Rogers Cavity PCB Manufacturing
Rogers Cavity PCB Manufacturing,Rogers Cavity PCBs are a specialized type of printed circuit board renowned for their high-performance characteristics. These PCBs feature a unique design that incorporates cavities or recessed areas within the board structure, utilizing advanced laminates from Rogers Corporation. The use of high-performance materials ensures exceptional electrical properties, including low dielectric loss, high dielectric constant, and precise impedance control. This design offers several advantages, such as improved signal integrity, reduced electromagnetic interference, efficient thermal management, and potential for miniaturization. Rogers Cavity PCBs are widely used in demanding applications such as aerospace, telecommunications, RF/microwave systems, high-speed computing, and power electronics. Manufacturers employ specialized manufacturing techniques to produce these PCBs, including cavity formation, precise layer stackup design, and rigorous quality testing. With their superior performance and reliability, Rogers Cavity PCBs are the preferred choice for engineers and designers seeking high-quality solutions for critical electronic systems.
What is a Rogers Cavity PCB?
A Rogers Cavity PCB (Printed Circuit Board) refers to a type of circuit board design that incorporates Rogers Corporation’s high-performance laminates. Rogers Corporation is a leading manufacturer of advanced materials used in various electronic applications.
In a Rogers Cavity PCB, a portion of the PCB is designed as a cavity or a recessed area within the board itself. This cavity is typically filled with a dielectric material that has specific electrical properties, such as low loss tangent and high dielectric constant, which are provided by Rogers laminates.
The cavity design in these PCBs offers several advantages, including:
- Improved Signal Integrity: The use of high-performance dielectric materials helps minimize signal loss and distortion, leading to improved signal integrity, especially in high-frequency applications.
- Reduced Cross-talk: By isolating signal traces within the cavity, Rogers Cavity PCBs can reduce electromagnetic interference and cross-talk between adjacent traces.
- Controlled Impedance: Rogers laminates offer precise control over impedance characteristics, which is crucial for maintaining signal integrity in high-speed digital and RF (Radio Frequency) circuits.
- Thermal Management: The cavity design can also be utilized for thermal management purposes, allowing for efficient heat dissipation in power electronics applications.
- Miniaturization: In some cases, the cavity design can enable more compact PCB layouts, contributing to overall system miniaturization.
Overall, Rogers Cavity PCBs are favored in applications where high-frequency performance, signal integrity, and reliability are paramount, such as in aerospace, telecommunications, high-speed computing, and RF/microwave systems.
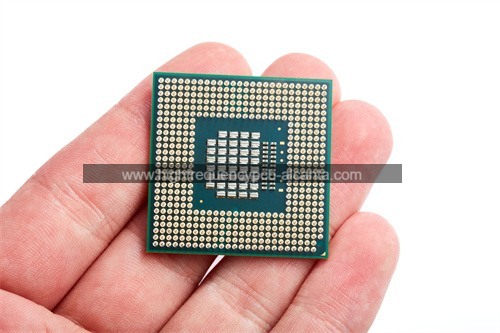
Rogers Cavity PCB Manufacturing
What are the Rogers Cavity PCB Design Guidelines?
The Rogers Cavity PCB design guidelines cover a range of key points to ensure optimal performance and reliability. These guidelines typically include the following:
- Material Selection: Choose the appropriate Rogers high-performance laminate material to meet design requirements, including specific dielectric constant, loss tangent, glass transition temperature, etc.
- PCB Layer Stackup: Determine the layer stackup of the PCB, including the position and size of internal cavities and the interconnection between different layers.
- Cavity Design: Design the geometry and dimensions of the cavity to best meet the requirements of specific applications, including signal integrity, thermal management, and electromagnetic compatibility.
- Routing and Impedance Control: Consider impedance control requirements during routing to ensure stability and consistency of signal transmission.
- Electrical Testing and Validation: Perform necessary electrical testing and validation to ensure that the design meets specification requirements and performs well in real-world applications.
- Thermal Management: Consider the impact of cavity design on thermal management to ensure effective heat dissipation in high-power applications.
- Signal Integrity Analysis: Use simulation tools to conduct signal integrity analysis, evaluating the impact of layout and routing on signal transmission and performing necessary optimizations.
- Production and Assembly Considerations: Consider the design characteristics of the PCB to select appropriate production and assembly processes and ensure repeatability and consistency during production.
Overall, the Rogers Cavity PCB design guidelines aim to guide engineers and designers on how to make the most of Rogers high-performance materials, designing PCBs that exhibit excellent performance and high reliability.
What is the Rogers Cavity PCB Fabrication Process?
The fabrication process for Rogers Cavity PCBs follows a series of steps similar to standard PCB manufacturing processes, with additional considerations for incorporating cavities and using high-performance materials. Below are the key steps involved in the fabrication process:
- Design Preparation: The process begins with the design of the PCB layout using specialized CAD (Computer-Aided Design) software. Engineers consider the placement and dimensions of the cavity, as well as the routing of traces and components, while adhering to design guidelines for Rogers high-performance materials.
- Material Selection: Select appropriate Rogers high-performance laminate materials based on the specific requirements of the application. These materials typically offer low dielectric loss, high dielectric constant, and other properties suitable for high-frequency and high-speed applications.
- Layer Stackup Design: Determine the layer stackup of the PCB, including the arrangement of copper layers, prepreg layers, and the placement of the cavity within the stack. The stackup design must ensure proper signal integrity, impedance control, and thermal management.
- Cavity Formation: Utilize specialized machining techniques, such as milling or routing, to create the cavity within the PCB substrate. The dimensions and geometry of the cavity are precisely controlled to meet design specifications.
- Copper Cladding: Apply copper foil to the outer layers of the PCB substrate through processes like lamination or electroplating. Copper traces are patterned using photolithography and etching techniques, following the layout design.
- Lamination: Assemble the layer stackup by laminating together the individual layers of the PCB substrate and copper foil. This process involves applying heat and pressure to bond the layers together, forming a solid structure.
- Drilling: Drill holes for vias and component mounting pads using precision drilling equipment. Vias are plated to provide electrical connections between different layers of the PCB.
- Surface Finishing: Apply surface finishes, such as HASL (Hot Air Solder Leveling), ENIG (Electroless Nickel Immersion Gold), or OSP (Organic Solderability Preservatives), to protect exposed copper surfaces and facilitate soldering during assembly.
- Testing and Inspection: Conduct electrical testing and visual inspection to ensure the integrity of the PCB design and manufacturing process. This includes checks for continuity, impedance, and dimensional accuracy.
- Component Assembly: Mount electronic components onto the PCB using surface mount technology (SMT) or through-hole technology (THT), depending on the design requirements.
- Final Testing: Perform final electrical testing to verify the functionality and performance of the assembled PCB.
By following these steps, manufacturers can produce Rogers Cavity PCBs that meet the stringent requirements of high-frequency, high-speed, and high-reliability applications.
How do you manufacture a Rogers Cavity PCB?
Manufacturing a Rogers Cavity PCB involves specialized processes to incorporate the cavity design and utilize high-performance materials effectively. Here’s a detailed overview of the manufacturing process:
- Design Preparation: Engineers create the PCB layout using CAD software, considering the placement and dimensions of the cavity, as well as routing of traces and components. Design guidelines specific to Rogers high-performance materials are followed.
- Material Selection: Choose appropriate Rogers high-frequency laminates based on the application’s requirements. These materials offer low dielectric loss, high dielectric constant, and other properties suitable for high-frequency applications
- Layer Stackup Design: Determine the layer stackup, including copper layers, prepreg layers, and cavity placement within the stack. The stackup ensures proper signal integrity, impedance control, and thermal management.
- Cavity Formation: Specialized machining techniques like milling or routing are used to create the cavity within the PCB substrate. Precisely control the cavity’s dimensions and geometry to meet design specifications.
- Prepreg and Copper Cladding: Apply copper foil to the outer layers of the PCB substrate through lamination or electroplating processes. Pattern copper traces using photolithography and etching techniques.
- Lamination: Assemble the layer stackup by laminating the individual layers together under heat and pressure. This bonds the layers into a solid structure, including the cavity.
- Drilling: Precision drilling equipment drills holes for vias and component mounting pads. Vias are plated to provide electrical connections between layers.
- Surface Finishing: Apply surface finishes like HASL, ENIG, or OSP to protect exposed copper surfaces and facilitate soldering during assembly.
- Testing and Inspection: Perform electrical testing and visual inspection to ensure PCB integrity, including continuity, impedance, and dimensional accuracy.
- Component Assembly: Mount electronic components using SMT or THT methods, depending on design requirements.
- Final Testing: Conduct final electrical testing to verify PCB functionality and performance.
Manufacturing a Rogers Cavity PCB requires attention to detail, precision machining, and adherence to design guidelines for high-performance materials. Following these steps ensures the production of PCBs suitable for high-frequency, high-speed, and high-reliability applications.
How much should a Rogers Cavity PCB cost?
The cost of a Rogers Cavity PCB can vary significantly depending on several factors, including the following:
- Board Size: Larger PCBs typically cost more due to increased material usage and manufacturing complexity.
- Number of Layers: More layers generally result in higher costs due to increased material and manufacturing complexity.
- Material Selection: Rogers high-performance materials are generally more expensive than standard FR-4 materials.
- Cavity Design: The complexity of the cavity design can impact manufacturing costs, especially if it requires specialized machining or additional processes.
- Surface Finish: Different surface finishes (e.g., HASL, ENIG, OSP) have different costs, with some being more expensive than others.
- Quantity: Ordering larger quantities of PCBs often results in lower per-unit costs due to economies of scale.
- Turnaround Time: Expedited manufacturing or delivery options may come with additional costs.
- Additional Features: Any additional features such as impedance control, controlled dielectric constants, or special tolerances will increase the overall cost.
To get an accurate cost estimate for a Rogers Cavity PCB, it’s best to consult with PCB manufacturers or suppliers. They can provide quotes based on your specific design requirements and quantities needed. Additionally, online PCB cost calculators may offer rough estimates based on parameters like board size, layer count, and material selection.
What is Rogers Cavity PCB base material?
The base material used in Rogers Cavity PCBs is typically a high-performance laminate manufactured by Rogers Corporation. Rogers offers a range of specialized laminates specifically designed for high-frequency and high-speed applications, which are well-suited for use in cavity PCBs.
Some common types of Rogers laminates used in cavity PCBs include:
- RO4000 Series: This series includes high-frequency laminates with low dielectric loss, excellent stability over a wide range of frequencies, and tight dimensional tolerance. Examples include RO4350B, RO4350B LoPro, RO4835, etc.
- RO3000 Series: These laminates are designed for high-frequency applications and offer low loss tangent, consistent dielectric constant, and excellent thermal conductivity. Examples include RO3003, RO3006, RO3010, etc.
- RO6000 Series: This series includes laminates with a ceramic-filled PTFE composite, providing high thermal conductivity and excellent electrical performance. Examples include RO6010, RO4350B, RO4835, etc.
- RT/duroid Series: These laminates feature ceramic-filled PTFE composites and are known for their low dielectric constant and low loss tangent. Examples include RT/duroid 5880, RT/duroid 6002, etc.
These Rogers laminates offer superior electrical properties, dimensional stability, and thermal performance compared to standard FR-4 materials, making them ideal choices for applications requiring high-frequency signal integrity, low loss, and reliable performance. The specific choice of base material depends on the application’s requirements, such as frequency range, signal speed, thermal management needs, and cost considerations.
Which company manufactures Rogers Cavity PCBs?
Manufacturing of Rogers Cavity PCBs is typically undertaken by specialized circuit board manufacturing companies. These companies generally possess advanced equipment, extensive experience, and technical knowledge to meet the manufacturing requirements of high-performance PCBs. They often establish partnerships with suppliers like Rogers Corporation to acquire high-quality materials and understand how to fully utilize these materials in the manufacturing process.
Our company is also capable of producing Rogers Cavity PCBs. We are an experienced and technologically advanced circuit board manufacturer with a professional team and state-of-the-art production equipment. We are committed to providing customers with high-quality and highly reliable circuit board solutions, including meeting the manufacturing requirements of Rogers Cavity PCBs.
Our company has the following advantages and capabilities:
- Professional Team: We have experienced engineers and technicians proficient in PCB design, manufacturing, and testing technologies, capable of providing comprehensive technical support and solutions.
- Advanced Equipment: Our production facilities are equipped with state-of-the-art production equipment and processes, including high-precision CNC drilling machines, automated surface mount lines, and advanced testing equipment, ensuring the production of high-quality PCB products.
- Strict Quality Control: We strictly adhere to international standards and industry regulations, implementing a comprehensive quality management system. Every aspect, from raw material procurement to final product delivery, undergoes strict quality control and inspection.
- Customized Services: We can customize PCB solutions according to the specific requirements of customers, including design, material selection, manufacturing processes, and surface treatments, to meet the specific application needs of customers.
- Timely Delivery: We are committed to delivering customer orders on time. Our flexible production planning and efficient production processes ensure that customers receive their required products in a timely manner.
Through our company’s professional technical team, advanced production equipment, and strict quality management system, we can provide high-quality and highly reliable Rogers Cavity PCBs to meet customers’ requirements for high-performance circuit boards.
Qualities of Good Customer Service
Good customer service encompasses several qualities that contribute to a positive experience for customers. Here are some key qualities of good customer service:
- Responsiveness: Responding promptly to customer inquiries, concerns, or requests for assistance shows that you value their time and are committed to addressing their needs in a timely manner.
- Empathy: Showing empathy means understanding and acknowledging the customer’s feelings, concerns, and perspective. Empathetic responses help build rapport and trust with customers, even in challenging situations.
- Clear Communication: Effective communication is essential for ensuring that customers understand information, instructions, or solutions provided by customer service representatives. Using clear and concise language helps avoid misunderstandings and confusion.
- Knowledgeability: Customer service representatives should have a good understanding of the products or services offered by the company, as well as policies, procedures, and troubleshooting techniques. Being knowledgeable enables them to provide accurate information and assistance to customers.
- Problem-Solving Skills: The ability to identify and resolve customer issues effectively is crucial for providing good customer service. Customer service representatives should be resourceful, proactive, and creative in finding solutions to meet customer needs.
- Professionalism: Maintaining professionalism in interactions with customers demonstrates respect, integrity, and competence. This includes being courteous, patient, and maintaining a positive attitude, even in challenging or stressful situations.
- Adaptability: Being adaptable means being flexible and able to adjust to different customer preferences, communication styles, and problem-solving approaches. Adaptable customer service representatives can better meet the diverse needs of customers.
- Proactive Communication: Anticipating customer needs and providing proactive assistance or information demonstrates initiative and attentiveness. Proactive communication can help prevent issues from escalating and enhance the overall customer experience.
- Follow-up and Resolution: Following up with customers to ensure that their issues have been resolved satisfactorily and addressing any remaining concerns or questions demonstrates commitment to customer satisfaction.
- Continuous Improvement: Good customer service involves a commitment to continuous learning and improvement. Soliciting feedback from customers, evaluating performance metrics, and implementing changes based on customer insights help enhance the quality of service provided.
By embodying these qualities, organizations can deliver exceptional customer service that fosters loyalty, positive word-of-mouth, and long-term relationships with customers.
FAQs (Frequently Asked Questions):
What is a Rogers Cavity PCB?
A Rogers Cavity PCB refers to a printed circuit board design that incorporates a cavity or recessed area within the board itself, utilizing high-performance laminates from Rogers Corporation.
What are the benefits of using Rogers Cavity PCBs?
Rogers Cavity PCBs offer advantages such as improved signal integrity, reduced electromagnetic interference, controlled impedance, thermal management capabilities, and potential for miniaturization in electronic applications.
What materials are used in Rogers Cavity PCBs?
Rogers Cavity PCBs typically utilize high-performance laminates from Rogers Corporation, such as materials from the RO4000, RO3000, or RT/duroid series, known for their excellent electrical properties and reliability.
What applications are suitable for Rogers Cavity PCBs?
Rogers Cavity PCBs are ideal for high-frequency, high-speed, and high-reliability applications, including aerospace, telecommunications, RF/microwave systems, high-speed computing, and power electronics.
How are Rogers Cavity PCBs manufactured?
The manufacturing process for Rogers Cavity PCBs involves specialized techniques such as cavity formation, precise layer stackup design, copper cladding, lamination, drilling, surface finishing, and rigorous testing to ensure quality and performance.
What design considerations are important for Rogers Cavity PCBs?
Important design considerations include cavity geometry and dimensions, material selection, layer stackup design, impedance control, thermal management, signal integrity analysis, and adherence to Rogers Cavity PCB design guidelines.
What are the cost factors associated with Rogers Cavity PCBs?
The cost of Rogers Cavity PCBs depends on factors such as board size, number of layers, material selection, cavity complexity, surface finish, quantity, and turnaround time.
Where can I find a reliable manufacturer for Rogers Cavity PCBs?
Several reputable PCB manufacturers specialize in producing Rogers Cavity PCBs. It’s essential to choose a manufacturer with experience, advanced capabilities, and a commitment to quality and customer satisfaction.