Semiconductor Glass Package Substrates Manufacturer
Semiconductor Glass Package Substrates Manufacturer,Glass Package Substrates (SGPS) are specialized substrates used in semiconductor packaging, playing a crucial role in providing a stable foundation for mounting and interconnecting semiconductor devices. These substrates are typically made of high-quality glass materials, chosen for their excellent electrical insulation properties, thermal stability, and compatibility with high-frequency signals.
SGPS feature intricate patterns of conductive traces, pads, and vias, created through advanced lithography, etching, and metallization processes. These patterns facilitate the routing of electrical signals between semiconductor components, ensuring optimal performance and reliability of the integrated circuits.
One of the key advantages of SGPS is their ability to offer superior thermal management, dissipating heat generated by semiconductor devices effectively. This helps to prevent overheating and ensures the longevity of the semiconductor components.
Additionally, SGPS provide protection against environmental factors such as moisture, dust, and mechanical stress, safeguarding the delicate semiconductor devices from damage.
Overall, Glass Package Substrates (SGPS) are essential components in modern semiconductor packaging, enabling the miniaturization, integration, and performance optimization of electronic devices across various industries.
What is a Semiconductor Glass Package Substrate?
A semiconductor glass package substrate is a component used in the packaging of semiconductor devices. It serves as a foundation or substrate upon which various components of the semiconductor device are mounted and interconnected.
These substrates are typically made of glass due to its excellent electrical insulation properties, thermal stability, and compatibility with high-frequency signals. The glass substrate provides a stable platform for mounting semiconductor chips, passive components, and interconnects. It also helps to protect the semiconductor components from environmental factors such as moisture, dust, and mechanical stress.
In addition to providing mechanical support and electrical insulation, semiconductor glass package substrates often feature integrated circuitry, such as wiring traces and vias, to facilitate electrical connections between different components of the semiconductor device.
Overall, semiconductor glass package substrates play a crucial role in the packaging and integration of semiconductor devices, ensuring their reliability, performance, and longevity.
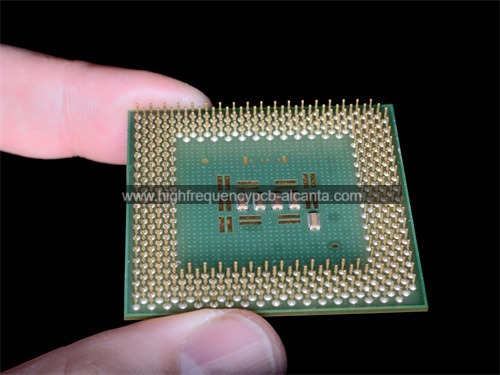
Semiconductor Glass Package Substrates Manufacturer
What are the SGPS Design Guidelines?
Design guidelines for semiconductor glass package substrates (SGPS) typically include various considerations to ensure optimal performance, reliability, and manufacturability of the semiconductor devices. Some common SGPS design guidelines may include:
- Thermal Management:Efficient thermal management is crucial to prevent overheating of semiconductor devices. Design guidelines may specify the use of thermal vias and heat spreaders to dissipate heat effectively from the device to the substrate and surrounding environment.
- Signal Integrity: High-speed semiconductor devices require careful consideration of signal integrity to minimize signal degradation and electromagnetic interference (EMI). Design guidelines may include recommendations for controlled impedance traces, signal routing techniques, and ground/power plane placement to maintain signal integrity.
- Power Distribution: Proper power distribution is essential for stable operation of semiconductor devices. Design guidelines may specify the use of low-impedance power distribution networks, decoupling capacitors, and power plane segmentation to minimize voltage drops and noise.
- Electrical Isolation: Semiconductor devices often require electrical isolation to prevent interference between different components. Design guidelines may include recommendations for isolation barriers, guard rings, and ground plane partitions to minimize crosstalk and leakage currents.
- Manufacturability: Design guidelines should consider manufacturability to ensure cost-effective and reliable production of semiconductor devices. Guidelines may include recommendations for panelization, fiducial markers, solder mask clearance, and minimum feature sizes to facilitate the manufacturing process.
- Reliability and Robustness: SGPS design should prioritize reliability and robustness to ensure the long-term performance of semiconductor devices in various operating conditions. Guidelines may include recommendations for material selection, component placement, and mechanical reinforcement to enhance reliability and durability.
- Environmental Considerations: SGPS design should take into account environmental factors such as temperature fluctuations, humidity, and mechanical stress. Guidelines may include recommendations for conformal coating, hermetic sealing, and environmental testing to ensure the reliability of semiconductor devices in harsh operating environments.
These are just a few examples of design guidelines for semiconductor glass package substrates. The specific guidelines may vary depending on the application, technology node, and manufacturing process used for semiconductor devices.
What is the SGPS Fabrication Process?
The fabrication process for semiconductor glass package substrates (SGPS) involves several steps to create a substrate suitable for mounting semiconductor devices. Here’s a general overview of the typical SGPS fabrication process:
- Substrate Preparation: The process begins with the preparation of the glass substrate. High-quality glass sheets are selected and cleaned to remove any contaminants or impurities that could affect the performance of the semiconductor devices.
- Lithography: Lithography is used to define the pattern of features on the glass substrate. A layer of photoresist is applied to the substrate, and then a mask containing the desired pattern is placed over the photoresist. UV light is then used to transfer the pattern from the mask to the photoresist.
- Etching: After lithography, the exposed areas of the photoresist are removed, leaving behind the patterned photoresist mask. The substrate is then etched using wet or dry etching techniques to transfer the pattern from the photoresist mask to the glass substrate.
- Metallization: Metallization is used to create conductive traces and pads on the substrate for interconnecting semiconductor devices. Thin layers of metal, such as copper or aluminum, are deposited onto the substrate using techniques such as sputtering or evaporation. These metal layers are then patterned using lithography and etching to create the desired conductive features.
- Dielectric Deposition: Dielectric materials, such as silicon dioxide or silicon nitride, are deposited onto the substrate to provide insulation between conductive traces and pads. These dielectric layers help prevent electrical shorts and interference between different components on the substrate.
- Via Formation: Vias are small holes drilled or etched through the dielectric layers to create electrical connections between different metal layers or between the metal layers and the semiconductor devices. Vias are typically formed using laser drilling or dry etching techniques.
- Surface Finishing: After the metallization and dielectric deposition steps, the substrate may undergo surface finishing processes such as planarization or chemical mechanical polishing (CMP) to ensure a smooth and flat surface for mounting semiconductor devices.
- Quality Control and Testing: Throughout the fabrication process, various quality control measures are implemented to ensure the integrity and reliability of the SGPS. Final testing is performed to verify the electrical and mechanical properties of the substrate before it is used for mounting semiconductor devices.
Overall, the SGPS fabrication process involves a combination of lithography, etching, metallization, dielectric deposition, via formation, and surface finishing techniques to create a substrate capable of supporting and interconnecting semiconductor devices.
How do you manufacture an SGPS?
Manufacturing semiconductor glass package substrates (SGPS) involves a series of steps to produce substrates that can host and interconnect semiconductor devices reliably. Here’s a detailed overview of the manufacturing process:
- Substrate Selection: High-quality glass sheets are chosen as the starting material for SGPS manufacturing. The glass should have excellent electrical insulation properties, thermal stability, and compatibility with the subsequent fabrication processes.
- Cleaning and Preparation: The glass sheets undergo thorough cleaning to remove any contaminants or residues that could affect the subsequent processing steps. This typically involves cleaning with solvents, rinsing with deionized water, and drying.
- Lithography: A photoresist material is applied uniformly onto the glass substrate. A mask containing the desired pattern for the SGPS features (such as conductive traces, vias, and pads) is then aligned and placed over the photoresist-coated substrate. UV light is used to expose the photoresist through the mask, defining the pattern.
- Development: The exposed photoresist is chemically removed, leaving behind the desired pattern on the substrate. The unexposed areas of the photoresist remain intact, protecting the underlying glass during subsequent processing steps.
- Etching: The glass substrate is etched using wet or dry etching techniques, depending on the specific requirements of the design. Etching removes the glass material from the areas not protected by the photoresist, defining the features of the SGPS pattern.
- Metallization: Thin layers of metal, such as copper or aluminum, are deposited onto the substrate using techniques like sputtering or evaporation. These metal layers form the conductive traces, pads, and interconnects on the SGPS. A photoresist mask is used to define the metal pattern, followed by etching to remove excess metal.
- Dielectric Deposition: Dielectric materials, such as silicon dioxide or silicon nitride, are deposited onto the substrate to insulate the metal layers and provide electrical isolation. This step typically involves chemical vapor deposition (CVD) or physical vapor deposition (PVD) techniques.
- Via Formation: Vias are created to establish electrical connections between different metal layers or between the metal layers and the semiconductor devices. Vias are formed by drilling or etching through the dielectric layers using techniques like laser ablation or reactive ion etching (RIE).
- Surface Finishing: The substrate undergoes surface finishing processes such as planarization or chemical mechanical polishing (CMP) to ensure a smooth and flat surface for mounting semiconductor devices.
- Quality Control: Throughout the manufacturing process, rigorous quality control measures are implemented to ensure the integrity and reliability of the SGPS. Final testing is performed to verify electrical connectivity, dimensional accuracy, and overall performance.
- Packaging and Assembly:Once manufactured, the SGPS are packaged and assembled with semiconductor devices using techniques such as flip-chip bonding, wire bonding, or soldering.
By following these steps, manufacturers can produce SGPS that meet the stringent requirements of modern semiconductor packaging, ensuring the reliability and performance of electronic devices.
How much should an SGPS cost?
The cost of semiconductor glass package substrates (SGPS) can vary significantly depending on various factors such as:
- Size and Complexity: Larger substrates or substrates with more complex designs requiring intricate features such as fine pitch traces, multiple layers, and high-density interconnects may cost more to manufacture due to increased material and processing requirements.
- Material Quality: The quality of the glass substrate and other materials used in the manufacturing process can impact the cost. High-purity glass and premium-quality metals and dielectrics may incur higher costs compared to lower-grade materials.
- Manufacturing Volume: Economies of scale play a significant role in determining the cost of SGPS. Higher manufacturing volumes typically lead to lower per-unit costs due to spreading fixed costs over a larger production quantity.
- Manufacturing Technology: Advanced manufacturing technologies and equipment used in the fabrication process may require significant initial investment but can lead to cost savings in the long run through improved efficiency, yield, and throughput.
- Customization and Special Features: SGPS customized to specific requirements, such as specialized material compositions, unique geometries, or advanced features like embedded components or sensors, may command higher prices due to additional engineering and development costs.
- Supplier and Location: The choice of supplier and manufacturing location can impact SGPS costs due to differences in labor costs, overhead expenses, taxes, and regulatory compliance.
- Market Demand and Competition: Supply-demand dynamics and competitive pressures within the semiconductor packaging industry can influence SGPS pricing. Prices may fluctuate based on market conditions, technological advancements, and the presence of alternative packaging solutions.
Due to these factors, it’s challenging to provide a precise cost estimate for SGPS without specific details about the design requirements, manufacturing process, and market conditions. However, SGPS costs typically range from a few cents to several dollars per unit, with high-end substrates for advanced applications potentially costing more.
What is an SGPS base material?
The base material for semiconductor glass package substrates (SGPS) is typically a type of glass that possesses specific properties suited for semiconductor packaging applications. These properties include:
- Electrical Insulation: The glass substrate must provide excellent electrical insulation to prevent leakage currents and ensure proper signal integrity in the semiconductor device.
- Thermal Stability:SGPS base materials should have high thermal stability to withstand the operating temperatures encountered during semiconductor device operation without significant deformation or degradation.
- Low Coefficient of Thermal Expansion (CTE): A low CTE is desirable to minimize thermal mismatch between the SGPS and the semiconductor devices mounted on it, reducing the risk of mechanical stress and potential damage.
- Chemical Compatibility: The glass material should be chemically compatible with the other materials used in the fabrication process, such as metals, dielectrics, and adhesives, to ensure good adhesion and reliability.
- Smooth Surface Finish: A smooth surface finish is important for achieving precise lithographic patterning and ensuring good adhesion of subsequent layers during the fabrication process.
- High Transmission Properties: In some cases, especially for optoelectronic devices, the glass substrate may need to have high optical transmission properties to allow light to pass through with minimal absorption or scattering.
Common types of glass used as base materials for SGPS include:
– Borosilicate Glass: Borosilicate glass is known for its low coefficient of thermal expansion, excellent thermal shock resistance, and good chemical durability. It is widely used in semiconductor packaging due to its reliability and suitability for high-temperature applications.
– Aluminosilicate Glass: Aluminosilicate glass offers similar properties to borosilicate glass but may have higher thermal stability and strength, making it suitable for demanding semiconductor packaging requirements.
– Quartz Glass: Quartz glass, also known as fused silica, has exceptional optical and thermal properties, making it suitable for applications requiring high purity and transparency, such as optoelectronic devices.
The choice of SGPS base material depends on the specific requirements of the semiconductor device, including operating conditions, performance specifications, and manufacturing constraints. Different glass formulations may be selected to optimize electrical, thermal, mechanical, or optical properties as needed.
Which companies make emiconductor Glass Package Substrates (SGPS)?
Several companies specialize in the manufacture of Semiconductor Glass Package Substrates (SGPS). Some of the major manufacturers include Corning, Shin-Etsu Chemical, AGC Inc., and Sharp Corporation. These companies have extensive experience and expertise in semiconductor materials and packaging technologies, offering various types and specifications of SGPS products to meet the needs of different applications.
As for our company, we have the capability to produce high-quality Semiconductor Glass Package Substrates (SGPS). We possess advanced manufacturing equipment and technology, focusing on the research and development of innovative materials and processes to meet customer requirements for high performance, reliability, and customization. Our manufacturing process strictly adheres to quality control standards to ensure that our products meet industry and customer requirements.
We have a professional R&D team capable of custom design and development according to specific customer needs. Whether in material selection, process optimization, or product performance, we are committed to providing the best solutions to meet customers’ individual requirements.
Furthermore, we emphasize close cooperation and communication with customers to understand their needs and provide timely technical support and services. We are dedicated to building long-term and stable partnerships, continually improving and enhancing our manufacturing capabilities to meet the evolving needs of the industry and customers.
In summary, as a professional manufacturer, we have the capability to produce high-quality, customized Semiconductor Glass Package Substrates (SGPS), and are committed to providing customers with quality products and services.
What are the 7 qualities of good customer service?
Good customer service is essential for maintaining customer satisfaction and loyalty. Here are seven qualities that characterize good customer service:
- Responsiveness: Good customer service involves being prompt and responsive to customer inquiries, concerns, and requests. Responding in a timely manner demonstrates attentiveness and shows customers that their needs are being taken seriously.
- Empathy: Empathy involves understanding and sharing the feelings of customers, particularly when they are experiencing difficulties or frustrations. Good customer service representatives listen actively, acknowledge customer concerns, and show genuine empathy towards their situation.
- Clarity and Communication Skills: Effective communication is crucial in delivering good customer service. Customer service representatives should be clear, concise, and articulate in their communication, whether it’s explaining product features, addressing issues, or providing instructions.
- Problem-Solving Skills: Good customer service involves the ability to resolve customer issues and problems efficiently and effectively. Customer service representatives should be resourceful, proactive, and adept at finding solutions to customer concerns.
- Professionalism: Professionalism encompasses various aspects of behavior and conduct, including politeness, respectfulness, and integrity. Good customer service representatives maintain a professional demeanor at all times, regardless of the situation, and strive to leave a positive impression on customers.
- Product Knowledge: Having a deep understanding of the products or services being offered is essential for providing good customer service. Customer service representatives should be well-trained and knowledgeable about the company’s offerings, enabling them to address customer inquiries accurately and confidently.
- Follow-Up and Feedback: Following up with customers after resolving their issues or completing a transaction demonstrates commitment to customer satisfaction. Good customer service includes seeking feedback from customers to understand their experiences, identify areas for improvement, and continually enhance the quality of service.
By embodying these qualities, businesses can deliver exceptional customer service experiences that foster loyalty, positive word-of-mouth, and long-term relationships with customers.
FAQs
What is a Semiconductor Glass Package Substrate (SGPS)?
An SGPS is a type of substrate used in semiconductor packaging. It serves as a foundation for mounting and interconnecting semiconductor devices such as chips, providing electrical insulation and thermal management.
What are the advantages of using SGPS?
SGPS offers several advantages, including excellent electrical insulation, thermal stability, compatibility with high-frequency signals, and protection against environmental factors such as moisture and dust.
What materials are used in SGPS?
Common materials used in SGPS include glass substrates (such as borosilicate or aluminosilicate glass), metal layers (typically copper or aluminum), and dielectric materials (such as silicon dioxide or silicon nitride).
What is the fabrication process for SGPS?
The fabrication process for SGPS involves steps such as substrate preparation, lithography, etching, metallization, dielectric deposition, via formation, surface finishing, and quality control/testing.
What are some design considerations for SGPS?
Design considerations for SGPS include thermal management, signal integrity, power distribution, electrical isolation, manufacturability, reliability, and environmental factors.
Which companies manufacture SGPS?
Several companies specialize in the manufacture of SGPS, including Corning, Shin-Etsu Chemical, AGC Inc., and Sharp Corporation, among others.
What are the applications of SGPS?
SGPS are used in a wide range of applications, including integrated circuits (ICs), microelectromechanical systems (MEMS), sensors, optoelectronic devices, and radio frequency (RF) components.