Semiconductor FC BGA Substrate Manufacturer
Semiconductor FC BGA Substrate Manufacturer,Semiconductor FC BGA Substrate is a key component in semiconductor packaging, facilitating direct connections between chips and printed circuit boards (PCBs) using flip chip technology. This substrate supports high-density integration and efficient signal transmission, enhancing the performance of semiconductor devices. Composed of multiple layers including insulating, conductive, and metal layers, Semiconductor FC BGA Substrates ensure reliable electrical connections and effective heat dissipation. They are vital in various industries such as telecommunications, automotive, and consumer electronics, where space-saving and high performance are crucial. These substrates drive advancements in semiconductor packaging, enabling innovation and progress in modern electronic devices.
What is Semiconductor FC BGA Substrate?
A Semiconductor FC BGA (Flip Chip Ball Grid Array) substrate is a type of packaging technology used in semiconductor devices, particularly integrated circuits (ICs) or microchips. This packaging technology is designed to provide electrical connections between the semiconductor chip and the circuit board it is mounted on.
In a Flip Chip BGA configuration, the semiconductor chip is flipped upside down and directly mounted onto the substrate. This allows for shorter electrical connections between the chip and the substrate compared to traditional wire bonding methods, resulting in improved electrical performance and higher speeds.
The substrate itself is typically made of a material with good electrical properties, such as ceramic or laminate, and it contains an array of solder balls or bumps that connect the chip to the external circuitry on the circuit board. These solder balls are arranged in a grid pattern, hence the name “Ball Grid Array.”
Overall, Semiconductor FC BGA substrates are commonly used in high-performance applications where reliability, compactness, and high-speed operation are critical, such as in advanced computing systems, telecommunications equipment, and consumer electronics devices.
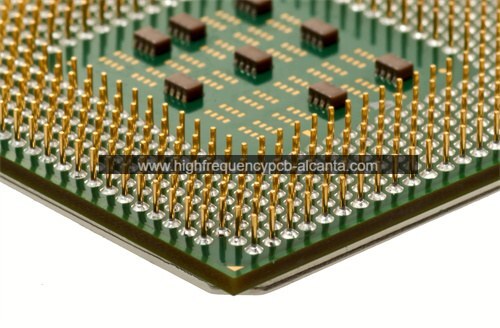
Semiconductor FC BGA substrate Manufacturer
What are the Functions of Semiconductor FC BGA Substrate?
Semiconductor FC BGA (Flip Chip Ball Grid Array) substrates serve several important functions in the packaging and operation of semiconductor devices. These functions include:
Electrical Interconnection: One of the primary functions of the FC BGA substrate is to provide electrical connections between the semiconductor chip and the external circuitry on the printed circuit board (PCB). This allows signals to be transmitted between the chip and other components in the system.
Heat Dissipation: Semiconductor devices generate heat during operation, and effective heat dissipation is essential for maintaining optimal performance and reliability. The FC BGA substrate may incorporate features such as thermal vias, metal layers, and heat spreaders to efficiently dissipate heat away from the chip to the surrounding environment or to a heat sink on the PCB.
Mechanical Support: The FC BGA substrate provides mechanical support for the semiconductor chip, ensuring its stability and protecting it from physical damage during handling, assembly, and operation.
Signal Integrity: The design of the FC BGA substrate plays a crucial role in maintaining signal integrity, minimizing signal degradation, noise, and electromagnetic interference (EMI) during signal transmission between the chip and the external circuitry.
Power Distribution: The substrate distributes power from the PCB to the semiconductor chip and other components as needed, ensuring stable and reliable power supply for proper device operation.
Package Integration: FC BGA substrates facilitate the integration of the semiconductor chip into the overall package design, enabling compact and space-efficient packaging solutions for semiconductor devices.
Reliability Enhancement: By providing a stable electrical and mechanical interface between the semiconductor chip and the PCB, FC BGA substrates contribute to the overall reliability and longevity of semiconductor devices, reducing the risk of failure due to electrical or mechanical stresses.
Overall, the functions of Semiconductor FC BGA substrates are critical for the performance, reliability, and integration of semiconductor devices in a wide range of applications across various industries.
What are the Different Types of Semiconductor FC BGA Substrate?
There are several different types of Semiconductor FC BGA (Flip Chip Ball Grid Array) substrates, each designed to meet specific requirements and performance criteria. Some common types include:
Ceramic Substrates: These substrates are made of ceramic materials such as alumina (Al2O3) or aluminum nitride (AlN). Ceramic substrates offer excellent thermal conductivity, mechanical strength, and reliability, making them suitable for high-power and high-frequency applications.
Organic Substrates: Organic substrates are typically made of materials such as epoxy-based laminates or polyimide films. They are lightweight, cost-effective, and offer good electrical performance for medium to high-speed applications. However, organic substrates have lower thermal conductivity compared to ceramics.
Flexible Substrates: Flexible substrates are made of thin, flexible materials such as polyimide or polyester films. They are suitable for applications requiring bendable or conformal packaging solutions, such as wearable electronics or flexible displays.
Metal Core Substrates: Metal core substrates incorporate a metallic core layer, typically made of aluminum or copper, sandwiched between layers of dielectric material. Metal core substrates offer enhanced thermal conductivity compared to organic substrates, making them suitable for high-power applications where efficient heat dissipation is critical.
Embedded Substrates: Embedded substrates feature embedded passive components such as resistors, capacitors, or inductors within the substrate material. This integration of passive components can reduce the overall footprint and complexity of the package, while also improving electrical performance and reliability.
High-Density Interconnect (HDI) Substrates: HDI substrates utilize advanced fabrication techniques to achieve very fine pitch interconnects, allowing for higher density and integration of components on the substrate. HDI substrates are commonly used in high-performance computing and telecommunications applications.
Stacked Substrates: Stacked substrates consist of multiple substrate layers stacked on top of each other, interconnected using through-silicon vias (TSVs) or other advanced packaging technologies. Stacked substrates enable increased functionality and integration within a compact form factor, suitable for applications requiring high performance and miniaturization.
These are some of the main types of Semiconductor FC BGA substrates, each offering unique advantages and capabilities to meet the diverse requirements of semiconductor packaging in various industries and applications.
How does Semiconductor FC BGA Substrate Relate to IC Packaging?
Semiconductor FC BGA (Flip Chip Ball Grid Array) substrates are a crucial component in the realm of IC (Integrated Circuit) packaging. IC packaging involves enclosing semiconductor chips within protective casings and providing electrical connections to the external circuitry. The FC BGA substrate plays a significant role in this process, particularly in flip chip packaging configurations.
Here’s how Semiconductor FC BGA substrates relate to IC packaging:
Electrical Interconnection: FC BGA substrates facilitate electrical connections between the semiconductor chip and the external circuitry on the printed circuit board (PCB). The flip chip configuration allows for direct connection of the chip’s bond pads to the substrate’s solder balls or bumps, enabling efficient signal transmission.
Mechanical Support: FC BGA substrates provide mechanical support for the semiconductor chip, ensuring its stability and protecting it from physical damage during handling, assembly, and operation. This mechanical support is essential for maintaining the integrity of the chip and preventing reliability issues.
Heat Dissipation: Efficient heat dissipation is crucial for maintaining the performance and reliability of semiconductor devices. FC BGA substrates may incorporate features such as thermal vias, metal layers, and heat spreaders to dissipate heat generated by the chip during operation, thereby preventing overheating and ensuring optimal performance.
Package Integration: FC BGA substrates facilitate the integration of the semiconductor chip into the overall package design. They allow for compact and space-efficient packaging solutions, enabling the development of smaller and more portable electronic devices without sacrificing performance or reliability.
Signal Integrity: The design of FC BGA substrates plays a critical role in maintaining signal integrity during signal transmission between the chip and the external circuitry. By minimizing signal degradation, noise, and electromagnetic interference (EMI), FC BGA substrates help ensure reliable communication between components within the IC package.
Reliability Enhancement: FC BGA substrates contribute to the overall reliability and longevity of semiconductor devices by providing a stable electrical and mechanical interface between the chip and the PCB. This reduces the risk of failure due to electrical or mechanical stresses, thereby improving the reliability of the packaged IC.
In summary, Semiconductor FC BGA substrates are an integral part of IC packaging, enabling efficient electrical interconnection, mechanical support, heat dissipation, package integration, signal integrity, and reliability enhancement in semiconductor devices. They play a vital role in ensuring the performance, reliability, and functionality of packaged ICs across various applications and industries.
What are the Differences Between Semiconductor FC BGA Substrate and PCB?
Semiconductor FC BGA substrates and PCBs (Printed Circuit Boards) are both crucial components in electronic systems, but they serve different purposes and exhibit distinct characteristics. Here are the key differences between Semiconductor FC BGA substrates and PCBs:
Function:
Semiconductor FC BGA Substrate: The primary function of FC BGA substrates is to provide electrical connections between the semiconductor chip and the external circuitry on the PCB. They also offer mechanical support, heat dissipation, and signal integrity enhancement specifically tailored for semiconductor devices.
PCB: PCBs are used to mechanically support and electrically connect various electronic components, including integrated circuits, resistors, capacitors, and connectors. They serve as the backbone of electronic systems, providing a platform for interconnecting and mounting components.
Material:
Semiconductor FC BGA Substrate: FC BGA substrates are typically made of materials optimized for the performance and reliability of semiconductor devices, such as ceramics (e.g., alumina or aluminum nitride), organic substrates (e.g., epoxy-based laminates or polyimide films), or metal core substrates.
PCB: PCBs are commonly made of fiberglass-reinforced epoxy laminate known as FR-4, which offers a balance of electrical insulation, mechanical strength, and cost-effectiveness. Other materials such as polyimide, ceramics, or metal core laminates may also be used for specialized applications.
Design and Layout:
Semiconductor FC BGA Substrate: FC BGA substrates are typically designed with high-density interconnects and specific layout configurations optimized for semiconductor packaging, such as flip chip bonding, thermal vias, and embedded passives.
PCB: PCBs feature a variety of layout designs tailored to the specific requirements of the electronic system they are part of. They incorporate traces, vias, and pads arranged in a specific pattern to route signals between components and provide power and ground connections.
Integration:
Semiconductor FC BGA Substrate: FC BGA substrates are integrated into semiconductor packages as a critical component of the overall packaging solution. They are designed to directly interface with semiconductor chips and provide essential functions tailored for semiconductor devices.
PCB: PCBs are integrated into electronic systems to provide a platform for mounting and interconnecting various components, including semiconductor devices, passive components, and connectors. They serve as the foundation for building complex electronic systems.
Application:
Semiconductor FC BGA Substrate: FC BGA substrates are primarily used in semiconductor packaging applications, where high-performance, reliability, and miniaturization are critical, such as in microprocessors, memory modules, and high-speed communication devices.
PCB: PCBs are used in a wide range of electronic devices and systems across various industries, including consumer electronics, telecommunications, automotive, aerospace, and medical devices.
In summary, while both Semiconductor FC BGA substrates and PCBs are essential components in electronic systems, they have distinct functions, materials, designs, integration methods, and applications tailored to their specific roles in electronic packaging and interconnection.
What are the Main Structures and Production Technologies of Semiconductor FC BGA Substrate?
The main structures and production technologies of Semiconductor FC BGA (Flip Chip Ball Grid Array) substrates can vary depending on the specific requirements of the semiconductor device and the desired performance characteristics. However, here are some common structures and production technologies used in the manufacturing of FC BGA substrates:
Structure:
Base Material: The substrate typically consists of a base material, which can be ceramic (e.g., alumina or aluminum nitride), organic (e.g., epoxy-based laminates or polyimide films), metal core (e.g., aluminum or copper), or a combination of these materials.
Metal Layers: Metal layers are deposited or laminated onto the substrate to form conductive traces, pads, and interconnects for routing signals and providing electrical connections between the semiconductor chip and the external circuitry.
Solder Balls or Bumps: Solder balls or bumps are attached to the substrate to provide electrical connections between the semiconductor chip and the PCB. These solder balls are typically arranged in a grid pattern and are made of materials such as lead-free solder alloys (e.g., SAC alloy) or gold (for high-reliability applications).
Passive Components (optional): In some cases, passive components such as resistors, capacitors, or inductors may be embedded within the substrate to reduce the overall footprint and complexity of the package and improve electrical performance.
Production Technologies:
Circuit Formation: The formation of circuit patterns on the substrate typically involves processes such as photolithography, etching, and metal deposition. Photolithography is used to define the circuit patterns on the substrate, while etching is used to remove unwanted material, leaving behind the desired conductive traces and pads. Metal deposition techniques such as sputtering or electroplating are used to deposit metal layers onto the substrate.
Solder Ball Attachment: Solder balls or bumps are attached to the substrate using techniques such as solder ball placement, reflow soldering, or solder jetting. These techniques involve depositing solder paste or preformed solder balls onto the substrate and then heating them to reflow and form the solder joints.
Embedding Passive Components (optional): If passive components are embedded within the substrate, processes such as laser drilling, laser ablation, or screen printing may be used to create cavities or trenches in the substrate for component placement. The components are then placed and bonded using techniques such as soldering or conductive adhesive bonding.
Surface Finish: The surface of the substrate may undergo surface finishing processes such as immersion tin, immersion silver, or gold plating to improve solderability and ensure reliable solder joint formation during assembly.
Overall, the production of Semiconductor FC BGA substrates involves a combination of advanced manufacturing processes, including circuit formation, solder ball attachment, passive component embedding (if required), and surface finishing, tailored to meet the specific requirements of semiconductor packaging applications. These technologies enable the production of high-performance, reliable, and compact packaging solutions for semiconductor devices.
Frequently Asked Questions (FAQs)
What is a Semiconductor FC BGA substrate?
A Semiconductor FC BGA (Flip Chip Ball Grid Array) substrate is a type of packaging technology used in semiconductor devices, particularly integrated circuits (ICs) or microchips. It provides electrical connections between the semiconductor chip and the circuit board it is mounted on, along with other functions such as mechanical support and heat dissipation.
What are the functions of Semiconductor FC BGA substrates?
Semiconductor FC BGA substrates serve several functions, including electrical interconnection between the chip and external circuitry, heat dissipation, mechanical support, signal integrity maintenance, power distribution, package integration, and reliability enhancement.
What are the different types of Semiconductor FC BGA substrates?
Common types of Semiconductor FC BGA substrates include ceramic substrates, organic substrates, flexible substrates, metal core substrates, embedded substrates, high-density interconnect (HDI) substrates, and stacked substrates. Each type offers unique advantages and capabilities to meet specific requirements.
How does Semiconductor FC BGA substrate relate to IC packaging?
Semiconductor FC BGA substrates are integral to IC packaging, facilitating electrical interconnection, mechanical support, heat dissipation, signal integrity maintenance, package integration, and reliability enhancement for semiconductor devices within the overall package design.
What are the differences between Semiconductor FC BGA substrates and PCBs?
Semiconductor FC BGA substrates are specifically designed for semiconductor packaging applications, providing optimized electrical and mechanical properties for semiconductor devices. PCBs, on the other hand, serve as general-purpose platforms for interconnecting various electronic components in electronic systems.
What are the main structures and production technologies of Semiconductor FC BGA substrates?
The main structures of Semiconductor FC BGA substrates may include layers of dielectric material, conductive traces, solder balls or bumps, thermal vias, and embedded passive components. Production technologies may involve processes such as substrate fabrication, circuit patterning, metallization, assembly, and testing.
Conclusion
In conclusion, Semiconductor FC BGA (Flip Chip Ball Grid Array) substrates are essential components in the packaging of semiconductor devices, providing crucial functions such as electrical interconnection, mechanical support, heat dissipation, signal integrity maintenance, and reliability enhancement. These substrates come in various types, including ceramic, organic, flexible, metal core, embedded, HDI, and stacked substrates, each offering unique advantages for specific applications. Semiconductor FC BGA substrates play a vital role in IC packaging by facilitating the integration and performance of semiconductor devices within electronic systems. Understanding the functions, types, relationships, and production technologies of Semiconductor FC BGA substrates is key to their effective utilization in various industries and applications.