Semiconductor Glass Substrates Manufacturer
Semiconductor Glass Substrates Manufacturer,Semiconductor glass substrates are specialized materials used in the fabrication of semiconductor devices. These substrates provide a stable and smooth surface for depositing thin films and semiconductor layers crucial for electronic components. They are engineered with high thermal stability and low coefficient of thermal expansion to withstand the rigorous processing conditions required in semiconductor manufacturing. Semiconductor glass substrates facilitate precise patterning of integrated circuits (ICs) and microelectromechanical systems (MEMS), enabling high-density packaging and miniaturization of electronic devices. They are essential in industries such as microelectronics, optoelectronics, and sensor technology, supporting advancements in semiconductor devices for applications ranging from smartphones to medical equipment.
What is a Semiconductor Glass Substrate?
A semiconductor glass substrate is a specialized material used in the manufacturing of electronic components and devices, particularly in semiconductor and optoelectronic industries. It serves as a base or foundation upon which semiconductor devices like integrated circuits (ICs), light-emitting diodes (LEDs), and photovoltaic cells are fabricated.
These substrates are typically made from materials like silicon dioxide (silica) or borosilicate glass, which possess specific properties essential for semiconductor device fabrication. Such properties include high thermal stability, excellent optical transparency in certain wavelengths, low thermal expansion coefficient to match that of silicon, and compatibility with various thin-film deposition techniques such as chemical vapor deposition (CVD) and physical vapor deposition (PVD).
The use of semiconductor glass substrates is crucial in enabling the miniaturization and performance enhancement of electronic devices. They provide a stable platform for the deposition and patterning of semiconductor materials and allow for precise control over the device’s electrical and optical characteristics. Moreover, these substrates facilitate the integration of multiple components onto a single chip, thereby enhancing the efficiency and functionality of modern electronics.
In summary, semiconductor glass substrates play a vital role in the semiconductor industry by providing a reliable foundation for the production of advanced electronic and optoelectronic devices, contributing significantly to technological advancements in various fields including telecommunications, computing, and renewable energy.
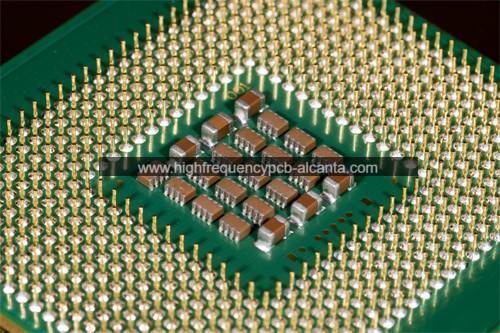
Semiconductor Glass Substrates Manufacturer
What are Semiconductor Glass Substrate Design Guidelines?
Design guidelines for semiconductor glass substrates are critical to ensure optimal performance and reliability of electronic and optoelectronic devices. Here are some key guidelines:
- Material Selection: Choose a substrate material with properties suitable for the intended application. Common materials include silicon dioxide (SiO2) and borosilicate glass due to their thermal stability, low thermal expansion coefficient, and compatibility with deposition processes.
- Surface Quality: Ensure the substrate has a smooth, clean surface free from defects, particles, and contaminants. This is crucial for uniform deposition and device reliability.
- Dimensional Stability: Semiconductor glass substrates should have precise dimensional control to match the requirements of photolithography and subsequent processing steps. This ensures accurate alignment and patterning.
- Thermal Properties: Optimize thermal conductivity and coefficient of thermal expansion (CTE) to match those of semiconductor materials like silicon. This minimizes thermal stress during device operation and thermal cycling.
- Optical Transparency: If optical transparency is required (e.g., for optoelectronic devices), select a substrate material with high transparency in relevant wavelengths.
- Chemical Compatibility: Ensure compatibility with the chemicals and processes used in deposition, etching, and cleaning steps. This prevents substrate damage and ensures device reliability.
- Electrical Properties: Maintain low electrical conductivity and high dielectric strength to minimize leakage currents and parasitic effects in electronic devices.
- Handling and Processing: Design substrates with appropriate handling features (e.g., notch, flat, or alignment marks) to facilitate automated handling and alignment during manufacturing.
- Quality Control: Implement rigorous quality control measures during substrate manufacturing to ensure uniformity and reliability across batches.
- Environmental Stability: Consider environmental factors such as humidity and temperature stability to ensure long-term device performance and reliability.
By adhering to these design guidelines, manufacturers can optimize the performance, reliability, and yield of semiconductor devices fabricated on glass substrates. Each guideline contributes to ensuring that the substrate provides a stable and conducive platform for the deposition, patterning, and integration of semiconductor materials and components.
What is the Semiconductor Glass Substrate Fabrication Process?
The fabrication process of semiconductor glass substrates involves several key steps to prepare the material for subsequent deposition and patterning of semiconductor devices. Here’s an overview of the typical fabrication process:
- Material Selection: Semiconductor glass substrates are usually made from materials like silicon dioxide (SiO2) or borosilicate glass. The choice depends on the desired properties such as thermal stability, thermal expansion coefficient, optical transparency, and compatibility with deposition techniques.
- Cleaning and Surface Preparation: The glass substrates undergo thorough cleaning to remove contaminants, particles, and organic residues. This is usually done using a combination of solvent cleaning, acid etching, and rinsing in deionized water. The goal is to achieve a clean, smooth surface free from defects that could affect subsequent processing steps.
- Preparation for Deposition: After cleaning, the substrates are dried and inspected for cleanliness and surface quality. They may undergo additional surface treatments if necessary to promote adhesion or modify surface properties.
- Thin Film Deposition: Semiconductor devices require thin films of materials like silicon (Si), silicon nitride (Si3N4), silicon dioxide (SiO2), metals, or other semiconductor materials. Deposition techniques such as Chemical Vapor Deposition (CVD), Physical Vapor Deposition (PVD), or Atomic Layer Deposition (ALD) are commonly used. These techniques allow precise control over film thickness and uniformity.
- Patterning: Photolithography is used to define patterns on the thin films deposited on the glass substrates. This involves coating the substrate with a photoresist, exposing it to UV light through a mask, and developing to selectively remove the resist. The exposed areas are then etched to transfer the pattern into the underlying thin films.
- Post-Processing Steps: After patterning, additional processing steps such as annealing, chemical cleaning, and surface passivation may be performed to improve the electrical and mechanical properties of the deposited materials.
- Quality Control and Testing: Throughout the fabrication process, rigorous quality control measures are implemented to ensure the substrates meet specifications for dimensional accuracy, surface smoothness, film thickness uniformity, and overall cleanliness. Testing may include electrical testing, optical inspection, and surface metrology.
- Packaging and Handling: Once fabricated, semiconductor glass substrates are packaged in clean environments to prevent contamination. They are handled carefully to avoid damage to the delicate thin films and patterns.
Overall, the semiconductor glass substrate fabrication process involves precise control over cleaning, deposition, patterning, and quality assurance to produce substrates that serve as reliable platforms for the fabrication of advanced semiconductor devices such as integrated circuits (ICs), LEDs, and photovoltaic cells. Each step plays a crucial role in achieving high device performance and yield in semiconductor manufacturing.
How do you manufacture Semiconductor Glass Substrates?
Manufacturing semiconductor glass substrates involves a series of meticulous steps to ensure the materials meet stringent requirements for subsequent semiconductor device fabrication. Here’s an in-depth look into the process:
- Material Selection and Preparation:Semiconductor glass substrates are typically made from materials such as silicon dioxide (SiO2) or borosilicate glass. The choice depends on factors like thermal stability, coefficient of thermal expansion (CTE), optical transparency, and compatibility with deposition processes. The raw materials undergo thorough inspection and purification to ensure they meet the required specifications.
- Cleaning and Surface Preparation:The first critical step is cleaning the glass substrates. This involves several stages of cleaning to remove organic residues, particles, and contaminants. Techniques include ultrasonic cleaning in solvents like acetone and isopropyl alcohol, followed by acid etching to remove metallic contaminants and oxide layers. Finally, rinsing in deionized water ensures a clean and particle-free surface.
- Surface Treatment:After cleaning, the substrates may undergo surface treatments to modify surface properties. This could include treatments to enhance surface adhesion for subsequent thin-film deposition processes. Plasma cleaning or chemical treatments are commonly used to activate the surface and promote adhesion of thin films.
- Thin Film Deposition:Semiconductor devices require thin films of various materials such as silicon (Si), silicon nitride (Si3N4), silicon dioxide (SiO2), metals (e.g., aluminum, titanium), or other semiconductor materials. Deposition techniques like Chemical Vapor Deposition (CVD), Physical Vapor Deposition (PVD), or Atomic Layer Deposition (ALD) are employed. These methods allow precise control over film thickness, uniformity, and composition. Each layer deposition is carefully monitored to ensure conformity to design specifications.
- Patterning:Patterning is a crucial step where photolithography techniques are used to define intricate patterns on the deposited thin films. This involves coating the substrate with a photoresist, exposing it to UV light through a mask that defines the desired pattern, and then developing the resist to remove the exposed areas. The exposed thin films are subsequently etched to transfer the pattern into the underlying layers. High-resolution lithography tools ensure precise alignment and pattern fidelity.
- Post-Processing:After patterning, additional steps may be performed to optimize the electrical and mechanical properties of the substrates. This can include annealing processes to relieve stress in the films, chemical cleaning to remove residues from etching processes, and surface passivation to protect the patterns and ensure long-term stability.
- Quality Control and Testing:Throughout the manufacturing process, rigorous quality control measures are implemented. This includes inspection of substrate cleanliness, film thickness uniformity, pattern fidelity, and defect detection using advanced metrology tools such as scanning electron microscopes (SEM) and optical profilometers. Electrical testing may also be conducted to verify substrate performance characteristics.
- Packaging and Handling:Once fabrication is complete, semiconductor glass substrates are carefully packaged in cleanroom environments to prevent contamination. They are handled using protocols that minimize the risk of damage to the delicate thin films and patterns. Proper packaging ensures the substrates maintain their integrity during transportation and storage.
In summary, the manufacturing process of semiconductor glass substrates integrates advanced materials science, precise deposition techniques, and stringent quality control measures. These substrates serve as essential platforms for the fabrication of high-performance semiconductor devices, contributing to advancements in electronics, optoelectronics, and renewable energy technologies. Each step in the process plays a crucial role in achieving reliable and efficient semiconductor glass substrates tailored to specific industry requirements.
How much should a Semiconductor Glass Substrate cost?
The cost of semiconductor glass substrates can vary widely depending on several factors:
- Material Type: The choice of glass material (e.g., silicon dioxide, borosilicate glass) can significantly impact the cost. Silicon dioxide substrates tend to be more affordable compared to specialized glasses with enhanced properties.
- Size and Thickness: Larger substrates and thicker substrates generally cost more due to increased material usage and manufacturing complexity.
- Surface Quality: Substrates with high surface cleanliness and smoothness command a premium due to the additional processing steps required to achieve these characteristics.
- Manufacturing Complexity:Complex patterning, multiple-layer deposition, and stringent quality control measures can increase manufacturing costs.
- Volume and Economy of Scale: Larger production volumes often lead to lower per-unit costs due to economies of scale. Small batch productions or custom orders may be more expensive.
- Supplier and Market Demand: Prices can vary between suppliers and regions based on competition, market demand, and supplier capabilities.
Generally, semiconductor glass substrates are priced based on a combination of these factors, with high-quality, large-area, and custom-designed substrates commanding higher prices. For precise pricing, contacting semiconductor substrate manufacturers or suppliers would provide the most accurate information tailored to current market conditions and specific requirements.
What is Semiconductor Glass Substrate base material?
Semiconductor glass substrates are primarily based on materials such as silicon dioxide (SiO2) and borosilicate glass. These materials are chosen for their specific properties that are crucial for semiconductor device fabrication:
- Silicon Dioxide (SiO2):
– Properties: Silicon dioxide is known for its excellent thermal stability, high transparency in certain wavelengths, and a low coefficient of thermal expansion (CTE) that closely matches that of silicon.
– Applications: It is widely used as a substrate material in semiconductor manufacturing, particularly for its compatibility with deposition techniques like Chemical Vapor Deposition (CVD) and its ability to provide a stable base for thin-film deposition and patterning.
- Borosilicate Glass:
– Properties: Borosilicate glass combines boron oxide with silica, offering enhanced thermal shock resistance compared to standard soda-lime glass. It also has a low CTE and good optical clarity.
– Applications: Borosilicate glass substrates are used when higher thermal stability and resistance to thermal shock are required, making them suitable for applications in which the substrate may be subjected to rapid temperature changes during processing or operation.
These base materials undergo rigorous manufacturing processes to ensure high purity, cleanliness, and uniformity, which are essential for semiconductor device fabrication. The choice between silicon dioxide and borosilicate glass depends on specific application requirements such as thermal management, optical transparency, and compatibility with deposition techniques. Each material plays a crucial role in providing a stable and reliable foundation for the deposition, patterning, and integration of semiconductor materials in various electronic and optoelectronic devices.
Which companies make Semiconductor Glass Substrates?
There are many companies that manufacture semiconductor glass substrates, mainly including leading semiconductor equipment suppliers and specialized semiconductor glass substrate manufacturers globally. Here are some well-known companies:
- Corning: Corning is a globally renowned glass and ceramics manufacturer. Its Corning Optical Communications division provides various glass substrates for optical and electronic applications, including specialty glass substrates used in semiconductor manufacturing.
- AGC (Asahi Glass Company): AGC is a leading Japanese glass manufacturing company, offering a range of high-performance glass products, including specialty glass substrates used in semiconductor manufacturing.
- Shin-Etsu Chemical: Shin-Etsu Chemical is a global leader in semiconductor materials. They provide a variety of high-purity glass substrates and materials for semiconductor manufacturing.
- Sumitomo Glass: Sumitomo Glass is a large Japanese glass manufacturing company involved in various glass products, including high-performance glass substrates for semiconductor industries.
- NGK Insulators: NGK is specialized in electronic materials and devices. They offer high-purity silicon and glass substrates for semiconductor manufacturing.
In addition, many other companies are involved in the manufacture of semiconductor glass substrates, such as Schott from Germany and Asahi Glass from the United States.
Our company can manufacture semiconductor glass substrates due to our advanced material preparation technology and process control capabilities. We specialize in custom production, providing semiconductor glass substrates in various sizes, thicknesses, and material characteristics according to specific customer requirements. Our manufacturing process includes rigorous raw material selection and quality control, advanced thin-film deposition technologies, precise lithography and patterning, and detailed post-processing steps to ensure the final performance and stability of our products. With our professional team and advanced equipment, we are committed to delivering high-quality semiconductor glass substrates to support innovative applications in electronics, optoelectronics, and other high-tech fields for our customers.
What are the qualities of good customer service?
Good customer service is characterized by several key qualities that contribute to positive interactions and relationships between businesses and their customers:
- Responsiveness:Being prompt in addressing customer inquiries, concerns, and requests. Quick response times show customers that their needs are valued and important.
- Empathy: Understanding and acknowledging the customer’s emotions, concerns, and perspective. Empathetic responses demonstrate care and build rapport.
- Clear Communication: Providing information in a clear and understandable manner. Avoiding jargon and ensuring customers have all the details they need promotes transparency and reduces misunderstandings.
- Professionalism: Maintaining a courteous and respectful demeanor in all interactions. Professionalism instills confidence and trust in customers.
- Problem-Solving Skills:Ability to effectively resolve issues and find solutions to customer problems. Being proactive in resolving issues demonstrates commitment to customer satisfaction.
- Knowledgeability: Having a thorough understanding of products, services, and policies. Knowledgeable staff can provide accurate information and guidance to customers.
- Patience: Remaining calm and patient, especially in challenging situations. Patience helps to de-escalate tensions and fosters a positive customer experience.
- Personalization: Tailoring interactions and solutions to meet the specific needs and preferences of each customer. Personalized service makes customers feel valued and understood.
- Consistency: Providing consistent service across all channels and interactions. Consistency builds trust and reliability with customers.
- Follow-up: Checking back with customers to ensure their issues were resolved satisfactorily. Follow-up shows commitment to customer satisfaction and can uncover any lingering concerns.
Businesses that prioritize these qualities in their customer service practices tend to build stronger customer loyalty, positive word-of-mouth recommendations, and ultimately, sustainable business growth.
FAQs
What are semiconductor glass substrates?
Semiconductor glass substrates are specialized materials used as the foundation for manufacturing semiconductor devices such as integrated circuits (ICs), LEDs, and photovoltaic cells. They provide a stable platform for depositing and patterning semiconductor materials.
What are semiconductor glass substrates made of?
Semiconductor glass substrates are typically made from materials like silicon dioxide (SiO2) or borosilicate glass. These materials offer properties such as thermal stability, low thermal expansion coefficient, and compatibility with deposition techniques.
How are semiconductor glass substrates manufactured?
Manufacturing involves processes such as cleaning and preparation of raw materials, deposition of thin films using techniques like Chemical Vapor Deposition (CVD), patterning through photolithography, and rigorous quality control to ensure uniformity and reliability.
What industries use semiconductor glass substrates?
Semiconductor glass substrates are essential in industries such as electronics, telecommunications, optoelectronics (LEDs and lasers), solar energy (photovoltaics), and semiconductor device manufacturing.
What sizes and shapes do semiconductor glass substrates come in?
They are available in various sizes and shapes depending on the specific application requirements, ranging from small wafers used in ICs to larger panels used in photovoltaic cells.
How do semiconductor glass substrates contribute to technology advancement?
They enable the miniaturization, integration, and performance enhancement of semiconductor devices, supporting advancements in electronics, renewable energy, telecommunications, and more.