RT5880 PCB Manufacturing
RT5880 PCB Manufacturing,RT5880 PCBs, constructed using RT/duroid® 5880 laminate material, represent the pinnacle of high-frequency printed circuit board technology. Renowned for their exceptional electrical properties, RT5880 PCBs offer a low dielectric constant, minimal signal loss, and stable performance across a broad frequency spectrum. Ideal for RF (radio frequency) and microwave applications, these PCBs ensure reliable signal integrity and enhanced performance in wireless communication systems, radar systems, satellite communications, and RF amplifiers. Their temperature stability and robust mechanical strength further underscore their suitability for demanding environments. With precise impedance control, meticulous layer stackup design, and advanced manufacturing techniques, RT5880 PCBs meet the stringent requirements of high-frequency electronic circuits. Whether it’s for prototyping or production, RT5880 PCBs cater to the needs of industries requiring cutting-edge solutions for high-frequency applications, delivering unparalleled performance and reliability.
What is a RT5880 PCB?
RT5880 PCB likely refers to a type of printed circuit board (PCB) designed for use with RT5880, which is a type of high-frequency material or substrate used in RF (radio frequency) and microwave applications. RT5880 is a type of laminate material commonly used in the construction of RF and microwave circuits due to its excellent electrical properties at high frequencies.
PCBs made using RT5880 material are often used in applications such as wireless communication systems, radar systems, satellite communications, and other high-frequency electronic devices where signal integrity and minimal signal loss are critical.
These PCBs are designed to provide optimal performance for circuits operating at high frequencies, typically in the gigahertz (GHz) range. They are manufactured using specialized processes to ensure precise impedance control, low signal loss, and minimal interference.
Overall, RT5880 PCBs are tailored for high-frequency applications where maintaining signal integrity and minimizing losses are paramount.
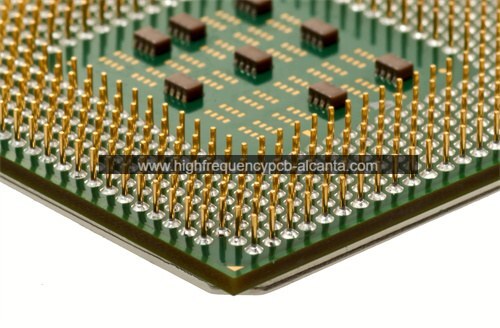
RT5880 PCB Manufacturing
What are the RT5880 PCB Design Guidelines?
The RT5880 PCB design guidelines typically include recommendations and best practices for designing printed circuit boards (PCBs) using RT5880 material to ensure optimal performance, signal integrity, and reliability. Here are some common guidelines:
- Impedance Control: RT5880 material has a specific dielectric constant (εr) and thickness. Maintaining controlled impedance traces on the PCB is crucial for proper signal transmission. Design guidelines usually specify trace width, spacing, and layer stackup to achieve the desired impedance.
- Layer Stackup: Designing the PCB with the appropriate layer stackup helps control impedance, minimize signal losses, and provide sufficient isolation between signal layers and ground/power planes. Guidelines often recommend a specific layer configuration to meet the requirements of the RF or microwave circuit.
- Transmission Line Design: Proper design of transmission lines, such as microstrips or coplanar waveguides, is essential for RF and microwave circuits. Guidelines cover parameters like trace width, spacing, and termination to ensure impedance matching and signal integrity.
- Component Placement: Strategic placement of components on the PCB can minimize signal distortion, crosstalk, and interference. Design guidelines provide recommendations for placing RF components, connectors, and critical signal traces to optimize performance.
- Grounding: Establishing a solid ground plane is vital for RF and microwave circuits to minimize noise and provide a reference for signal return paths. Guidelines often include recommendations for ground plane continuity, via placement, and minimizing ground loops.
- Signal Integrity Analysis: Conducting signal integrity simulations and analysis using software tools like electromagnetic field solvers can help validate the PCB design and identify potential issues such as reflections, impedance mismatches, or EMI problems.
- Thermal Management: Proper thermal management is essential, especially for high-power RF applications. Guidelines may include recommendations for heat sinking, thermal vias, and PCB layout to dissipate heat effectively and prevent overheating of components.
- Manufacturing Considerations: Design guidelines should also consider manufacturing constraints and capabilities to ensure the PCB can be fabricated reliably and cost-effectively. This may include aspects like minimum feature size, panelization, and material handling requirements.
These guidelines serve as a foundation for designing RT5880 PCBs for RF and microwave applications, helping engineers achieve optimal performance and reliability in their designs. However, it’s essential to consult the specific datasheets, application notes, and design resources provided by the material manufacturer for detailed guidance tailored to RT5880.
What is the RT5880 PCB Fabrication Process?
The fabrication process for RT5880 PCBs involves several steps to create the printed circuit board using RT5880 material. Here’s a general overview of the process:
- Design Preparation: Before fabrication begins, the PCB design is prepared using PCB design software. This includes creating the PCB layout, defining the layer stackup, routing signal traces, placing components, and ensuring adherence to design guidelines for RT5880 material.
- Material Selection: RT5880 laminate material is chosen for the PCB based on its high-frequency performance requirements. The material is typically available in various thicknesses and copper foil options.
- Layer Stackup Design: The layer stackup is determined based on the specific requirements of the PCB design and the characteristics of RT5880 material. The stackup defines the arrangement of copper layers, dielectric layers, and any additional prepreg layers.
- Preparation of Substrate Material: The RT5880 laminate material is prepared for PCB fabrication by cutting it to the required size and cleaning it to remove any contaminants that could affect the adhesion of copper foil.
- Copper Cladding: Copper foil is bonded to both sides of the RT5880 substrate material using a lamination process. The copper foil thickness is chosen based on the specific requirements of the PCB design, such as impedance control and current carrying capacity.
- Circuit Patterning: The desired circuit pattern is transferred onto the copper foil using a process called photolithography. A photoresist material is applied to the copper surface, exposed to UV light through a photomask, and developed to create the circuit pattern.
- Etching: The unmasked copper areas are removed from the substrate using an etching solution, leaving behind the desired circuit traces and pads. The etching process is typically controlled to ensure precise trace widths and geometries.
- Drilling: Precision holes are drilled through the PCB at locations specified by the design, such as for component mounting holes and vias. Advanced drilling techniques may be employed to ensure accuracy and reliability, especially for high-frequency applications.
- Plating: Through-hole vias and plated through-holes (PTHs) are electroplated with copper to provide electrical connectivity between layers and to reinforce mechanical strength.
- Surface Finish: The exposed copper surfaces are coated with a surface finish to protect them from oxidation and facilitate soldering during assembly. Common surface finishes for RT5880 PCBs include immersion gold, immersion silver, or immersion tin.
- Final Inspection: The finished PCBs undergo thorough inspection to ensure they meet the design specifications and quality standards. This may include electrical testing, dimensional measurements, and visual inspection of circuit traces and features.
- Panelization and Singulation: Multiple PCBs may be fabricated on a single panel to improve efficiency during manufacturing. After fabrication, the panel is singulated into individual PCBs using routing or mechanical separation methods.
Overall, the RT5880 PCB fabrication process involves precise steps to create high-quality printed circuit boards tailored for high-frequency RF and microwave applications. Each step is critical to ensuring the performance, reliability, and functionality of the final PCB product.
How do you manufacture a RT5880 PCB?
Manufacturing an RT5880 PCB involves several steps, including material preparation, layer stackup design, circuit patterning, etching, drilling, plating, surface finishing, and final inspection. Here’s a more detailed breakdown of the manufacturing process:
- Design Preparation: Begin by preparing the PCB design using appropriate PCB design software. Ensure that the design adheres to the specifications and guidelines for RT5880 material, including impedance control, layer stackup, and trace routing.
- Material Selection: Choose RT5880 laminate material suitable for high-frequency applications. Determine the thickness and copper foil options based on the specific requirements of your design.
- Layer Stackup Design: Design the layer stackup considering factors such as signal integrity, impedance control, and manufacturing constraints. Define the arrangement of copper layers, dielectric layers, and any additional prepreg layers.
- Substrate Preparation: Cut the RT5880 laminate material to the required size for the PCB. Clean the substrate to remove any contaminants that could affect the adhesion of copper foil.
- Copper Cladding: Bond copper foil to both sides of the RT5880 substrate using a lamination process. Ensure proper adhesion and alignment of the copper foil to the substrate.
- Circuit Patterning: Apply a layer of photoresist material onto the copper surface. Expose the photoresist to UV light through a photomask to transfer the desired circuit pattern. Develop the photoresist to reveal the patterned copper areas.
- Etching: Remove the unwanted copper from the substrate using an etching solution. Control the etching process to achieve precise trace widths and geometries according to the design specifications.
- Drilling: Drill precision holes through the PCB at locations specified by the design, such as for component mounting holes and vias. Ensure accuracy and alignment of the drill holes.
- Plating: Electroplate the through-hole vias and plated through-holes (PTHs) with copper to provide electrical connectivity between layers and reinforce mechanical strength.
- Surface Finish: Apply a surface finish to the exposed copper surfaces to protect them from oxidation and facilitate soldering during assembly. Common surface finishes for RT5880 PCBs include immersion gold, immersion silver, or immersion tin.
- Final Inspection: Inspect the finished PCBs thoroughly to ensure they meet the design specifications and quality standards. Perform electrical testing, dimensional measurements, and visual inspection of circuit traces and features.
- Panelization and Singulation: Fabricate multiple PCBs on a single panel to improve manufacturing efficiency. After fabrication, separate the individual PCBs from the panel using routing or mechanical separation methods.
Throughout the manufacturing process, adhere to best practices for handling RT5880 material and follow any specific guidelines provided by the material manufacturer. Quality control measures should be implemented at each stage to ensure the reliability and performance of the final RT5880 PCBs.
How much should a RT5880 PCB cost?
The cost of an RT5880 PCB can vary significantly depending on various factors such as size, complexity, layer count, material specifications, surface finish, quantity, and additional services required. However, to provide a rough estimate, let’s consider some typical price ranges:
- Prototype or Small Quantity Orders: For low-volume orders or prototype PCBs, the cost per square inch can range from $5 to $20 or more, depending on the complexity of the design and the specific requirements of the RT5880 material.
- Medium Volume Orders: For medium-volume orders, where quantities range from a few dozen to a few hundred PCBs, the cost per square inch may decrease slightly. Prices could range from $3 to $15 per square inch, again depending on various factors.
- High Volume Orders: High-volume orders typically offer economies of scale, resulting in lower unit costs. Prices for large quantities (thousands of units or more) may range from $1 to $8 per square inch, depending on the specifics of the order and negotiations with the PCB manufacturer.
- Additional Costs: Keep in mind that additional costs may apply for services such as expedited manufacturing, special material requirements, impedance control, surface finishes, panelization, and assembly services. These factors can add to the overall cost of the RT5880 PCB.
It’s essential to obtain quotes from multiple PCB manufacturers to compare prices and ensure you’re getting a competitive rate for your specific requirements. Additionally, consider the quality, reliability, and lead times offered by different suppliers when making your decision.
Remember that these are rough estimates, and actual prices may vary based on the specific details of your RT5880 PCB project and the prevailing market conditions.
What is RT5880 PCB base material?
RT5880 PCBs are constructed using a base material known as RT/duroid® 5880. RT/duroid® 5880 is a high-frequency laminate material specifically designed for use in RF (radio frequency) and microwave applications. It belongs to the family of polytetrafluoroethylene (PTFE)-based materials and is manufactured by Rogers Corporation, a leading supplier of advanced materials for electronic applications.
RT/duroid® 5880 offers excellent electrical properties, mechanical stability, and dimensional stability at high frequencies. Its key characteristics include:
- Low Dielectric Constant (εr): RT/duroid® 5880 has a low dielectric constant, typically around 2.20, which helps minimize signal loss and maintain signal integrity in high-frequency circuits.
- Stable Electrical Performance: The material exhibits stable electrical properties over a wide range of frequencies, making it suitable for applications requiring consistent performance across various RF and microwave bands.
- Low Loss Tangent (Dissipation Factor): RT/duroid® 5880 has a low loss tangent, indicating minimal energy loss during signal transmission. This property is crucial for maintaining high signal quality and efficiency in RF and microwave circuits.
- Temperature Stability: The material offers excellent temperature stability, ensuring consistent performance over a wide temperature range. This characteristic is essential for applications operating in harsh environmental conditions.
- Mechanical Strength: RT/duroid® 5880 has good mechanical strength and dimensional stability, making it suitable for fabrication processes such as drilling, routing, and handling during PCB manufacturing.
- Compatibility with Lead-free Assembly: The material is compatible with lead-free soldering processes, facilitating assembly and ensuring compliance with environmental regulations.
Overall, RT/duroid® 5880 is a high-performance laminate material specifically engineered for demanding RF and microwave applications. Its combination of low dielectric constant, low loss tangent, and temperature stability makes it well-suited for use in high-frequency PCBs where signal integrity and performance are critical.
Which company makes RT5880 PCB? (with a note that your company can produce RT5880 PCBs)
RT5880 PCBs are produced by Rogers Corporation. Rogers Corporation is a well-known electronic materials supplier dedicated to providing advanced material solutions for various applications. Their RT/duroid® series of products, including RT/duroid® 5880, are high-frequency laminate materials specifically designed for RF (radio frequency) and microwave applications.
RT/duroid® 5880 features excellent electrical performance, mechanical stability, and temperature stability, making it suitable for a variety of high-frequency circuit designs. Its low dielectric constant, low loss tangent, and stable temperature characteristics make it an ideal choice for manufacturing high-performance RF and microwave circuits.
As a professional electronic manufacturing service provider, our company has advanced production equipment and experienced engineering teams to provide RT5880 PCB manufacturing services. Our manufacturing process strictly adheres to industry standards, and we can customize RT5880 PCBs in different sizes, layer counts, and surface finishes according to specific customer requirements. We prioritize quality control to ensure that the produced PCBs meet design specifications and offer competitive prices and timely delivery.
Whether it’s a sample order or mass production, we can meet customer needs and provide professional technical support and excellent after-sales service. Choosing our company as your manufacturing partner, you can confidently obtain high-quality, reliable RT5880 PCB products.
What are the 7 qualities of good customer service?
Good customer service is essential for building positive relationships with customers and fostering loyalty to a business. Here are seven qualities that characterize good customer service:
- Responsiveness: Good customer service involves promptly addressing customer inquiries, concerns, and requests. Responsiveness demonstrates that the business values the customer’s time and is committed to providing timely assistance.
- Empathy: Empathy is the ability to understand and share the feelings of others. Good customer service representatives demonstrate empathy by actively listening to customers, acknowledging their concerns, and showing genuine care and concern for their needs.
- Clear Communication: Effective communication is crucial in customer service interactions. Clear and concise communication helps ensure that customers understand the information provided and feel confident in the assistance they receive. Customer service representatives should communicate in a friendly and professional manner, using language that is easy to understand.
- Problem-Solving Skills: Good customer service involves effectively resolving customer issues and concerns. Customer service representatives should be equipped with problem-solving skills to identify the root cause of problems, offer appropriate solutions, and follow through to ensure customer satisfaction.
- Positive Attitude: A positive attitude can significantly impact customer interactions. Customer service representatives should maintain a positive and upbeat demeanor, even in challenging situations. A positive attitude helps create a welcoming and enjoyable experience for customers and can help diffuse tense situations.
- Knowledgeability: Customers expect customer service representatives to be knowledgeable about products, services, policies, and procedures. Good customer service involves providing accurate and helpful information to address customer inquiries and assist with their needs. Continuous training and development are essential for ensuring that customer service representatives stay updated on relevant information.
- Follow-Up: Good customer service doesn’t end with the resolution of a customer’s issue. Following up with customers to ensure their satisfaction and address any lingering concerns demonstrates a commitment to customer care. Following up also provides an opportunity to gather feedback and make improvements to the customer service process.
By embodying these qualities, businesses can deliver exceptional customer service experiences that leave a lasting positive impression on customers and contribute to long-term success.
FAQs
What is RT5880 PCB?
RT5880 PCB refers to a printed circuit board constructed using RT/duroid® 5880 laminate material. RT/duroid® 5880 is a high-frequency laminate material designed for RF (radio frequency) and microwave applications due to its excellent electrical properties at high frequencies.
What are the key features of RT5880 PCB?
RT5880 PCBs offer low dielectric constant, low loss tangent, stable electrical performance over a wide range of frequencies, temperature stability, and good mechanical strength. These properties make them ideal for high-frequency RF and microwave circuits.
What are the applications of RT5880 PCB?
RT5880 PCBs are commonly used in various high-frequency electronic applications, including wireless communication systems, radar systems, satellite communications, RF amplifiers, microwave circuits, and more.
What are the advantages of using RT5880 PCB?
The advantages of using RT5880 PCB include reduced signal loss, improved signal integrity, enhanced performance at high frequencies, temperature stability, and reliable mechanical properties.
What design considerations should be taken into account for RT5880 PCB?
Design considerations for RT5880 PCBs include impedance control, layer stackup design, transmission line design, component placement for signal integrity, grounding techniques, thermal management, and adherence to manufacturer specifications and guidelines.
How are RT5880 PCBs manufactured?
RT5880 PCBs are manufactured using a process that involves material preparation, layer stackup design, circuit patterning, etching, drilling, plating, surface finishing, and final inspection. The fabrication process ensures precise control of impedance, signal integrity, and quality.
Where can I find RT5880 PCB fabrication services?
RT5880 PCB fabrication services are offered by various PCB manufacturers and electronic manufacturing service (EMS) providers. Companies specializing in high-frequency PCB fabrication and assembly can produce RT5880 PCBs according to custom requirements and specifications.