Showa Denko MCL-E-705G Package Substrate Manufacturer
Showa Denko MCL-E-705G Package Substrate Manufacturer,The Showa Denko MCL-E-705G package substrate stands as a pinnacle of innovation in the realm of semiconductor packaging. Crafted with precision and expertise by Showa Denko, a renowned Japanese chemical company, this substrate represents a fusion of advanced materials and cutting-edge technology. Engineered to deliver exceptional performance, the MCL-E-705G substrate boasts superior thermal conductivity, ensuring efficient heat dissipation in electronic devices. Its low electrical resistance and high mechanical strength make it ideal for a wide range of applications, from CPUs to GPUs and beyond. With meticulous attention to detail and uncompromising quality standards, Showa Denko has created a substrate that not only meets but exceeds the demanding requirements of modern electronic systems. The MCL-E-705G package substrate is not just a component; it’s a testament to Showa Denko’s commitment to excellence and innovation in the semiconductor industry.
What is a Showa Denko MCL-E-705G package substrate?
The Showa Denko MCL-E-705G package substrate refers to a type of material used in the packaging of semiconductor devices. Package substrates provide the necessary physical and electrical interface between the chip and the circuit board on which it is mounted.
Specifically, “Showa Denko” is a Japanese chemical company that produces a variety of materials, including those used in the semiconductor industry. The designation “MCL-E-705G” is a product name or specification for one of their package substrates. This particular substrate likely has specific properties designed for enhanced performance in electronic applications, such as high thermal conductivity, low electrical resistance, or special mechanical characteristics to suit different types of semiconductor devices.
The exact details like the material composition (which could be ceramic, organic, or a composite), layer structure, and intended application (such as for CPUs, GPUs, or other microelectronic devices) would be specified in detailed product sheets or technical documentation from Showa Denko. These substrates play a crucial role in ensuring the durability, performance, and reliability of semiconductor components.
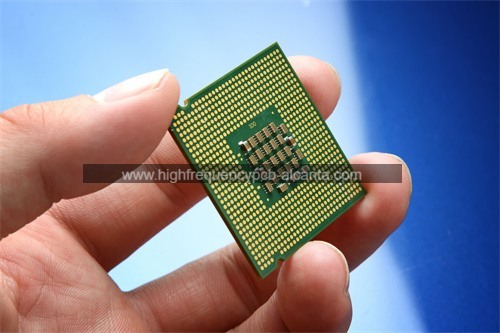
Showa Denko MCL-E-705G Package Substrate Manufacturer
What are the Showa Denko MCL-E-705G package substrate design guidelines?
Specific design guidelines for the Showa Denko MCL-E-705G package substrate may not be publicly available without accessing proprietary documentation or contacting Showa Denko directly. However, I can provide some general design considerations that are typically applicable to package substrates in the semiconductor industry:
- Thermal Management: Efficient heat dissipation is crucial for semiconductor devices to maintain optimal performance and reliability. Designing the substrate with features such as thermal vias, metal layers for heat spreading, and thermally conductive materials can help manage heat effectively.
- Electrical Performance: The substrate must provide low electrical resistance and impedance to ensure proper signal transmission and power distribution. Designing the substrate with controlled impedance traces, signal vias, and ground planes can help achieve desired electrical performance.
- Mechanical Integrity: The substrate must be mechanically robust to withstand handling during assembly and operation. Considerations such as material selection, thickness, and reinforcement structures (such as stiffeners or underfills) can enhance mechanical integrity.
- Signal Integrity: Maintaining signal integrity is essential for high-speed digital and analog circuits. Minimizing signal distortion, crosstalk, and electromagnetic interference (EMI) through careful layout, impedance matching, and shielding techniques is important.
- Reliability: The substrate design should consider long-term reliability factors such as thermal cycling, moisture resistance, solder joint reliability, and mechanical stress. Compliance with industry standards and qualification testing can help ensure reliability.
- Manufacturability: Designing for manufacturability involves considerations such as panelization, material compatibility, fabrication process compatibility, and cost-effectiveness. Collaboration with substrate manufacturers during the design phase can help optimize manufacturability.
These guidelines provide a broad overview of factors to consider when designing package substrates for semiconductor devices. However, for specific design guidelines for the Showa Denko MCL-E-705G substrate, consulting with the manufacturer or accessing their proprietary documentation would be necessary.
What is the Showa Denko MCL-E-705G package substrate fabrication process?
The specific fabrication process for the Showa Denko MCL-E-705G package substrate may not be publicly disclosed without accessing proprietary documentation or information from Showa Denko directly. However, I can provide a general overview of the typical fabrication process for package substrates in the semiconductor industry:
- Substrate Material Selection: The fabrication process begins with the selection of suitable substrate materials, which could include various types of ceramics, organic laminates, or composite materials. The choice of material depends on factors such as thermal conductivity, electrical properties, mechanical strength, and cost.
- Substrate Preparation: The selected substrate material is prepared for processing by cleaning and smoothing the surface to remove any contaminants and ensure uniformity.
- Layer Formation: The substrate undergoes a series of processes to create the required layers. This may include deposition techniques such as sputtering, chemical vapor deposition (CVD), or electroplating to form metal layers, dielectric layers, and other functional layers.
- Pattern Formation: Photolithography or other patterning techniques are used to define the circuitry and features on the substrate. A photoresist material is applied, exposed to UV light through a photomask, and developed to create patterns for metal traces, vias, and other elements.
- Etching: Chemical or plasma etching is used to remove the unwanted material from the substrate, leaving behind the patterned features defined by the photoresist. This process selectively removes material to create the desired circuitry and interconnects.
- Surface Finishing: Surface finishing processes such as metallization, solder mask application, and surface coating are applied to enhance electrical conductivity, protect against corrosion, and provide solderability for component attachment.
- Quality Control and Testing: Throughout the fabrication process, quality control measures are implemented to ensure the substrate meets the required specifications and standards. Various testing methods, including electrical testing, visual inspection, and mechanical testing, are performed to validate the quality and reliability of the finished substrate.
- Packaging and Shipping: Once fabrication is complete and the substrates pass quality assurance tests, they are packaged and prepared for shipment to semiconductor device manufacturers for further assembly and integration into electronic products.
This overview provides a general understanding of the fabrication process for package substrates in the semiconductor industry. For specific details regarding the fabrication process for the Showa Denko MCL-E-705G substrate, consulting proprietary documentation or contacting Showa Denko directly would be necessary.
How do you manufacture a Showa Denko MCL-E-705G package substrate?
Specific details about the manufacturing process for the Showa Denko MCL-E-705G package substrate are not publicly available. The manufacturing processes of specialized electronic components like package substrates often involve proprietary techniques and technologies that are closely guarded by the manufacturer.
However, I can provide a general outline of the typical steps involved in manufacturing package substrates in the semiconductor industry:
- Substrate Material Selection: Choose the appropriate substrate material based on the desired electrical, thermal, and mechanical properties. This could include ceramics, organic laminates, or composite materials.
- Substrate Preparation: Clean and smooth the substrate surface to remove contaminants and ensure uniformity.
- Layer Formation: Deposit or form the required layers on the substrate using techniques such as sputtering, chemical vapor deposition (CVD), or electroplating. These layers may include conductive metal layers, dielectric layers, and other functional coatings.
- Pattern Formation: Use photolithography or other patterning techniques to define the circuitry and features on the substrate. Apply photoresist, expose it to UV light through a photomask, and develop it to create patterns for metal traces, vias, and other elements.
- Etching: Use chemical or plasma etching to selectively remove material from the substrate, leaving behind the patterned features defined by the photoresist.
- Surface Finishing: Apply surface finishing processes such as metallization, solder mask application, and surface coating to enhance electrical conductivity, protect against corrosion, and provide solderability for component attachment.
- Quality Control and Testing: Implement quality control measures throughout the manufacturing process to ensure that the substrate meets required specifications and standards. Perform various tests, including electrical testing, visual inspection, and mechanical testing, to validate the quality and reliability of the finished substrate.
- Packaging and Shipping: Package the finished substrates and prepare them for shipment to semiconductor device manufacturers for further assembly and integration into electronic products.
It’s important to note that the specific manufacturing processes and technologies used for the Showa Denko MCL-E-705G package substrate may vary and could involve proprietary techniques developed by Showa Denko. For detailed information on the manufacturing process, it would be necessary to consult proprietary documentation or contact Showa Denko directly.
How much should a Showa Denko MCL-E-705G package substrate cost?
Determining the exact cost of a Showa Denko MCL-E-705G package substrate would depend on various factors including market demand, volume of production, customization requirements, and supplier agreements. Typically, package substrate costs are influenced by the complexity of the design, the materials used, the manufacturing process, and the level of technology integration.
Here are some factors that could influence the cost:
- Material Costs: The materials used in the substrate, such as ceramic or organic laminates, and the quality of the materials can significantly impact the cost. Higher-quality materials or those with specific properties like high thermal conductivity or low electrical resistance may command a higher price.
- Manufacturing Complexity: The complexity of the manufacturing process, including the number of layers, feature sizes, and tolerances, can affect the cost. More intricate designs or specialized fabrication techniques may require additional processing steps, which can increase production costs.
- Volume of Production: Economies of scale play a significant role in determining the cost of package substrates. Higher volumes typically result in lower per-unit costs due to efficiencies in production and manufacturing setup costs spread across a larger number of units.
- Customization and Special Requirements: If the substrate requires customization to meet specific customer requirements, such as unique layouts, materials, or performance characteristics, the cost may be higher to account for development and setup expenses.
- Market Dynamics: Market conditions, including supply and demand dynamics, competition among suppliers, and industry trends, can influence pricing. Prices may fluctuate based on market conditions and competitive pressures.
- Supplier Relationships: Long-term relationships between suppliers and customers, as well as negotiated contracts and agreements, can impact pricing. Bulk purchasing agreements or preferred supplier status may result in discounted pricing for certain customers.
Given these factors, it’s challenging to provide a specific cost for the Showa Denko MCL-E-705G package substrate without more detailed information about the specific requirements and market conditions. For accurate pricing information, it would be advisable to contact Showa Denko or authorized distributors for a customized quote based on your specific needs and volume requirements.
What is the Showa Denko MCL-E-705G package substrate base material?
The specific base material used for the Showa Denko MCL-E-705G package substrate may not be publicly disclosed in detail without accessing proprietary documentation or information directly from Showa Denko. However, package substrates in the semiconductor industry are typically made from various types of materials, each with its own properties and advantages.
Common base materials for package substrates include:
- Ceramics: Ceramic substrates offer excellent thermal conductivity, mechanical strength, and dimensional stability. Aluminum oxide (Al2O3) and aluminum nitride (AlN) are commonly used ceramic materials for high-power applications.
- Organic Laminates: Organic substrates, often referred to as printed circuit boards (PCBs), are made from layers of organic materials such as epoxy resin and fiberglass. They are lightweight, cost-effective, and suitable for high-density interconnects in many electronic applications.
- Composite Materials: Some package substrates may use composite materials that combine properties of ceramics and organics, offering a balance between thermal performance and cost-effectiveness.
- Metal Substrates: In certain applications, metal substrates such as copper or aluminum may be used, particularly for applications requiring high thermal conductivity and dimensional stability.
The choice of base material depends on factors such as thermal management requirements, electrical performance, mechanical properties, cost considerations, and specific application needs. Showa Denko may use proprietary formulations or specialty materials for the MCL-E-705G substrate to meet the performance requirements of their customers’ applications. For detailed information on the base material used in the Showa Denko MCL-E-705G package substrate, it would be necessary to consult proprietary documentation or contact Showa Denko directly.
Which company produces Showa Denko MCL-E-705G package substrates?
The Showa Denko MCL-E-705G package substrate is manufactured by Showa Denko, a Japanese company. As a leading chemical industry enterprise, Showa Denko possesses rich experience and technological strength in the semiconductor industry. Its MCL-E-705G package substrate is widely used in electronic products such as central processing units (CPUs), graphics processing units (GPUs), and others.
Our company also has the capability to produce MCL-E-705G package substrates. We have advanced manufacturing equipment, experienced engineering teams, and a strict quality management system, allowing us to produce high-quality package substrate products according to customer requirements. We focus on technological innovation and continuous improvement, optimizing production processes to enhance efficiency and product quality.
Our production capacity can meet various scale requirements, whether it’s small-batch customization or large-scale mass production. We are committed to providing customers with high-quality products and services, working together with them for mutual development. If you have any needs or questions regarding the production of MCL-E-705G package substrates, please feel free to contact us at any time. We will be dedicated to providing you with support and assistance.
What are the 7 qualities of good customer service?
Good customer service is characterized by several key qualities that help build positive relationships with customers and meet their needs effectively. Here are seven qualities of good customer service:
- Responsiveness: A good customer service team responds promptly to customer inquiries, concerns, and requests. This includes acknowledging messages or calls in a timely manner and providing timely updates on the status of any issues or requests.
- Empathy:Empathy involves understanding and relating to the emotions and perspectives of customers. Good customer service representatives listen actively, show genuine concern for customers’ experiences, and strive to address their needs with sensitivity and compassion.
- Professionalism: Professionalism encompasses behaving courteously, respectfully, and professionally in all interactions with customers. This includes maintaining a positive attitude, speaking clearly and politely, and adhering to company policies and standards.
- Knowledgeability: Good customer service representatives are knowledgeable about the products or services they support. They can answer questions accurately, provide relevant information, and offer helpful recommendations or solutions to customers’ problems.
- Problem-Solving Skills: Effective problem-solving skills are crucial for resolving customer issues efficiently and satisfactorily. Customer service teams should be equipped to identify and understand problems, analyze root causes, and propose viable solutions to address customer concerns.
- Consistency: Consistency in service delivery is essential for building trust and loyalty with customers. Good customer service teams strive to maintain consistent standards of service quality across all interactions and touchpoints, ensuring a reliable and predictable experience for customers.
- Follow-Up and Feedback: Following up with customers after resolving their issues demonstrates commitment to their satisfaction and provides an opportunity to gather feedback for continuous improvement. Good customer service teams seek feedback proactively, incorporate customer input into their processes, and use it to enhance the overall customer experience.
By embodying these qualities, organizations can cultivate strong customer relationships, foster customer loyalty, and differentiate themselves in the competitive marketplace.
FAQs
What is the Showa Denko MCL-E-705G package substrate?
The Showa Denko MCL-E-705G package substrate is a specialized material used in the packaging of semiconductor devices. It provides the necessary physical and electrical interface between the chip and the circuit board.
What are the key features of the MCL-E-705G package substrate?
The MCL-E-705G package substrate likely offers specific properties tailored for enhanced performance in electronic applications, such as high thermal conductivity, low electrical resistance, and excellent mechanical characteristics.
What are the typical applications of the MCL-E-705G package substrate?
The MCL-E-705G package substrate is commonly used in various electronic products, including central processing units (CPUs), graphics processing units (GPUs), and other microelectronic devices.
What materials are used in the construction of the MCL-E-705G package substrate?
While the exact materials used in the MCL-E-705G package substrate may vary, it typically involves ceramics, organic laminates, or composite materials, chosen based on desired properties and performance requirements.
What is the fabrication process for the MCL-E-705G package substrate?
The fabrication process likely involves several steps, including substrate preparation, layer formation, patterning, etching, surface finishing, quality control, and packaging. However, specific details of the process may be proprietary to Showa Denko.
What are the benefits of using the MCL-E-705G package substrate?
The MCL-E-705G package substrate offers benefits such as improved thermal management, enhanced electrical performance, mechanical robustness, and reliability, contributing to the overall performance and longevity of electronic devices.
Where can I obtain more information about the MCL-E-705G package substrate?
For more detailed information about the MCL-E-705G package substrate, including technical specifications, design guidelines, and availability, it is recommended to contact Showa Denko directly or refer to their official documentation and product resources.