Rogers 4003c Substrate Manufacturer
Rogers 4003c Substrate Manufacturer,Rogers 4003c Substrate PCBs offer unparalleled performance in high-frequency applications. Engineered by Rogers Corporation, these circuit boards feature low dielectric loss, stable electrical characteristics, and exceptional thermal stability. With a consistent dielectric constant and excellent dimensional stability, Rogers 4003c substrates ensure reliable signal integrity and reduced signal loss, making them ideal for RF and microwave designs. From telecommunications to aerospace, industries rely on Rogers 4003c PCBs for their superior quality and predictability in demanding electronic systems.
What is a Rogers 4003c Substrate?
A Rogers 4003c substrate is a type of high-frequency circuit board material known for its excellent electrical properties, widely used in RF (Radio Frequency) and microwave applications. The “4003c” designation refers to its specific formulation and characteristics.
This substrate is made by Rogers Corporation, a leading manufacturer of advanced materials. It’s engineered to provide low dielectric loss, consistent electrical performance over a wide frequency range, and stable mechanical properties. These properties make it ideal for applications where signal integrity and reliability are crucial, such as in telecommunications, aerospace, defense, and automotive industries.
The Rogers 4003c substrate typically consists of a fiberglass-reinforced hydrocarbon ceramic laminate with a high-performance, thermoset resin system. Its low loss tangent and stable dielectric constant make it suitable for high-frequency designs, including microstrip, stripline, and coplanar waveguide circuits.
Engineers often choose the Rogers 4003c substrate for its predictable performance, ease of fabrication, and compatibility with standard PCB manufacturing processes. Its thermal stability and durability also contribute to its popularity in demanding environments. Overall, the Rogers 4003c substrate is valued for its contribution to achieving high-performance RF and microwave systems.
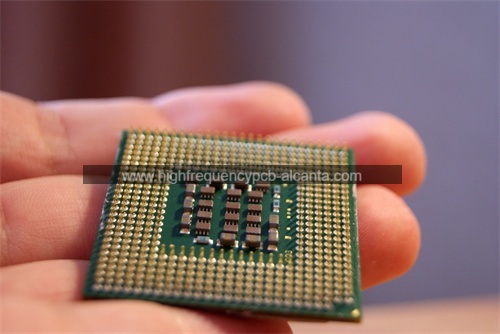
Rogers 4003c Substrate Manufacturer
What are the Rogers 4003c Substrate Design Guidelines?
Designing with Rogers 4003c substrates involves following specific guidelines to ensure optimal performance. Here are some key considerations:
- Dielectric Constant (Dk): Rogers 4003c has a stable dielectric constant of around 3.38 at 10 GHz. Designers should account for this value in their calculations for impedance matching and signal propagation.
- Dielectric Thickness: The thickness of the substrate affects impedance and signal propagation. Rogers 4003c substrates come in various thicknesses, so choose the one that best suits your design requirements.
- Trace Width and Spacing: Maintain appropriate trace widths and spacing to achieve the desired characteristic impedance and minimize signal loss. Rogers provides calculators and guidelines for determining these parameters based on the substrate properties.
- Ground Plane: Ensure a solid ground plane beneath signal traces to minimize interference and maintain signal integrity. Proper grounding is critical for RF and microwave circuits.
- Via Design: Use proper via structures to transition between layers and maintain signal integrity. Via placement and sizing are crucial to minimize impedance mismatches and signal losses.
- Copper Cladding:Rogers 4003c substrates typically come with high-quality copper cladding for excellent conductivity. Follow best practices for copper etching, plating, and finishing to ensure reliable connections and performance.
- Environmental Considerations: Consider the operating environment when designing with Rogers 4003c. It offers good thermal stability, but thermal management may still be necessary in high-power applications or extreme conditions.
- Manufacturability: Design for manufacturability by considering the capabilities and limitations of PCB fabrication processes. Rogers provides guidelines for stackup design, material handling, and assembly to facilitate smooth production.
- Testing and Validation: Validate your design through simulation, prototyping, and testing to ensure it meets performance requirements. Use RF testing equipment to verify impedance, signal loss, and other key parameters.
By following these guidelines and leveraging the excellent electrical properties of Rogers 4003c substrates, designers can create high-performance RF and microwave circuits with confidence. Additionally, consulting with Rogers or experienced RF engineers can provide valuable insights and assistance throughout the design process.
What is the Rogers 4003c Substrate Fabrication Process?
The fabrication process for Rogers 4003c substrates involves several steps to produce high-quality circuit boards suitable for RF and microwave applications. Here’s an overview of the typical fabrication process:
- Material Preparation: The process starts with preparing the Rogers 4003c substrate material. This involves cutting the material into sheets or panels of the desired size and thickness. The material may also undergo surface preparation to ensure proper adhesion of copper layers.
- Copper Cladding: The prepared substrate panels are then clad with copper on one or both sides using a process such as lamination or electrodeposition. Copper cladding provides the conductive layers for the circuit traces and ground planes.
- Circuit Patterning: Next, the copper-clad substrate is coated with a photoresist material. A photomask, which defines the circuit pattern, is then applied to the photoresist-coated substrate. The substrate is exposed to UV light, which transfers the circuit pattern from the photomask to the photoresist.
- Etching: After exposure, the substrate undergoes a chemical etching process to remove the copper not protected by the developed photoresist. This leaves behind the desired circuit traces and features on the substrate surface.
- Photoresist Stripping: Once the etching is complete, the remaining photoresist is stripped from the substrate, leaving clean copper traces and features.
- Drilling: Holes for vias and component mounting are drilled into the substrate using precision drilling equipment. These holes provide electrical connections between different layers of the circuit board and accommodate component leads or solder connections.
- Plating and Surface Finishing: After drilling, the vias are plated with conductive material to ensure electrical continuity between layers. Surface finishing processes, such as applying solder mask and surface treatment (e.g., immersion gold, HASL), are performed to protect the copper traces, improve solderability, and enhance the board’s durability.
- Final Inspection and Testing:The fabricated circuit boards undergo inspection to ensure they meet quality standards and dimensional accuracy. Electrical testing may also be performed to verify impedance, continuity, and other electrical properties.
- Cutting and Profiling: Finally, the fabricated panels are cut into individual boards and profiled to their final dimensions. This may involve routing, scoring, or other cutting methods to remove excess material and shape the boards as required.
Throughout the fabrication process, strict quality control measures are implemented to ensure consistency, reliability, and adherence to design specifications. Collaboration with experienced PCB manufacturers familiar with working with Rogers 4003c substrates can help ensure successful fabrication and optimal performance of RF and microwave circuits.
How do you manufacture a Rogers 4003c Substrate PCB?
Manufacturing a PCB (Printed Circuit Board) using Rogers 4003c substrate involves several steps. Here’s a detailed overview of the typical process:
- Design Preparation: The process begins with designing the PCB layout using specialized PCB design software. Engineers define the circuit schematic, component placement, and routing based on the desired electrical characteristics and mechanical constraints.
- Material Selection: Rogers 4003c substrate material is selected based on the specific requirements of the design, such as frequency, signal integrity, and thermal performance. The material is ordered in the form of sheets or panels of the required thickness.
- Panelization: If needed, multiple PCB designs are arranged on a larger panel to optimize manufacturing efficiency. Panelization involves arranging the individual PCB layouts within the panel area, leaving sufficient space for handling and processing.
- Lamination:The Rogers 4003c substrate panels are prepared for copper cladding through a lamination process. This involves cleaning the substrate surface and applying an adhesive layer to facilitate bonding with the copper foil.
- Copper Cladding: Copper foil is bonded to one or both sides of the substrate panel using heat and pressure. The bonded panel is then passed through a series of rollers to ensure proper adhesion and uniform thickness of the copper layer.
- Circuit Patterning: A photoresist layer is applied to the copper-clad substrate surface. A photomask, containing the circuit pattern, is aligned and placed over the photoresist-coated panel. UV light is used to transfer the circuit pattern onto the photoresist layer.
- Etching: The panel is immersed in an etchant solution, which selectively removes the exposed copper, leaving behind the desired circuit traces and features on the substrate surface. The etching process is closely monitored to ensure precise control of trace widths and feature dimensions.
- Photoresist Stripping: After etching, the remaining photoresist is stripped from the substrate surface using chemical solvents or stripping solutions. This leaves clean copper traces and features on the substrate.
- Drilling: Precision drills are used to create holes for vias and component mounting pads. These holes provide electrical connections between different layers of the PCB and accommodate component leads or solder connections.
- Plating and Surface Finishing: The drilled vias are plated with conductive material to ensure electrical continuity between layers. Surface finishing processes, such as applying solder mask and surface treatment (e.g., immersion gold, HASL), are performed to protect the copper traces, improve solderability, and enhance the board’s durability.
- Final Inspection and Testing: The manufactured PCBs undergo inspection to ensure they meet quality standards and dimensional accuracy. Electrical testing may also be performed to verify impedance, continuity, and other electrical properties.
- Cutting and Profiling: The fabricated panels are cut into individual PCBs and profiled to their final dimensions. This may involve routing, scoring, or other cutting methods to remove excess material and shape the boards as required.
Throughout the manufacturing process, strict quality control measures are implemented to ensure consistency, reliability, and adherence to design specifications. Collaboration with experienced PCB manufacturers familiar with working with Rogers 4003c substrates can help ensure successful fabrication and optimal performance of RF and microwave circuits.
How much should a Rogers 4003c Substrate PCB cost?
The cost of a Rogers 4003c substrate PCB can vary significantly depending on several factors, including:
- Size and Complexity: Larger and more complex PCBs require more materials and processing time, leading to higher costs.
- Quantity:Economies of scale often apply in PCB manufacturing. Higher quantities typically result in lower per-unit costs due to efficiencies in production.
- Material Cost: Rogers 4003c substrate is a specialized material known for its high performance, which can make it more expensive compared to standard FR-4 substrates.
- Layer Count:PCBs with more layers require additional processing steps and materials, contributing to higher costs.
- Surface Finish and Features: Specialized surface finishes or features such as blind vias, buried vias, and controlled impedance may increase the cost of the PCB.
- Lead Time: Shorter lead times may incur expedited manufacturing charges, while longer lead times may offer cost savings.
- Supplier and Location: PCB manufacturing costs can vary based on the supplier’s pricing structure, location, and manufacturing capabilities.
As a rough estimate, a simple single-layer Rogers 4003c substrate PCB of standard size (e.g., 100 mm x 100 mm) may cost anywhere from tens to hundreds of dollars per board, depending on the quantity and other factors mentioned above. More complex PCBs with multiple layers, intricate designs, or specialized requirements can cost significantly more.
For accurate pricing, it’s best to consult with PCB manufacturers or suppliers who specialize in Rogers 4003c substrate PCBs. They can provide detailed quotes based on your specific design and requirements. Additionally, requesting quotes from multiple suppliers can help you compare costs and find the most competitive pricing for your project.
What is Rogers 4003c Substrate base material?
The base material of Rogers 4003c substrate is a high-performance composite laminate specifically engineered for RF (Radio Frequency) and microwave applications. Rogers Corporation, the manufacturer of Rogers 4003c, typically formulates this base material using a fiberglass-reinforced hydrocarbon ceramic laminate.
Here’s a breakdown of the key components:
- Fiberglass Reinforcement: Fiberglass provides mechanical strength and dimensional stability to the substrate. It helps maintain the structural integrity of the PCB and withstands mechanical stress during fabrication and operation.
- Hydrocarbon Ceramic:The hydrocarbon ceramic matrix serves as the dielectric material of the substrate. It determines the electrical properties of the PCB, including the dielectric constant (Dk) and loss tangent (Df). Rogers 4003c is known for its low dielectric loss and stable electrical performance over a wide frequency range, attributes enabled by the composition and structure of the hydrocarbon ceramic.
- Thermoset Resin System: The resin system binds the fiberglass reinforcement and hydrocarbon ceramic matrix together, forming a durable composite laminate. This resin system is carefully formulated to ensure compatibility with high-frequency signals, low moisture absorption, and excellent thermal stability.
Overall, the combination of fiberglass reinforcement, hydrocarbon ceramic, and thermoset resin in Rogers 4003c substrate provides a reliable and high-performance material for RF and microwave circuit applications. It offers consistent electrical properties, good dimensional stability, and ease of fabrication, making it a preferred choice for demanding electronic designs.
Which company makes Rogers 4003c Substrate PCBs?
Rogers 4003c substrate PCBs are manufactured by Rogers Corporation. Rogers Corporation is a leading company specializing in the production of high-performance materials, headquartered in Connecticut, USA. With over 180 years of history, the company provides innovative material solutions to various industries worldwide. Rogers 4003c substrate is one of the company’s specialized high-frequency circuit board materials, widely used in the fields of Radio Frequency (RF) and microwave.
Our company is also capable of producing Rogers 4003c substrate PCBs. As a professional PCB manufacturer, we have advanced production equipment and a skilled technical team to provide high-quality circuit boards that meet customer requirements. Our production processes adhere to international standards, with strict control at every manufacturing stage to ensure reliable product quality. With our experienced team, we can produce custom Rogers 4003c substrate PCBs according to customer design requirements and specifications.
Our strengths include:
- Professional Team:We have an experienced engineering team to provide comprehensive technical support and services to meet customer needs.
- Advanced Equipment: We have introduced advanced production equipment and process technologies to achieve efficient production and precise processing, ensuring product quality and delivery lead time.
- Strict Quality Control: We implement a rigorous quality management system, with strict quality control from raw material procurement to production, ensuring product stability and reliability.
- Customized Services: We offer customized solutions to produce Rogers 4003c substrate PCBs according to customer requirements, including dimensions, layer count, surface treatment, etc.
- Competitive Pricing: We can provide competitive prices based on customer order quantity and requirements while ensuring product quality and delivery lead time.
By choosing our company as a partner, you can confidently obtain high-quality Rogers 4003c substrate PCBs with professional technical support and services. We are committed to providing satisfactory solutions to customers and growing together with them.
What are the 7 qualities of good customer service?
Good customer service is essential for building positive relationships with customers and fostering loyalty. Here are seven qualities that contribute to excellent customer service:
- Attentiveness: Good customer service begins with being attentive to customers’ needs and concerns. Listening actively, asking clarifying questions, and showing genuine interest in resolving issues demonstrate attentiveness and help customers feel valued.
- Empathy: Empathy involves understanding and acknowledging customers’ feelings and perspectives. Empathetic customer service representatives can relate to customers’ experiences, show compassion, and provide support, even in challenging situations.
- Patience: Patience is crucial, especially when dealing with frustrated or confused customers. Customer service representatives should remain calm, composed, and patient, allowing customers to express themselves fully and addressing their concerns without rushing or becoming agitated.
- Clear Communication: Clear communication is essential for ensuring customers understand information, instructions, and solutions provided by customer service representatives. Using simple language, avoiding jargon, and confirming understanding can prevent misunderstandings and enhance the customer experience.
- Product Knowledge: Customer service representatives should have a deep understanding of the products or services they support. Having comprehensive product knowledge enables representatives to answer questions accurately, offer relevant recommendations, and troubleshoot issues effectively, instilling confidence in customers.
- Problem-Solving Skills: Good customer service involves proactively resolving issues and finding solutions to customers’ problems. Customer service representatives should be resourceful, creative, and empowered to address customer concerns efficiently, aiming for timely resolution and customer satisfaction.
- Positive Attitude: A positive attitude can significantly impact the customer experience. Customer service representatives who approach interactions with enthusiasm, friendliness, and optimism can create a welcoming atmosphere, build rapport with customers, and leave a lasting positive impression.
By embodying these qualities, businesses can deliver exceptional customer service that exceeds expectations, fosters customer loyalty, and strengthens the overall reputation of the brand.
FAQs
What are the key characteristics of Rogers 4003c substrate?
Rogers 4003c substrate is known for its low dielectric loss, stable electrical performance over a wide frequency range, and excellent thermal stability. It also has a consistent dielectric constant (Dk) and low moisture absorption.
What are the advantages of using Rogers 4003c substrate PCBs?
Rogers 4003c substrate PCBs provide superior signal integrity, reduced signal loss, and improved reliability in high-frequency applications. They offer predictable performance, ease of fabrication, and compatibility with standard PCB manufacturing processes.
What types of applications are suitable for Rogers 4003c substrate PCBs?
Rogers 4003c substrate PCBs are commonly used in telecommunications, aerospace, defense, automotive, and other industries where high-frequency performance and reliability are critical. They are ideal for RF amplifiers, antennas, power amplifiers, radar systems, and more.
How do I design PCBs with Rogers 4003c substrate?
Designing PCBs with Rogers 4003c substrate involves following specific guidelines to optimize performance. These guidelines include considerations for trace width and spacing, ground plane design, via placement, and environmental factors. Consulting with experienced RF engineers and utilizing simulation tools can aid in the design process.
What is the fabrication process for Rogers 4003c substrate PCBs?
The fabrication process includes steps such as material preparation, copper cladding, circuit patterning, etching, drilling, plating, surface finishing, final inspection, and cutting. It requires specialized equipment and expertise to ensure the quality and reliability of the finished PCBs.
Where can I purchase Rogers 4003c substrate PCBs?
Rogers 4003c substrate PCBs can be purchased from authorized PCB manufacturers and distributors specializing in high-frequency circuit boards. It’s essential to choose a reputable supplier with experience in handling Rogers materials and producing high-quality PCBs.