SShowa Denko MCL-E-770G Package Substrate Manufacturer
Showa Denko MCL-E-770G Package Substrate Manufacturer,Showa Denko MCL-E-770G package substrates are advanced components designed to meet the demanding requirements of modern semiconductor packaging. Featuring a blend of cutting-edge materials and precision engineering, these substrates offer exceptional thermal performance, high density, and reliability crucial for various electronic applications. MCL-E-770G substrates are meticulously crafted to provide a stable platform for mounting semiconductor chips, ensuring efficient heat dissipation and optimal electrical connectivity. With a focus on quality and innovation, Showa Denko has developed the MCL-E-770G to empower industries such as telecommunications, automotive, consumer electronics, and industrial electronics with solutions that enable the next generation of electronic devices. Whether it’s powering high-performance computing systems or enabling connectivity in smart devices, Showa Denko MCL-E-770G package substrates deliver the performance and reliability required to drive innovation forward.
What is the Showa Denko MCL-E-770G package substrate?
The Showa Denko MCL-E-770G is a type of package substrate manufactured by Showa Denko K.K., a Japanese chemical company. Package substrates are essential components in semiconductor packaging, providing a platform for mounting and connecting semiconductor chips within electronic devices.
The MCL-E-770G substrate is likely designed to meet specific requirements such as high density, thermal performance, and reliability for advanced semiconductor packaging applications. However, specific details about its features, dimensions, and materials would typically be provided in technical specifications or datasheets provided by the manufacturer.
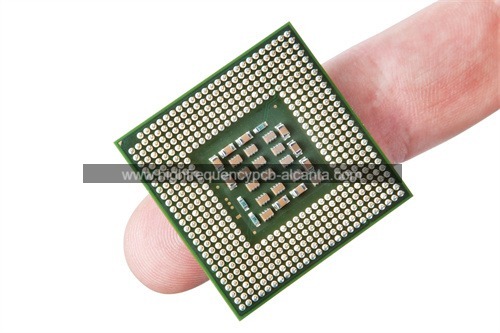
Showa Denko MCL-E-770G Package Substrate Manufacturer
What are the Showa Denko MCL-E-770G package substrate Design Guidelines?
While detailed design guidelines for the Showa Denko MCL-E-770G package substrate may not be readily available in the public domain, I can provide some general considerations and best practices that are typically relevant when designing with package substrates:
- Dimensional Requirements: Ensure that the substrate dimensions align with the specifications of the semiconductor chip or component that will be mounted on it. This includes considerations for the substrate’s length, width, thickness, and any specific placement requirements for mounting holes or other features.
- Material Selection: Understand the material properties of the MCL-E-770G substrate, including its thermal conductivity, coefficient of thermal expansion (CTE), electrical properties, and mechanical strength. Select materials compatible with the substrate that will ensure proper performance and reliability in the intended application.
- Routing and Layout: Plan the routing of electrical traces and vias on the substrate to optimize signal integrity, minimize signal interference, and ensure proper power distribution. Follow industry-standard design practices for signal integrity, such as controlled impedance routing for high-speed signals.
- Thermal Management: Consider thermal management strategies to dissipate heat generated by the semiconductor devices mounted on the substrate. This may involve incorporating thermal vias, thermal pads, or heat sinks into the substrate design to enhance heat dissipation and prevent overheating of the components.
- Assembly and Mounting: Design the substrate with features that facilitate the assembly process, such as fiducial marks for alignment during component placement, solder mask openings for soldering pads, and appropriate clearance and tolerances for component mounting.
- Reliability and Durability: Ensure that the substrate design meets reliability and durability requirements for the intended application, including considerations for mechanical stress, thermal cycling, vibration, and environmental factors such as humidity and temperature variations.
- Electrical Performance: Perform thorough electrical simulations and testing to verify the electrical performance of the substrate design, including signal integrity, power delivery, and impedance matching.
- Compliance and Standards: Ensure that the substrate design complies with relevant industry standards and regulations, such as IPC (Association Connecting Electronics Industries) standards for PCB design and assembly, as well as any specific requirements or certifications applicable to the target market or application.
By following these design guidelines and best practices, designers can develop robust and reliable electronic systems using the Showa Denko MCL-E-770G package substrate or similar substrates. Additionally, consulting with the substrate manufacturer and leveraging their expertise can provide valuable insights and recommendations for optimizing the substrate design for specific applications.
What is the Showa Denko MCL-E-770G package substrate Fabrication Process?
The specific fabrication process for the Showa Denko MCL-E-770G package substrate may not be publicly disclosed by the manufacturer, as it likely involves proprietary techniques and technologies. However, I can outline a general fabrication process for package substrates, which may include some common steps:
- Substrate Preparation: The process begins with the preparation of the substrate material, which may involve cleaning and surface treatment to ensure proper adhesion of subsequent layers.
- Layer Deposition: Multiple layers of materials are deposited onto the substrate using techniques such as chemical vapor deposition (CVD), physical vapor deposition (PVD), or electrochemical deposition. These layers may include dielectric materials, conductive traces, and metal plating for electrical connections.
- Lithography:Photolithography techniques are used to define the patterns of conductive traces and features on the substrate. A photoresist material is applied to the substrate, exposed to light through a mask, and developed to selectively remove areas of the deposited material, leaving behind the desired patterns.
- Etching: The exposed areas of the substrate are etched away using wet or dry etching processes, leaving behind the patterned conductive traces and features.
- Surface Finishing: Surface finishing processes such as chemical mechanical polishing (CMP) or electroplating may be used to smoothen the substrate surface and improve the conductivity of the metal traces.
- Through-Hole Drilling: Holes are drilled through the substrate to create vias for electrical connections between different layers of the substrate. These vias may be filled with conductive materials to ensure electrical continuity.
- Curing and Annealing: The substrate may undergo curing or annealing processes to enhance the mechanical and electrical properties of the deposited materials and ensure proper adhesion between layers.
- Testing and Inspection: The fabricated substrate undergoes rigorous testing and inspection to verify its electrical performance, dimensional accuracy, and reliability. This may include electrical continuity tests, impedance measurements, and visual inspection for defects.
- Surface Mounting: Finally, semiconductor chips and other electronic components are mounted onto the substrate using soldering or flip-chip bonding techniques, and the entire assembly may undergo additional testing to ensure proper functionality.
It’s important to note that the actual fabrication process for the Showa Denko MCL-E-770G package substrate may involve additional steps or variations specific to its design and materials. Additionally, the manufacturer may employ proprietary technologies or processes to optimize the performance and reliability of the substrate for its intended applications.
How do you manufacture a Showa Denko MCL-E-770G package substrate?
The Showa Denko MCL-E-770G package substrate is a specific product manufactured by Showa Denko K.K. While I don’t have access to proprietary information about the manufacturing process for this particular substrate, I can provide a general outline of how package substrates are typically manufactured, which might give you some insights into the process:
- Design: The substrate design is created based on the specific requirements of the application, including the size, number of layers, placement of components, and electrical connections.
- Substrate Material Selection: The substrate material is chosen based on factors such as thermal conductivity, electrical properties, and cost. Common materials include FR-4, ceramics, and specialized materials for high-frequency applications.
- Lamination: Layers of substrate material are laminated together using adhesive. This creates a multi-layered board with conductive traces and insulating layers.
- Drilling: Holes are drilled into the substrate for component mounting and interconnection. High precision drilling equipment is used to ensure accuracy.
- Copper Deposition: A thin layer of copper is deposited onto the surface of the substrate through processes like electroplating or sputtering. This copper layer forms the conductive traces that connect the components.
- Etching: The unwanted copper is then removed from the substrate using a chemical etching process, leaving behind the desired copper traces.
- Surface Finish: A surface finish is applied to protect the copper traces and provide a solderable surface for component attachment. Common surface finishes include HASL (Hot Air Solder Leveling), ENIG (Electroless Nickel Immersion Gold), and OSP (Organic Solderability Preservatives).
- Solder Mask Application: A solder mask is applied over the substrate, leaving openings for the solder pads and vias. This solder mask helps prevent solder bridges and protects the copper traces from environmental damage.
- Silkscreen Printing: Component labels, reference indicators, and other markings are added to the substrate using silkscreen printing.
- Testing: Various electrical tests are conducted to ensure the substrate meets quality standards and specifications.
- Routing: The individual substrates are routed or scored to separate them from each other, creating the final package substrate units.
- Final Inspection: A final inspection is performed to check for any defects or irregularities before packaging and shipment.
For specific details on manufacturing the Showa Denko MCL-E-770G package substrate, you would need to consult Showa Denko K.K. or refer to their documentation if available.
How much should a Showa Denko MCL-E-770G package substrate cost?
The cost of a Showa Denko MCL-E-770G package substrate can vary based on several factors, including the substrate’s size, complexity, material composition, manufacturing volume, and market conditions. Additionally, pricing information for specific products like the MCL-E-770G may not be readily available to the public without contacting Showa Denko directly or through authorized distributors.
Typically, package substrates are priced per unit or per square inch/square centimeter, and the cost may decrease with larger order volumes due to economies of scale. However, substrates with specialized features or materials may command higher prices.
For accurate pricing information, it’s recommended to reach out to Showa Denko or their authorized distributors to inquire about the cost of the MCL-E-770G package substrate based on your specific requirements and order quantities.
What is the Showa Denko MCL-E-770G package substrate base material?
The specific base material used for the Showa Denko MCL-E-770G package substrate may not be publicly disclosed by the manufacturer. However, package substrates typically utilize materials with specific properties to meet the demands of the intended application. Here are some common base materials used in package substrate fabrication:
- Organic Substrates: Organic substrates are commonly used in package substrate manufacturing. They are typically made from materials such as epoxy resin, polyimide, or BT (bismaleimide triazine). Organic substrates offer advantages such as low cost, lightweight, and ease of processing. However, they may have limitations in terms of thermal conductivity and dimensional stability compared to other materials.
- Ceramic Substrates: Ceramic substrates, often composed of alumina (Al2O3) or aluminum nitride (AlN), are preferred for high-power applications requiring excellent thermal conductivity and stability. Ceramic substrates have superior heat dissipation properties compared to organic substrates, making them suitable for power electronics and high-frequency applications. However, ceramic substrates are more expensive and brittle than organic substrates.
- Metal Substrates: Metal substrates, such as aluminum or copper, offer exceptional thermal conductivity and mechanical strength. Metal substrates are commonly used in LED packaging and high-power applications where efficient heat dissipation is critical. They can be manufactured using techniques such as direct bond copper (DBC) or metal core printed circuit board (MCPCB) technology.
- Composite Substrates: Composite substrates combine different materials to leverage their complementary properties. For example, a composite substrate may consist of a ceramic core with metal or organic layers for improved thermal performance and manufacturability.
The choice of base material for the Showa Denko MCL-E-770G package substrate would depend on factors such as thermal management requirements, electrical properties, dimensional stability, and cost considerations. Showa Denko may utilize proprietary formulations or combinations of materials to optimize the performance of the MCL-E-770G substrate for its intended applications. For detailed information about the base material used in the MCL-E-770G substrate, it would be best to contact Showa Denko directly or refer to their technical documentation.
Which company manufactures Showa Denko MCL-E-770G package substrates?
Showa Denko MCL-E-770G package substrates are manufactured by Showa Denko Corporation. As our company, we also have the capability to produce similar package substrates to meet the needs of our customers.
We have advanced manufacturing facilities and a skilled technical team dedicated to the research and production of high-quality package substrate products. Our manufacturing process is carefully designed to ensure that our products meet the specifications of our customers and achieve optimal levels of performance, reliability, and cost-effectiveness.
Our manufacturing capabilities include, but are not limited to, the following:
- Material Selection and Preparation: We are able to select and prepare various materials, including organic substrates, ceramic substrates, and metal substrates, to meet the requirements of different applications.
- Lamination and Deposition: We have advanced lamination and deposition equipment to deposit multiple layers of materials on substrates, ensuring good adhesion and uniformity.
- Photolithography and Etching: We use advanced photolithography and etching techniques to define patterns and structures on substrates, achieving high-precision circuit designs.
- Drilling and Via Filling: We can accurately drill holes on substrates and fill them with conductive materials for interlayer connections as needed.
- Surface Treatment and Coating: Our surface treatment and coating technologies ensure the smoothness, electrical performance, and durability of substrate surfaces.
- Testing and Quality Control: We have comprehensive testing equipment and quality control processes to conduct thorough testing and verification of produced package substrates, ensuring that our products meet customer requirements and standards.
Through our manufacturing capabilities and professional team, we can provide customized package substrate solutions to meet the needs of various application fields, including communications, consumer electronics, automotive electronics, industrial control, and more. We are committed to providing our customers with high-quality, high-performance products, and excellent services, working together to achieve business success.
What are the qualities of good customer service?
Good customer service encompasses a range of qualities and practices that aim to meet and exceed customer expectations while building positive relationships. Here are some key qualities of good customer service:
- Responsive: Good customer service involves promptly addressing customer inquiries, concerns, and requests. Being responsive shows that you value the customer’s time and are committed to assisting them in a timely manner.
- Empathetic: Empathy is essential in understanding and empathizing with the customer’s feelings and perspectives. Showing empathy helps to build trust and rapport with customers and can turn a negative experience into a positive one.
- Knowledgeable: Customer service representatives should have a good understanding of the products or services offered by the company. Being knowledgeable allows them to provide accurate information, answer questions, and offer helpful solutions to customer issues.
- Effective Communication:Clear and effective communication is crucial in customer service interactions. This includes listening actively to customers, expressing ideas and information clearly, and adapting communication styles to meet the needs of different customers.
- Problem-Solving Skills: Good customer service involves the ability to identify and resolve customer problems or issues effectively. Customer service representatives should be resourceful, creative, and proactive in finding solutions that meet the customer’s needs.
- Professionalism: Customer service interactions should be conducted with professionalism and courtesy at all times. This includes maintaining a positive attitude, staying calm under pressure, and treating all customers with respect and dignity.
- Consistency:Consistency in service delivery helps to build trust and reliability with customers. Providing consistent experiences across all touchpoints reinforces the company’s brand and enhances customer loyalty.
- Personalization: Tailoring the customer experience to meet individual needs and preferences can make customers feel valued and appreciated. Personalization can involve remembering customer preferences, acknowledging their past interactions, and offering personalized recommendations or solutions.
- Follow-Up: Following up with customers after resolving their issues or completing a transaction shows that you care about their satisfaction and are committed to their ongoing support. Follow-up communication can include thank-you messages, feedback requests, or updates on their inquiries or orders.
- Continuous Improvement:Good customer service is not static but evolves over time through continuous improvement and feedback. Companies should actively seek feedback from customers, analyze trends and patterns, and make adjustments to their customer service strategies and processes accordingly.
By embodying these qualities and practices, companies can deliver exceptional customer service experiences that foster loyalty, satisfaction, and long-term success.
FAQs
What is Showa Denko MCL-E-770G package substrate?
Showa Denko MCL-E-770G is a type of package substrate manufactured by Showa Denko K.K. It is designed to provide a platform for mounting and connecting semiconductor chips within electronic devices.
What are the key features of MCL-E-770G package substrate?
The specific features of MCL-E-770G may vary, but typical features include high density, thermal performance, reliability, and compatibility with advanced semiconductor packaging technologies.
What materials are used in MCL-E-770G package substrate?
The exact materials used in MCL-E-770G substrate may not be publicly disclosed, but package substrates commonly utilize materials such as organic laminates, ceramics, or metal cores to meet specific performance requirements.
What applications are suitable for MCL-E-770G package substrate?
MCL-E-770G package substrates are suitable for a wide range of applications in industries such as telecommunications, automotive, consumer electronics, and industrial electronics, where high-density packaging and thermal management are critical.
What are the available sizes and configurations of MCL-E-770G substrate?
The available sizes and configurations of MCL-E-770G substrate may vary depending on customer requirements and manufacturing capabilities. Showa Denko or authorized distributors can provide information on available options.
What are the thermal properties of MCL-E-770G substrate?
MCL-E-770G substrate is designed to have excellent thermal conductivity properties to efficiently dissipate heat generated by semiconductor devices mounted on it. Specific thermal performance data may be available from Showa Denko or through technical documentation.
Is MCL-E-770G package substrate compatible with lead-free soldering processes?
MCL-E-770G package substrates are typically designed to be compatible with lead-free soldering processes to comply with environmental regulations and industry standards.
What reliability testing has been performed on MCL-E-770G substrate?
Showa Denko may conduct various reliability tests on MCL-E-770G substrates to ensure their performance under different environmental conditions, including thermal cycling, mechanical stress, and electrical reliability testing.