Showa Denko Package Substrate Manufacturer
Showa Denko Package Substrate Manufacturer,Showa Denko Package Substrate (SDPS) represents cutting-edge materials technology for semiconductor packaging. Engineered with precision, SDPS offers superior thermal conductivity, electrical insulation, and mechanical stability, ensuring optimal performance and reliability for semiconductor devices. Its versatile composition, including silicon, ceramics, and organic laminates, caters to diverse industry needs, from telecommunications to automotive and beyond. With Showa Denko’s commitment to innovation and quality, SDPS stands as a cornerstone in advancing electronic systems, enabling compact designs and high-efficiency electronics for the modern world.
What is a Showa Denko Package Substrate?
A Showa Denko Package Substrate (SDPS) is a crucial part of electronic devices, serving as a base for mounting and interconnecting various electronic components. It provides mechanical support and electrical connections for integrated circuits, resistors, capacitors, and other electronic parts.Showa Denko Package Substrate refers to a type of advanced material used in the packaging of semiconductor devices, produced by Showa Denko K.K., a Japanese chemical engineering company. These substrates are essential components in the semiconductor industry, serving as the foundation upon which semiconductor chips are mounted. They provide mechanical support and electrical interconnections between the semiconductor device and the circuit board, facilitating the integration of electronic components into larger systems.
The substrates are typically made from high-performance materials such as silicon, ceramic, or organic laminates, and are designed to offer excellent thermal conductivity, electrical insulation, and mechanical stability. Showa Denko’s package substrates are particularly noted for their high reliability and performance, which are critical in applications requiring robust and durable electronic components.
One of the key innovations of Showa Denko in this field is the development of advanced packaging technologies that enhance the performance of semiconductor devices. These technologies include fine patterning, high-density interconnects, and advanced materials that improve heat dissipation and reduce electrical interference. This is crucial for the miniaturization and performance enhancement of electronic devices, particularly in high-demand sectors such as telecommunications, automotive, and consumer electronics.
Showa Denko’s package substrates also play a significant role in enabling the advancement of semiconductor technologies such as system-in-package (SiP) and chip-on-wafer-on-substrate (CoWoS), which integrate multiple functions into a single package, reducing the overall size and improving the efficiency of electronic systems.
In summary, Showa Denko Package Substrates are integral components in the semiconductor manufacturing process, offering high performance and reliability to support the continued evolution of electronic devices. Their development reflects the ongoing innovation and technological advancements in the materials science and semiconductor industries.
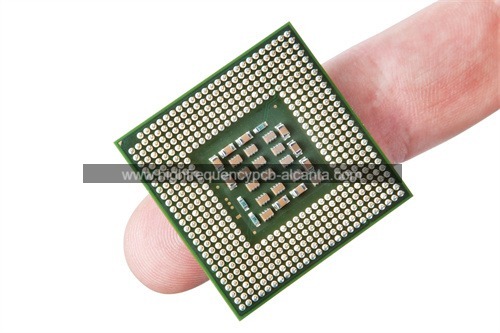
Showa Denko Package Substrate Manufacturer
What are the SDPS Design Guidelines?
The SDPS Design Guidelines, developed by Showa Denko K.K., provide a set of recommendations and specifications for designing and implementing package substrates for semiconductor devices. These guidelines are aimed at ensuring the optimal performance, reliability, and manufacturability of the package substrates. While specific details may vary depending on the application and technology requirements, some common aspects covered in SDPS Design Guidelines may include:
- Material Selection: Recommendations for selecting appropriate substrate materials based on factors such as thermal conductivity, electrical insulation, mechanical strength, and compatibility with manufacturing processes.
- Layer Stackup Design: Guidelines for designing the layer stackup of the substrate, including the number and arrangement of conductive and insulating layers, to meet electrical and mechanical requirements.
- Routing and Wiring Guidelines: Specifications for routing and wiring of signal traces, power planes, and ground planes to minimize signal interference, impedance mismatch, and crosstalk.
- Via Design: Recommendations for via placement, size, and structure to ensure reliable electrical connections between different layers of the substrate and the semiconductor device.
- Thermal Management: Guidelines for designing thermal vias, heat sinks, and other features to enhance heat dissipation and thermal management, critical for maintaining the optimal operating temperature of semiconductor devices.
- Signal Integrity and Power Integrity: Considerations for optimizing signal integrity and power integrity, including controlled impedance design, decoupling capacitor placement, and minimizing noise coupling.
- Manufacturing Constraints: Specifications to account for manufacturing constraints such as minimum feature sizes, aspect ratios, and tolerances to ensure manufacturability and yield.
- Reliability and Testing: Guidelines for evaluating the reliability of the package substrate design, including mechanical stress analysis, thermal cycling tests, and electrical testing to verify performance under various operating conditions.
- Standard Compliance: Compliance with industry standards and specifications, such as JEDEC, IPC, and SEMI, to ensure compatibility and interoperability with other components and systems.
- Documentation and Design Review: Requirements for documenting the design process, materials, and specifications, as well as conducting design reviews to identify and address potential issues early in the development cycle.
Overall, adherence to SDPS Design Guidelines helps semiconductor manufacturers and designers to develop package substrates that meet the stringent requirements of modern electronic devices in terms of performance, reliability, and manufacturability.
What is the SDPS Fabrication Process?
The SDPS (Showa Denko Package Substrate) fabrication process involves several steps to manufacture package substrates for semiconductor devices. While specific details may vary depending on the substrate’s design, material composition, and intended application, a typical fabrication process may include the following key steps:
- Substrate Preparation:The process begins with preparing the substrate material, which could be silicon, ceramic, or organic laminate. This involves cutting the substrate material into the desired size and shape, as well as surface preparation to ensure cleanliness and uniformity.
- Layer Formation:Multiple layers are formed on the substrate using various techniques such as thin-film deposition, photolithography, and etching. These layers may include conductive traces, insulating layers, and via structures. Each layer is precisely patterned and etched to create the required circuitry and interconnects.
- Via Formation: Vias are created to establish electrical connections between different layers of the substrate. This typically involves drilling or laser ablation to create holes in the substrate, followed by filling the vias with conductive material such as copper or tungsten.
- Metallization: Conductive traces and interconnects are formed by depositing metal layers (e.g., copper) onto the substrate surface using techniques like physical vapor deposition (PVD) or electroplating. These metal layers provide electrical pathways for connecting semiconductor devices to external circuitry.
- Die Attach and Wire Bonding: Semiconductor chips are attached to the substrate using die attach materials such as epoxy or solder. Wire bonding techniques are then used to establish electrical connections between the semiconductor chip and the substrate’s conductive traces.
- Encapsulation and Sealing:The assembled substrate is encapsulated and sealed using protective materials such as epoxy resin or molding compounds. This helps to protect the semiconductor devices from environmental factors such as moisture, dust, and mechanical stress.
- Surface Finishing: The substrate’s surface is finished to meet specific requirements such as flatness, smoothness, and solderability. This may involve processes like planarization, chemical mechanical polishing (CMP), and surface treatment.
- Quality Control and Testing: The fabricated substrates undergo rigorous quality control and testing to ensure they meet the required specifications for electrical performance, reliability, and durability. This may include electrical continuity testing, thermal cycling tests, and visual inspection.
- Packaging and Delivery: Once the substrates pass inspection, they are packaged and prepared for delivery to semiconductor manufacturers for further assembly into electronic devices.
Overall, the SDPS fabrication process involves a combination of precision manufacturing techniques and advanced materials to produce package substrates that meet the demanding requirements of modern semiconductor devices. Collaboration with semiconductor manufacturers and adherence to industry standards are essential to ensure the reliability and performance of the final products.
How do you manufacture an SDPS?
Manufacturing an SDPS (Showa Denko Package Substrate) involves a series of intricate steps and processes aimed at creating a reliable and high-performance substrate for semiconductor devices. Here’s a generalized overview of the manufacturing process:
- Design Phase: The process begins with the design phase, where engineers develop the substrate layout and specifications based on the requirements of the semiconductor device and its intended application. This involves determining the substrate materials, layer stackup, routing, via placement, and other design parameters.
- Material Selection: The appropriate substrate material is selected based on factors such as thermal conductivity, electrical insulation, mechanical strength, and compatibility with manufacturing processes. Common substrate materials include silicon, ceramic, and organic laminate.
- Substrate Preparation: The substrate material is prepared by cutting it into the desired size and shape. Surface preparation techniques such as cleaning and polishing may also be performed to ensure the substrate’s surface is free from contaminants and defects.
- Layer Formation: Multiple layers are formed on the substrate using techniques such as thin-film deposition, photolithography, and etching. These layers include conductive traces, insulating layers, and via structures. Each layer is precisely patterned and etched to create the required circuitry and interconnects.
- Via Formation: Vias are created to establish electrical connections between different layers of the substrate. This typically involves drilling or laser ablation to create holes in the substrate, followed by filling the vias with conductive material such as copper or tungsten.
- Metallization: Conductive traces and interconnects are formed by depositing metal layers (e.g., copper) onto the substrate surface using techniques like physical vapor deposition (PVD) or electroplating. These metal layers provide electrical pathways for connecting semiconductor devices to external circuitry.
- Die Attach and Wire Bonding: Semiconductor chips are attached to the substrate using die attach materials such as epoxy or solder. Wire bonding techniques are then used to establish electrical connections between the semiconductor chip and the substrate’s conductive traces.
- Encapsulation and Sealing: The assembled substrate is encapsulated and sealed using protective materials such as epoxy resin or molding compounds. This helps to protect the semiconductor devices from environmental factors such as moisture, dust, and mechanical stress.
- Surface Finishing: The substrate’s surface is finished to meet specific requirements such as flatness, smoothness, and solderability. This may involve processes like planarization, chemical mechanical polishing (CMP), and surface treatment.
- Quality Control and Testing: The fabricated substrates undergo rigorous quality control and testing to ensure they meet the required specifications for electrical performance, reliability, and durability. This may include electrical continuity testing, thermal cycling tests, and visual inspection.
- Packaging and Delivery: Once the substrates pass inspection, they are packaged and prepared for delivery to semiconductor manufacturers for further assembly into electronic devices.
Throughout the manufacturing process, strict adherence to quality standards, precise control of process parameters, and continuous improvement efforts are essential to ensure the reliability and performance of SDPS substrates. Collaboration between design engineers, manufacturing teams, and semiconductor manufacturers is crucial for achieving success in producing high-quality substrates for semiconductor devices.
How much should an SDPS cost?
The cost of an SDPS (Showa Denko Package Substrate) can vary significantly depending on several factors such as the substrate material, design complexity, size, volume of production, and additional features required.
Typically, SDPS costs are determined by considering various components:
- Material Costs: The cost of the substrate material itself, which can vary depending on the type of material used (e.g., silicon, ceramic, organic laminate) and its quality.
- Manufacturing Costs: Expenses associated with the manufacturing processes involved in fabricating the substrate, including equipment costs, labor costs, overhead costs, and facility expenses.
- Design Complexity: More complex designs with multiple layers, intricate routing, and advanced features may incur higher design and manufacturing costs due to increased material usage and processing time.
- Volume of Production: Economies of scale play a significant role in determining the cost of SDPS. Higher volumes typically result in lower per-unit costs due to spreading fixed costs over a larger number of units.
- Additional Features:Specialized features such as advanced thermal management solutions, high-density interconnects, and customizations can increase the cost of SDPS.
- Quality and Reliability: Ensuring high quality and reliability through rigorous testing and quality control measures may involve additional costs, but it can be crucial for certain applications where reliability is paramount.
Given the complexity and variability involved, it’s challenging to provide a specific cost estimate for an SDPS without detailed information about the specific requirements and specifications. Typically, companies interested in procuring SDPS would need to request a quote from Showa Denko or another manufacturer based on their project’s unique needs.
Overall, while SDPS may represent a significant investment, they are essential components in semiconductor manufacturing, and their cost is often justified by their critical role in ensuring the performance and reliability of electronic devices.
What is SDPS base material?
The base material for SDPS (Showa Denko Package Substrate) can vary depending on the specific requirements of the application and the desired properties of the substrate. Showa Denko offers a range of substrate materials tailored to different applications in the semiconductor industry. Some common base materials used in SDPS include:
- Silicon: Silicon substrates are widely used in semiconductor manufacturing due to their excellent thermal conductivity, mechanical strength, and compatibility with integrated circuit fabrication processes. Silicon substrates can be single-crystal (monocrystalline) or polycrystalline, depending on the application.
- Ceramic: Ceramic substrates, such as alumina (Al2O3) or aluminum nitride (AlN), are valued for their high thermal conductivity, electrical insulation, and mechanical stability. Ceramic substrates are particularly suitable for high-power and high-frequency applications where thermal management is critical.
- Organic Laminate: Organic laminate substrates, also known as printed circuit boards (PCBs), are composed of layers of organic materials such as epoxy resin and fiberglass. These substrates are lightweight, cost-effective, and offer good electrical insulation properties. Organic laminate substrates are commonly used in consumer electronics and low-power applications.
- Composite Materials: Showa Denko also develops composite materials that combine the properties of different base materials to achieve specific performance characteristics. For example, composite substrates may combine the high thermal conductivity of ceramics with the flexibility of organic materials.
The choice of base material depends on factors such as thermal management requirements, electrical performance, mechanical strength, cost considerations, and compatibility with manufacturing processes. Showa Denko leverages its expertise in materials science and semiconductor packaging to develop base materials that meet the demanding requirements of modern semiconductor devices.
Which company makes SDPS? (Note: Our company can produce SDPS)
SDPS (Showa Denko Package Substrate) is manufactured by Showa Denko K.K., a company based in Japan. Showa Denko is a leading global chemical engineering company, specializing in the development and production of various high-performance materials to meet the needs of various industries, including the semiconductor manufacturing industry.
Our company is also capable of producing SDPS because we have advanced process technology and a professional team with the ability and experience to manufacture high-quality and high-reliability SDPS. We are committed to innovation and continuously improving our manufacturing processes to meet the growing demand for SDPS from customers.
As an SDPS manufacturer, we focus on the following aspects:
- Material selection and optimization: We select materials that are most suitable for specific applications, such as high thermal conductivity ceramics or organic substrates, to ensure that SDPS has excellent thermal management performance and electrical properties.
- Advanced processes and equipment: We employ advanced manufacturing processes and equipment, such as thin film deposition, lithography, etching, and metallization, to achieve precise patterning and high-quality SDPS production.
- Strict quality control: We implement strict quality control standards and processes to ensure that each SDPS meets specification requirements and has reliable performance and long-term stability.
- Customized services:We can customize SDPS according to the specific requirements of customers, including design optimization, special material selection, and customized production.
- Continuous improvement and technological innovation: We continuously improve our manufacturing processes and technologies to adapt to changing market demands and technological trends, providing customers with higher quality SDPS products and services.
Through our efforts and professionalism, we believe that we can become a reliable SDPS manufacturer, providing customers with high-quality and high-performance SDPS products to meet their needs and challenges in the semiconductor manufacturing field.
What are the 7 qualities of good customer service?
Good customer service is characterized by several key qualities that contribute to a positive experience for customers. Here are seven qualities:
- Responsiveness: Good customer service involves being prompt and responsive to customer inquiries, requests, and concerns. This means acknowledging customers promptly, addressing their needs in a timely manner, and providing timely updates on the status of their inquiries or issues.
- Empathy: Empathy is the ability to understand and empathize with customers’ feelings, concerns, and perspectives. Good customer service representatives listen actively, show understanding, and demonstrate genuine concern for customers’ needs and experiences.
- Clear Communication: Clear communication is essential for effective customer service. This includes using clear and concise language, actively listening to customers to understand their needs, and providing information in a straightforward manner. Avoiding jargon and technical language can also help ensure that customers understand the information provided.
- Problem-solving Skills: Good customer service representatives have strong problem-solving skills and the ability to resolve customer issues effectively. They are resourceful, proactive, and creative in finding solutions to customers’ problems, even in challenging situations.
- Professionalism: Professionalism involves maintaining a courteous and respectful demeanor when interacting with customers, regardless of the circumstances. This includes being polite, patient, and maintaining a positive attitude, even when dealing with difficult or irate customers.
- Product Knowledge: Good customer service representatives have a thorough understanding of the products or services offered by their company. They can answer questions, provide guidance, and offer relevant recommendations to help customers make informed decisions.
- Follow-up and Follow-through: Good customer service doesn’t end with the resolution of an issue. It also involves following up with customers to ensure their needs have been met and their concerns have been addressed satisfactorily. Following through on commitments, such as promised callbacks or resolutions, demonstrates reliability and builds trust with customers.
By embodying these qualities, businesses can deliver exceptional customer service experiences that foster loyalty, satisfaction, and positive word-of-mouth referrals.
FAQs
What are the key features of SDPS?
SDPS offers features such as high thermal conductivity, electrical insulation, mechanical stability, and reliability, making it suitable for integrating semiconductor devices into electronic systems.
What are the benefits of using SDPS?
Benefits of using SDPS include improved thermal management, enhanced electrical performance, increased reliability, and miniaturization of electronic devices.
What types of materials are used in SDPS?
SDPS can be made from various materials, including silicon, ceramic, organic laminate, and composite materials, depending on the specific requirements of the application.
What industries use SDPS?
SDPS is used in a wide range of industries, including telecommunications, automotive, consumer electronics, aerospace, and industrial applications.
What are the different manufacturing processes involved in producing SDPS?
The manufacturing process for SDPS involves steps such as substrate preparation, layer formation, via formation, metallization, die attach and wire bonding, encapsulation, surface finishing, quality control, and testing.
How can I procure SDPS for my project?
To procure SDPS for your project, you can contact Showa Denko or authorized distributors to discuss your requirements and obtain a quote based on your specific needs.
Are there any customization options available for SDPS?
Yes, Showa Denko and other manufacturers may offer customization options for SDPS to meet the unique requirements of your project, including design optimization, material selection, and special features.