What is Rogers CLTE?
Rogers CLTE Manufacturer,Rogers CLTE is a high-performance microwave laminate material widely used in high-frequency communication systems and precision electronic devices. It is renowned for its exceptional electrical properties and mechanical stability, making it especially suitable for the demanding aerospace, military, and automotive industries. Rogers CLTE features an extremely low dielectric constant and loss factor, ensuring efficient signal transmission with minimal attenuation. Additionally, its low coefficient of thermal expansion ensures stability in physical dimensions and electrical performance under extreme temperature variations. These characteristics make Rogers CLTE an ideal material choice for RF applications and high-speed digital applications.
CLTE laminates have proven excellent dimensional stability and low planar CTE, providing consistent performance for embedded resistors: among the lowest variance available for PTFE-based laminates. CLTE laminates have a long history of use with Resistor Foil and are available with a full range of other cladding types (including electrodeposited, reverse treated copper, rolled copper foil or more). CLTE laminates’ tried and tested performance continues to make them a top choice for a wide range of ground-based and airborne communications and radar systems.
Features
Low thermal expansion in X, Y and Z of 10, 12 and 34 ppm/°C
Dielectric constant stability with temperature change
Available as a reliable and consistent thin laminate (.0003”)
Available with heavy metal backing (aluminum, brass and copper)
Benefits
High plated through hole reliability
Reduced stress attachment to ceramic active devices
Supports complex multi-layer boards
Reliably designed with embedded resistor networks
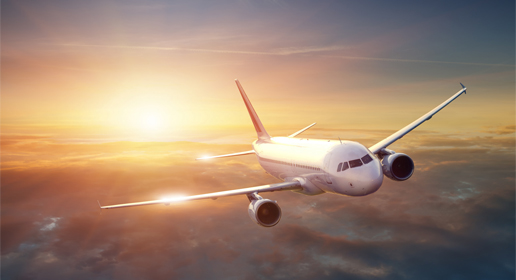
Rogers CLTE Manufacturer
How Does Rogers CLTE Optimize Signal Integrity and Thermal Performance?
Rogers CLTE (Ceramic Liquid Crystal Polymer) stands out in the field of package substrates for several unique features. Here are some notable characteristics that set Rogers CLTE apart in the world of package substrates:
Low Dielectric Loss: Rogers CLTE substrates have a low dielectric constant and low loss, providing excellent performance in high-frequency applications. This is crucial for applications requiring high performance and low signal attenuation, such as communication equipment and radar systems.
Thermal Stability: Rogers CLTE substrates exhibit outstanding thermal stability, maintaining stable performance in high-temperature environments. This is particularly important for applications that need to operate under elevated temperature conditions, such as automotive electronics and aerospace systems.
Superior Dimensional Stability: In high-temperature and high-humidity environments, Rogers CLTE substrates demonstrate excellent dimensional stability. This ensures reliable performance in various applications, especially under complex environmental conditions.
Diverse Material Options: Rogers provides a variety of CLTE substrates to meet the requirements of different applications. This diversity allows engineers to choose the material that best suits their designs, enhancing flexibility and performance.
Excellent Processing Performance: Rogers CLTE substrates are easy to process and manufacture, contributing to improved production efficiency. This is crucial for large-scale production and applications with high demands.
In summary, Rogers CLTE substrates have become a favored choice in the field of package substrates due to their low dielectric loss, thermal stability, dimensional stability, diverse material options, and excellent processing performance.
What Sets Rogers CLTE Apart in the World of Package Substrates?
Rogers Corporation’s CLTE (Ceramic Low Temperature Co-fired Ceramic) is an advanced technology designed to optimize signal integrity and thermal performance. CLTE achieves this goal through several key aspects:
Low-Temperature Co-fired Ceramic Technology (LTCC): CLTE employs the LTCC process, a method for manufacturing ceramic multilayer boards at relatively low temperatures. This helps maintain the material’s stability during the manufacturing process, reducing the coefficient of thermal expansion and thereby enhancing signal integrity.
Precise Material Selection: CLTE utilizes high-performance ceramics and precision materials that exhibit excellent performance at high frequencies and temperatures. By selecting these materials, CLTE can provide outstanding signal transmission performance and remain stable in complex thermal environments.
Design Flexibility: CLTE allows designers to implement highly complex circuit board designs, including microstrip lines, RF antennas, and other high-frequency components. This design flexibility enables engineers to optimize signal integrity and ensure maximized signal transmission on the circuit board.
Thermal Performance Optimization: As CLTE is designed for high-temperature environments, it can operate at elevated temperatures without sacrificing performance. This capability makes CLTE excel in challenging thermal conditions, such as high-power applications or RF applications in high-temperature environments.
In summary, Rogers’ CLTE combines low-temperature co-fired ceramic technology, high-quality material selection, design flexibility, and thermal performance optimization to provide a reliable solution for circuit board designs, achieving excellent signal integrity and thermal performance in high-frequency and high-temperature environments.
How Does Rogers CLTE Compare to IC Package Technologies?
Rogers CLTE (Ceramic Liquid Crystal Polymer) has several distinctions and advantages compared to IC (Integrated Circuit) package technologies:
Material Characteristics: Rogers CLTE is based on a Ceramic Liquid Crystal Polymer, featuring low dielectric loss and excellent thermal stability, making it suitable for high-frequency applications. In contrast, IC package technologies may utilize diverse materials, including plastics, encapsulation resins, with varying characteristics.
High-Frequency Performance: Rogers CLTE excels in high-frequency applications, particularly suitable for wireless communication, radar, and other high-frequency electronic devices. In comparison, some IC package technologies may have limitations in high-frequency performance.
Thermal Management: Due to the outstanding thermal stability of Rogers CLTE, it maintains stable performance in high-temperature environments, making it applicable to high-temperature applications like automotive engine control modules. In contrast, some IC package technologies may require additional heat dissipation design.
Package Density and Size: IC package technologies typically involve complex processes such as chip packaging and solder ball arrangements, allowing for higher package density. In comparison, while Rogers CLTE excels in high-frequency performance, it may not match some technologies specifically designed for chip-level packaging in terms of package density.
Cost and Manufacturing: IC package technologies are often more cost-effective in large-scale production as they can adapt to the economies of scale in chip-level manufacturing processes. Rogers CLTE may be more suitable for applications with specific requirements for high performance and environmental adaptability, but it might bring higher manufacturing costs in certain situations.
In summary, Rogers CLTE has advantages in high-frequency performance and environmental adaptability, catering to specific high-performance electronic applications. On the other hand, IC package technologies focus more on chip-level packaging, emphasizing package density and cost-effectiveness in large-scale production. The choice of technology depends on the specific requirements and design goals of the application.
How Does Rogers CLTE Bridge the Divide Between Traditional PCBs?
Rogers Corporation’s CLTE (Ceramic Low Temperature Co-fired Ceramic) is a technology designed to bridge the gap between traditional Printed Circuit Boards (PCBs) and the demands of the new generation of high-performance applications. CLTE achieves this bridging effect in several ways:
High-Frequency Performance: Traditional PCBs may face challenges in signal integrity and transmission loss in high-frequency applications. CLTE, through the use of advanced ceramic technology and materials, provides outstanding high-frequency performance, helping overcome the limitations of traditional PCBs in high-frequency environments.
Thermal Performance: As electronic devices demand higher performance, managing thermal challenges becomes crucial. CLTE is specifically engineered for high-temperature environments, offering superior heat handling capabilities when compared to traditional PCBs and delivering enhanced thermal performance.
Design Flexibility: Traditional PCBs may have limitations in some complex circuit designs. CLTE offers greater design flexibility, allowing engineers to better meet the demands of modern electronic devices for complex circuit designs, especially in high-frequency and high-performance applications.
Multilayer Integration: CLTE utilizes multi-layer co-fired ceramic technology, enabling the integration of multiple functions in a compact structure. This integration helps reduce the size of the circuit board and increase component integration.
CLTE technology successfully closes the divide between conventional PCBs and the next generation of high-performance circuit boards. It delivers a dependable and inventive solution for meeting the elevated demands of electronic devices in terms of both high-frequency operation and overall performance.
What Constitutes the Marvel of Rogers CLTE: Its Structure and Production Technologies?
The marvel of Rogers CLTE (Ceramic Liquid Crystal Polymer) is embodied in its unique structure and production technologies. Here are the key factors that constitute the marvel of Rogers CLTE:
Ceramic Liquid Crystal Polymer Structure: The foundation of Rogers CLTE lies in a structure based on Ceramic Liquid Crystal Polymer. This structure combines the high-temperature stability of ceramics with the mechanical properties of liquid crystal polymers, creating a material that excels in both high-frequency performance and thermal stability. This structure makes CLTE well-suited for functioning in complex and demanding working environments.
Lamination Process: Manufacturing Rogers CLTE involves a lamination process where multiple layers of materials are precisely stacked according to design requirements. This lamination process ensures the uniformity and consistency of the material, providing reliable electrical performance and structural strength.
Microfabrication Technologies: To meet the requirements of high-frequency applications, Rogers CLTE employs advanced microfabrication technologies. These technologies include precision printing, etching, and stacking processes, ensuring the precise manufacturing of tiny components on the circuit board to support the high-performance demands of complex electronic systems.
Surface Mount Technology: In the production process, surface mount technology is widely utilized to precisely mount tiny electronic components (such as chips, resistors, capacitors, etc.) onto Rogers CLTE substrates. This helps enhance the integration and performance of the circuit.
Stringent Quality Control: As a leading material manufacturer, Rogers implements stringent quality control standards. Through rigorous inspection and testing at each production stage, the consistency and reliability of Rogers CLTE are ensured.
The marvel of Rogers CLTE is attributed to its unique Ceramic Liquid Crystal Polymer structure, advanced lamination, microfabrication, and surface mount technologies, as well as the implementation of stringent quality control standards. These factors collectively make Rogers CLTE stand out in the field of package substrates, making it an ideal choice for high-performance electronic devices.
What Common Queries Does Rogers CLTE Address?
Rogers CLTE (Ceramic Liquid Crystal Polymer) typically addresses the following common issues or requirements:
High-Frequency Application Needs: Due to its low dielectric loss and excellent high-frequency performance, Rogers CLTE is well-suited for various high-frequency applications, such as communication devices, radar systems, and RF modules. It provides stable signal transmission and lower signal attenuation.
Thermal Stability Requirements: Rogers CLTE exhibits outstanding thermal stability, maintaining performance in high-temperature environments. Therefore, it is often chosen for applications that operate in complex thermal conditions, such as automotive electronics, aerospace, and energy systems.
Dimensional Stability and Precision Machining Requirements: For applications with high demands on dimensional stability and precision machining, such as microelectronics packaging and chip carriers, the performance of Rogers CLTE makes it an ideal choice.
Multilayer Design and Complex Circuit Demands: Due to its lamination process and microfabrication technology, Rogers CLTE is well-suited for designing complex multilayer circuit boards to meet the requirements of highly integrated and high-performance applications, such as advanced communication equipment and computer systems.
Special Environmental Requirements: Because of its superior characteristics, Rogers CLTE is frequently chosen for applications with special environmental requirements, including military applications, medical electronics, and industrial control systems.
Overall, Rogers CLTE, with its outstanding electrical, thermal, and processing characteristics, can meet a range of high-performance, high-frequency, and special environmental requirements. Therefore, engineers often consider Rogers CLTE as an ideal choice for their packaging substrate when faced with the mentioned demands.
How Does Rogers CLTE Navigate the Future of PCB Engineering?
How does Rogers CLTE lead the future development of PCB engineering?
High-Frequency Performance: With the continuous advancement of communication and RF applications, the demand for high-frequency performance is increasing. CLTE, through the adoption of advanced ceramic technology and precision materials, provides excellent signal transmission performance for high-frequency environments, making it a powerful choice for future high-frequency PCB engineering.
Integration and Miniaturization: As electronic devices trend towards being lightweight and compact, there is a growing demand for higher integration and compactness in circuit boards. CLTE, utilizing multi-layer co-fired ceramic technology, achieves compact integration of multifunctional components and is expected to become an ideal choice for future miniaturized electronic devices.
Thermal Performance: With the improvement of electronic device performance, thermal management becomes a critical issue. CLTE is designed for high-temperature environments, possessing outstanding thermal performance to meet the future demands of high-performance electronic devices for good thermal stability.
Innovative Design: CLTE provides greater design flexibility, enabling engineers to create more innovative and complex circuit designs. In future PCB engineering, this design flexibility will become more crucial to meet the evolving application requirements.
In summary, Rogers CLTE, with its advantages in high-frequency performance, integration and miniaturization, thermal performance, and innovative design, is poised to play a leading role in future PCB engineering, meeting the evolving needs of advancing electronic devices.