Showa Denko MCL-E-795G Package Substrate Manufacturer
Showa Denko MCL-E-795G Package Substrate Manufacturer,Showa Denko’s MCL-E-795G is an advanced package substrate renowned for its exceptional performance and reliability. Utilizing high-quality materials and cutting-edge manufacturing processes, this substrate provides robust support and connectivity for electronic devices. Its intricate design and compact dimensions suit a variety of packaging needs. The MCL-E-795G boasts excellent thermal conductivity and electrical characteristics, effectively reducing operating temperatures of electronic components, thereby enhancing device performance and stability. Furthermore, the substrate exhibits excellent corrosion resistance and mechanical strength, ensuring stable operation even in harsh evironments. Overall, Showa Denko’s MCL-E-795G stands as a dependable packaging substrate solution applicable across diverse electronic applications, delivering outstanding performance and reliability to customers.
What is a Showa Denko MCL-E-795G package substrate?
The Showa Denko MCL-E-795G package substrate is a type of substrate used in electronic packaging. Specifically, it’s designed for semiconductor devices like integrated circuits (ICs) and microchips. This substrate is crucial because it provides a stable base for mounting and interconnecting various electronic components within a package.
The “MCL-E-795G” designation likely refers to specific material properties or manufacturing specifications set by Showa Denko, a company known for producing advanced materials for electronics. These substrates are typically made from materials like ceramics or specialized composites, chosen for their thermal stability, electrical insulation, and mechanical strength.
The “795G” part may indicate certain characteristics of the substrate, such as its thermal conductivity, coefficient of thermal expansion, or electrical properties. These specifications are crucial for ensuring the reliable performance of the semiconductor devices mounted on the substrate.
Overall, the Showa Denko MCL-E-795G package substrate plays a vital role in modern electronics manufacturing, providing a stable foundation for building high-performance semiconductor packages that meet the stringent demands of today’s electronic devices.
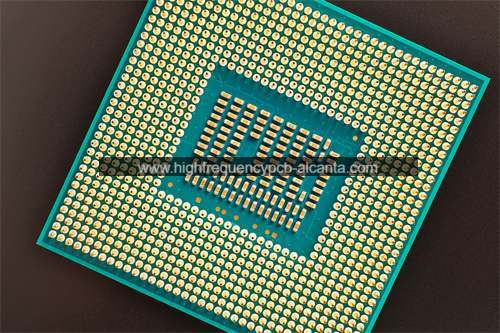
Showa Denko MCL-E-795G Package Substrate Manufacturer
What are the Showa Denko MCL-E-795G package substrate Design Guidelines?
Specific design guidelines for the Showa Denko MCL-E-795G package substrate may vary depending on the application and specific requirements of the semiconductor devices being mounted on it. However, there are some general design principles and considerations that typically apply:
- Dimensional Accuracy: Ensure that the substrate dimensions meet the specifications provided by Showa Denko. This includes the substrate thickness, width, and length, which are critical for compatibility with standard packaging processes.
- Material Compatibility: Verify that the materials used in the substrate construction are compatible with the intended application and environment. This includes considerations for thermal expansion coefficients, electrical insulation properties, and mechanical strength.
- Mounting and Interconnection: Design the substrate to facilitate the mounting and interconnection of semiconductor devices. This involves providing appropriate mounting locations, alignment features, and interconnect patterns to accommodate the specific layout of the devices.
- Thermal Management: Implement thermal management features to dissipate heat generated by the semiconductor devices effectively. This may include incorporating thermal vias, heat spreaders, or other cooling mechanisms to maintain optimal operating temperatures and prevent thermal damage.
- Electrical Performance: Optimize the electrical performance of the substrate by minimizing parasitic capacitance, inductance, and resistance. This may involve careful routing of signal traces, power distribution networks, and grounding structures to ensure signal integrity and minimize electrical losses.
- Reliability Considerations: Design the substrate to meet reliability requirements, such as mechanical shock resistance, thermal cycling durability, and resistance to environmental factors like moisture and chemical exposure. This may involve reinforcing critical areas, selecting robust materials, and implementing appropriate protective coatings.
- Manufacturability: Consider manufacturability aspects during the design phase to ensure that the substrate can be efficiently produced at scale. This includes optimizing the layout for fabrication processes such as photolithography, etching, and metallization, as well as minimizing waste and reducing production costs.
- Compliance and Standards: Ensure that the design complies with relevant industry standards and regulations governing semiconductor packaging, such as JEDEC standards or customer-specific requirements.
By adhering to these design guidelines and principles, engineers can develop reliable and high-performance electronic packages using Showa Denko MCL-E-795G package substrates. Additionally, collaboration with Showa Denko or other materials suppliers may provide valuable insights and support in optimizing substrate designs for specific applications.
What is the Showa Denko MCL-E-795G package substrate Fabrication Process?
The fabrication process for Showa Denko MCL-E-795G package substrates typically involves several steps to create the final substrate structure with desired material properties and dimensions. While specific details may vary depending on the substrate’s design and application, the following is a general overview of the fabrication process:
- Material Selection: The fabrication process begins with the selection of appropriate materials for the substrate. Showa Denko MCL-E-795G substrates are typically composed of advanced materials such as ceramics or specialized composites chosen for their thermal, electrical, and mechanical properties.
- Substrate Preparation: The selected materials are prepared for processing, which may involve cutting or machining them into the desired shape and dimensions. This step ensures that the substrate blanks are ready for subsequent manufacturing processes.
- Layer Deposition:Depending on the substrate’s design, various layers of materials may be deposited onto the substrate blanks. This can include the deposition of conductive or insulating layers using techniques such as physical vapor deposition (PVD), chemical vapor deposition (CVD), or screen printing.
- Pattern Formation: Next, patterns are formed on the substrate surface to define features such as conductive traces, vias, and bonding pads. This step typically involves photolithography, where a photoresist material is applied to the substrate surface, exposed to UV light through a mask, and developed to create the desired pattern.
- Etching: The exposed areas of the substrate are then selectively etched away to remove unwanted material and define the desired features. Wet or dry etching techniques may be used depending on the substrate material and the complexity of the pattern.
- Metallization: Metal layers are deposited onto the substrate surface to create conductive pathways for electrical connections between semiconductor devices. This can involve techniques such as sputtering or electroplating to deposit thin layers of metals such as copper, aluminum, or gold.
- Surface Finishing:After metallization, surface finishing processes may be applied to the substrate to improve its performance and reliability. This can include processes such as chemical mechanical polishing (CMP) to planarize the substrate surface and improve its flatness.
- Quality Control: Throughout the fabrication process, rigorous quality control measures are implemented to ensure that the substrates meet the required specifications and standards for dimensional accuracy, material properties, and reliability.
- Packaging and Testing: Once fabricated, the substrates are packaged and tested to verify their performance and suitability for the intended application. This may involve mounting semiconductor devices onto the substrates, wire bonding or soldering connections, and conducting electrical and thermal testing to assess their functionality.
By following these fabrication steps and quality control measures, Showa Denko produces MCL-E-795G package substrates with the necessary properties and performance characteristics for use in a wide range of electronic applications.
How do you manufacture a Showa Denko MCL-E-795G package substrate?
Manufacturing a Showa Denko MCL-E-795G package substrate involves a series of sophisticated processes to create a high-quality substrate with precise dimensions, material properties, and performance characteristics. Here’s an overview of the manufacturing process:
- Material Selection:Showa Denko selects advanced materials such as ceramics or specialized composites with specific thermal, electrical, and mechanical properties suitable for the MCL-E-795G substrate.
- Preparation of Substrate Blanks: The selected materials are prepared for processing by cutting or machining them into the desired shape and dimensions. This step ensures that the substrate blanks are ready for subsequent manufacturing processes.
- Layer Deposition: Depending on the substrate design, various layers of materials may be deposited onto the substrate blanks. This can include conductive or insulating layers applied using techniques such as physical vapor deposition (PVD), chemical vapor deposition (CVD), or screen printing.
- Pattern Formation: Patterns are formed on the substrate surface to define features such as conductive traces, vias, and bonding pads. Photolithography is typically used, where a photoresist material is applied to the substrate surface, exposed to UV light through a mask, and developed to create the desired pattern.
- Etching: The exposed areas of the substrate are selectively etched away to remove unwanted material and define the desired features. Wet or dry etching techniques may be used depending on the substrate material and the complexity of the pattern.
- Metallization: Metal layers are deposited onto the substrate surface to create conductive pathways for electrical connections between semiconductor devices. Techniques such as sputtering or electroplating deposit thin layers of metals like copper, aluminum, or gold.
- Surface Finishing: After metallization, surface finishing processes are applied to the substrate to improve its performance and reliability. Chemical mechanical polishing (CMP) may be used to planarize the substrate surface and enhance its flatness.
- Quality Control: Rigorous quality control measures are implemented throughout the manufacturing process to ensure that the substrates meet the required specifications and standards for dimensional accuracy, material properties, and reliability.
- Packaging and Testing: Once fabricated, the substrates are packaged and tested to verify their performance and suitability for the intended application. This involves mounting semiconductor devices onto the substrates, wire bonding or soldering connections, and conducting electrical and thermal testing.
By following these manufacturing steps and maintaining strict quality control standards, Showa Denko produces MCL-E-795G package substrates with the necessary properties and performance characteristics for use in a wide range of electronic applications.
How much should a Showa Denko MCL-E-795G package substrate cost?
The cost of a Showa Denko MCL-E-795G package substrate can vary depending on several factors, including:
- Material Costs: The cost of the raw materials used in manufacturing the substrate, such as ceramics or specialized composites, can significantly impact the overall cost.
- Manufacturing Complexity: The complexity of the manufacturing process, including the number of fabrication steps, level of precision required, and sophistication of equipment used, can influence the cost.
- Production Volume: Economies of scale apply in manufacturing, meaning that higher production volumes often lead to lower per-unit costs. Larger orders typically result in lower costs per substrate.
- Customization Requirements: If the substrate requires customization or special features tailored to a specific application, such as unique patterns, materials, or dimensions, this may increase the cost.
- Quality and Performance Specifications: Substrates designed to meet stringent quality and performance standards may require additional testing, inspection, and quality control measures, which can contribute to higher costs.
- Market Demand and Competition: Market dynamics, including supply and demand fluctuations, competition among substrate manufacturers, and industry trends, can influence pricing.
Given these variables, it’s challenging to provide a specific cost for a Showa Denko MCL-E-795G package substrate without more detailed information about the specific requirements and order quantity. Typically, customers would need to contact Showa Denko directly for pricing inquiries based on their individual needs and specifications.
What is a Showa Denko MCL-E-795G package substrate base material?
The base material of the Showa Denko MCL-E-795G package substrate is typically composed of advanced materials chosen for their specific properties suitable for electronic packaging applications. While the exact composition may not be publicly disclosed due to proprietary reasons, Showa Denko is known for utilizing materials such as ceramics or specialized composites for their package substrates.
Ceramic materials offer advantages such as high thermal conductivity, excellent electrical insulation properties, and mechanical stability, making them well-suited for use in electronic packaging where heat dissipation and electrical isolation are critical. Specialized composites may also be employed to achieve specific performance requirements such as tailored thermal expansion coefficients or enhanced mechanical strength.
Overall, the base material of the Showa Denko MCL-E-795G package substrate is carefully selected to meet the stringent demands of modern electronic devices, providing a reliable foundation for mounting and interconnecting semiconductor devices while ensuring optimal performance and reliability.
Which company manufactures Showa Denko MCL-E-795G package substrates?
Currently, Showa Denko is one of the main manufacturers of MCL-E-795G package substrates. In addition to Showa Denko, there may be other companies producing similar products in specific markets or fields. These companies could be electronic materials manufacturers, semiconductor packaging companies, or enterprises focusing on specific packaging technologies.
Our company can also manufacture similar products. As a company specializing in electronic materials and packaging solutions, we have advanced production equipment and technologies and work closely with supply chain partners to ensure product quality and performance. Our production process includes:
- Material Selection and Procurement: We collaborate with high-quality material suppliers to select ceramic materials or specialized composite materials with excellent performance as the raw materials for substrates.
- Substrate Preparation:We use advanced processing equipment to precisely cut and process the raw materials to produce substrates that meet specifications.
- Layer Deposition: According to design requirements, we deposit different material layers onto the substrate to form the necessary structures and characteristics.
- Pattern Formation: We employ precise lithography processes to form the required patterns and structures on the substrate surface to define conductive paths and other functions.
- Metallization: Through metal deposition processes, we cover the substrate surface with conductive metal layers to establish electrical connections and conductive paths.
- Surface Treatment: We treat the surface of the metallized substrate to improve its flatness and surface quality, ensuring good bonding performance.
- Quality Control: We implement strict quality control measures, including inspections and testing throughout the production process, to ensure that products meet specifications and standards.
- Customization Services: We can provide customized solutions according to customer requirements, including specific design requirements, material selection, and production processes, to meet the needs of different application scenarios.
Through the above production process and quality management measures, we can produce high-quality, stable-performance package substrates of the MCL-E-795G type, providing reliable electronic packaging solutions for customers.
What are the 7 qualities of good customer service?
Good customer service is characterized by several key qualities that help build positive relationships with customers and enhance their overall experience. Here are seven qualities of good customer service:
- Empathy: Empathy involves understanding and acknowledging the customer’s feelings, concerns, and needs. Customer service representatives who demonstrate empathy can connect with customers on a personal level, showing genuine care and concern for their well-being.
- Responsiveness: Responsiveness refers to the promptness and efficiency with which customer inquiries, requests, and issues are addressed. Customers appreciate timely responses and solutions to their problems, which helps build trust and satisfaction.
- Professionalism: Professionalism involves maintaining a courteous, respectful, and professional demeanor when interacting with customers. This includes using appropriate language, tone of voice, and behavior, regardless of the situation or the customer’s demeanor.
- Knowledgeability: Knowledgeability refers to having a deep understanding of the company’s products, services, policies, and procedures. Customer service representatives who are knowledgeable can provide accurate information, answer questions, and offer helpful guidance to customers.
- Adaptability: Adaptability is the ability to adjust and tailor the customer service approach to meet the unique needs and preferences of each customer. This may involve adapting communication styles, problem-solving techniques, or service delivery methods based on the situation and the customer’s preferences.
- Consistency: Consistency involves delivering a consistent level of service quality across all customer interactions and touchpoints. Customers expect consistency in terms of service standards, policies, and communication regardless of when or how they interact with the company.
- Proactiveness: Proactiveness involves anticipating and addressing customer needs and issues before they arise. Customer service representatives who are proactive can identify potential problems, offer proactive assistance, and provide recommendations to enhance the customer experience.
By embodying these qualities, businesses can provide exceptional customer service that fosters loyalty, satisfaction, and positive word-of-mouth recommendations.
FAQs
What is Showa Denko MCL-E-795G package substrate?
Showa Denko MCL-E-795G package substrate is a type of substrate used in electronic packaging, particularly for semiconductor devices like integrated circuits (ICs) and microchips. It provides a stable base for mounting and interconnecting electronic components within a package.
What are the key features of MCL-E-795G package substrates?
MCL-E-795G package substrates typically offer high thermal conductivity, excellent electrical insulation properties, and mechanical stability. These substrates are designed to meet the stringent demands of modern electronic devices, providing reliable performance and durability.
What materials are used in MCL-E-795G package substrates?
The exact composition of MCL-E-795G package substrates may vary, but they are typically composed of advanced materials such as ceramics or specialized composites chosen for their thermal, electrical, and mechanical properties.
What are the applications of MCL-E-795G package substrates?
MCL-E-795G package substrates are used in various electronic applications where high-performance semiconductor packaging is required. These include consumer electronics, automotive electronics, telecommunications, industrial equipment, and more.
What are the benefits of using MCL-E-795G package substrates?
The benefits of using MCL-E-795G package substrates include improved thermal management, enhanced electrical performance, increased reliability, and compatibility with advanced packaging technologies.
Are MCL-E-795G package substrates customizable?
Yes, MCL-E-795G package substrates can be customized to meet specific design requirements and performance specifications. Showa Denko and other manufacturers may offer customization services to tailor substrates for specific applications.
Where can I purchase MCL-E-795G package substrates?
MCL-E-795G package substrates are typically available through authorized distributors or directly from Showa Denko. Customers can contact Showa Denko or their local distributors for purchasing inquiries and technical support.