What is Showa Denko Package Substrate?
Showa Denko Package substrate Manufacturer,Rigid-flex package substrates combine the benefits of rigid and flexible PCBs, enabling versatile and reliable electronic assemblies. These substrates feature rigid sections for component mounting and flexible sections for dynamic bending or folding. They offer enhanced space utilization and reduce the need for connectors, minimizing assembly complexity. Rigid-flex substrates ensure excellent signal integrity, thermal management, and mechanical durability, making them ideal for compact and high-reliability applications like medical devices, aerospace systems, and wearables. Their ability to withstand repeated bending and vibration while maintaining electrical performance makes them essential for modern electronic designs requiring flexibility and durability.
Showa Denko Package Substrate (SDPS) emerges as a revolutionary force in the landscape of semiconductor packaging substrates, crafted with precision by Showa Denko Corporation. Positioned as a linchpin within electronic devices, the semiconductor packaging substrate intricately weaves together chips and a spectrum of electronic components, ensuring fluid electrical connectivity, and delivering essential physical support. SDPS technology takes center stage with a mission to amplify the capabilities, reliability, and energy efficiency of semiconductor devices.
SDPS embraces a sophisticated multi-layered structure, seamlessly fusing diverse levels of electrical connections, insulation layers, and heat dissipation layers through meticulously honed manufacturing processes. This avant-garde design significantly trims the profile of the packaging substrate, heightening the density of chip connections, and fine-tuning heat dissipation—a strategic maneuver in response to the prevailing trend of chip downsizing while concurrently advancing overall performance.
Moreover, SDPS capitalizes on advanced materials endowed with stellar electrical properties, tenacious mechanical strength, and superior thermal conductivity. This not only contributes to minimizing power consumption but also propels the velocity of signal transmission, bolstering semiconductor devices for unwavering operation in intricate environmental conditions.
In essence, Showa Denko Package Substrate stands as a vanguard in semiconductor packaging technology. Through its inventive design and material applications, it not only augments the performance and reliability of semiconductor devices but also propels the electronics industry into an era of unparalleled possibilities.
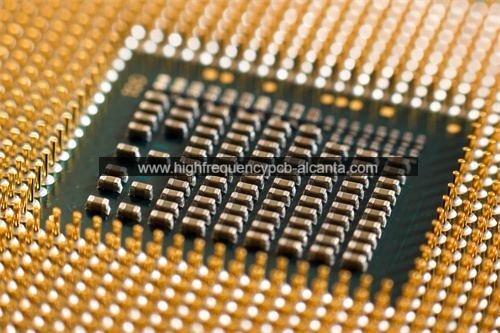
Showa Denko Package substrate Manufacturer
What are the Functions of Showa Denko Package Substrate?
Showa Denko Package Substrate (SDPS) plays a pivotal and versatile role in the intricate world of semiconductor packaging. It serves as the linchpin, orchestrating various functions that collectively enhance the efficiency and reliability of electronic devices. Here’s a breakdown of SDPS’s key functions:
Seamless Electrical Integration: SDPS functions as the silent conductor, seamlessly linking semiconductor chips with diverse electronic components. Its ingeniously crafted multi-layered structure ensures the swift and efficient transmission of signals across different sections of the device.
Stalwart Mechanical Foundation: Beyond its electrical role, SDPS steps into the arena as a robust protector. It provides essential physical support to semiconductor chips, standing guard against potential harm from mechanical stresses such as vibrations or impacts.
Efficient Heat Symphony: SDPS takes on the role of a thermal maestro, conducting the dissipation of heat generated by semiconductor chips during their operational crescendo. Through its sophisticated multi-layered composition, SDPS ensures a harmonious transfer and dissipation of heat, preventing the devices from overheating and ensuring a steady performance.
Architect of Miniaturization: In response to the prevailing trend of shrinking electronic devices, SDPS emerges as an architectural marvel. Its innovative design allows for a reduction in the size of the packaging substrate, contributing to the overall symphony of miniaturization.
Density Composer: SDPS takes center stage in orchestrating a symphony of connections. It enhances the density of electrical connections between semiconductor chips, playing a crucial role in meeting the demands of modern electronics that require intricate connections for advanced functionalities and superior performance.
Material Virtuoso: SDPS doesn’t just conduct; it leverages a repertoire of advanced materials. With superior electrical properties, mechanical strength, and thermal conductivity, these materials become the virtuoso elements that contribute to the overall efficiency and reliability of semiconductor devices.
In essence, Showa Denko Package Substrate isn’t merely a supporting cast member; it’s the orchestrator of a symphony, ensuring the seamless integration, robust stability, and efficient performance of semiconductor devices in tune with the dynamic cadence of the electronics industry.
What are the Different Types of Showa Denko Package Substrate?
Showa Denko Package Substrate (SDPS) caters to a spectrum of needs with its diverse range of configurations, meticulously designed to align with distinct application requirements and technical nuances. Here’s a glimpse into the potential variations of SDPS:
High-Density Interconnect (HDI): Crafted for cutting-edge electronic devices craving compact dimensions and an abundance of connections, HDI-type SDPS achieves a heightened electrical connection density.
Thermal Substrate: Uniquely tailored for applications with specific heat dissipation demands, such as high-performance processors or temperature-sensitive chips, Thermal Substrate SDPS stands out in optimizing heat dissipation.
RF and Microwave Mastery: SDPS designed for RF and microwave applications incorporates specialized designs and materials to ensure peak performance for high-frequency signals.
Rigid-Flex Fusion: For applications demanding flexibility, Rigid-Flex Hybrid SDPS seamlessly blends rigid and flexible characteristics, ideal for devices requiring bending or folding capabilities.
High-Velocity Signal Transmission: To meet the demands of applications craving high-speed data transmission, SDPS is engineered with specialized materials and designs, ensuring efficient low-loss transmission of high-frequency signals.
Tailored Materials and Applications: SDPS unveils customized versions for unique applications, including those thriving in extreme environments or those demanding specific material attributes.
It’s worth noting that the landscape of SDPS types and specifications may undergo evolution over time, responding to the dynamism of technological progress and market trends. For the most up-to-date and accurate insights into SDPS product types and specifications, referring to Showa Denko’s official documentation or engaging with their representatives is highly recommended.
How is Showa Denko Package Substrate Related to IC Packaging?
Showa Denko Package Substrate (SDPS) and IC (Integrated Circuit) packaging engage in a symbiotic dance, each playing a crucial role in the holistic packaging and assembly of integrated circuits. This dynamic relationship unfolds across several essential dimensions:
Electrical Fusion: SDPS steps into the scene as the foundational substrate, orchestrating the mounting and interconnection of individual semiconductor chips within an IC package. It facilitates the harmonious establishment of electrical connections between the chips and other components on the substrate, culminating in the creation of a functional circuit.
Structural Bedrock: Serving as the structural bedrock of IC packaging, SDPS provides indispensable mechanical support to semiconductor chips. It acts as a vigilant guardian, ensuring the secure attachment of chips, shielding them from potential damage due to mechanical stresses, and contributing to the overall stability of the IC package.
Signal Choreography: The intricate and multi-layered composition of SDPS unfolds as a canvas for the choreography of electrical signals. It enables a sophisticated dance of signals between different components on the substrate, ensuring a seamless and orchestrated communication within the integrated circuit.
Heat Symphony: SDPS assumes the role of a conductor in managing and dissipating the heat generated by semiconductor chips during their operational crescendo. Its design is a symphony of effective heat dissipation, preventing overheating and preserving the optimal performance of the integrated circuit.
Size and Density Ballet: SDPS takes center stage in the ongoing ballet of miniaturization within IC packages. Its design gracefully allows for the reduction of the overall footprint of the package while elevating connection density, aligning with the pursuit of smaller yet more potent electronic devices.
Versatile Configurations: SDPS unveils a repertoire of configurations, adapting to the diverse needs of IC packaging. Whether it’s weaving high-density interconnects, crafting thermal substrates for heat-sensitive applications, or flexibly accommodating specific form factors, SDPS emerges as a versatile artist meeting various IC packaging requirements.
In essence, Showa Denko Package Substrate emerges not merely as a component but as a maestro in the symphony of IC packaging, providing the foundational elements for electrical connectivity, mechanical fortification, signal intricacy, heat dissipation, and size optimization in the grand assembly of integrated circuits.
What are the Differences Between Showa Denko Package Substrate and PCB?
Showa Denko Package Substrate (SDPS) and Printed Circuit Board (PCB) stand as pivotal contributors to the electronic landscape, each donning a distinctive role with its own set of attributes. Let’s navigate through the nuanced disparities between SDPS and PCB:
Functional Finesse:
SDPS: Crafted exclusively for the intricacies of semiconductor packaging, SDPS emerges as a specialized maestro. Its primary repertoire includes finely tuned electrical connectivity, unwavering mechanical support, and an artful ballet of heat dissipation within the confines of an integrated circuit (IC) package.
PCB: In a contrasting symphony, the Printed Circuit Board commands a broader stage. It serves as the central hub orchestrating the interplay among an eclectic ensemble of electronic components—ICs, resistors, capacitors, and connectors—conducting a harmonious symphony of functionalities in electronic devices.
Application Versatility:
SDPS: Tailored for the precision dance of IC packages, SDPS finds its sweet spot in addressing the specialized packaging needs of semiconductor devices.
PCB: PCBs, with their versatile choreography, transcend boundaries, finding expression in an array of electronic devices, ranging from the mundane to the sophisticated realms of computers and smartphones.
Layered Intricacies:
SDPS: Unfurling a multi-layered tapestry, SDPS showcases a complexity that, while significant, may not scale the heights ventured by some of the more intricate PCBs.
PCB: The layer count of PCBs, akin to the movements in a dance, varies based on the intricacies of the electronic performance. High-end devices often embrace PCBs with numerous layers, orchestrating an intricate performance of functionalities.
Material Symphony:
SDPS: Sculpted with an acute sensitivity to the demands of semiconductor packaging, SDPS weaves a tale with materials renowned for their prowess in heat dissipation, electrical conductivity, and mechanical fortitude.
PCB: The material repertoire of PCBs, akin to a diverse musical ensemble, encompasses options like fiberglass-reinforced epoxy. The selection is a choreography, considering the thermal dynamics, rigidity, and economic cadence.
Integration Ballet:
SDPS: Entwining its essence with semiconductor chips, SDPS becomes a bespoke stage intricately designed for the nuances of IC packages.
PCB: A master of integration, PCBs host a diverse ensemble of electronic components, extending their influence beyond semiconductors to ensure seamless connectivity and an optimal performance ballet.
In summation, while SDPS takes center stage in the precision dance of semiconductor packaging, PCBs emerge as versatile conductors orchestrating a symphony of electronics, accommodating a diverse range of components in various applications.
What are the Main Structure and Production Technologies of Showa Denko Package Substrate?
Showa Denko’s package substrate intricately weaves together various elements of structure and production technology:
Structure:
Layered Complexity: The substrate unfolds in multiple layers, enabling the intricate dance of electrical connections across different tiers. This design, akin to a technological tapestry, allows the accommodation of sophisticated circuits within confined spaces.
Insulating Ballet: Intervening layers host insulating materials, performing a ballet of their own to ensure a harmonious absence of electrical interference or short circuits.
Conductive Symphony: Dedicated layers harmonize to create electrical connections, with copper foil layers often taking center stage, conducting signals with efficiency.
Production Technique:
Art of Printing: The manufacturing overture involves a choreography of printing techniques, where circuit structures emerge through successive layers of printing. Conductive inks or kindred materials grace the stage during this printing performance.
Chemical Etching Ballet: Circuit patterns pirouette into existence as selective removal of coverings on conductive layers unfolds through a chemical etching ballet.
Layering Pas de Deux: The manufacturing crescendo involves layering different components and subjecting them to a ballet of high temperatures and pressures. This ensures a sturdy and resilient connection between layers.
Specialized Artistry:
Blind and Buried Hole Artistry: Advancements in the performance feature techniques reminiscent of an artistry of blind holes (piercing through select layers) or buried holes (enveloped in a cocoon of layers), enhancing the overall circuit density performance.
Material Alchemy: For high-performance or avant-garde applications, Showa Denko may employ the alchemy of special substrate materials. These materials, akin to the prima donnas of the technological stage, may include high-frequency performers or those with a unique thermal ballet.
In essence, the orchestration of Showa Denko’s package substrate involves a symphony of structure and production techniques, each playing a unique role in the technological performance.
FAQs
What exactly is Showa Denko Package Substrate (SDPS)?
SDPS is a specialized substrate engineered by Showa Denko, designed to serve as the foundation for mounting and connecting semiconductor chips within integrated circuit (IC) packages.
What’s the primary role of SDPS in semiconductor packaging?
SDPS is crafted to offer a dedicated platform for semiconductor chip mounting, ensuring not just electrical connectivity but also delivering essential mechanical support and proficient heat dissipation within the confines of IC packages.
How does SDPS distinguish itself from traditional Printed Circuit Boards (PCBs)?
Unlike PCBs, which have a broader application, SDPS is tailored specifically for the intricate demands of semiconductor packaging. It optimizes electrical, mechanical, and thermal considerations within the compact space of IC packages.
What standout features can be expected from SDPS?
SDPS typically showcases a multi-layered structure, incorporates specialized materials for effective heat dissipation, and is configured to meet the unique requirements of semiconductor devices.
In which types of semiconductor devices is SDPS commonly employed?
SDPS finds application in various semiconductor devices, including microprocessors, memory chips, and other integrated circuits where precision packaging is paramount for performance and reliability.
Are there different variants of SDPS available?
Yes, Showa Denko may offer diverse types of SDPS to cater to a range of semiconductor packaging needs. Variations could encompass differences in materials, configurations, and performance attributes.
What advantages does SDPS bring to semiconductor packaging?
SDPS delivers benefits such as enhanced electrical connectivity, resilient mechanical support for chips, proficient heat dissipation, and the ability to meet the compact design demands of contemporary electronic devices.
Conclusion
In summary, Showa Denko Package Substrate (SDPS) stands as a specialized cornerstone within semiconductor packaging. Its intricate design, featuring multiple layers and specialized materials, caters specifically to the nuanced demands of mounting and interconnecting semiconductor chips within integrated circuits (ICs). Unlike conventional Printed Circuit Boards (PCBs), SDPS is meticulously crafted to optimize electrical connectivity, provide robust mechanical support, and proficiently manage heat dissipation within the confined spatial constraints of IC packages.
The manufacturing process of SDPS involves advanced techniques, including printing, chemical etching, and strategic layering, demonstrating a commitment to technological excellence. Showa Denko offers a range of SDPS types, allowing adaptability to diverse semiconductor packaging needs with variations in materials, configurations, and performance attributes.
SDPS plays a pivotal role in elevating the overall performance and reliability of semiconductor devices. It contributes to the seamless orchestration of electrical connections, ensuring chip stability, and adeptly navigating thermal considerations. As technology continues to evolve, SDPS remains at the forefront, adapting to the dynamic landscape of semiconductor advancements.
For those seeking comprehensive and accurate information about SDPS products and specifications, referring to Showa Denko’s official documentation, product datasheets, or engaging directly with their representatives is recommended. In essence, the integration of SDPS is not merely a technological necessity; it stands as a key facilitator of innovation and efficiency in the intricate realm of electronic devices.