RT/duroid® 5880 Laminates PCB manufacturing
RT/duroid® 5880 Laminates PCB Manufacturing,RT/duroid® 5880 Laminates is a high-performance PCB (Printed Circuit Board) material with outstanding electrical properties and reliability. This advanced composite material utilizes a polytetrafluoroethylene
(PTFE) substrate combined with glass fiber reinforcement layers, providing excellent mechanical strength and thermal stability. Its low loss and low dielectric constant characteristics make it an ideal choice for high-frequency applications, especially in microwave and millimeter-wave frequencies. One of the key features of RT/duroid® 5880 Laminates is its exceptional chemical stability, maintaining performance integrity even under harsh environmental conditions. It also exhibits excellent flame retardancy, meeting the UL 94 V-0 standard, ensuring reliable safety for electronic devices. Additionally, its surface flatness and uniformity make it suitable for high-precision processing and packaging requirements, offering greater flexibility and reliability in the design and manufacture of electronic products.
What is RT/duroid® 5880 Laminates?
RT/duroid® 5880 is a high-performance, PTFE-based composite material used in microwave and RF applications. It’s a type of laminate known for its excellent electrical properties, stability, and reliability at high frequencies. This material is often used in the construction of high-frequency circuit boards, antennas, radar systems, and other telecommunications equipment where maintaining signal integrity is crucial.
The key characteristics of RT/duroid® 5880 include low dielectric constant and loss tangent, which help minimize signal loss and maintain signal integrity at high frequencies. It also has a tightly controlled thickness tolerance and consistent electrical properties across a range of frequencies, making it suitable for demanding RF and microwave applications.
Overall, RT/duroid® 5880 laminates are valued for their high performance, reliability, and consistency, making them a popular choice in the design and manufacturing of advanced RF and microwave circuits.
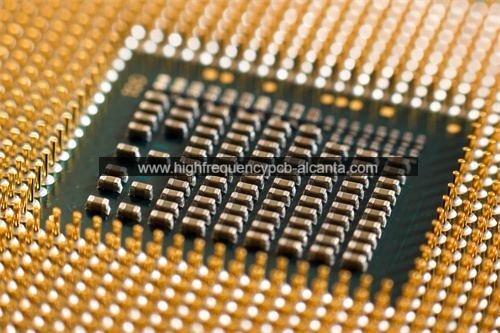
RT/duroid® 5880 Laminates PCB Manufacturing
What are the RT/duroid® 5880 Laminates Design Guidelines?
Design guidelines for RT/duroid® 5880 laminates typically focus on ensuring optimal performance and reliability of high-frequency circuits. Here are some common design guidelines:
- Material Properties: Understand the electrical properties of RT/duroid® 5880, including its dielectric constant (εr), loss tangent (tan δ), and thermal conductivity. These properties are crucial for accurate design and simulation of high-frequency circuits.
- Transmission Line Design: When designing transmission lines (microstrip, stripline, or coplanar waveguide) on RT/duroid® 5880, ensure proper dimensions to achieve the desired characteristic impedance (Z0). Use simulation tools to verify impedance matching and signal integrity.
- Grounding: Proper grounding is essential for minimizing signal losses and maintaining signal integrity. Ensure solid and continuous ground planes beneath signal traces to reduce ground impedance and minimize electromagnetic interference (EMI).
- Component Placement: Carefully place components on the PCB to minimize signal path lengths, reduce parasitic effects, and optimize signal integrity. Pay attention to routing and avoid sharp bends or discontinuities in signal traces.
- Via Design: Use high-quality vias with minimal impedance discontinuities. Properly design vias to maintain signal integrity and minimize signal loss, especially at high frequencies.
- Thermal Management: Consider thermal management techniques to dissipate heat efficiently, especially in high-power applications. Ensure adequate thermal vias and proper heat sinking for components that generate heat.
- Manufacturing Considerations: Communicate with your PCB manufacturer to ensure they have experience working with RT/duroid® 5880 laminates. Provide detailed fabrication notes and specifications to ensure the PCBs are manufactured to the required tolerances and quality standards.
- Testing and Validation: Perform thorough testing and validation of the designed circuits using appropriate RF test equipment. Measure key parameters such as insertion loss, return loss, and impedance matching to verify performance against design specifications.
By following these design guidelines, engineers can maximize the performance and reliability of high-frequency circuits using RT/duroid® 5880 laminates.
What is the RT/duroid® 5880 Laminates Fabrication Process?
The fabrication process for RT/duroid® 5880 laminates involves several steps to create high-quality printed circuit boards (PCBs) suitable for high-frequency applications. While specific processes may vary slightly depending on the manufacturer and requirements of the PCB design, the general fabrication process typically includes the following steps:
- Material Preparation: The process begins with the preparation of RT/duroid® 5880 laminate sheets. These sheets are typically made of woven fiberglass cloth impregnated with PTFE (polytetrafluoroethylene) resin. The resin content and thickness of the laminate sheets are tightly controlled to ensure consistent electrical properties.
- Prepreg Application: Prepreg, a partially cured epoxy resin, is often applied to the surfaces of the RT/duroid® 5880 laminate sheets. Prepreg helps bond multiple layers of laminate together during the lamination process that follows.
- Layer Stacking: Multiple layers of prepreg-coated RT/duroid® 5880 laminate sheets are stacked together along with conductive copper foil layers. The copper foil is typically etched to create the desired circuit patterns and traces.
- Lamination: The stacked layers undergo lamination under high temperature and pressure to bond them together into a single rigid panel. This process ensures proper adhesion between the layers and eliminates air voids, which could affect electrical performance.
- Drilling: Precision drilling machines are used to drill holes for through-hole components and vias. These holes are plated with conductive material to establish electrical connections between different layers of the PCB.
- Copper Etching: Chemical etching processes remove excess copper from the surface of the laminate, leaving behind the desired circuit traces and patterns. Etching is carefully controlled to achieve the desired trace widths and spacing.
- Surface Finish: Surface finish techniques such as immersion gold, immersion silver, or OSP (organic solderability preservatives) may be applied to protect exposed copper surfaces and facilitate soldering of components.
- Final Inspection: The fabricated PCBs undergo thorough inspection to ensure they meet quality standards and specifications. This may include visual inspection, dimensional measurement, electrical testing, and other quality checks.
- Routing and Profiling: Individual PCBs are routed or milled from the larger panel and then profiled to their final dimensions. This step ensures that each PCB is separated and ready for assembly.
- Final Testing: PCBs may undergo final electrical testing to verify their performance and functionality before they are shipped to customers.
Throughout the fabrication process, strict quality control measures are implemented to ensure that the RT/duroid® 5880 laminates meet the required electrical and mechanical specifications for high-frequency applications.
How do you manufacture RT/duroid® 5880 Laminates PCBs?
Manufacturing PCBs using RT/duroid® 5880 laminates involves similar processes to those used for standard PCB fabrication, with some specific considerations due to the material’s properties and requirements for high-frequency applications. Here’s an overview of the manufacturing process for RT/duroid® 5880 laminates PCBs:
- Material Selection: Choose RT/duroid® 5880 laminates with the appropriate thickness and dielectric properties for the intended application. These laminates typically come in standard sheet sizes, which may need to be cut to the desired dimensions for PCB fabrication.
- Preparation of Substrate: Clean the RT/duroid® 5880 laminate sheets to remove any contaminants or residues that could affect adhesion or electrical properties during fabrication.
- Copper Cladding: Apply copper foil to one or both sides of the RT/duroid® 5880 laminate sheets. The copper foil thickness should be chosen based on the required current-carrying capacity and impedance requirements of the circuit.
- Circuit Layout and Etching: Design the PCB layout using CAD software, taking into account the high-frequency characteristics of RT/duroid® 5880 laminates. Use appropriate trace widths and spacing to achieve the desired impedance and signal integrity. Transfer the layout onto the copper-clad laminate using photolithography or direct imaging techniques. Etch away the excess copper using chemical etchants, leaving behind the desired circuit traces.
- Drilling: Precision drill holes for through-hole components and vias using CNC drilling machines. Vias are plated with conductive material to establish electrical connections between different layers of the PCB.
- Plating and Surface Finish: Plate the drilled holes with copper or other conductive materials to ensure good electrical conductivity. Apply surface finish techniques such as immersion gold, immersion silver, or OSP to protect exposed copper surfaces and facilitate soldering.
- Lamination: Stack multiple layers of RT/duroid® 5880 laminate with copper-clad layers and prepreg in between. Apply heat and pressure in a lamination press to bond the layers together into a single rigid panel. This process ensures proper adhesion between layers and eliminates air voids.
- Routing and Profiling: Use CNC routing or milling machines to separate individual PCBs from the larger panel and profile them to their final dimensions.
- Quality Control: Perform visual inspection, dimensional measurement, and electrical testing on the fabricated PCBs to ensure they meet quality standards and specifications for high-frequency applications.
- Assembly and Testing: Assemble components onto the PCBs using surface mount technology (SMT) or through-hole assembly techniques. Perform final electrical testing to verify the functionality and performance of the assembled PCBs.
Throughout the manufacturing process, strict quality control measures are essential to ensure that RT/duroid® 5880 laminates PCBs meet the stringent requirements for high-frequency applications, including impedance control, signal integrity, and reliability. Collaboration with experienced PCB manufacturers familiar with working with RT/duroid® 5880 laminates can help ensure successful fabrication of high-quality PCBs.
How much should RT/duroid® 5880 Laminates PCBs cost?
The cost of RT/duroid® 5880 laminates PCBs can vary depending on several factors, including:
- Board Size and Complexity: Larger boards or those with intricate designs may require more material and manufacturing time, leading to higher costs.
- Layer Count: PCBs with more layers typically cost more to manufacture due to increased material and processing requirements.
- Material Thickness: Thicker RT/duroid® 5880 laminates may cost more than thinner ones due to the increased material usage.
- Copper Weight: PCBs with thicker copper layers or higher copper weight may incur additional costs for material and processing.
- Surface Finish: Different surface finish options, such as immersion gold or immersion silver, can affect the overall cost of PCB fabrication.
- Trace Width and Spacing: Tighter tolerances for trace width and spacing may require more precise manufacturing processes, potentially increasing costs.
- Quantity: Economies of scale typically apply, meaning that larger production quantities may result in lower per-unit costs.
- Turnaround Time: Expedited or quick-turn PCB fabrication services may come with additional fees.
- Supplier and Location:PCB manufacturers may have different pricing structures based on their overhead costs, location, and capabilities.
Given these factors, it’s challenging to provide an exact cost without specific details about the PCB design, quantity, and manufacturing requirements. However, as a rough estimate, the cost of RT/duroid® 5880 laminates PCBs can range from a few dollars for simple single-layer boards to several hundred dollars or more for complex multi-layer boards or prototypes. For precise pricing, it’s best to consult with PCB manufacturers and provide them with detailed specifications for a quote.
What is the RT/duroid® 5880 Laminates base material?
The base material of RT/duroid® 5880 laminates is a PTFE (polytetrafluoroethylene) composite. This composite material typically consists of woven fiberglass cloth impregnated with PTFE resin. PTFE is a type of synthetic fluoropolymer known for its excellent electrical insulating properties, low dielectric constant, and low loss tangent, especially at high frequencies.
The fiberglass reinforcement provides mechanical strength and dimensional stability to the laminate, while the PTFE resin matrix offers electrical insulation and maintains consistent electrical properties across a wide range of frequencies. The combination of these materials makes RT/duroid® 5880 laminates well-suited for high-frequency and microwave applications where maintaining signal integrity is critical.
Overall, the base material of RT/duroid® 5880 laminates provides a robust foundation for fabricating high-performance PCBs with excellent electrical properties and reliability in demanding RF and microwave environments.
Which company manufactures RT/duroid® 5880 Laminates PCBs?
Manufacturers of RT/duroid® 5880 copper-clad laminates include several well-known PCB manufacturing companies, some of which specialize in producing circuit boards for high-frequency applications, such as Rogers Corporation. Our company is also capable of producing RT/duroid® 5880 copper-clad laminates to meet the demand for high-frequency circuit boards from customers.
As an experienced and knowledgeable PCB manufacturer, we have advanced production equipment and a skilled technical team capable of providing high-quality RT/duroid® 5880 copper-clad laminate products. We adhere to strict quality control standards to ensure that every PCB meets our customers’ requirements and specifications.
Our production process includes material selection, engineering design, manufacturing processing, quality inspection, and other stages. We choose premium RT/duroid® 5880 copper-clad laminate materials and conduct engineering design and layout according to customer design requirements. During the manufacturing process, we use advanced equipment and technology to ensure the precision and stability of our products.
In terms of quality inspection, we strictly adhere to ISO quality management systems, conducting comprehensive quality testing and verification to ensure that our products meet international standards and customer requirements. We also provide flexible customization services to meet the personalized needs of our customers, catering to various industries and application areas.
Through our production of RT/duroid® 5880 copper-clad laminates, customers can obtain high-performance and highly reliable circuit board products suitable for various high-frequency applications, such as communication equipment, radar systems, satellite communications, and more. We continuously strive to improve our technical capabilities and service quality to provide customers with superior products and services.
What are the 7 qualities of good customer service?
Good customer service is characterized by several key qualities that help businesses build strong relationships with their customers and enhance overall satisfaction. Here are seven qualities of good customer service:
- Responsiveness: Good customer service involves being prompt and responsive to customer inquiries, requests, and concerns. This includes acknowledging customer messages promptly, providing timely assistance, and addressing issues in a timely manner.
- Empathy: Empathy is crucial in understanding and relating to customers’ emotions, needs, and perspectives. Good customer service representatives listen actively, show empathy towards customers’ challenges, and strive to find solutions that meet their needs.
- Professionalism: Professionalism entails maintaining a courteous and respectful demeanor when interacting with customers. This includes using polite language, maintaining a positive attitude, and adhering to company policies and standards.
- Knowledgeability: Good customer service representatives possess in-depth knowledge about the products or services they offer. They can answer customer questions accurately, provide relevant information, and offer valuable guidance and recommendations.
- Flexibility: Flexibility involves being adaptable and accommodating to meet customers’ changing needs and preferences. Good customer service representatives are willing to go the extra mile, offer customized solutions, and accommodate reasonable requests to ensure customer satisfaction.
- Transparency: Transparency is essential for building trust and credibility with customers. Good customer service involves being honest and transparent about products, pricing, policies, and any potential limitations or challenges.
- Follow-up and Resolution: Good customer service doesn’t end with the initial interaction. It includes following up with customers to ensure their issues have been resolved satisfactorily and their needs have been met. This may involve proactive communication, checking in with customers after a purchase or service experience, and addressing any remaining concerns promptly.
By embodying these qualities, businesses can deliver exceptional customer service experiences that foster loyalty, build positive brand reputation, and drive long-term success.
FAQs
What is RT/duroid® 5880 laminate?
RT/duroid® 5880 is a high-performance PTFE-based composite material used in microwave and RF applications. It is known for its excellent electrical properties and stability at high frequencies.
What are the key characteristics of RT/duroid® 5880 laminates?
RT/duroid® 5880 laminates have low dielectric constant and loss tangent, consistent electrical properties across frequencies, and tight thickness tolerance, making them suitable for demanding RF and microwave applications.
What are RT/duroid® 5880 laminates used for?
RT/duroid® 5880 laminates are used in the construction of high-frequency circuit boards, antennas, radar systems, telecommunications equipment, and other applications where maintaining signal integrity is crucial.
How are RT/duroid® 5880 laminates PCBs fabricated?
The fabrication process involves material preparation, layer stacking, lamination, drilling, copper etching, surface finish application, routing, profiling, and final inspection. Each step is crucial for ensuring high-quality PCBs.
What are the design guidelines for RT/duroid® 5880 laminates PCBs?
Design guidelines include considerations for transmission line design, grounding, component placement, via design, thermal management, manufacturing considerations, testing, and validation to optimize performance and reliability.
How much do RT/duroid® 5880 laminates PCBs cost?
Costs vary based on factors like board size, complexity, layer count, material thickness, copper weight, surface finish, quantity, turnaround time, supplier, and location. It’s best to consult with PCB manufacturers for precise pricing.
Which companies manufacture RT/duroid® 5880 laminates PCBs?
Several PCB manufacturing companies produce RT/duroid® 5880 laminates PCBs, including those specializing in high-frequency applications like Rogers Corporation. Additionally, some companies, including ours, can produce these PCBs to meet customer demand.