Substrate Packaging Manufacturer
Substrate Packaging Manufacturer,Substrate packaging is a pivotal process in semiconductor manufacturing, involving the encapsulation and connection of integrated circuits (ICs) to substrates. It encompasses various techniques to mount and interconnect ICs onto substrates, ensuring electrical connections and thermal management. Substrate packaging utilizes advanced materials and precise manufacturing processes to meet the stringent demands of modern electronics. It plays a crucial role in optimizing signal transmission, power distribution, and reliability in electronic devices. Substrate packaging supports diverse applications across industries, from consumer electronics to automotive and aerospace, driving advancements in technology and enabling innovative solutions for complex electronic systems.
Substrate packaging invites us to delve into the nuanced arena of fortifying the essential components nestled within electronic gadgets, commonly known as substrates. Imagine substrates as the unsung heroes, cradling vital elements like semiconductors and sensors that power our electronic devices. The packaging process steps into the shoes of a vigilant guardian, erecting a shield to protect these components from external adversaries such as moisture, dust, and temperature fluctuations.
This intricate undertaking involves a delicate choreography of material selection, the artistry of designing packaging structures, and the integration of features like thermal management, electromagnetic shielding, and electrical interconnections. The overarching objective is to sculpt a robust armor for our electronic components, not just shielding them from harm but also aiding them in maintaining their poise amidst the thermal rigors of operation.
The collective brilliance steering substrate packaging spans diverse engineering realms—from the alchemy of materials science to the precision of mechanical engineering, electrical engineering, and thermal management. Their collaborative mission is to ensure that our electronic devices not only hit the high notes of performance but also exhibit unwavering resilience in the face of the unpredictable challenges of the real world. Additionally, they navigate the maze of industry regulations and standards, ensuring these devices toe the line.
In the ever-evolving theater of cutting-edge technologies, including advanced semiconductor packaging and microelectronics, substrate packaging takes center stage. As our gadgets undergo a metamorphosis, becoming more compact, intelligent, and seamlessly integrated into our daily lives, the quest for avant-garde substrate packaging solutions intensifies. This entails an ongoing pursuit of pioneering materials, unconventional packaging designs, and refined manufacturing processes to harmonize with the dynamic demands of the electronics ecosystem.
In essence, substrate packaging dons the hat of a custodian, tailoring superhero suits for our electronic devices, ensuring not only their aesthetic allure but also their unyielding resilience in the face of real-world tribulations.
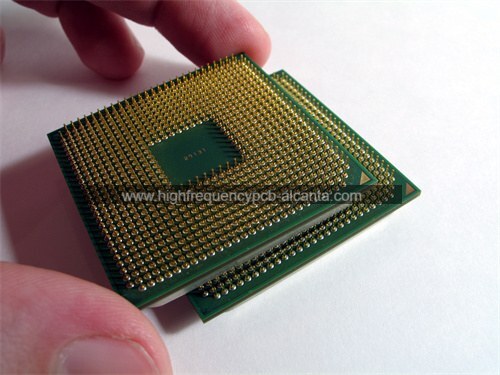
Substrate Packaging Manufacturer
What are the functions of Substrate Packaging?
Substrate packaging can be likened to the unsung hero in the electronic device orchestra, playing a crucial symphony of functions to harmonize the performance and longevity of our gadgets. Let’s unravel the diverse roles this packaging ensemble undertakes:
Guardian Against External Threats:
Assumes the role of a vigilant guardian, shielding sensitive electronic components from the elements—fending off moisture, dust, and other potential hazards.
Environmental Bastion:
Constructs a fortress against environmental adversaries such as shifts in humidity, temperature fluctuations, and exposure to chemicals, ensuring the internal components remain unscathed.
Temperature Maestro:
Takes on the responsibility of managing the device’s temperature dynamics, adeptly dissipating the heat generated during operation to prevent any overheating debacles.
EMI Minimizer:
Functions as an electromagnetic interference maestro, orchestrating a serene electronic environment to allow components to communicate without unwanted disruptions.
Electrical Maestro:
Provides a stage for electrical connections, choreographing a seamless dance of information flow between components to orchestrate the device’s overall functionality.
Structural Pillar:
Stands as a sturdy pillar, offering structural support to prevent the delicate components from succumbing to the rigors of daily handling and potential shocks.
Size Magician:
Exhibits magical prowess by enabling the miniaturization of devices, a vital act for the sleek and portable gadgets dominating the contemporary tech landscape.
Compliance Sentinel:
Takes on the role of a compliance sentinel, ensuring that electronic devices adhere to industry standards and regulations, a key performance in the symphony of safety and environmental responsibility.
Assembly Choreographer:
Acts as a meticulous choreographer in the manufacturing process, orchestrating the seamless integration of electronic components to bring the device to life.
Cost-Efficiency Virtuoso:
Plays a virtuoso tune in cost-efficiency, averting potential component failures and device malfunctions, thus reducing the financial strains of repairs and replacements.
Reliability Virtuoso:
Elevates the reliability of electronic devices to virtuoso levels, ensuring a smooth performance without disruptions or breakdowns.
In essence, substrate packaging is the unseen conductor, weaving a tapestry of functions that ensures electronic devices not only perform optimally but also endure the rigors of the real-world stage.
What are the different types of Substrate Packaging?
Substrate packaging emerges as a versatile array, intricately fashioned to cater to the nuanced demands and functionalities of electronic devices. Let’s traverse the landscape of some standout variations:
Chip-on-Board (COB):
Simplifying the narrative, COB involves the direct placement of a bare semiconductor chip onto a printed circuit board (PCB), establishing connections through the artistry of wire bonding or flip-chip technology.
Ball Grid Array (BGA):
Unveiling an organized ensemble of solder balls, BGA packages solder the semiconductor device onto a substrate, typically a PCB. This choreography not only elevates thermal efficiency but also conducts a symphony of streamlined form factors.
Quad Flat Package (QFP):
Embracing a sleek surface-mount aesthetic, QFP unveils leads extending gracefully from all four sides of the package. It finds its rhythm as a preferred choice for microcontrollers and a variety of integrated circuits.
Dual In-line Package (DIP):
Stepping into the realm of nostalgia, DIP packaging presents parallel rows of leads extending from the sides. While it may be less ubiquitous in today’s electronic tapestry, it holds echoes of significance from a bygone era.
Chip Scale Package (CSP):
Advocating for the elegance of simplicity, CSP minimizes excess materials, encapsulating the semiconductor chip with a form factor mirroring its intrinsic beauty. This type often takes the stage for miniaturized devices.
System-in-Package (SiP):
Elevating integration to an art form, SiP seamlessly weaves multiple semiconductor devices within a single package, orchestrating a symphony of increased functionality while orchestrating a reduction in form factors.
Through-Hole Technology (THT):
Navigating the currents of tradition, THT unfolds a tale of inserting component leads through PCB holes, soldering them on the opposite side. While less conspicuous in modern electronics, it retains a role in specific applications.
Multi-Chip Module (MCM):
Orchestrating a synergy of components, MCM packages intricately weave multiple semiconductor chips into a harmonious module, unleashing heightened performance and functionality within a confined space.
Flip-Chip Technology:
Embracing the avant-garde, flip-chip technology flips and mounts the semiconductor chip face-down on the substrate, forging direct connections between the chip and its supporting stage.
Wafer-Level Packaging (WLP):
Embracing efficiency as a guiding principle, WLP choreographs the packaging dance at the wafer level before individual chips take center stage. This streamlined approach resonates particularly well in the symphony of high-volume manufacturing.
Flexible Substrate Packaging:
Celebrating the art of adaptability, this type harmonizes with flexible materials like polyimide for the substrate, offering versatility in packaging design. It takes the lead in applications where flexibility emerges as the star.
These packaging variations weave a tapestry of options, addressing the multifaceted needs of electronic devices based on factors like size, thermal dynamics, integration intricacies, and the cadence of cost considerations. The selection of substrate packaging is a meticulous decision, finely tuned to the distinctive requirements of each application and the desired performance attributes of the electronic device.
What is the relationship between Substrate Packaging and IC packaging?
The interplay between substrate packaging and IC (Integrated Circuit) packaging is an integral facet of the electronic ecosystem. While IC packaging takes center stage in encapsulating integrated circuits within protective casings, substrate packaging gracefully twirls into the scene as a crucial subset, specifically concerning the foundation that cradles and interconnects the various electronic components.
In the grand theater of electronics, IC packaging wears multiple hats—it shields delicate integrated circuits, establishes vital electrical connections, and orchestrates effective heat dissipation. Its forms, whether the classic Dual In-line Packages (DIP), the contemporary Surface Mount Devices (SMD), or the intricate Ball Grid Arrays (BGA), all contribute to this symphony of encapsulating semiconductor marvels.
Enter substrate packaging, a co-star with a nuanced role. It shifts the spotlight to the substrate—a foundational material like a printed circuit board (PCB) or alternative substrates like ceramic or organics. This substrate becomes the canvas upon which various electronic components, including integrated circuits, find their stage. It’s not just a physical platform; it conducts the electrical connections, facilitates thermal management, and provides the structural support necessary for the performance art of electronics.
In essence, the relationship is symbiotic. IC packaging relies on substrate packaging for a sturdy and functional stage where its encapsulated integrated circuits can shine. The substrate, in turn, leans on IC packaging to safeguard and enhance the performance of the components it hosts.
Together, they create a harmonious duet—a ballet of protective casings and foundational substrates—that shapes the performance, reliability, and functionality of electronic devices and systems on the grand stage of technology.
How does Substrate Packaging differ from PCB?
Substrate packaging and PCB (Printed Circuit Board) may share the electronic landscape, but their roles and characteristics diverge in fascinating ways. Let’s unravel the distinctive traits that set them apart:
Function and Purpose:
Substrate Packaging: Assumes a central role in providing a sturdy foundation for an ensemble of electronic components, placing a particular emphasis on the intricate world of integrated circuits (ICs). It plays a multifaceted role, navigating the realms of thermal management, electrical connectivity, and structural support.
PCB: Takes on the crucial responsibility of creating an electrical tapestry. Its purpose is to weave a network of pathways that enables the harmonious flow of signals between electronic components, contributing to the overarching functionality of the electronic system.
Components Hosted:
Substrate Packaging: Embraces the diversity of electronic components, from ICs to resistors and capacitors. Its canvas involves intricate designs, often comprising multiple layers and complex configurations to accommodate this diverse electronic orchestra.
PCB: Acts as the gracious host for electronic components but focuses primarily on providing a physical platform for mounting and interconnecting them. Its spotlight is on creating an environment that facilitates seamless electrical connectivity.
Complexity:
Substrate Packaging: Showcases complexity through tailored designs catering to the specific needs of hosted components. Features like vias, ball grid arrays (BGAs), and layers add layers of intricacy to its performance.
PCB: While capable of complexity, its essence lies in the art of routing electrical traces. The challenge is to craft efficient electrical pathways rather than navigating the complexities of diverse electronic elements.
Integration with Integrated Circuits (ICs):
Substrate Packaging: Establishes an intimate connection with ICs and other components, offering an all-encompassing packaging solution that addresses electrical, thermal, and structural demands.
PCB: Plays a supporting role by providing a stable platform for IC integration. Its task is to ensure a solid foundation, whether through socketed or soldered connections, allowing the seamless integration of ICs into the broader electronic narrative.
Applications:
Substrate Packaging: Takes center stage in sophisticated electronic devices, especially those with high integration requirements like microprocessors, memory modules, and intricate electronic systems.
PCB: Graces a myriad of electronic devices, from everyday gadgets to advanced industrial equipment. It stands as the fundamental cornerstone for constructing electronic systems.
In essence, while substrate packaging emerges as the lead performer in the comprehensive packaging of electronic components, the PCB adopts the role of a backstage conductor, ensuring a seamless and reliable electrical performance for the entire electronic symphony.
What are the structure and production technology of Substrate Packaging?
Substrate packaging boasts a nuanced architecture and a production process that unfolds like a well-choreographed performance. Let’s delve into the intricacies of its structure and the technological ballet that brings it to life:
Structure of Substrate Packaging:
Foundation Material: The substrate finds its roots in a foundational material, often a printed circuit board (PCB), ceramic, or advanced alternatives like organic substrates. This material provides the essential support for the electronic components.
Layered Complexity: Substrate packaging often embraces multiple layers stacked together, each playing a specific role. These layers might include conductive layers for electrical pathways, insulating layers, and additional elements to enhance structural robustness.
Circuitry Maze: Conductive traces, frequently crafted from copper, weave intricate patterns across the substrate. These traces act as the nerve system, establishing crucial electrical connections and ensuring seamless signal flow within the electronic realm.
Landing Sites and Pathways: Pads serve as strategic landing sites for component connections, while vias carve pathways traversing various layers, enabling vertical electrical connections. These elements are the keystones ensuring effective electrical conduction.
Production Technology of Substrate Packaging:
Inception in Design: The journey commences with an artful design phase, where engineers sculpt the layout, mapping out component arrangements, electrical trace routes, and the overall structural blueprint. Advanced software lends its prowess in optimizing for both performance and manufacturability.
Material Alchemy: The substrate’s material, a pivotal choice, undergoes careful selection, considering attributes such as thermal conductivity, electrical properties, and structural resilience. Ceramic, organic substrates, and specialized PCB materials cater to diverse needs.
Crafting Circuitry: PCB-based substrates often undergo a dance of printing circuitry patterns onto the substrate, followed by an etching ritual to remove excess copper. This craftily shapes the intricate network of conductive traces.
Additive Mastery: Advanced substrates embrace additive manufacturing techniques like 3D printing or inkjet printing, constructing layers with meticulous precision. This approach allows for fine-tuned control over material composition and structure.
Precision Placement: Automated machinery takes center stage, delicately placing electronic components onto the substrate. This mechanical ballet demands precision to ensure accurate connections and flawless alignment.
Soldering Symphony: Connection points, such as pads and vias, engage in a soldering spectacle. This act securely fastens components to the substrate, contributing to both mechanical and electrical stability.
Performance Evaluation: Rigorous testing and inspection enter the stage, scrutinizing the substrate’s integrity. Checks span electrical continuity, component alignment, and overall functionality, ensuring a flawless performance.
Art of Encapsulation: Some substrates undergo an encore, with the encapsulation of the entire assembly in protective materials. This final act adds an extra layer of defense against environmental elements, mechanical stress, and potential contaminants.
In essence, the structure of substrate packaging emerges as a tapestry of materials and layers, while the production technology orchestrates a meticulously synchronized performance encompassing design, material alchemy, manufacturing finesse, and stringent quality checks. This collaborative symphony yields a foundation that not only supports but elevates the intricate realm of electronic components with grace, precision, and unwavering reliability.
Frequently Asked Questions (FAQs)
What exactly is Substrate Packaging?
Substrate packaging, in the tech world, is the art of crafting a solid foundation for electronic components, especially those elusive integrated circuits (ICs). It’s like the backstage magician that provides structural support, electrical connectivity, and a cool breeze for the gadgets to perform flawlessly.
Substrate Packaging vs. IC Packaging—what’s the deal?
It’s a bit like comparing the stage manager to the lead actor. Substrate packaging focuses on creating the stage—the foundation for all components—while IC packaging is all about dressing up individual integrated circuits in fancy protective attire.
What’s the secret recipe for Substrate Packaging materials?
Think of it as a kitchen—there’s a mix of printed circuit board (PCB) ingredients, ceramics, organic substrates, and sometimes, a touch of flexibility with polyimide for those electronic dishes that need a bit of bend.
How’s the design process for Substrate Packaging like?
Imagine orchestrating a visual feast where engineers use high-tech software to create the perfect layout of conductive traces, place components strategically, and make sure everything looks stunning. It’s like the haute couture of electronic design.
What’s Substrate Packaging’s role in handling the heat?
It’s the cool cat in the electronic world. Substrate packaging ensures that electronic devices don’t break a sweat by offering a platform that efficiently lets go of excess heat. Because nobody wants a hot gadget party.
What are the perks of being a Substrate Packaging expert?
Oh, the perks include top-notch electrical connectivity, solid structural support, heat dissipation like a pro, and the ability to host a variety of electronic elements—all in a sleek, compact package.
Where does Substrate Packaging shine in the tech spotlight?
Substrate packaging loves the limelight in microprocessors, memory modules, integrated circuits, and any tech space that demands a blend of elegance and high integration.
How does Substrate Packaging make tech gadgets shrink?
Think of it as the magic wand for miniaturization. Substrate packaging enables the integration of multiple components in a tight space, making gadgets sleek, compact, and oh-so-portable.
Conclusion
In conclusion, substrate packaging emerges as a crucial player in the intricate landscape of electronic packaging. Its role as the foundational architect for hosting and interconnecting electronic components, particularly integrated circuits, underscores its significance in the realm of technology.
The structure of substrate packaging, a symphony of materials and layers, creates a robust platform that provides structural support, efficient electrical connectivity, and adept thermal management. From the choice of substrate material to the design intricacies, the process is a meticulous dance of precision and technology.
Production technology, akin to a well-choreographed ballet, brings this structure to life. The design phase sets the stage, material selection becomes an artful alchemy, and innovative manufacturing techniques contribute to the production’s avant-garde nature. Automated component placement and vigilant testing ensure the final performance meets the highest standards.
Substrate packaging answers the call for miniaturization, contributing to the sleek designs of modern electronic devices. Its versatility shines in various applications, from microprocessors to integrated circuits, showcasing its adaptability and importance across the technological spectrum.
With its ability to enhance electrical connectivity, provide structural integrity, and efficiently manage thermal dynamics, substrate packaging becomes an unsung hero in the seamless functionality of electronic systems. As technology continues to evolve, the dance of substrate packaging will undoubtedly play a pivotal role in shaping the future of electronic devices, ensuring they stand tall on a foundation that combines precision, reliability, and innovation.