Semiconductor IC Substrate Manufacturer
Semiconductor IC Substrate Manufacturer,Semiconductor IC Substrate is a foundational element in integrated circuit manufacturing, providing a platform for mounting and connecting semiconductor chips. It comprises multiple layers of materials, including insulators, conductors, and metal traces, to ensure reliable electrical connections and efficient heat dissipation. Semiconductor IC Substrates support high-density integration, enabling the miniaturization of electronic devices. They play a crucial role in optimizing signal transmission and power distribution, enhancing the performance and reliability of semiconductor devices across various applications, from consumer electronics to industrial automation. These substrates drive advancements in semiconductor technology, enabling innovation and progress in modern electronics.
A Semiconductor IC (Integrated Circuit) substrate, also known as a wafer substrate, is a foundational material upon which semiconductor devices are manufactured. It serves as a base for the fabrication of integrated circuits, which are essential components in electronic devices.
Semiconductor IC substrates are typically made from materials such as silicon, silicon germanium, or other semiconductor materials. These substrates undergo various processes such as doping, etching, deposition, and lithography to create the intricate patterns and structures that form the integrated circuits.
The choice of substrate material depends on the specific requirements of the integrated circuit being manufactured, including factors such as performance, cost, and scalability. Silicon is the most commonly used substrate material due to its abundance, excellent semiconductor properties, and established manufacturing processes.
Overall, the semiconductor IC substrate plays a crucial role in the manufacturing of integrated circuits, providing the foundation upon which electronic devices are built.
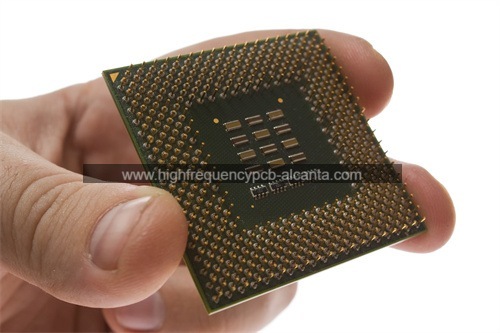
Semiconductor IC Substrate Manufacture?
What are the functions of Semiconductor IC Substrate?
Semiconductor IC substrates serve several critical functions in the manufacturing and operation of integrated circuits:
Support Structure: The substrate provides a stable and mechanically robust platform upon which semiconductor devices can be fabricated. It supports the various layers and components of the integrated circuit.
Electrical Conduction: Substrates typically have electrical conductivity or are doped to facilitate the flow of electric current within the integrated circuit. This enables the connection of different components and the transmission of signals between them.
Thermal Management: Substrates often dissipate heat generated during the operation of the integrated circuit. Efficient thermal management is essential to prevent overheating, which can degrade performance and reliability.
Dielectric Isolation: In some cases, substrates are used to provide electrical isolation between different components or sections of the integrated circuit. This prevents interference and ensures proper functioning of the device.
Integration of Components: Substrates enable the integration of various semiconductor components, such as transistors, diodes, and resistors, into a single device. This integration is essential for achieving high performance and compactness in modern electronic devices.
Chemical Compatibility: Substrates must be chemically compatible with the materials used in the fabrication process, including deposition, etching, and doping processes. Compatibility ensures proper manufacturing and reliability of the integrated circuit.
Dimensional Stability: Substrates must maintain their dimensional stability and flatness throughout the manufacturing process to ensure precise patterning and alignment of components. Any distortions or deviations can lead to defects and performance issues in the integrated circuit.
Overall, semiconductor IC substrates play a crucial role in the fabrication and operation of integrated circuits, providing structural support, electrical connectivity, thermal management, and other essential functions necessary for the proper functioning of electronic devices.
What are the different types of Semiconductor IC Substrate?
There are several different types of semiconductor IC substrates, each with its own unique characteristics and applications. Some common types include:
Silicon Substrates: Silicon is the most widely used substrate material in semiconductor manufacturing. It offers excellent electrical properties, compatibility with standard fabrication processes, and high mechanical strength. Silicon substrates come in various grades and orientations (such as <100>, <111>, etc.) to suit different manufacturing requirements.
Silicon-on-Insulator (SOI) Substrates: SOI substrates consist of a thin layer of silicon (the device layer) on top of a thick layer of insulating material (usually silicon dioxide). This structure reduces parasitic capacitance, improves device performance, and enables integration of advanced features such as silicon-on-insulator transistors and silicon germanium devices.
Gallium Arsenide (GaAs) Substrates: GaAs substrates are used in high-frequency and high-speed applications, such as RF (Radio Frequency) devices, microwave amplifiers, and optoelectronic components. GaAs offers superior electron mobility compared to silicon, making it well-suited for high-frequency operation.
Silicon Germanium (SiGe) Substrates: SiGe substrates combine silicon and germanium to enhance the performance of silicon-based integrated circuits. SiGe substrates are used in applications requiring high-speed transistors, such as communication systems, radar, and aerospace applications.
Gallium Nitride (GaN) Substrates: GaN substrates are used in power electronics and high-frequency devices due to their excellent electrical properties, high breakdown voltage, and high electron mobility. GaN-based integrated circuits are commonly employed in applications such as LED lighting, wireless power transfer, and RF amplifiers.
Sapphire Substrates: Sapphire substrates are used primarily in optoelectronic applications, such as LEDs (Light Emitting Diodes) and laser diodes. Sapphire offers excellent thermal conductivity, optical transparency, and mechanical durability, making it suitable for high-power and high-temperature environments.
Glass Substrates: Glass substrates are used in certain niche applications, such as MEMS (Microelectromechanical Systems) devices and biochips. Glass offers advantages such as optical transparency, chemical inertness, and compatibility with microfabrication processes.
These are just a few examples of the diverse range of semiconductor IC substrates available, each tailored to specific performance requirements and manufacturing processes in different applications.
What is the relationship between Semiconductor IC Substrate and IC packaging?
Semiconductor IC substrates and IC packaging are two essential components in the fabrication and assembly of integrated circuits (ICs), and they are closely related in the overall IC manufacturing process. Here’s how they are interconnected:
Fabrication Process: Semiconductor IC substrates serve as the foundation upon which the semiconductor devices are fabricated using various processes such as doping, etching, deposition, and lithography. These processes create the intricate patterns and structures that form the integrated circuits. Once the semiconductor devices are fabricated on the substrate, they need to be protected, interconnected, and mounted onto a package.
Interconnection: After the semiconductor devices are fabricated on the substrate, they need to be interconnected to form functional circuits. This interconnection is achieved through a combination of metal traces, vias, and bonding wires, which link the individual devices together and connect them to the external pins or leads of the IC package. The layout and design of the interconnection are critical for ensuring proper functionality, performance, and reliability of the integrated circuit.
Protection and Encapsulation: IC packaging provides protection for the semiconductor devices from environmental factors such as moisture, dust, and mechanical stress. The IC package encapsulates the semiconductor die and interconnects them to the external world through pins, leads, or solder balls. The package material and design play a crucial role in ensuring the reliability and longevity of the integrated circuit in various operating conditions.
Thermal Management: Both semiconductor IC substrates and IC packages play a role in thermal management. Substrates dissipate heat generated by the semiconductor devices during operation, while IC packages provide additional thermal dissipation through features such as thermal vias, heat sinks, and thermal pads. Efficient thermal management is essential for maintaining the reliability and performance of the integrated circuit.
Overall, semiconductor IC substrates and IC packaging are integral components in the fabrication, assembly, and protection of integrated circuits. They work together to ensure proper functionality, reliability, and performance of ICs in various applications ranging from consumer electronics to industrial and automotive systems.
How does Semiconductor IC Substrate differ from PCB?
Semiconductor IC substrates and PCBs (Printed Circuit Boards) are both essential components in electronic devices, but they serve different purposes and exhibit distinct characteristics. Here are some key differences between the two:
Functionality:
Semiconductor IC Substrate: The primary function of a semiconductor IC substrate is to serve as the foundation upon which semiconductor devices are fabricated. It provides support, electrical connectivity, and thermal management for the integrated circuits.
PCB: A PCB, on the other hand, acts as a platform for mounting and interconnecting various electronic components such as integrated circuits, resistors, capacitors, and connectors. It provides electrical pathways for signal transmission and power distribution within the electronic system.
Materials:
Semiconductor IC Substrate: Substrates for integrated circuits are typically made from semiconductor materials such as silicon, silicon germanium, gallium arsenide, or sapphire. These materials have specific electrical, thermal, and mechanical properties tailored for semiconductor device fabrication.
PCB: PCBs are typically made from non-conductive materials such as fiberglass epoxy laminates (FR-4), polyimide, or ceramic. Conductive traces made from copper or other metals are patterned on the surface of the PCB to create electrical pathways.
Manufacturing Processes:
Semiconductor IC Substrate: The fabrication of semiconductor IC substrates involves specialized processes such as doping, etching, deposition, and lithography to create semiconductor devices such as transistors, diodes, and resistors.
PCB: PCBs are manufactured using processes such as printing, etching, drilling, and soldering. Electronic components are mounted onto the PCB surface and connected using soldering, wire bonding, or surface-mount technology (SMT).
Complexity and Integration:
Semiconductor IC Substrate: IC substrates are typically used for fabricating complex integrated circuits containing thousands to billions of transistors. They are highly integrated and optimized for specific applications such as microprocessors, memory chips, and sensors.
PCB: PCBs can vary in complexity from simple single-layer boards to highly complex multilayer boards with intricate routing and multiple components. They can support a wide range of electronic devices and circuits, from basic electronic gadgets to sophisticated computer systems and telecommunications equipment.
In summary, while both semiconductor IC substrates and PCBs are crucial components in electronic devices, they differ in their functionality, materials, manufacturing processes, and complexity. Semiconductor IC substrates focus on the fabrication of integrated circuits, whereas PCBs facilitate the interconnection and mounting of electronic components within a system.
What are the structure and production technology of Semiconductor IC Substrate?
The structure and production technology of semiconductor IC substrates can vary depending on factors such as the substrate material, device architecture, and manufacturing requirements. However, I’ll outline a general overview of the structure and production technology commonly used for silicon-based semiconductor IC substrates:
Structure:
Silicon-based semiconductor IC substrates typically consist of a single crystalline silicon wafer with specific crystal orientation (e.g., <100>, <111>). The substrate’s surface is usually polished to achieve a smooth and flat surface, essential for subsequent processing steps.
Depending on the application and device requirements, additional layers may be added to the substrate. For example, in Silicon-on-Insulator (SOI) substrates, a layer of silicon dioxide (SiO2) is added to provide electrical isolation between the substrate and the device layer.
The substrate may also undergo doping processes to modify its electrical properties. Dopants such as boron, phosphorus, or arsenic are introduced into the silicon substrate to create regions with specific conductivity types (p-type or n-type) required for semiconductor devices.
Production Technology:
Wafer Preparation: The production process begins with the preparation of silicon wafers. Raw silicon ingots are sliced into thin wafers using diamond saws or wire saws. The wafers are then polished to remove surface defects and achieve the desired flatness and smoothness.
Doping: Dopants are introduced into the silicon substrate to create regions with specific electrical properties. This is typically done through processes such as ion implantation or diffusion, where dopant atoms are implanted or diffused into the substrate and then activated through annealing.
Epitaxial Growth (Optional): In some cases, epitaxial layers may be grown on the substrate to enhance device performance. Epitaxial growth involves depositing a thin layer of semiconductor material (e.g., silicon or silicon germanium) onto the substrate’s surface using techniques such as chemical vapor deposition (CVD) or molecular beam epitaxy (MBE).
Lithography and Patterning: Photolithography and patterning processes are used to define the intricate patterns and structures of semiconductor devices on the substrate’s surface. This involves applying a photoresist layer, exposing it to ultraviolet light through a mask, and then developing the resist to transfer the pattern onto the substrate through etching or deposition processes.
Device Fabrication: Following lithography, various processes such as ion implantation, oxidation, deposition (e.g., thin-film deposition, chemical vapor deposition), and etching are used to create semiconductor devices such as transistors, diodes, and interconnects on the substrate.
Packaging: Once the semiconductor devices are fabricated on the substrate, they are typically packaged to protect them from environmental factors and facilitate their integration into electronic systems. Packaging processes involve mounting the substrate onto a package, wire bonding or flip-chip bonding the devices, encapsulating them with a protective material (e.g., epoxy resin), and connecting them to external leads or pins.
Overall, the production technology of semiconductor IC substrates involves a series of precise and intricate processes to create the complex structures and devices required for integrated circuits. These processes require advanced equipment, cleanroom facilities, and expertise in semiconductor fabrication techniques.
Frequently Asked Questions (FAQs):
What is a Semiconductor IC Substrate?
A Semiconductor IC Substrate, also known as a wafer substrate, is a foundational material upon which semiconductor devices are manufactured. It serves as a base for the fabrication of integrated circuits, providing support, electrical connectivity, and thermal management for the devices.
What materials are used in Semiconductor IC Substrates?
Semiconductor IC substrates are typically made from materials such as silicon, silicon germanium, gallium arsenide, sapphire, or glass, depending on the specific requirements of the integrated circuit being manufactured.
What is the difference between Semiconductor IC Substrate and PCB?
Semiconductor IC substrates focus on the fabrication of semiconductor devices such as transistors, diodes, and resistors, while PCBs (Printed Circuit Boards) facilitate the interconnection and mounting of various electronic components within a system. IC substrates are typically made from semiconductor materials, whereas PCBs are made from non-conductive materials such as fiberglass epoxy laminates or polyimide.
What are the functions of Semiconductor IC Substrates?
Semiconductor IC substrates serve several critical functions, including providing structural support, electrical conduction, thermal management, dielectric isolation, integration of components, chemical compatibility, and dimensional stability for the fabrication and operation of integrated circuits.
How are Semiconductor IC Substrates manufactured?
The production technology of semiconductor IC substrates involves processes such as wafer preparation, doping, epitaxial growth (if needed), lithography, patterning, device fabrication, and packaging. These processes require advanced equipment, cleanroom facilities, and expertise in semiconductor fabrication techniques.
What are the different types of Semiconductor IC Substrates?
Semiconductor IC substrates come in various types, including silicon substrates, Silicon-on-Insulator (SOI) substrates, gallium arsenide (GaAs) substrates, silicon germanium (SiGe) substrates, gallium nitride (GaN) substrates, and sapphire substrates, each tailored to specific performance requirements and manufacturing processes in different applications.
Conclusion
In conclusion, Semiconductor IC Substrates play a crucial role in the manufacturing and operation of integrated circuits (ICs), serving as the foundation upon which semiconductor devices are fabricated. These substrates provide structural support, electrical connectivity, thermal management, and other essential functions necessary for the proper functioning of electronic devices.
Semiconductor IC substrates are manufactured using advanced processes such as wafer preparation, doping, epitaxial growth, lithography, patterning, device fabrication, and packaging. Different types of substrates, such as silicon, Silicon-on-Insulator (SOI), gallium arsenide (GaAs), silicon germanium (SiGe), gallium nitride (GaN), and sapphire, are available to meet specific performance requirements in various applications.
Understanding the functions, materials, manufacturing processes, and types of semiconductor IC substrates is essential for engineers, researchers, and professionals involved in semiconductor device fabrication and electronics manufacturing. These substrates enable the development of innovative electronic devices that drive advancements in technology and improve the quality of life for people worldwide.