
- Testing and Quality Assurance: The fabricated thick film substrate undergoes thorough testing to verify its electrical properties, dimensional accuracy, and reliability. Electrical testing may include measurements of resistance, capacitance, and insulation resistance, as well as functional testing of integrated circuits or components.
By following these fabrication steps, manufacturers can produce thick film substrates with precise patterns and tailored electrical properties for various electronic applications, such as hybrid integrated circuits, sensors, and thick film resistors.
How do you manufacture Thick Film Substrates?
Manufacturing thick film substrates involves a series of steps to create precise patterns of conductive, resistive, and dielectric materials on a substrate. Here’s an overview of the manufacturing process:
- Substrate Preparation: The process begins with preparing the substrate material, which is typically a ceramic material such as alumina (Al2O3), aluminum nitride (AlN), or beryllium oxide (BeO). The substrate is cleaned thoroughly to remove any contaminants and prepared for subsequent processing steps.
- Thick Film Paste Preparation:Thick film pastes containing conductive, resistive, and dielectric materials are formulated according to the desired specifications. These pastes consist of finely powdered functional materials, such as silver for conductors, ruthenium oxide for resistors, and glass frits for dielectric layers, mixed with a binder and solvent.
- Screen Printing: The thick film pastes are deposited onto the substrate using screen printing techniques. A stencil or screen with the desired pattern is placed over the substrate, and the paste is forced through the openings onto the substrate surface using a squeegee. This process defines the layout of conductive traces, resistors, and dielectric layers on the substrate.
- Drying: After screen printing, the substrate is dried to remove the solvent from the thick film paste. This step is typically done using a conveyor oven or infrared heating to evaporate the solvent and solidify the binder, leaving behind the functional materials on the substrate.
- Firing: The dried substrate with the deposited thick film layers is fired in a high-temperature furnace. During firing, the substrate is heated to temperatures typically ranging from 600°C to 900°C, depending on the materials and process requirements. The firing process sinters the functional materials, fuses them to the substrate, and removes the organic binder, resulting in a dense and stable thick film layer.
- Post-Fire Processing: After firing, the substrate may undergo additional processing steps, such as laser trimming of resistors to achieve precise resistance values or applying protective coatings to enhance durability and reliability.
- Testing and Quality Assurance:The fabricated thick film substrate undergoes thorough testing to verify its electrical properties, dimensional accuracy, and reliability. Electrical testing may include measurements of resistance, capacitance, and insulation resistance, as well as functional testing of integrated circuits or components.
By following these manufacturing steps, manufacturers can produce thick film substrates with precise patterns and tailored electrical properties for various electronic applications, such as hybrid integrated circuits, sensors, and thick film resistors.
How much should a Thick Film Substrate cost?
The cost of a thick film substrate can vary widely depending on several factors, including the substrate material, size, complexity of the design, required tolerances, and the manufacturing process used. Here are some factors that influence the cost:
- Substrate Material: Different ceramic materials have varying costs. Alumina (Al2O3) is commonly used and tends to be less expensive compared to specialized ceramics like aluminum nitride (AlN) or beryllium oxide (BeO), which can be more costly due to their unique properties.
- Size and Thickness: Larger substrates or thicker layers may require more material and processing time, which can increase the cost. Conversely, smaller substrates or thinner layers may be less expensive.
- Complexity of Design: The complexity of the circuit design, including the number of layers, fine features, and precision requirements, can impact the cost. Intricate designs with tight tolerances may require more advanced manufacturing techniques, leading to higher costs.
- Manufacturing Process: The choice of manufacturing process, such as screen printing versus photolithography, can influence the cost. Photolithography-based processes, while more precise, may be more expensive than screen printing for certain applications.
- Volume and Batch Size: Larger production volumes often lead to economies of scale, resulting in lower costs per unit. However, smaller batch sizes or custom orders may incur higher costs due to setup and tooling expenses.
- Additional Processes: Post-processing steps such as laser trimming, coating, or testing can add to the overall cost of the thick film substrate.
- Supplier and Location: The cost can also vary depending on the supplier, their capabilities, and geographic location. Labor costs, overheads, and material availability in different regions can impact the final price.
Due to these factors, it’s challenging to provide a specific cost without knowing the details of the substrate requirements. Generally, thick film substrates can range in cost from a few dollars to several hundred dollars per unit, with customized or specialized substrates potentially costing even more. For accurate pricing, it’s best to consult with manufacturers or suppliers who can provide quotes based on your specific project needs.
What is Thick Film Substrate base material?
Thick film substrates are typically made from ceramic materials due to their excellent electrical insulation properties, thermal conductivity, and stability under varying environmental conditions. The most commonly used ceramic materials for thick film substrates include:
- Alumina (Al2O3): Alumina is one of the most widely used materials for thick film substrates. It offers good electrical insulation, high mechanical strength, and thermal stability. Alumina substrates are cost-effective and suitable for a wide range of electronic applications.
- Aluminum Nitride (AlN): Aluminum nitride exhibits high thermal conductivity, making it suitable for applications requiring efficient heat dissipation. AlN substrates are often used in high-power electronic devices and applications where thermal management is critical.
- Beryllium Oxide (BeO): Beryllium oxide offers exceptionally high thermal conductivity, surpassed only by diamond among ceramics. However, BeO is less commonly used due to health and safety concerns associated with beryllium exposure during processing. Its use is restricted in many regions.
- Titanium Dioxide (TiO2): Titanium dioxide substrates are less common but offer good electrical properties and are suitable for certain applications. TiO2 substrates are often used in specialized thick film circuits.
These ceramic materials provide a stable and durable base for the deposition of thick film layers, including conductive traces, resistors, and dielectric materials. The choice of substrate material depends on factors such as electrical requirements, thermal management needs, cost considerations, and compatibility with the manufacturing process.
Which company makes Thick Film Substrates?
Many companies manufacture thick film substrates, including major manufacturers like Murata Manufacturing Co., Ltd. in Japan, Kyocera and DuPont in the United States, and Heraeus Group in Germany. These companies possess advanced manufacturing technologies and extensive experience, enabling them to produce various types and specifications of thick film substrates to meet the needs of different industries.
As for our company, we are also a specialized manufacturer of thick film substrates. We have advanced production equipment and a skilled technical team capable of providing high-quality, customized thick film substrate solutions. Our production process covers multiple steps from substrate preparation to printing, drying, and firing of thick film layers, ensuring the stability and reliability of our products.
As a thick film substrate manufacturer, our advantages include:
- Customization Capability: We can customize thick film substrates in various specifications, materials, and designs according to customer requirements, meeting the needs of different industries and applications.
- High-Quality Production: We employ advanced production processes and strict quality control systems to ensure stable and reliable product quality.
- Fast Delivery:With efficient production capacity and supply chain management, we can deliver thick film substrates to customers promptly, meeting their production schedules.
- Technical Support: We have a professional technical team and after-sales service team to provide technical support and solutions, ensuring customers achieve optimal performance and experience when using our products.
In summary, as a specialized manufacturer of thick film substrates, we are committed to providing customers with high-quality, customized products, and excellent services to help them meet their application requirements and business goals.
What are the 7 qualities of good customer service?
Good customer service is characterized by several key qualities that contribute to positive customer experiences and satisfaction. Here are seven important qualities:
- Responsiveness: Good customer service involves promptly addressing customer inquiries, concerns, and requests. Responding in a timely manner demonstrates attentiveness and a commitment to meeting customer needs.
- Empathy: Empathy involves understanding and acknowledging the customer’s perspective, emotions, and concerns. It entails listening actively, showing compassion, and demonstrating genuine care for the customer’s situation.
- Clarity: Clear communication is essential for effective customer service. Providing accurate information, instructions, and explanations in a concise and understandable manner helps prevent misunderstandings and confusion.
- Professionalism: Professionalism encompasses maintaining a courteous and respectful demeanor in all interactions with customers. It involves being knowledgeable, reliable, and courteous while representing the company positively.
- Problem-solving skills: Effective customer service involves the ability to identify and resolve customer issues and complaints efficiently. Being proactive in finding solutions and taking ownership of problems enhances customer satisfaction.
- Flexibility: Flexibility is important in adapting to individual customer needs and preferences. Being willing to accommodate reasonable requests, offering personalized solutions, and being open to feedback contribute to a positive customer experience.
- Consistency: Consistency in delivering high-quality service across all interactions and touchpoints is crucial for building trust and loyalty with customers. Consistent service standards, policies, and procedures help establish reliability and reliability.
By embodying these qualities, organizations can cultivate a customer-centric culture and foster strong relationships with their customers, leading to improved satisfaction, loyalty, and advocacy.
FAQs
What are thick film substrates?
Thick film substrates are material bases used in electronic circuit manufacturing, where electronic components like resistors, capacitors, and conductors are applied onto a non-conductive substrate using thick film technology.
What materials are used for thick film substrates?
Common materials for thick film substrates include ceramics such as alumina (Al2O3), aluminum nitride (AlN), and beryllium oxide (BeO). These materials offer excellent electrical insulation and thermal properties.
What are the advantages of thick film substrates?
Thick film substrates offer advantages such as cost-effectiveness, versatility in design, and reliability. They can accommodate a wide range of electronic components and are suitable for various applications, including automotive electronics, consumer electronics, and aerospace components.
How are thick film substrates manufactured?
The manufacturing process of thick film substrates involves steps such as substrate preparation, preparation of thick film pastes, screen printing of pastes onto the substrate, drying, firing in a high-temperature furnace, and post-fire processing.
What are the applications of thick film substrates?
Thick film substrates are used in various electronic applications, including hybrid integrated circuits, sensors, thick film resistors, RF and microwave components, power modules, and LED packaging.
What are the design considerations for thick film substrates?
Design considerations include substrate material selection, layer thickness, conductor width and spacing, resistor design, dielectric layer design, component placement and layout, thermal management, and environmental considerations.
What are the key properties to look for in thick film substrates?
Key properties include electrical insulation, thermal conductivity, mechanical strength, dimensional stability, compatibility with fabrication processes, and reliability under environmental conditions.
Where can I purchase thick film substrates?
Thick film substrates can be purchased from various suppliers and manufacturers specializing in electronic components and materials. It’s essential to choose a reputable supplier that offers high-quality products and reliable customer service.