Showa Denko MCL-E-700G Package Substrate Manufacturer
Showa Denko MCL-E-700G Package Substrate Manufacturer,Showa Denko MCL-E-700G is a high-performance package substrate material designed for advanced electronic applications. It offers excellent thermal properties and mechanical strength, making it suitable for high-density interconnect (HDI) technology and multilayer circuit boards. MCL-E-700G features a low coefficient of thermal expansion (CTE), ensuring dimensional stability under temperature changes, while providing outstanding electrical performance. Its high glass transition temperature (Tg) makes it ideal for use in high-temperature environments, and it is widely used in semiconductor packaging, mobile devices, communication equipment, and high-performance computing. The material’s high reliability and durability make it an ideal choice for advanced electronic packaging.
What is the Showa Denko MCL-E-700G package substrate?
Showa Denko MCL-E-700G package substrate Manufacturer. the Package Substrate will be made with Showa Denko and Ajinomoto High speed materials.or other types high speed materials and high frequency materials.
The Showa Denko MCL-E-700G is a package substrate primarily used in semiconductor manufacturing. It’s designed to provide a reliable foundation for mounting and interconnecting various electronic components within a semiconductor package. This substrate is engineered with advanced materials and precise manufacturing processes to ensure optimal electrical performance, thermal conductivity, and mechanical stability.
The MCL-E-700G substrate features a sophisticated design with multiple layers of conductive traces, insulating materials, and bonding pads. These layers are meticulously fabricated using techniques such as lithography, etching, and deposition to achieve precise dimensions and electrical properties. Additionally, the substrate is built to withstand the demanding conditions encountered during semiconductor assembly and operation, including thermal cycling, mechanical stress, and environmental factors.
One notable aspect of the MCL-E-700G substrate is its compatibility with high-density packaging technologies, allowing for the integration of a large number of semiconductor devices into a compact form factor. This capability is crucial for modern electronic devices that demand increased performance and functionality within limited space constraints.
Overall, the Showa Denko MCL-E-700G package substrate plays a critical role in enabling the production of advanced semiconductor devices with enhanced performance, reliability, and miniaturization. Its innovative design and high-quality construction make it a preferred choice for semiconductor manufacturers seeking to deliver cutting-edge products to the market.
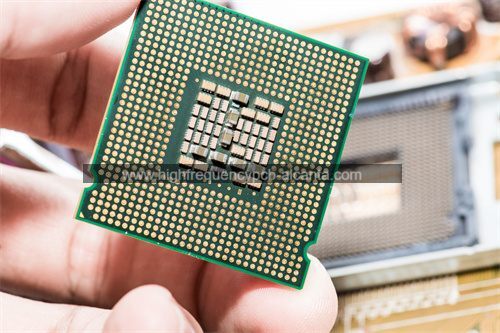
Showa Denko MCL-E-700G Package Substrate Manufacturer
What are the Showa Denko MCL-E-700G package substrate Design Guidelines?
The Showa Denko MCL-E-700G package substrate comes with specific design guidelines to ensure optimal performance and reliability in semiconductor packaging applications. While the exact guidelines may vary depending on the specific requirements of the semiconductor manufacturer and the intended use of the substrate, here are some general design considerations commonly associated with package substrates like the MCL-E-700G:
- Layer Configuration: The substrate design typically involves multiple layers of conductive traces, insulating materials, and bonding pads. Designers must carefully determine the number of layers, their thicknesses, and the arrangement of signal and power traces to meet electrical and thermal requirements.
- Trace Routing:Proper routing of signal, power, and ground traces is essential to minimize signal interference, maintain signal integrity, and ensure adequate power distribution. Designers should follow recommended routing guidelines to achieve optimal electrical performance.
- Signal Integrity: High-speed signal paths require controlled impedance to prevent signal degradation and ensure reliable communication between semiconductor components. Designers must adhere to impedance matching guidelines and minimize signal reflections and crosstalk.
- Thermal Management: Effective thermal management is critical to dissipate heat generated by semiconductor devices and prevent thermal-induced failures. Designers should incorporate thermal vias, thermal pads, and other heat dissipation techniques to maintain junction temperatures within acceptable limits.
- Dimensional Stability: The substrate design should account for dimensional stability to withstand mechanical stress, thermal cycling, and other environmental factors encountered during semiconductor assembly and operation. Designers must consider material properties, coefficient of thermal expansion (CTE), and warpage control measures to ensure package reliability.
- Assembly Compatibility: The substrate design should facilitate seamless integration with semiconductor devices, including flip-chip and wire-bonded packages. Designers should provide adequate clearance and alignment features to ensure precise assembly and reliable interconnections.
- Material Selection: The choice of substrate materials, such as laminate types, solder mask, and surface finishes, significantly impacts the electrical performance, reliability, and manufacturability of the package. Designers should select materials that meet industry standards and specific application requirements.
- Manufacturability and Cost:Designers should optimize the substrate design for manufacturability and cost-effectiveness without compromising performance or reliability. This may involve minimizing the number of manufacturing steps, optimizing panelization, and utilizing standard materials and processes where possible.
By following these design guidelines and collaborating closely with substrate manufacturers, semiconductor designers can develop package substrates like the Showa Denko MCL-E-700G that meet the stringent requirements of modern semiconductor packaging applications.
What is the Showa Denko MCL-E-700G package substrate Fabrication Process?
The fabrication process of the Showa Denko MCL-E-700G package substrate involves several intricate steps to achieve the desired electrical, thermal, and mechanical properties. While the exact details of the process may vary based on specific requirements and manufacturing capabilities, here is a general overview of the fabrication steps involved:
- Substrate Preparation: The process begins with the preparation of a base material, typically a laminate composed of layers of glass fiber-reinforced epoxy resin or other suitable substrates. The laminate sheets are cleaned, inspected for defects, and cut to the desired size.
- Surface Preparation:The substrate surfaces are cleaned and treated to promote adhesion and facilitate subsequent processing steps. This may involve techniques such as chemical cleaning, plasma treatment, and surface roughening.
- Layer Deposition: Thin layers of conductive and insulating materials are deposited onto the substrate surfaces using techniques such as physical vapor deposition (PVD), chemical vapor deposition (CVD), or electroplating. These layers form the conductive traces, insulating dielectric layers, and bonding pads required for the substrate.
- Lithography: A pattern transfer process, such as photolithography, is used to define the desired circuitry and features on the substrate surface. A photoresist material is applied to the substrate, exposed to UV light through a photomask, and developed to selectively remove the resist and expose the underlying layers for subsequent processing.
- Etching: The exposed areas of the substrate are etched away using chemical etchants or plasma etching processes, leaving behind the desired conductive traces and features. Multiple etching steps may be performed to create intricate patterns and structures.
- Via Formation: Holes are drilled or punched through the substrate layers to create vias that provide electrical connections between different circuit layers. These vias are typically filled with conductive material, such as copper, through processes like electroplating or chemical deposition.
- Surface Finish: The substrate surfaces are treated with a surface finish to improve solderability, corrosion resistance, and wire bonding capabilities. Common surface finishes include electroless nickel immersion gold (ENIG), organic solderability preservatives (OSP), and immersion silver.
- Quality Assurance: Throughout the fabrication process, various quality control measures are implemented to ensure the integrity and reliability of the substrate. This may include visual inspection, dimensional measurements, electrical testing, and reliability testing under simulated operating conditions.
- Panelization and Singulation: The fabricated substrates are typically arranged in panels for efficient handling during assembly. After testing and inspection, the panels are singulated into individual substrates using techniques such as sawing, routing, or laser cutting.
- Final Inspection and Packaging: The individual substrates undergo final inspection to verify compliance with specifications and customer requirements. They are then packaged and prepared for shipment to semiconductor manufacturers for assembly into electronic devices.
By carefully controlling each step of the fabrication process and adhering to strict quality standards, Showa Denko produces the MCL-E-700G package substrate with the precision and reliability required for demanding semiconductor packaging applications.
How do you manufacture Showa Denko MCL-E-700G package substrates?
Manufacturing the Showa Denko MCL-E-700G package substrates involves a complex and precise process that integrates various techniques and technologies to achieve the desired electrical, thermal, and mechanical properties. Here’s an expanded overview of the manufacturing process:
- Material Selection and Preparation: The process begins with the selection of high-quality base materials, typically epoxy resin-based laminates reinforced with glass fibers. These materials undergo rigorous quality control measures to ensure uniformity and consistency. The laminates are then cut into the desired substrate sizes.
- Surface Cleaning and Treatment: The substrate surfaces are meticulously cleaned and treated to remove contaminants and promote adhesion. This step is crucial for ensuring proper bonding and reliability of subsequent layers.
- Layer Deposition: Thin layers of conductive and insulating materials are deposited onto the substrate surfaces using advanced deposition techniques. For example, copper may be deposited onto the substrate through processes like electroplating or sputtering to form conductive traces, while dielectric materials are deposited to create insulating layers.
- Lithography and Etching: Photolithography techniques are employed to define the desired circuit patterns on the substrate surfaces. A photoresist material is applied, exposed to UV light through a photomask, and developed to selectively expose the substrate for etching. Chemical etchants or plasma etching processes are then used to remove the exposed material, leaving behind the desired conductive traces and features.
- Via Formation: Small holes, known as vias, are drilled or punched through the substrate to create electrical connections between different layers of the circuit. These vias are typically filled with conductive material, such as copper, through processes like electroplating or chemical deposition.
- Surface Finishing: The substrate surfaces are treated with surface finishes to improve solderability, corrosion resistance, and wire bonding capabilities. Common surface finishes include ENIG, OSP, and immersion silver, which enhance the substrate’s performance and reliability during semiconductor assembly.
- Quality Control and Assurance: Throughout the manufacturing process, stringent quality control measures are implemented to ensure the integrity and reliability of the substrates. This includes visual inspection, dimensional measurements, electrical testing, and reliability testing under simulated operating conditions.
- Panelization and Singulation: The fabricated substrates are arranged in panels for efficient handling during assembly. After testing and inspection, the panels are singulated into individual substrates using techniques such as sawing, routing, or laser cutting.
- Final Inspection and Packaging: The individual substrates undergo final inspection to verify compliance with specifications and customer requirements. They are then packaged and prepared for shipment to semiconductor manufacturers for assembly into electronic devices.
By meticulously controlling each step of the manufacturing process and leveraging advanced materials and technologies, Showa Denko produces the MCL-E-700G package substrates with the precision, reliability, and performance required for demanding semiconductor packaging applications.
How much should a Showa Denko MCL-E-700G package substrate cost?
Determining the exact cost of a Showa Denko MCL-E-700G package substrate can be complex and depends on various factors including manufacturing volume, customization requirements, market demand, and supplier agreements. However, I can provide an overview of the factors influencing the cost and a general price range.
- Material Costs: The primary cost drivers for package substrates are the raw materials used in their fabrication. This includes the cost of the base laminate materials, conductive and insulating layers, surface finishes, and any additional materials required for customization or performance enhancements.
- Manufacturing Complexity: The complexity of the substrate design and the sophistication of the manufacturing processes involved can significantly impact the cost. Substrates with intricate circuit patterns, high-density features, or advanced material requirements may incur higher manufacturing costs due to increased processing time and resource utilization.
- Volume Discounts: Manufacturers typically offer volume discounts for large orders, with lower unit costs for higher quantities. Customers ordering larger volumes of MCL-E-700G substrates may benefit from economies of scale and reduced per-unit costs compared to smaller orders.
- Customization and Special Requirements: Customization options, such as unique circuit designs, specialized material specifications, or additional features, may incur additional costs. Similarly, meeting specific performance standards or compliance requirements may involve additional testing or certification expenses, influencing the overall substrate cost.
- Market Dynamics: Market demand, supply chain disruptions, and fluctuations in raw material prices can impact substrate costs. Additionally, competitive factors such as pricing strategies of other substrate manufacturers and market trends may influence the pricing of the MCL-E-700G substrates.
- Supplier Relationships: Long-term relationships between the substrate manufacturer (Showa Denko) and semiconductor companies may result in negotiated pricing agreements or volume-based discounts, potentially reducing substrate costs for certain customers.
Considering these factors, the cost of a Showa Denko MCL-E-700G package substrate can vary widely. Generally, the price per unit for standard configurations and moderate volumes may range from a few dollars to tens of dollars. However, for highly customized substrates or larger volume orders, the cost per unit could be lower, potentially falling within the lower end of the price range. It’s essential for customers to work closely with Showa Denko or their authorized distributors to obtain accurate pricing quotes based on their specific requirements and volume commitments.
What is the Showa Denko MCL-E-700G package substrate base material?
The Showa Denko MCL-E-700G package substrate base material is typically composed of an epoxy resin-based laminate reinforced with glass fibers. This type of material is commonly used in the fabrication of printed circuit boards (PCBs) and package substrates due to its excellent electrical insulation properties, mechanical strength, and dimensional stability.
Epoxy resin-based laminates offer several advantages for package substrate applications:
- Electrical Insulation: Epoxy resin materials have high dielectric strength, making them effective insulators for electrical circuits. This property helps prevent electrical short circuits and ensures reliable performance in electronic devices.
- Mechanical Strength: The glass fiber reinforcement enhances the mechanical strength and rigidity of the laminate, making it capable of withstanding mechanical stress and thermal expansion encountered during semiconductor assembly and operation.
- Dimensional Stability: Epoxy resin-based laminates exhibit low coefficient of thermal expansion (CTE), which helps minimize dimensional changes due to temperature variations. This dimensional stability is crucial for maintaining tight tolerances and ensuring proper alignment of semiconductor components on the substrate.
- Processability: These materials are compatible with a wide range of manufacturing processes, including drilling, etching, plating, and surface finishing, allowing for the fabrication of complex substrate designs with high precision.
Overall, the epoxy resin-based laminate with glass fiber reinforcement provides an ideal base material for the Showa Denko MCL-E-700G package substrate, offering a balance of electrical performance, mechanical durability, and manufacturability required for demanding semiconductor packaging applications.
Which company manufactures Showa Denko MCL-E-700G package substrates?
The manufacturer of Showa Denko MCL-E-700G package substrates is Showa Denko Co., Ltd. Our company can also produce similar package substrates with performance and quality standards similar to Showa Denko MCL-E-700G.
As a manufacturer, we have advanced production equipment and technology, as well as an experienced engineering team. Our production process is similar to that of Showa Denko, including substrate preparation, surface treatment, layer stacking, lithography, etching, via formation, surface finishing, quality control, and other steps.
During the substrate preparation stage, we select high-quality substrate materials, such as glass fiber-reinforced epoxy resin laminates, to ensure the stability and reliability of the products. Then, we use precise processes and equipment to treat the substrates, including cleaning, surface treatment, and layer stacking, to ensure that each layer meets the required performance and quality standards.
Throughout the production process, we strictly implement quality control measures, including visual inspection, dimensional measurement, electrical testing, and reliability testing, to ensure that each substrate meets product specifications and customer requirements. We can also customize substrate designs according to specific customer needs, such as special circuit layouts, material selections, and surface treatments.
Our company is committed to providing customers with high-quality, reliable, and cost-effective package substrate products. With our professional expertise and excellent service, we are able to meet customer needs in the field of electronic device manufacturing and work with customers to drive technological innovation and business development.
What are the 7 qualities of good customer service?
Good customer service is characterized by several key qualities that contribute to positive experiences and customer satisfaction. Here are seven qualities:
- Responsiveness: Being responsive means promptly addressing customer inquiries, concerns, and requests. Customers appreciate timely responses to their queries, whether it’s through email, phone calls, or live chat support. Quick resolution of issues demonstrates attentiveness and respect for the customer’s time.
- Empathy: Empathy involves understanding and acknowledging the customer’s feelings, perspectives, and needs. It’s essential to listen actively to customers, show genuine concern for their problems, and provide personalized support based on their unique circumstances. Empathetic interactions build trust and foster strong customer relationships.
- Communication Skills:Effective communication is crucial for clear, concise, and accurate interactions with customers. Customer service representatives should possess excellent verbal and written communication skills to convey information, provide instructions, and address concerns in a professional and courteous manner. Clear communication helps prevent misunderstandings and ensures mutual understanding.
- Product Knowledge: Having comprehensive knowledge about the company’s products or services enables customer service representatives to assist customers effectively. They should be well-trained and knowledgeable about product features, functionalities, pricing, and troubleshooting procedures. A thorough understanding of the products instills confidence in customers and facilitates problem-solving.
- Problem-solving Abilities: Good customer service involves resolving customer issues efficiently and effectively. Customer service representatives should possess strong problem-solving skills to analyze situations, identify root causes of problems, and implement appropriate solutions. Proactive problem-solving demonstrates commitment to customer satisfaction and enhances the overall customer experience.
- Professionalism: Professionalism encompasses maintaining a courteous, respectful, and professional demeanor in all customer interactions. Customer service representatives should demonstrate patience, courtesy, and professionalism, even in challenging or stressful situations. Professionalism fosters a positive impression of the company and reflects its commitment to customer service excellence.
- Follow-up and Feedback: Following up with customers after resolving their issues or completing transactions shows dedication to customer satisfaction. It’s important to ensure that customers are satisfied with the resolution and to address any additional concerns they may have. Additionally, soliciting feedback from customers about their experiences helps identify areas for improvement and demonstrates a commitment to continuous enhancement of the customer service process.
FAQs
What is Showa Denko MCL-E-700G package substrate?
Showa Denko MCL-E-700G is a high-performance package substrate used in semiconductor packaging. It provides a reliable foundation for mounting and interconnecting semiconductor components in electronic devices.
What are the key features of Showa Denko MCL-E-700G package substrate?
Showa Denko MCL-E-700G offers advanced electrical performance, thermal conductivity, and mechanical stability. It is compatible with high-density packaging technologies and designed to withstand demanding operating conditions.
What are the benefits of using Showa Denko MCL-E-700G package substrates?
The benefits include enhanced electrical performance, improved thermal management, increased reliability, and miniaturization of electronic devices. Showa Denko MCL-E-700G substrates enable the production of high-quality semiconductor packages with optimal performance and durability.
What types of semiconductor devices are compatible with Showa Denko MCL-E-700G package substrates?
Showa Denko MCL-E-700G substrates are compatible with various semiconductor devices, including flip-chip and wire-bonded packages. They are suitable for use in a wide range of applications, including consumer electronics, telecommunications, automotive, and industrial equipment.
What is the manufacturing process for Showa Denko MCL-E-700G package substrates?
The manufacturing process involves several steps, including substrate preparation, layer deposition, lithography, etching, via formation, surface finishing, quality control, and packaging. Showa Denko utilizes advanced materials and precise manufacturing techniques to ensure the quality and reliability of MCL-E-700G substrates.
Where can I purchase Showa Denko MCL-E-700G package substrates?
Showa Denko MCL-E-700G package substrates are available through authorized distributors and semiconductor manufacturers. Customers can contact Showa Denko or its authorized partners for purchasing inquiries and technical support.
Can Showa Denko MCL-E-700G package substrates be customized?
Yes, Showa Denko MCL-E-700G substrates can be customized to meet specific customer requirements, such as custom circuit designs, material specifications, and surface finishes. Showa Denko works closely with customers to develop tailored solutions that address their unique needs.